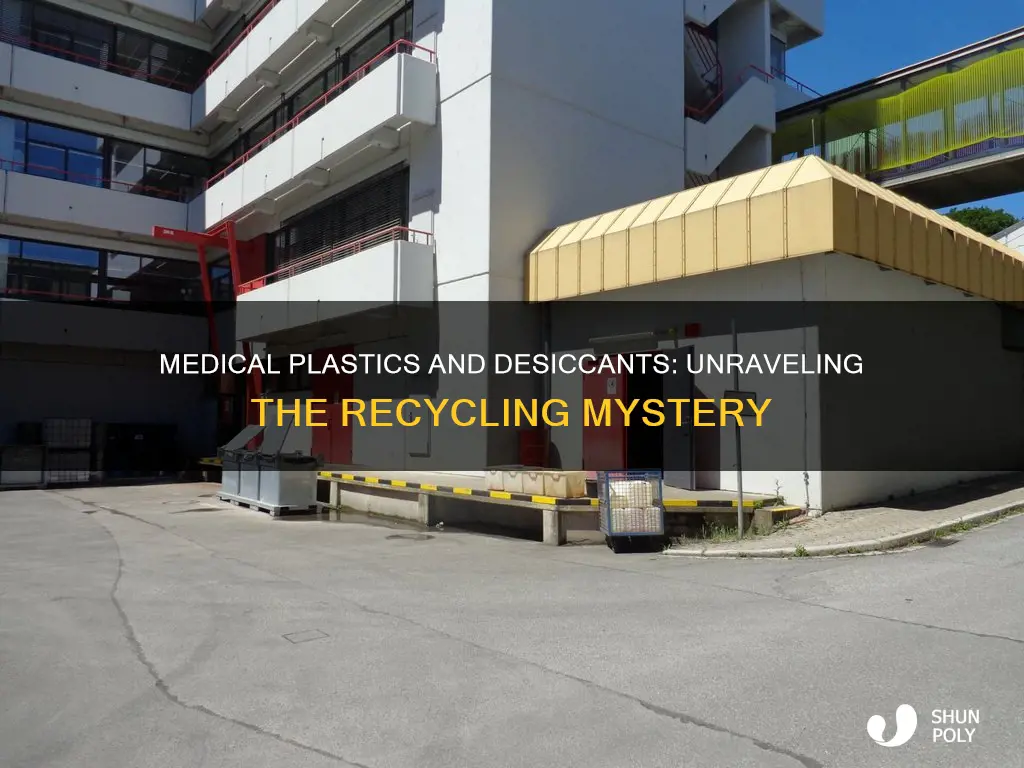
The use of desiccants in medical plastics is a critical aspect of ensuring the safety and efficacy of medical devices. However, the environmental impact of these materials, particularly their recyclability, is a growing concern. This paragraph aims to explore the question of whether desiccants in medical plastics can be effectively recycled, considering the challenges and potential solutions in the recycling process. It will discuss the composition of medical plastics, the role of desiccants, and the current recycling methods, as well as the barriers and opportunities for improving the recyclability of these materials.
Characteristics | Values |
---|---|
Environmental Impact | Desiccants in medical plastics can be recycled, but the process is complex and energy-intensive. The recyclability depends on the type of desiccant and the plastic matrix. |
Regulatory Compliance | Many medical plastics and desiccants are regulated by strict standards, ensuring biocompatibility and safety. Recycling processes must adhere to these regulations. |
Material Compatibility | Desiccants should be compatible with the plastic material to avoid degradation or chemical reactions during recycling. |
Moisture Removal Efficiency | Desiccants can effectively remove moisture from medical plastics, but their efficiency may vary depending on the desiccant type and application. |
Cost Considerations | Recycling medical plastics with desiccants can be expensive due to specialized processes and materials. However, it can be cost-effective for high-volume production. |
Waste Management | Proper waste management practices are crucial when disposing of medical plastics with desiccants to ensure environmental protection. |
Research and Development | Ongoing research focuses on developing more sustainable desiccants and recycling methods for medical plastics. |
Application Specifics | Different medical applications may require specific desiccant properties and recycling techniques. |
What You'll Learn
- Desiccant Types: Silica gel, calcium chloride, and zeolites are common desiccants in medical plastics
- Recycling Methods: Mechanical recycling, chemical recycling, and pyrolysis are methods to recycle desiccant-infused plastics
- Environmental Impact: Desiccants can affect the recyclability and sustainability of medical plastics
- Regulatory Considerations: Compliance with medical device regulations is crucial for desiccant-treated plastics
- Alternatives: Natural desiccants and innovative materials offer eco-friendly alternatives to traditional desiccants in medical plastics
Desiccant Types: Silica gel, calcium chloride, and zeolites are common desiccants in medical plastics
Silica gel, calcium chloride, and zeolites are widely used desiccants in the medical plastics industry, each with unique properties that make them suitable for various applications. These desiccants play a crucial role in maintaining the integrity and safety of medical devices and packaging.
