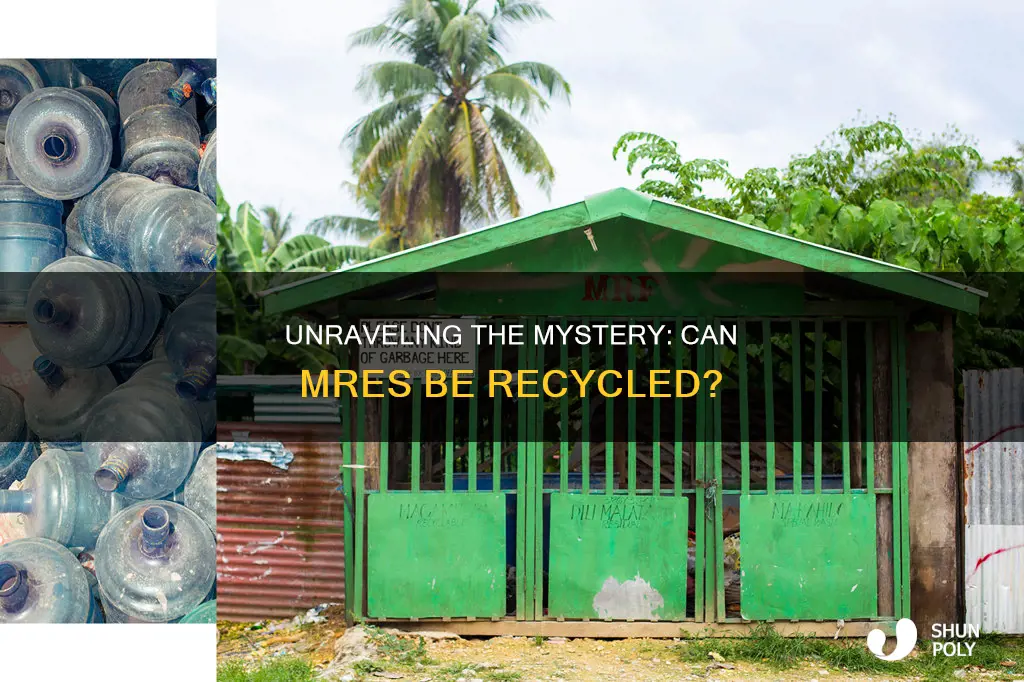
Many people are curious about the recyclability of MREs (Meals Ready-to-Eat), especially regarding their plastic components. MREs are often packaged in plastic containers and wrappers, which can raise concerns about environmental impact. This paragraph aims to shed light on the recyclability of these plastic materials used in MREs, exploring the options available for proper disposal and the potential for recycling these common military and emergency food packages.
Characteristics | Values |
---|---|
Material | Polyester (PET) or Polyethylene (PE) |
Recycling Process | MREs can be recycled through specialized facilities that handle plastic waste. |
Recycling Symbols | Look for the recycling symbol (3 arrows) and the number inside (resin identification code) to identify the type of plastic. MREs typically contain PET or PE, which are commonly recyclable. |
Environmental Impact | Recycling MREs reduces waste and helps conserve resources. However, improper disposal can still lead to environmental pollution. |
Local Recycling Options | Check with local recycling centers or waste management facilities to see if they accept MREs. Some facilities may require specific preparation, such as removing packaging. |
Alternative Disposal | If recycling is not available, MREs can be disposed of in landfills, but this is not ideal due to the potential for environmental contamination. |
Biodegradability | MREs are not biodegradable and can persist in the environment for a long time if not managed properly. |
Chemical Composition | The plastic used in MREs may contain additives and chemicals, but these are generally not harmful if the plastic is recycled properly. |
Market for Recycled Plastic | Recycled PET and PE can be used to produce new products like fibers, bottles, and containers, contributing to a circular economy. |
What You'll Learn
- Types of Plastic: Identify and differentiate between various types of plastic used in MREs
- Recycling Processes: Explore methods and challenges in recycling MRE plastic packaging
- Environmental Impact: Assess the environmental benefits and drawbacks of recycling MRE plastics
- Consumer Awareness: Educate consumers on proper disposal and recycling practices for MRE plastics
- Industry Standards: Examine industry guidelines and regulations for MRE plastic recycling
Types of Plastic: Identify and differentiate between various types of plastic used in MREs
The world of military rations, or MREs, relies on various types of plastic to ensure the longevity and safety of the food items they contain. Understanding these plastics is crucial for recycling efforts and environmental sustainability. Here's a breakdown of the common plastics used in MREs and their characteristics:
- High-Density Polyethylene (HDPE): This is one of the most prevalent plastics in MREs, particularly for packaging. HDPE is known for its durability and resistance to moisture and chemicals. It is often used for the outer packaging of MREs, such as the plastic bag or pouch that holds the meal. The number '2' is typically found on the recycling symbol of HDPE products, indicating their recyclability. MRE manufacturers use HDPE-coated paperboards to create the meal's packaging, ensuring a lightweight and protective barrier.
