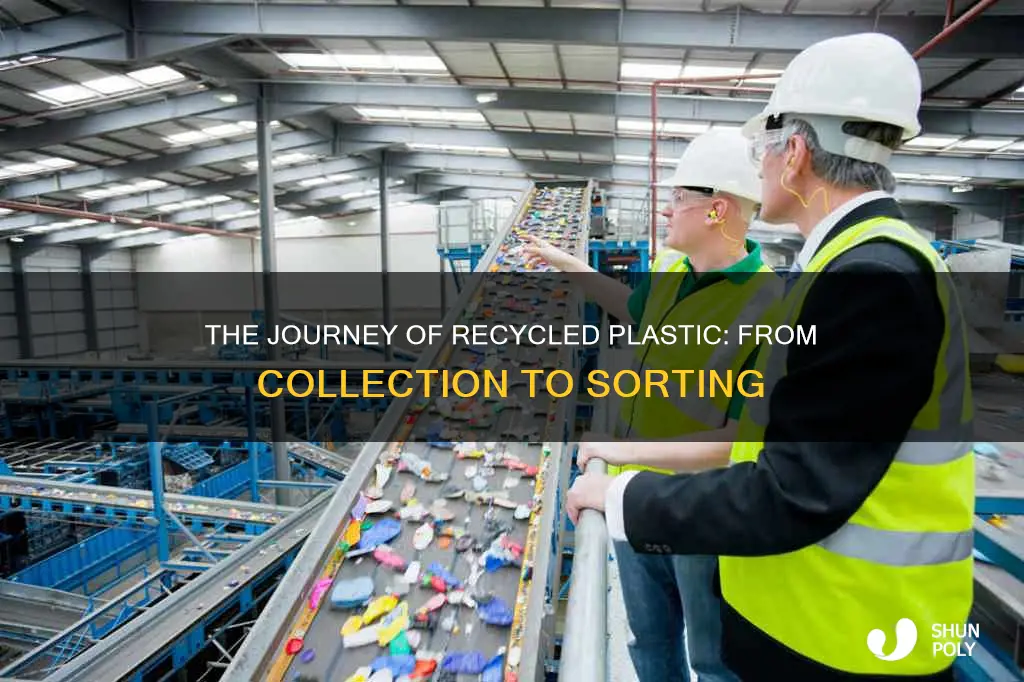
The process of recycling plastic involves a complex journey from collection to transformation. Once plastic waste is gathered, it undergoes a meticulous sorting process to separate different types of plastic materials. This crucial step ensures that each type of plastic can be recycled effectively and efficiently, contributing to a more sustainable and environmentally friendly approach to waste management.
What You'll Learn
- Sorting Process: Mechanical separation, manual sorting, and optical scanners
- Material Identification: Identifying different types of plastic resins
- Quality Control: Inspecting and rejecting contaminated or damaged plastic
- Recycling Streams: Creating separate streams for different plastic types
- End-Use Applications: Determining the recycled plastic's suitability for specific products
Sorting Process: Mechanical separation, manual sorting, and optical scanners
The process of sorting recycled plastic is a crucial step in the journey from waste to new products, ensuring that the right materials are directed to the appropriate recycling streams. This sorting process involves various methods, each playing a vital role in separating different types of plastic, metals, and other materials. Here, we delve into the mechanical separation, manual sorting, and the use of optical scanners in this intricate process.
Mechanical Separation: This method is often the first line of defense in recycling facilities. It involves the use of machines to separate materials based on their physical properties. For plastic recycling, this typically includes a process called 'air classification.' Plastic waste is fed into a machine, where it is separated into different streams based on density. Lighter materials, such as plastic films and bags, are directed to one side, while denser items like bottles and containers go to another. This mechanical separation is efficient and can handle large volumes of waste, making it a cornerstone of modern recycling operations.
Manual Sorting: Despite the advancements in technology, manual sorting remains an essential part of the process, especially for specialized and complex recycling streams. Skilled workers carefully examine the sorted materials, identifying and separating items that might have been missed by mechanical processes. This step is crucial for ensuring the purity of the recycled materials. For instance, manual sorting can be used to separate different types of plastic, like PET (polyethylene terephthalate) and HDPE (high-density polyethylene), which have distinct characteristics and recycling requirements. Workers may also remove contaminants, such as non-plastic items or heavily soiled materials, ensuring that the final product meets quality standards.
Optical Scanners: In the realm of recycling, optical scanners are powerful tools that utilize light to identify and separate materials. These scanners are particularly useful for distinguishing between different types of plastics, which often have similar physical properties. By shining light onto the waste stream, these scanners can detect the unique light absorption and reflection patterns of each plastic type. For example, a scanner can identify PET bottles by recognizing their distinct spectral signature. This technology is highly accurate and can process large quantities of material quickly, making it an indispensable asset in modern recycling facilities. Optical scanners often work in conjunction with other sorting methods, providing an additional layer of precision to the overall process.
The sorting process is a complex and intricate dance, where each step contributes to the successful separation of materials. Mechanical separation lays the foundation with its efficiency, manual sorting adds a human touch to ensure quality, and optical scanners provide the precision needed to identify the most challenging materials. Together, these methods ensure that recycled plastic can be transformed into new products, contributing to a more sustainable and circular economy.
