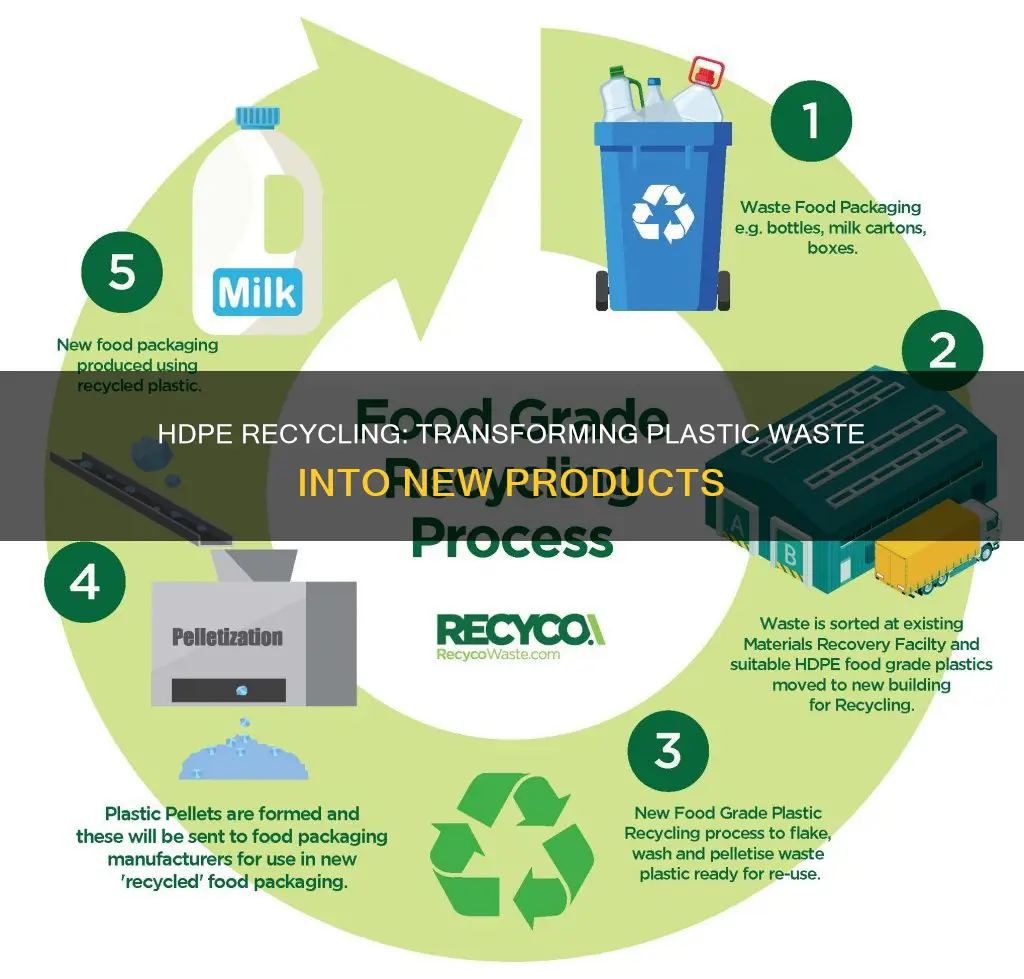
HDPE, or High-Density Polyethylene, is a common plastic widely used in various products, from milk jugs to shampoo bottles. Recycling HDPE is an important process to reduce waste and environmental impact. The recycling process begins with collecting used HDPE items, which are then sorted and cleaned to remove any contaminants. After cleaning, the HDPE is shredded into small pieces called flakes. These flakes are further processed through a washing and drying process to remove any remaining impurities. The cleaned HDPE flakes are then melted and extruded into pellets, which can be used as raw materials for manufacturing new products, such as plastic furniture, outdoor gear, and even new HDPE containers. This recycling process not only helps conserve natural resources but also reduces the amount of plastic waste ending up in landfills or the environment.