Silica gel is a popular choice due to its high efficiency in moisture absorption. It is often used in the form of small, granular particles that can be easily integrated into medical plastic components. When exposed to moisture, silica gel crystals form, effectively removing water vapor from the surrounding environment. This property is essential in medical plastics, as it helps prevent microbial growth and ensures the stability of sensitive medications and medical devices. Silica gel is also known for its non-toxic nature, making it safe for use in medical applications.
Calcium chloride is another desiccant commonly employed in medical plastics. It is highly effective at absorbing moisture and can be used in both solid and liquid forms. In medical devices, calcium chloride is often incorporated into the plastic material during manufacturing. As a result, it continuously absorbs moisture from the environment, ensuring that the device remains dry and free from potential contaminants. This is particularly important in medical applications where moisture can compromise the performance and safety of the equipment.
Zeolites, a group of porous materials, are also utilized as desiccants in medical plastics. They possess a unique structure that allows for the selective absorption of water molecules. Zeolites can be tailored to have specific absorption capacities, making them versatile for different medical applications. These desiccants are often used in packaging materials to protect sensitive products from moisture-related issues. Zeolites' ability to regenerate and release absorbed moisture under controlled conditions further enhances their value in the medical plastics industry.
The recyclability of these desiccants is an important consideration for the sustainability of medical plastics. Silica gel, for instance, can be regenerated through heating, allowing it to be reused multiple times. This process helps reduce waste and ensures a continuous supply of desiccant for medical applications. Similarly, zeolites can be recycled through various methods, including chemical treatment and physical separation, making them an environmentally friendly choice. However, the recyclability of calcium chloride is less straightforward, as it may require specialized processes to recover and reuse the material effectively.
In summary, silica gel, calcium chloride, and zeolites are essential desiccants in medical plastics, each contributing to the preservation of product quality and safety. While their effectiveness is well-established, the recyclability of these desiccants varies, and further research and development are needed to optimize their environmental sustainability. Understanding the properties and recyclability of these desiccants is crucial for the medical plastics industry to ensure a reliable and eco-friendly supply chain.
Bejot Chairs: Eco-Friendly or Recycled? Unraveling the Mystery
You may want to see also
Recycling Methods: Mechanical recycling, chemical recycling, and pyrolysis are methods to recycle desiccant-infused plastics
Mechanical recycling is a widely used process for recycling desiccant-infused medical plastics. This method involves breaking down the plastic into smaller pieces, often through shredding or granulating, and then reprocessing these fragments into new products. The desiccants, which are typically small particles or fibers, are separated from the plastic during this process. Mechanical recycling is advantageous as it can handle a variety of plastic types and is relatively energy-efficient. However, it may not be suitable for all desiccant-infused plastics, especially those with complex structures or high desiccant content, as the desiccants might not be easily recoverable or reusable.
Chemical recycling, also known as feedstock recycling, is another effective approach to recycling desiccant-infused medical plastics. This process involves breaking down the plastic and desiccant into their constituent chemicals, which can then be repurposed. Chemical recycling methods include solvent extraction, where the desiccant is separated using solvents, and thermal degradation, which uses heat to break down the plastic and desiccant. This method is particularly useful for plastics with high desiccant content, as it allows for the recovery of both the plastic and the desiccant. However, chemical recycling can be more complex and energy-intensive compared to mechanical recycling, and it may require specialized equipment and processes.