Eco-Friendly Blooms: Recycled Plastic's Role in Artificial Flowers
You may want to see also
Material Identification: Identifying different types of plastic resins
The process of recycling plastic is a complex journey, and at its core lies the crucial task of material identification. This process is essential to ensure that the right types of plastic resins are sorted and recycled appropriately, preventing contamination and maximizing the efficiency of the recycling stream. Here's an in-depth look at how this identification process works:
Understanding Plastic Resins: Plastic, often referred to as a single material, is actually a diverse group of polymers. Each type of plastic has unique properties, such as strength, flexibility, and chemical composition, which are determined by the specific resin used. Common plastic resins include Polyethylene Terephthalate (PET), High-Density Polyethylene (HDPE), Polyvinyl Chloride (PVC), Low-Density Polyethylene (LDPE), Polypropylene (PP), and Polystyrene (PS). Each resin has a unique number, known as the Resin Identification Code (RIC), which is a crucial identifier for sorting.
Resin Identification Codes (RIC): The RIC system is a universal coding system used to identify different types of plastic resins. These codes are typically found on the bottom of plastic containers and products. Here's a breakdown of the RICs:
- PET (1): Commonly used for beverage bottles, food containers, and some packaging.
- HDPE (2): Widely used for milk jugs, detergent bottles, and shopping bags.
- PVC (3): Found in construction materials, pipes, and some packaging.
- LDPE (4): Used for grocery bags, film, and some flexible packaging.
- PP (5): Common in food containers, bottle caps, and some packaging.
- PS (6): Used for disposable cups, food containers, and packaging.
- Other codes (7 and beyond): These are for specialized resins or blends that may not be widely recycled.
Sorting Process: When recycled plastic materials are collected, they are first sorted by type using a combination of manual and automated methods. Manual sorting involves trained personnel who visually inspect and identify the plastic types based on their appearance, feel, and knowledge of RICs. Automated sorting uses advanced technologies such as near-infrared (NIR) spectroscopy, which can identify different resins based on their unique molecular structures. This automated process is highly efficient and accurate, ensuring that the right materials are directed to the appropriate recycling streams.
Benefits of Accurate Identification: Proper material identification is crucial for several reasons. Firstly, it ensures that each type of plastic is recycled correctly, maintaining the integrity of the recycling process. For example, PET and HDPE have different melting points and properties, and recycling them together can lead to contamination and reduced product quality. Secondly, accurate identification helps in the development of specialized recycling processes for specific resins, improving the overall efficiency of recycling operations.
Challenges and Solutions: One of the challenges in material identification is the presence of plastic blends and compounds, which may contain multiple resins. Advanced sorting techniques, such as density separation and chemical analysis, can help identify and separate these complex mixtures. Additionally, educating the public about proper recycling practices and providing clear guidelines on what types of plastics are accepted for recycling can significantly improve the accuracy of material identification at the source.
Unraveling the Mystery: Can Plastic Litter Pans Be Recycled?
You may want to see also
Quality Control: Inspecting and rejecting contaminated or damaged plastic
In the realm of recycling, ensuring the quality of recycled materials is paramount to maintaining efficiency and sustainability. When it comes to plastic recycling, quality control is a critical process that involves meticulous inspection and rejection of contaminated or damaged materials. This process is essential to prevent the spread of contaminants and maintain the integrity of the recycling stream.
The inspection process begins with a thorough visual examination of the plastic materials. Trained personnel carefully analyze each batch for any signs of contamination, such as food residue, labels, or non-plastic items. Contaminated plastic can render the entire batch unsuitable for recycling, as it may lead to cross-contamination and affect the quality of the recycled product. For instance, food-grade plastic should not be mixed with non-food-grade materials to avoid potential health risks.
One effective method for quality control is the use of specialized equipment like near-infrared (NIR) spectrometers. These devices can rapidly identify the type of plastic and detect any impurities or additives. By analyzing the unique absorption patterns of different plastics, NIR spectrometers can provide quick and accurate assessments, ensuring that only pure and suitable materials progress through the recycling process.
Rejected materials, which include contaminated or damaged plastic, are carefully segregated and disposed of appropriately. This step is crucial to prevent the reintroduction of contaminants into the recycling stream. Proper disposal methods may involve incineration, landfilling, or specialized treatment processes to ensure environmental safety. Additionally, rejected materials can be further analyzed to identify the root causes of contamination, allowing for process improvements and better waste management strategies.
Furthermore, quality control extends beyond the inspection stage. It also involves implementing strict protocols for handling and storing rejected materials. Proper labeling and segregation of contaminated plastic ensure that it is managed separately from clean and reusable materials. This practice prevents the potential spread of contaminants to other recycling streams and promotes a more organized and efficient recycling system.
Unzip the Mystery: Can Plastic Zip Pouches Be Recycled?