- Low-Density Polyethylene (LDPE): LDPE is another common plastic in MREs, often used for flexible packaging. It is lightweight and flexible, making it ideal for forming the plastic bags or wraps that enclose individual food items. LDPE is also recyclable, identified by the number '4' on its recycling symbol. The breathable nature of LDPE allows for the release of excess moisture, which is beneficial for keeping food fresh.
- Polypropylene (PP): Polypropylene is a versatile plastic used in MREs for various components. It is known for its heat resistance and ability to withstand high temperatures, making it suitable for microwaveable meals. PP is also lightweight and rigid, providing structural integrity to containers. The number '5' on the recycling symbol indicates that PP is recyclable. MRE manufacturers often use PP for the inner lining of packaging or as a separate component to hold the meal.
- Polyethylene Terephthalate (PET): PET is a type of plastic commonly associated with beverage bottles, but it also finds its way into MREs. It is lightweight, transparent, and has excellent barrier properties, making it ideal for packaging dry goods and snacks. PET is recyclable, as indicated by the number '1' on its recycling symbol. The use of PET in MREs ensures that the food items remain protected and fresh during storage and transportation.
Differentiating and Recycling: Identifying the different types of plastic in MREs is essential for proper recycling. Each plastic type has unique properties and recycling requirements. HDPE and LDPE, being recyclable, can often be found in the recycling stream, while PP and PET may require specialized recycling facilities. Understanding these distinctions ensures that MRE packaging is managed appropriately, contributing to a more sustainable approach to military rations.
Unraveling the Mystery: Can 01 and 02 Plastics Be Recycled?
You may want to see also
Recycling Processes: Explore methods and challenges in recycling MRE plastic packaging
MRE (Meal, Ready-to-Eat) plastic packaging, commonly made from polypropylene (PP) and polyethylene (PE), presents unique challenges and opportunities in the recycling process. The first step in understanding the recyclability of MRE plastic is to recognize the materials used. MREs often contain a combination of PP and PE, which are both widely accepted in recycling streams. However, the structure and composition of MRE packaging can complicate the recycling process.
The primary challenge lies in the multi-layered nature of MRE packaging. These layers often include an inner PE layer for food contact, an aluminum foil layer for oxygen barrier properties, and an outer PP layer for structural integrity. Separating these layers during recycling is technically difficult and often not economically viable. As a result, mixed-plastic streams containing MRE packaging can lead to contamination, making it harder to process and recycle effectively.
One of the key methods to recycle MRE plastic is through mechanical recycling. This process involves shredding or granulating the MRE packaging into small pieces or pellets. However, the multi-layer structure can lead to issues with contamination and degradation of the material's quality. Advanced mechanical recycling techniques, such as using specialized shredders and washing processes, can help mitigate these problems. These processes aim to separate the different layers and clean the material to ensure it meets the required standards for reuse.
Chemical recycling offers another approach, particularly for MRE packaging with complex structures. This method involves breaking down the plastic into its base chemicals, which can then be used to produce new materials. For instance, PP can be chemically recycled to create new PP pellets, while PE can be converted into other valuable chemicals. While chemical recycling has the potential to handle the multi-layer structure of MRE packaging, it is currently more expensive and less widely available compared to mechanical recycling.
Despite the challenges, there are ongoing efforts and innovations in the recycling industry to improve the recyclability of MRE plastic. These include developing more efficient separation technologies, exploring new recycling pathways, and promoting the use of biodegradable or compostable materials in MRE packaging. Addressing the recycling of MRE plastic is crucial for reducing waste, conserving resources, and ensuring a more sustainable approach to food packaging.
Unraveling the Mystery: Can Plastic Fruit Containers Be Recycled?