What You'll Learn
- Collection: HDPE is gathered from various sources like recycling bins and waste streams
- Sorting: Materials are sorted by color and type to ensure efficient processing
- Cleaning: Contaminants are removed to prepare HDPE for further recycling
- Shredding: HDPE is shredded into small pieces for easier processing
- Melting and Reforming: The shredded HDPE is melted and reformed into new products
Collection: HDPE is gathered from various sources like recycling bins and waste streams
The collection process for HDPE (High-Density Polyethylene) is a crucial step in recycling this widely used plastic. HDPE is commonly found in various household and commercial waste streams, making it easily accessible for recycling efforts. One of the primary sources of HDPE collection is recycling bins, which are strategically placed in public spaces, residential areas, and offices. These bins are designed to separate HDPE from other types of plastics and general waste, ensuring that it can be effectively recycled. Residents and businesses are encouraged to sort their waste and place HDPE items, such as milk jugs, detergent bottles, and shopping bags, into these designated bins.
In addition to recycling bins, waste streams generated by manufacturing and commercial activities also contribute significantly to HDPE collection. Industrial processes often produce HDPE waste, including scrap materials, offcuts, and by-products. These waste streams can be collected from factories, warehouses, and distribution centers, ensuring that HDPE is not discarded but instead becomes a valuable resource. Specialized collection services or partnerships with industrial facilities can facilitate the efficient gathering of HDPE from these sources.
Another essential aspect of HDPE collection is the implementation of waste management systems that encourage proper disposal. Educating the public about the importance of recycling and providing clear guidelines for waste segregation can significantly increase HDPE collection rates. Local governments and recycling organizations can play a vital role in promoting awareness campaigns and ensuring that HDPE is consistently and correctly placed in recycling bins. This collective effort helps to streamline the collection process and reduces the contamination of HDPE with other materials.
Furthermore, the collection process may involve specialized equipment and vehicles designed to handle HDPE efficiently. These vehicles are equipped to sort and separate HDPE from other recyclables, ensuring that it is clean and ready for the next stage of recycling. The collected HDPE is then transported to recycling facilities, where it undergoes further processing to be transformed into new products.
In summary, the collection of HDPE from recycling bins and waste streams is a critical component of the recycling process. By encouraging proper waste segregation, utilizing specialized collection methods, and engaging various stakeholders, HDPE can be effectively gathered and recycled, contributing to a more sustainable and environmentally friendly approach to plastic waste management.
Unraveling the Mystery: Can Plastic Milk Cartons Be Recycled in the UK?
You may want to see also
Sorting: Materials are sorted by color and type to ensure efficient processing
The initial step in the recycling process of HDPE (High-Density Polyethylene) and other plastics is sorting, a critical phase that significantly impacts the efficiency and quality of the recycling stream. This sorting process is designed to separate materials based on their type and color, ensuring that each category is handled appropriately for the next stage of recycling. The primary goal is to streamline the recycling process, making it more effective and environmentally friendly.
Color-based sorting is a common practice in recycling facilities. HDPE, for instance, is typically found in two primary colors: clear and white. Clear HDPE is often associated with containers like water bottles, while white HDPE is commonly used for items like milk jugs and detergent bottles. By sorting these materials by color, recyclers can direct them to the appropriate processing lines, ensuring that each type of plastic is treated with the right methods. This precision in sorting is crucial because different colors of HDPE may have varying chemical compositions, which can affect the recycling process.
Type-based sorting is equally important. HDPE is a versatile plastic used in a wide range of products, including bottles, containers, and even some packaging materials. By categorizing these items by their intended use or type, recyclers can optimize the recycling process. For example, bottles and containers made from HDPE are often sorted separately from HDPE packaging materials. This separation ensures that the recycling process can be tailored to the specific properties of each type of HDPE, improving the overall efficiency and quality of the recycled material.
