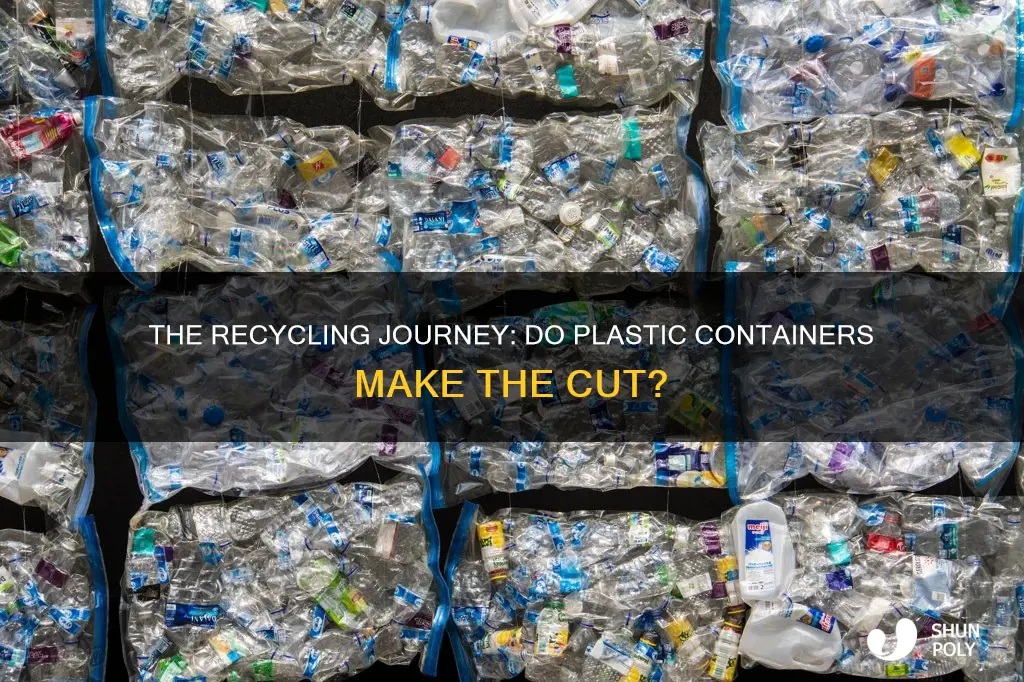
Plastic containers are a common household item, but their end-of-life journey is often unclear. Many people wonder if these containers can be recycled and what happens to them after they're discarded. This paragraph aims to shed light on the recycling process for plastic containers, exploring the challenges and opportunities in recycling these materials and providing insights into the current practices and potential improvements in the recycling industry.
Characteristics | Values |
---|---|
Recyclable Plastic Types | PET (Polyethylene Terephthalate), HDPE (High-Density Polyethylene), LDPE (Low-Density Polyethylene), PP (Polypropylene), PS (Polystyrene) |
Recycle Process | 1. Collection: Plastic containers are collected through recycling programs or drop-off locations. 2. Sorting: Materials are sorted by type and color. 3. Cleaning: Containers are cleaned to remove contaminants. 4. Shredding/Grinding: Plastic is shredded or ground into small pieces. 5. Melting: The plastic flakes are melted and formed into pellets. 6. Manufacturing: Pellets are used to create new products like fibers, containers, or other items. |
Challenges | - Contamination: Food residue, labels, and other materials can make recycling difficult. - Downcycling: Some plastics can only be recycled into lower-quality products. - Infrastructure: Recycling facilities and infrastructure vary by region. |
Environmental Impact | Recycling plastic containers reduces waste in landfills and incinerators, conserving resources and energy. However, the process is energy-intensive, and not all plastics are easily recycled. |
Consumer Responsibility | Properly disposing of plastic containers, cleaning them, and following local recycling guidelines is crucial for successful recycling. |
Alternatives | Reusable containers, glass, and metal are more sustainable options. |
What You'll Learn
- Collection and Sorting: Plastic containers are collected, sorted by type, and prepared for recycling
- Processing: Sorted containers are processed to remove contaminants and prepare for reuse
- Melting and Reforming: Plastic is melted and reformed into new products, reducing waste
- Quality Control: Recycled plastic is tested to ensure it meets quality standards for new products
- Market Demand: Consumer demand for recycled products drives the recycling process and sustainability
Collection and Sorting: Plastic containers are collected, sorted by type, and prepared for recycling
The process of recycling plastic containers begins with their collection, which is a crucial step in ensuring the effectiveness of the recycling program. Plastic waste is often collected through various means, including curbside recycling programs, drop-off centers, and specialized collection events. During these collection efforts, it is essential to separate plastic containers from other waste materials to facilitate the recycling process. This separation is typically done at the source, where individuals and businesses place their plastic waste into designated recycling bins or bags.