Pyrolysis is a thermal recycling technique that offers a promising solution for desiccant-infused medical plastics. This process involves heating the plastic and desiccant in the absence of oxygen, causing them to decompose and form new materials. Pyrolysis can produce a range of products, including hydrocarbons, which can be further refined for various applications. This method is advantageous as it can handle a wide range of plastic types and desiccant concentrations. Additionally, pyrolysis can be a rapid and energy-efficient process, making it a viable option for large-scale recycling operations. However, it may require careful control to ensure the complete removal of desiccants and the production of high-quality recycled materials.
In summary, recycling desiccant-infused medical plastics is achievable through various methods, including mechanical recycling, chemical recycling, and pyrolysis. Mechanical recycling is a straightforward process for separating plastics and desiccants, while chemical recycling allows for the recovery of both components. Pyrolysis offers a versatile and efficient approach, especially for plastics with high desiccant content. Each method has its advantages and considerations, and the choice of recycling technique depends on the specific plastic type, desiccant concentration, and the desired end-use of the recycled material. Further research and development in these recycling processes will contribute to a more sustainable approach to managing desiccant-infused medical plastics.
Amazon's Plastic Envelopes: Unraveling the Recycling Mystery
You may want to see also
Environmental Impact: Desiccants can affect the recyclability and sustainability of medical plastics
Desiccants, commonly used in medical packaging to control moisture, can have a significant environmental impact when it comes to the recyclability and sustainability of medical plastics. These small, moisture-absorbing particles are often made from silica gel or other synthetic materials and are designed to be highly effective in their task. However, their presence in medical plastic products can present challenges during the recycling process.
One of the primary environmental concerns is the potential for desiccants to contaminate the recycling stream. Medical plastics, such as those used in syringes, IV bags, and surgical instruments, often contain desiccants to ensure product sterility. When these products are discarded, the desiccants can remain in the plastic, making it difficult to recycle. Desiccants may not be compatible with standard recycling processes, as they can interfere with the mechanical and chemical recycling methods used to process plastic waste. This incompatibility can lead to contamination, where desiccants mix with other recyclables, making it harder to sort and process the materials effectively.
The impact of desiccants on recyclability becomes even more critical when considering the limited availability of medical plastic recycling facilities. Many medical waste streams are not easily recyclable due to the specialized nature of the materials and the need for strict sterility standards. Desiccants, if not properly managed, can complicate the recycling process, potentially leading to increased costs and reduced efficiency. As a result, medical facilities and waste management companies might be discouraged from adopting recycling practices, hindering the progress towards a more sustainable healthcare system.
Furthermore, the environmental impact extends beyond the recycling process. Desiccants, when not properly contained or disposed of, can leach chemicals into the environment. Some desiccants are made from synthetic materials that may release harmful substances when exposed to moisture or when broken down. These chemicals can contaminate soil and water sources, posing risks to ecosystems and potentially affecting human health. Proper disposal methods, such as specialized waste management practices, are essential to mitigate these environmental risks.
To address these challenges, medical device manufacturers and healthcare providers should consider implementing strategies to minimize the use of desiccants or explore alternative moisture control methods. This could include using moisture-vapor transmission barriers, desiccants with lower environmental impact, or innovative packaging designs that reduce the need for desiccants. By adopting more sustainable practices, the medical industry can contribute to a circular economy, ensuring that medical plastics are recyclable and environmentally friendly.
The Journey of Plastic: From Waste to New Life
You may want to see also
Regulatory Considerations: Compliance with medical device regulations is crucial for desiccant-treated plastics
The use of desiccants in medical plastics is a common practice to control moisture and ensure the integrity of medical devices. However, the presence of these desiccants can pose challenges when it comes to recycling and regulatory compliance. Medical device regulations are stringent and require manufacturers to adhere to specific standards to ensure the safety and efficacy of the products. One of the critical aspects of these regulations is the management of materials and their potential environmental impact.
When desiccants are used in medical plastics, the primary concern is the potential for these substances to interfere with the recycling process and the overall sustainability of the materials. Desiccants, such as silica gel or calcium chloride, are often used in small packets or sachets within the plastic components. While these desiccants are effective in moisture absorption, they can also introduce complexities in the recycling stream. Some desiccants may not be easily separable from the plastic, making it challenging to recycle the materials effectively.