Advanced sorting techniques are employed to enhance the accuracy and speed of this process. Optical sorters, for instance, use sensors to identify and separate materials based on color and type. These machines can quickly analyze the composition of each item, ensuring that only the desired materials are directed to the appropriate streams. This level of precision is essential in large-scale recycling operations, where the volume of materials can be immense, and the need for efficient processing is critical.
In summary, the sorting process is a fundamental step in the recycling journey of HDPE and other plastics. By separating materials by color and type, recyclers can optimize the recycling process, ensuring that each category of plastic is processed efficiently and effectively. This meticulous approach to sorting contributes to the overall sustainability of recycling efforts, making it an essential practice in the management of plastic waste.
Can California Recycle Plastic Milk Containers? Unveiling the Truth
You may want to see also
Cleaning: Contaminants are removed to prepare HDPE for further recycling
The cleaning process is a critical step in recycling HDPE (High-Density Polyethylene) to ensure the material is of high quality and suitable for reuse. HDPE is a common plastic used in various products, including milk jugs, shampoo bottles, and shopping bags. Before it can be recycled, HDPE must undergo a thorough cleaning process to remove contaminants that could compromise the material's integrity and value.
The initial step in cleaning HDPE involves removing any labels or non-HDPE components attached to the plastic. Labels, often made of paper or a different type of plastic, can be separated using a process called "label removal." This process may involve soaking the HDPE in a chemical solution to dissolve the adhesive that holds the label in place or using mechanical methods to peel off the labels. Once the labels are removed, the HDPE is ready for the next stage.
Contaminants, such as food residue, dirt, and other debris, are then eliminated through a process known as "washing." HDPE is placed in a washing machine or a specialized cleaning system, where it undergoes a series of steps to remove impurities. The washing process typically includes several cycles of cleaning with hot water and detergents or surfactants to break down and wash away any remaining contaminants. This step is crucial to ensure that the HDPE is clean and free from any harmful substances that could affect its recyclability or future use.
After washing, the HDPE may undergo additional processes to further refine the material. This can include drying the HDPE to remove any remaining moisture, which can be achieved through various methods such as air drying or using specialized dryers. Drying is essential to prevent the HDPE from absorbing moisture from the air, which could lead to mold growth or other issues during storage and processing.
Once the HDPE has been thoroughly cleaned and dried, it is ready for further recycling processes. The cleaned HDPE can be shredded into small pieces, known as "flakes," which are then sorted and classified based on their color and quality. These flakes can be used to create new HDPE products, such as new bottles, containers, or even new HDPE-based materials for construction or manufacturing. The cleaning process is a vital part of the recycling journey, ensuring that HDPE can be effectively reused and contributing to a more sustainable approach to plastic waste management.
Crocs' Plastic Recycling Journey: A Sustainable Step Forward
You may want to see also
Shredding: HDPE is shredded into small pieces for easier processing
The process of recycling HDPE (High-Density Polyethylene) begins with the collection of used HDPE products, such as milk jugs, shampoo bottles, and grocery bags. These items are then sorted and cleaned to ensure they are free from contaminants and ready for recycling. Once sorted, the HDPE materials are prepared for the shredding process, which is a crucial step in the recycling journey.
Shredding is an essential mechanical process that transforms HDPE into smaller, more manageable pieces. This step is designed to increase the surface area of the HDPE material, making it easier to process and recycle. The shredding process involves feeding the HDPE items into a specialized machine, often a shredder or granulator, which cuts and chops the plastic into tiny fragments. These fragments are typically in the form of flakes or pellets, which are easier to handle and transport compared to the original HDPE products.
The shredding process is carefully controlled to ensure the HDPE is shredded to the desired size. This size reduction is vital because it allows for better mixing and blending during the recycling process. Smaller pieces provide a larger surface area, facilitating more efficient chemical reactions and ensuring a higher-quality recycled product. The shredded HDPE material is then cleaned further to remove any remaining contaminants, such as labels or non-HDPE components, which could interfere with the recycling process.