Once collected, the plastic containers undergo a sorting process to categorize them based on their type and resin identification code. This code, usually a number inside a triangle on the container's bottom, indicates the type of plastic used. Common types of plastic used in containers include PET (polyethylene terephthalate), HDPE (high-density polyethylene), and LDPE (low-density polyethylene). Sorting by type is essential because different plastics have varying recycling methods and compatibility with other materials. For instance, PET bottles are widely accepted in recycling streams, while HDPE containers might have more limited recycling options.
Advanced sorting techniques are employed to streamline the process and ensure accuracy. Optical scanners and infrared sensors are used to identify and separate different types of plastics. These technologies can detect the unique characteristics of each plastic type, such as color, shape, and resin code. Manual sorting, where trained personnel inspect and separate plastics, is also practiced in some facilities, especially for more complex or contaminated materials. The goal is to create clean and sorted streams of plastic, ensuring that each type is isolated for proper recycling.
After sorting, the plastic containers undergo additional preparation steps. This includes cleaning to remove any residual contaminants, such as food residue or labels, which can interfere with the recycling process. The containers may also be shredded or granulated to reduce their size and facilitate further processing. These prepared plastics are then ready for the next stage of recycling, where they are transformed into raw materials for manufacturing new products.
Efficient collection and sorting systems are vital to the success of plastic recycling programs. They ensure that the right plastics are directed to the appropriate recycling streams, reducing contamination and maximizing resource recovery. Public awareness and education play a significant role in promoting proper waste segregation at the source, which directly impacts the quality and quantity of materials available for recycling. By implementing comprehensive collection and sorting practices, communities can contribute to a more sustainable and circular economy, where plastic waste is minimized and valuable resources are conserved.
Strawberry Containers: Are They Recyclable? Unveiling the Truth
You may want to see also
Processing: Sorted containers are processed to remove contaminants and prepare for reuse
The process of recycling plastic containers begins with meticulous sorting, a crucial step to ensure the quality of the recycled material. Once sorted, the containers are carefully inspected to identify and remove any contaminants. This step is vital as it directly impacts the purity and value of the recycled plastic. Contaminants can include food residue, labels, and other non-plastic materials, which, if left in, can compromise the integrity of the final product.
After sorting and inspection, the containers are cleaned. This cleaning process varies depending on the type of plastic. For instance, PET (polyethylene terephthalate) bottles, commonly used for beverages, are often washed with water and sometimes a detergent solution to remove any remaining liquids or labels. HDPE (high-density polyethylene) containers, often used for milk and cleaning products, might be washed with a more aggressive cleaning agent to ensure a thorough removal of contaminants.
The next step in the processing is shredding or granulating the cleaned containers. Shredding involves breaking down the plastic into small pieces, which are then sorted by color and density. This step is crucial for creating a consistent and high-quality recycled material. Granulating, on the other hand, involves melting the plastic and then extruding it into small pellets, which can be used to create new products.