You may want to see also
Recycling Streams: Creating separate streams for different plastic types
In the realm of recycling, creating distinct streams for various plastic types is a crucial practice that significantly enhances the efficiency and effectiveness of the recycling process. This approach is essential to ensure that each plastic material is recycled appropriately, maximizing its value and minimizing environmental impact. Here's an in-depth look at why and how this system works:
The Importance of Separate Streams:
When recycled plastics are not sorted, they can become a mixed bag of materials, leading to contamination and reduced quality. For instance, combining PET (polyethylene terephthalate) bottles, which are commonly used for beverages, with HDPE (high-density polyethylene) containers, often used for milk and cleaning products, can result in cross-contamination. This mixing can lead to the degradation of the recycled material's quality, making it less desirable for manufacturers and potentially leading to downcycling or even waste. By creating separate streams, we can prevent such issues and ensure that each type of plastic is recycled in the most suitable manner.
Implementing Separate Streams:
The process begins with consumer education and awareness. Informing the public about the different types of plastics and their respective recycling symbols is vital. For example, PET bottles are typically identified by the recycling symbol of a triangle with a number 1 inside, while HDPE containers are marked with a number 2. This knowledge empowers individuals to sort their plastics accordingly. Local governments and waste management companies can play a pivotal role here by providing clear guidelines and resources to facilitate proper sorting.
Sorting Facilities and Infrastructure:
Once sorted at the household level, plastics are directed to specialized recycling facilities. These facilities employ advanced sorting technologies, such as optical sorters and eddy current separators, to efficiently separate different plastic types. Optical sorters use light to identify colors and types, while eddy current separators detect the conductivity of materials, allowing for the separation of metals and non-metals. This meticulous sorting ensures that each plastic type is handled separately, maintaining its integrity.
Benefits of Stream Separation:
- Enhanced Quality: Sorted streams result in higher-quality recycled plastics, which are more valuable to manufacturers. This can lead to the production of better products and potentially reduce the environmental impact of plastic production.
- Reduced Contamination: By keeping plastics separate, the risk of cross-contamination is minimized, ensuring that the recycled material meets the required standards.
- Increased Recycling Rates: Effective sorting can lead to higher recycling rates, as more plastics are properly processed and reused.
- Environmental Impact: Proper sorting reduces the need for downcycling, which often results in lower-quality products. It also minimizes the environmental impact associated with the production and disposal of mixed plastics.
Creating separate streams for different plastic types is a critical step in the recycling process, ensuring that each material is recycled efficiently and effectively. It empowers individuals to take an active role in recycling, while specialized facilities and technologies handle the sorting process with precision. This approach not only benefits the environment but also contributes to a more sustainable and circular economy, where recycled materials are valued and utilized to their full potential.
Unraveling the Mystery: Can Plastic Blister Packs Be Recycled?
You may want to see also
End-Use Applications: Determining the recycled plastic's suitability for specific products
When it comes to recycling plastic, the end-use applications play a crucial role in determining the suitability of recycled materials. The process of sorting and processing recycled plastic is a complex one, and the final product's performance and quality depend on the specific requirements of the intended application. Here's an overview of how to assess the suitability of recycled plastics for various end-use products:
- Understanding Product Requirements: Begin by thoroughly understanding the specifications and requirements of the product you intend to manufacture. Different products have unique physical, chemical, and mechanical properties needed to function optimally. For instance, a product requiring high impact resistance, like a children's toy, will have different criteria than a product needing flexibility, such as a flexible packaging film. Knowing these requirements is essential to ensure the recycled plastic meets the necessary standards.
- Material Testing and Analysis: Conduct comprehensive testing and analysis of the recycled plastic to evaluate its properties. This includes assessing its mechanical properties (tensile strength, impact resistance, flexibility), thermal stability, chemical composition, and color. Advanced techniques like Fourier-Transform Infrared Spectroscopy (FTIR) can be employed to identify the types of polymers present in the recycled material. This analysis will help determine if the plastic is suitable for the desired application.
- Sorting and Processing for Specific Applications: The recycling process should be tailored to the end-use application. For example, if the goal is to produce a high-impact plastic for automotive parts, the recycled plastic should be sorted and processed to remove contaminants and ensure a consistent material. This might involve additional washing, drying, and pelletizing processes to enhance the material's properties. Similarly, for flexible packaging, the focus could be on maintaining the plastic's flexibility and processability.
- Quality Control and Consistency: Establishing a robust quality control system is vital to ensure consistency in the recycled plastic products. This includes regular testing of the final products to verify that they meet the required specifications. Consistency is key, especially in industries where product performance and safety are critical, such as automotive or medical device manufacturing.
- Case Studies and Industry Standards: Researching case studies and industry standards specific to your target application can provide valuable insights. Many industries have developed guidelines and standards for using recycled materials, ensuring their performance and safety. Adhering to these standards can help manufacturers gain acceptance and trust in the market.
By carefully considering the end-use applications and tailoring the recycling process accordingly, it is possible to produce recycled plastic that meets the specific requirements of various products, contributing to a more sustainable and circular economy. This approach ensures that recycled materials are not just sorted but also optimized for their intended purposes.
Unraveling the Mystery: Can Plastic Labels Be Recycled?
You may want to see also