After shredding, the HDPE flakes are often washed to eliminate any residual dirt or impurities. This washing step is crucial to ensure the recycled HDPE meets the required quality standards. The cleaned HDPE flakes are then dried to remove any moisture, which can affect the recycling process and the final product's performance. Once dried, the HDPE flakes are ready for the next stage of recycling, where they will be melted, blended, and formed into new products, completing the recycling loop.
Shredding is a critical step in the HDPE recycling process, as it prepares the material for subsequent stages, ensuring a more efficient and effective recycling cycle. This process not only reduces the volume of HDPE waste but also contributes to the production of new, high-quality products, promoting a more sustainable approach to plastic recycling.
Unraveling NYC's Plastic Recycling Mystery: Can Number 5 Be Recycled?
You may want to see also
Melting and Reforming: The shredded HDPE is melted and reformed into new products
The process of recycling HDPE (High-Density Polyethylene) involves several stages, and one of the key steps is melting and reforming the shredded HDPE material. This method is commonly used to create new products from the recycled plastic, offering a sustainable alternative to virgin HDPE. Here's an overview of this crucial phase in HDPE recycling:
Shredding and Sorting: The recycling journey begins with collecting HDPE waste, which can include items like milk cartons, shampoo bottles, and plastic containers. These items are then sorted to ensure only HDPE is processed, as it is the desired plastic type for recycling. After sorting, the HDPE items are shredded into small pieces, often in the form of flakes or pellets. This step reduces the size of the plastic, making it easier to handle and process further.
Melting Process: The shredded HDPE is then fed into a melting machine, typically a single-screw or twin-screw extruder. In this process, the plastic is heated to its melting point, which is around 230-260°C (446-500°F) for HDPE. The heat and mechanical action of the extruder melt the HDPE flakes, transforming them into a molten state. This molten HDPE is now ready for further processing and reformation.
Reformulation and Shaping: Once melted, the HDPE material is often mixed with other additives and pigments to enhance its properties or give it a specific color. This mixture is then extruded through a die, which shapes it into the desired form. For example, it can be extruded into pellets, which are essentially small, uniform pieces of HDPE. These pellets can then be used as a raw material for manufacturing various products. Alternatively, the molten HDPE can be directly molded into new containers, toys, or other items, depending on the intended application.
This melting and reforming process is a critical aspect of HDPE recycling as it allows for the creation of new products with the same quality and characteristics as those made from virgin HDPE. It showcases the potential of recycling to reduce waste and provide a sustainable solution for plastic production. By reforming the shredded HDPE, manufacturers can contribute to a circular economy, minimizing the environmental impact of plastic waste.
Are Melissa Campana Shoes Eco-Friendly? Unveiling the Recycled Plastic Mystery
You may want to see also
Frequently asked questions
HDPE is a type of plastic commonly used in various products like milk jugs, detergent bottles, and shopping bags. Recycling HDPE is crucial because it helps reduce waste, conserve resources, and minimize environmental impact.
The recycling process begins with collecting HDPE waste, which is then sorted and cleaned. The sorted HDPE is shredded or granulated into small pieces. These pieces are melted and molded into new products, such as outdoor furniture, park benches, or new containers.
Yes, it is essential to rinse HDPE containers to remove any residue or contaminants. Flatten or crush the containers to save space and make them easier to transport. Ensure that only HDPE items are placed in the recycling bin, as mixing different plastics can complicate the recycling process.
Recycled HDPE can be used in numerous applications. It is often transformed into new containers, such as water bottles, shampoo bottles, and detergent jugs. It can also be utilized in manufacturing outdoor items like playground equipment, picnic tables, and landscaping products, promoting sustainability and reducing the demand for new raw materials.
While HDPE is widely recyclable, there are some challenges. Not all HDPE products are accepted in curbside recycling programs, and some may have complex structures that make recycling difficult. Additionally, the recycling process can be energy-intensive, and the quality of recycled HDPE may vary, affecting its usability in certain applications.