The shredded or granulated plastic is then dried to remove any remaining moisture, which can affect the quality of the final product. After drying, the material is often tested to ensure it meets the required standards for reuse. This testing may include checking for contaminants, measuring the thickness and color consistency, and assessing the material's physical properties.
Finally, the processed plastic is ready for reuse. It can be used to create a wide range of products, from new containers and packaging to furniture, construction materials, and even clothing. This process not only reduces the demand for new plastic production but also minimizes the amount of plastic waste that ends up in landfills or the environment, contributing to a more sustainable and circular economy.
Uncovering the Financial Incentives for Plastic Recycling
You may want to see also
Melting and Reforming: Plastic is melted and reformed into new products, reducing waste
The process of recycling plastic containers involves a fascinating technique known as melting and reforming, which plays a crucial role in reducing waste and promoting sustainability. This method is an effective way to give new life to used plastic materials, ensuring they are transformed into valuable resources rather than ending up in landfills.
When plastic containers are collected for recycling, they undergo a meticulous process. The first step is sorting, where different types of plastics are separated to ensure compatibility with the recycling process. This is essential because not all plastics can be recycled together, and proper sorting prevents contamination. Once sorted, the plastic containers are cleaned to remove any residual contaminants, such as food particles or labels, which could hinder the recycling process.
The cleaned plastic containers are then shredded or granulated into small pieces. This step is crucial as it prepares the plastic for the melting process. The shredded plastic is fed into a specialized machine called a pelletizer, which melts the plastic and forms it into small, uniform pellets. These pellets are essentially the raw material for creating new products. The melting and reforming process involves heating the plastic to its melting point, typically around 200-300 degrees Celsius, depending on the type of plastic. This temperature varies for different polymers, ensuring that the plastic is not damaged during the recycling process.
After melting, the plastic is reformed into new products through various manufacturing techniques. One common method is injection molding, where the molten plastic is injected into a mold to create the desired shape. This process allows for the production of a wide range of items, including furniture, automotive parts, and even new plastic containers. The reformed plastic products can then be sold or used in various industries, reducing the demand for virgin plastic production.
This recycling process is an eco-friendly alternative to traditional disposal methods, as it minimizes the environmental impact of plastic waste. By melting and reforming plastic, we can reduce the amount of plastic pollution, conserve natural resources, and decrease the reliance on non-renewable materials. Additionally, this process creates a closed-loop system, where used plastic is transformed into new products, reducing the overall waste generated.
In summary, the melting and reforming process is a vital step in the recycling journey of plastic containers. It showcases the potential for waste reduction and the creation of valuable resources. Through this method, we can actively contribute to a more sustainable future, ensuring that plastic waste is given a new purpose and reducing its environmental footprint.
Sustainable Gardening: Can Plastic Seed Trays Be Recycled?
You may want to see also
Quality Control: Recycled plastic is tested to ensure it meets quality standards for new products
The process of recycling plastic containers is a crucial step in promoting sustainability and reducing environmental impact. Once collected, these containers undergo a rigorous quality control process to ensure that the recycled plastic meets the necessary standards for reuse in new products. This testing is essential to guarantee the integrity and performance of the recycled material, providing consumers with reliable and safe products.
Quality control for recycled plastic involves several key steps. Firstly, the plastic waste is sorted and classified based on its type and quality. Different types of plastic, such as PET, HDPE, and LDPE, have varying properties and uses, so proper sorting is crucial. This initial step ensures that the recycled material is categorized appropriately for its intended applications.
After sorting, the plastic is cleaned and processed to remove any contaminants. This includes removing labels, caps, and other non-plastic components, as well as cleaning the plastic to eliminate dirt, debris, and residual chemicals. Thorough cleaning is vital to prevent the introduction of impurities that could affect the final product's quality.
The next phase involves testing the recycled plastic for its physical and chemical properties. This includes assessing its color, transparency, and overall appearance, ensuring it meets the required standards. Mechanical tests are also conducted to evaluate the plastic's strength, flexibility, and durability. These tests might include impact resistance, tensile strength, and flexibility tests to determine the material's performance.