You may want to see also
Environmental Impact: Assess the environmental benefits and drawbacks of recycling MRE plastics
The process of recycling MRE (Meal Ready-to-Eat) plastics, which are commonly used in military and emergency food packaging, can have both positive and negative environmental implications. On the positive side, recycling these plastics can significantly reduce the amount of waste that ends up in landfills or is incinerated, thus minimizing the environmental impact of these single-use items. MRE plastics are typically made from polyolefins, such as polyethylene (PE) and polypropylene (PP), which are known for their recyclability and relatively low environmental impact compared to other plastics. Recycling these materials can help conserve natural resources, as it reduces the need for virgin plastic production, which often relies on fossil fuels and can contribute to environmental degradation.
However, there are several drawbacks and challenges associated with recycling MRE plastics. Firstly, the recycling process itself can be energy-intensive and may require significant energy input, which could potentially offset some of the environmental benefits. Additionally, the recycling infrastructure for MRE plastics might not be as widely available as that for more common plastics like PET (polyethylene terephthalate), which can make the recycling process less accessible and efficient. Another concern is the potential for contamination, as MRE plastics often contain various additives and may be mixed with other materials, making their recycling more complex. This can lead to lower-quality recycled materials and potential environmental hazards if not managed properly.
The environmental benefits of recycling MRE plastics are particularly relevant in the context of military operations and emergency response, where these packages are commonly used. By implementing recycling programs, military organizations can reduce their environmental footprint and contribute to a more sustainable approach to waste management. This is especially important in remote or challenging environments where waste disposal options are limited. Furthermore, recycling MRE plastics can help divert waste from landfills, which can prevent the release of harmful greenhouse gases and reduce the overall environmental impact of military activities.
Despite the potential advantages, it is essential to consider the entire lifecycle of MRE plastics to gain a comprehensive understanding of their environmental impact. The initial production and transportation of these plastics may have their own ecological consequences, and the recycling process should be optimized to minimize energy consumption and waste generation. Additionally, educating consumers and organizations about proper waste management and recycling practices is crucial to ensuring the successful implementation of recycling programs for MRE plastics.
In summary, recycling MRE plastics can have a positive environmental impact by reducing waste and conserving resources, but it also presents challenges related to energy consumption, recycling infrastructure, and contamination. A holistic approach, considering the entire lifecycle and implementing efficient recycling practices, is necessary to maximize the benefits while mitigating the potential drawbacks. This ensures that the environmental impact of MRE plastics is minimized, contributing to a more sustainable and responsible waste management system.
Eco-Friendly Fashion: Unraveling the Environmental Impact of Recycled Plastic Clothing
You may want to see also
Consumer Awareness: Educate consumers on proper disposal and recycling practices for MRE plastics
MRE (Meal, Ready-to-Eat) plastics are a type of packaging commonly used for individual meals, especially in military and outdoor settings. These plastics are designed to be lightweight, durable, and easy to transport, making them ideal for field operations and emergency situations. However, like any plastic, MRE plastics can be challenging to recycle due to their composition and the potential for contamination. Educating consumers about proper disposal and recycling practices is crucial to ensure these materials are managed responsibly and do not contribute to environmental degradation.
The first step in proper disposal is understanding the types of plastics used in MRE packaging. MREs typically contain multiple layers of plastic, including a foil or aluminum layer, a plastic film, and sometimes a paper or cardboard component. The most common types of plastics used are polyethylene (PE) and polypropylene (PP). These plastics are generally recyclable, but their recyclability can vary depending on local recycling facilities and infrastructure. It is essential to check with your local waste management authority to understand the specific recycling guidelines for your area.
When disposing of MRE plastics, consumers should follow these steps: 1. Separate the different components of the packaging. For example, remove any foil or aluminum layers and separate the plastic film from any paper or cardboard inserts. 2. Clean the plastic components to remove any food residue or dirt. This step is crucial to prevent contamination, which can render the plastics unrecyclable. 3. Check if the local recycling center accepts MRE plastics. If not, consider alternative disposal methods, such as composting or ensuring the plastics are sent to a specialized recycling facility. 4. Dispose of the cleaned and separated components in the appropriate recycling streams. For example, PE and PP plastics can often be recycled through regular plastic recycling programs.