To comply with medical device regulations, manufacturers must consider the entire lifecycle of the product, including its end-of-life management. The regulatory bodies emphasize the importance of sustainable practices, and this includes the proper disposal and recycling of medical devices and their components. For desiccant-treated plastics, this means implementing strategies to remove or neutralize the desiccants before recycling. This could involve specialized cleaning processes or the use of desiccant-free alternatives.
Compliance with regulations also requires detailed documentation and traceability. Manufacturers need to maintain records of the desiccant usage, including the type, quantity, and placement within the medical devices. This information is crucial for demonstrating compliance and ensuring that the recycling process adheres to the required standards. Additionally, providing clear instructions for end-users on desiccant handling and disposal is essential to meet regulatory requirements.
In summary, while desiccants play a vital role in maintaining the quality of medical plastics, their presence introduces regulatory considerations. Manufacturers must navigate the challenges of desiccant removal and recycling while adhering to strict medical device regulations. By implementing appropriate processes and maintaining comprehensive documentation, companies can ensure compliance and contribute to the overall sustainability of the medical device industry.
Eco-Friendly Choice: Compostable or Recyclable? The Ultimate Cup Comparison
You may want to see also
Alternatives: Natural desiccants and innovative materials offer eco-friendly alternatives to traditional desiccants in medical plastics
The medical industry's reliance on desiccants in plastic packaging is well-known, but the environmental impact of these traditional desiccants raises concerns. Traditional desiccants, often made from synthetic materials, can be non-biodegradable and potentially harmful when disposed of. This has led to a growing interest in exploring eco-friendly alternatives that can provide effective moisture control without the environmental drawbacks.
One promising approach is the use of natural desiccants. These materials, derived from natural sources, offer a more sustainable option. For instance, silica gel, a naturally occurring mineral, is widely used as a desiccant. It can be easily recycled and reused, making it an environmentally friendly choice. Other natural desiccants include calcium chloride and calcium sulfate, both of which are biodegradable and can be safely disposed of, reducing the environmental impact on landfills.
Innovative materials are also being developed to replace traditional desiccants. One such material is a bio-based polymer that can absorb moisture and is fully biodegradable. This polymer can be engineered to have specific moisture-absorbing properties, making it suitable for medical packaging. Another innovative solution is the use of active carbon, which has excellent moisture-absorbing capabilities and can be incorporated into plastic materials, providing an effective and eco-conscious desiccant.
In addition to these materials, researchers are exploring the use of moisture-scavenging technologies. These technologies can actively remove moisture from the environment, reducing the need for desiccants in the first place. For example, a new type of polymer membrane can be used to create a self-healing barrier that prevents moisture penetration, thus eliminating the need for desiccants in medical packaging.
The transition to these eco-friendly alternatives is a significant step towards a more sustainable medical industry. By adopting natural desiccants and innovative materials, manufacturers can reduce their environmental footprint while maintaining the necessary moisture control in medical plastics. This shift not only benefits the environment but also aligns with the growing consumer demand for sustainable products, ensuring a greener future for medical packaging.
Unraveling the Recycling Mystery: 5 Plastics and Their Fate
You may want to see also
Frequently asked questions
Desiccants, such as calcium sulfate or silica gel, are often used in medical packaging to absorb moisture and maintain a dry environment for sensitive medical devices and products. While these desiccants themselves are not typically recyclable, the medical plastics they are used with can be. The recyclability of the entire assembly depends on the specific materials and the manufacturing process.
In some cases, desiccants can be removed or replaced before the recycling process. Medical facilities and manufacturers often have procedures in place to handle desiccants properly. This may involve replacing the desiccant packets, carefully removing them, or following specific guidelines provided by the recycling facility to ensure the materials are recyclable.
The presence of desiccants in medical plastics generally does not significantly impact the recyclability of the final product. However, the type and concentration of desiccants used can influence the recycling process. Some desiccants may require specific handling or preprocessing to ensure they do not interfere with the recycling stream. It is essential to consult with recycling experts and follow industry guidelines to ensure proper recycling practices.
Using desiccants in medical plastics can provide several environmental advantages. By maintaining a dry environment, desiccants help prevent microbial growth and ensure the stability of medical products, reducing the need for excessive packaging or additional preservatives. This can lead to more sustainable packaging designs and potentially lower overall environmental impact. Additionally, proper recycling and disposal of medical plastics with desiccants can contribute to resource conservation and minimize waste.