Chemical analysis is another critical aspect of quality control. Recycled plastic is tested for its chemical composition to ensure it is free from harmful contaminants and meets regulatory standards. This process involves sophisticated laboratory techniques to identify and quantify various chemicals, ensuring the recycled material is safe and suitable for consumer use.
Furthermore, the recycled plastic is often subjected to additional tests to assess its compatibility with other materials and its performance in specific applications. This comprehensive testing ensures that the recycled plastic can be successfully integrated into new products without compromising their quality or functionality. By adhering to these rigorous quality control measures, the recycling industry can deliver high-quality recycled plastic, contributing to a more sustainable and environmentally friendly future.
Eco-Friendly Choice: Compostable or Recyclable? The Ultimate Cup Comparison
You may want to see also
Market Demand: Consumer demand for recycled products drives the recycling process and sustainability
Consumer demand for recycled products has become a powerful force in driving the recycling process and promoting sustainability. As environmental awareness grows, so does the desire for consumers to make eco-conscious choices. This shift in consumer behavior has led to a significant increase in the demand for recycled materials, including plastic containers.
In recent years, the market has witnessed a surge in the availability of recycled plastic products. From reusable water bottles and food containers to packaging materials, consumers are actively seeking out items made from recycled content. This trend is not just a passing fad but a conscious effort to reduce waste and support sustainable practices. As a result, businesses are responding to this market demand by incorporating recycled materials into their production processes.
The rise in consumer demand for recycled products has several positive impacts. Firstly, it encourages manufacturers to adopt more sustainable practices. By using recycled plastic containers, companies can reduce their reliance on virgin resources, minimize waste, and lower their environmental footprint. This shift in production methods contributes to a more circular economy, where materials are reused and recycled, reducing the strain on natural resources.
Secondly, consumer demand for recycled goods creates a financial incentive for recycling. When consumers actively seek out and purchase recycled products, it becomes economically viable for recycling facilities to operate. This, in turn, leads to increased recycling rates and improved infrastructure for processing and sorting recycled materials. As the demand for recycled plastic containers grows, so does the efficiency and accessibility of recycling processes.
Moreover, consumer awareness and preference for sustainable products have a ripple effect on the entire supply chain. It encourages the development of innovative recycling technologies and processes, ensuring that recycled materials meet the required standards and quality. This includes advancements in sorting, cleaning, and transforming recycled plastics into usable forms. As a result, the market becomes more responsive to the needs of both consumers and the environment.
In summary, consumer demand for recycled products plays a pivotal role in driving the recycling process and fostering sustainability. It empowers individuals to make a positive impact on the environment through their purchasing choices. By supporting recycled plastic containers and similar products, consumers contribute to a greener economy, encouraging businesses to adopt eco-friendly practices and driving the continuous improvement of recycling systems. This market-driven approach is essential in the journey towards a more sustainable future.
Eco-Friendly Wheelie Bins: Unveiling the Recycled Plastic Revolution
You may want to see also
Frequently asked questions
Yes, plastic containers are widely accepted in recycling programs. Many cities and municipalities have specific guidelines for recycling plastic, often categorizing it by type (e.g., PET, HDPE) to ensure proper processing.
Once collected, plastic containers undergo a series of processes. They are first sorted by type and color, then cleaned to remove contaminants. After cleaning, the plastic is shredded or ground into small pieces called 'flakes'. These flakes are then melted and molded into new products, such as new containers, clothing, or even car parts.
Not all plastic containers are created equal. The recycling symbol on the bottom of a container, often referred to as the resin identification code, indicates the type of plastic it is made from. Common types include PET (1), HDPE (2), and PP (5). Some plastics, like polystyrene (6) and certain types of plastic bags, may have limited recycling options and are often not accepted in standard recycling programs. It's best to check with your local recycling guidelines to ensure proper disposal.