Recycling MRE plastics can be a bit more complex due to the potential for contamination and the need for specialized recycling processes. Here are some additional tips for consumers: - Always rinse MRE packaging to remove any food particles, ensuring that the plastics are clean and dry before recycling. - Flatten or crush the packaging to save space and make it easier for recycling facilities to process. - Avoid using MRE plastics for food storage or other purposes after disposal, as they may not be suitable for reuse. - If in doubt, contact your local recycling center or waste management authority for specific instructions on recycling MRE plastics.
By following these guidelines, consumers can play a vital role in promoting environmental sustainability. Proper disposal and recycling of MRE plastics can help reduce waste, conserve resources, and minimize the environmental impact of these convenient meal packages. It is a small but significant step towards a more sustainable future, ensuring that even in the most remote or challenging situations, responsible waste management practices can be maintained.
Plastic Recycling: A Guide to Environmental Impact and Action
You may want to see also
Industry Standards: Examine industry guidelines and regulations for MRE plastic recycling
Industry standards play a crucial role in determining the recyclability of MRE (Meal, Ready-to-Eat) plastic packaging. MREs are often packaged in flexible plastic pouches, which can be challenging to recycle due to their complex composition. Here's an overview of industry guidelines and regulations related to MRE plastic recycling:
Material Composition: MRE plastic pouches are typically made from a blend of polymers, including polyethylene (PE) and polypropylene (PP). These materials have different recycling properties. PE is widely accepted in recycling streams, while PP can be more problematic. Industry guidelines emphasize the importance of using recyclable materials and often set standards for the percentage of each polymer that should be included in the packaging. For instance, some regulations may require a minimum of 50% PE and 30% PP to ensure the material is recyclable.
Recycling Processes: The recycling process for MRE plastic is a critical aspect of industry standards. One common method is mechanical recycling, which involves shredding the pouches and processing them into new products. However, this process can be challenging due to the potential for contamination from food residue and other packaging materials. To address this, industry guidelines may specify cleaning and sorting procedures to ensure the plastic is clean and free from impurities before recycling. Advanced recycling techniques, such as chemical recycling, are also being explored to break down the polymers into their original components, offering a more comprehensive recycling solution.
Regulations and Standards: Various regulatory bodies and industry associations have established standards for MRE plastic recycling. For example, the European Union's Plastic Strategy includes specific guidelines for flexible packaging, encouraging the use of recyclable materials and providing frameworks for recycling processes. In the United States, the Food and Drug Administration (FDA) sets regulations for food contact materials, ensuring the safety and recyclability of MRE packaging. These regulations often mandate that manufacturers provide detailed information about the composition of their packaging, making it easier for recycling facilities to process the materials effectively.
Industry Collaboration: Collaboration between MRE manufacturers, recyclers, and environmental organizations is essential to establishing industry-wide standards. These partnerships can lead to the development of best practices and guidelines that ensure MRE plastic is recyclable and environmentally friendly. By sharing knowledge and resources, the industry can work towards creating a more sustainable recycling system.
Consumer Education: Industry standards also emphasize the importance of educating consumers about proper recycling practices. MRE packaging should include clear instructions on how and where to recycle, encouraging responsible disposal. Consumer awareness is vital in ensuring that MRE plastic reaches recycling facilities, where it can be processed and potentially reused.
Unraveling the Mystery: Can No. 6 Plastic Be Recycled?
You may want to see also
Frequently asked questions
MREs are a type of plastic composite material commonly used in packaging, particularly for beverage bottles and food containers. While MREs are not typically recyclable in standard recycling streams due to their complex structure, some recycling programs have specialized processes to handle these materials. It's best to check with your local recycling center or waste management authority to determine if they can process MREs.
Multi-layer Film (MLF) plastics, often used for shopping bags, wrappings, and bubble wrap, can be challenging to recycle due to their multi-layer structure. However, some recycling facilities have the capability to process MLF plastics. It's important to ensure that the MLF material is clean and dry before recycling, as contamination can hinder the recycling process.
Multi-Resin Plastic (MRP) bottles, also known as co-polyethylene (COP) or multi-layer PET bottles, are a blend of different types of plastic resins. These bottles can be recycled, but the process may vary depending on the recycling facility's capabilities. Some facilities can process MRP bottles, while others might require separating the different resin layers. It's advisable to contact your local recycling program to understand their specific guidelines for recycling MRP bottles.