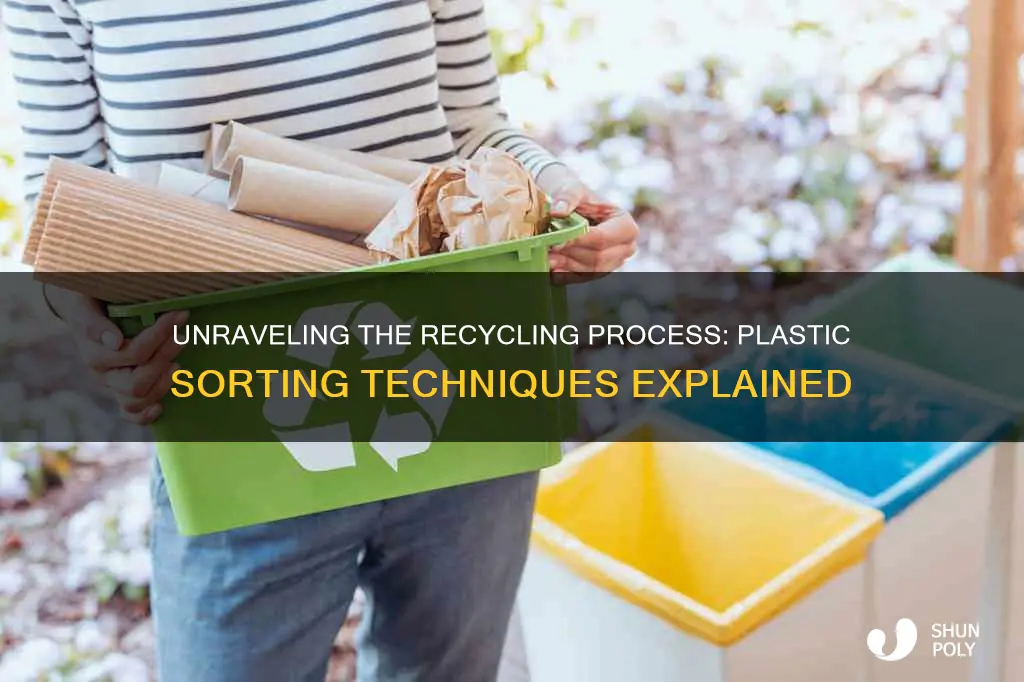
The process of recycling plastics is a complex and crucial step in sustainable waste management. Different types of plastics require specific methods for separation to ensure effective recycling. This paragraph will explore the various techniques employed to distinguish and categorize various plastic materials, highlighting the importance of accurate sorting in the recycling process. From manual inspection to advanced technologies, the methods used to separate plastics are essential for the successful recycling of these materials and the reduction of environmental impact.
Characteristics | Values |
---|---|
Plastic Type | PET (Polyethylene Terephthalate), HDPE (High-Density Polyethylene), LDPE (Low-Density Polyethylene), PP (Polypropylene), PS (Polystyrene), PVC (Polyvinyl Chloride), and others. |
Resin Identification Code (RIC) | A numerical code (1-7) used to identify the plastic type. For example, PET has a RIC of 1, HDPE is 2, and so on. |
Melting Point | Different plastics have varying melting points, which can be used for separation. For instance, PET melts around 250-260°C, while HDPE melts at 130-140°C. |
Density | Plastic density varies, with PET being one of the lightest at around 0.91 g/cm³, while HDPE is denser at 0.93 g/cm³. |
Color | Some plastics are color-coded, like PET, which is often clear or slightly tinted. Others may be colored, aiding in identification. |
Flexibility | PET is rigid, while LDPE and HDPE are flexible. This property can help in manual sorting. |
Brittleness | PS (Polystyrene) can be brittle, making it distinguishable from more flexible plastics. |
Chemical Composition | Different plastics have unique chemical structures, which can be analyzed for identification. |
Environmental Impact | Some plastics are more environmentally friendly and biodegradable, which may influence recycling processes. |
Market Demand | Certain plastics have higher market demand, making them more valuable for recycling. |
Collection and Sorting Methods | Manual sorting, optical sorting, near-infrared (NIR) technology, and density-based separation are common methods used in recycling facilities. |
End-of-Life Applications | Recycled plastics can be used for various products, including new packaging, textiles, and construction materials. |
What You'll Learn
- Sorting: Manual or automated processes to separate plastics by type
- Density: Differences in density help separate plastics like PET and HDPE
- Color: Visual inspection and sorting by color is a common method
- Chemical Composition: Advanced techniques identify plastics by their chemical makeup
- Size: Grinding and sorting by particle size for better processing
Sorting: Manual or automated processes to separate plastics by type
The process of sorting plastics for recycling is a critical step in the recycling stream, ensuring that each type of plastic is handled appropriately and can be effectively recycled. This sorting can be achieved through either manual labor or automated systems, each with its own advantages and applications.
Manual Sorting:
Manual sorting involves trained personnel physically separating plastics based on their types. This method is often used in smaller-scale recycling operations or as a secondary step after initial sorting. Workers are typically instructed to identify plastics by their color, shape, and feel, as different plastics have distinct characteristics. For example, high-density polyethylene (HDPE) bottles are usually translucent and feel slightly rigid, while polypropylene (PP) containers are often clear and have a slightly different texture. Manual sorting requires a keen eye and a good understanding of the various plastic types. It is a labor-intensive process but can be highly effective for achieving a high level of purity in the sorted materials.
Automated Sorting:
Automated sorting systems have become increasingly prevalent in modern recycling facilities due to their efficiency and accuracy. These systems utilize a combination of technologies, including optical scanners, infrared sensors, and air classifiers. Optical scanners can identify plastics based on color and transparency, while infrared sensors detect the heat signatures of different plastics, allowing for more precise sorting. Air classifiers use air currents to separate plastics based on their density. Automated sorters can process large volumes of material quickly and accurately, often achieving a higher degree of purity in the sorted plastics. This technology is particularly useful for large-scale recycling operations where speed and consistency are essential.
The choice between manual and automated sorting depends on various factors, including the scale of the recycling operation, the desired level of purity, and the specific requirements of the recycling market. Manual sorting is valuable for small-scale operations or when dealing with unique or challenging plastic types. In contrast, automated systems are ideal for high-volume recycling, ensuring efficient and consistent sorting.
In some cases, a hybrid approach is employed, combining manual and automated processes. For instance, automated sorters might be used to separate plastics into broad categories, and then manual labor could be utilized to further refine the sorting, especially for more complex or contaminated materials. This combined method can provide the best of both worlds, ensuring efficiency and accuracy in the recycling process.
Utah's Plastic Recycling Journey: Progress and Potential
You may want to see also
Density: Differences in density help separate plastics like PET and HDPE
Density plays a crucial role in the recycling process of plastics, particularly in the separation of different types of polymers. The concept is simple: materials with varying densities can be separated using physical methods, making it an effective technique for recycling facilities. This method is especially useful for sorting plastic waste into distinct categories, ensuring that each type of plastic is handled appropriately.
One of the most common examples of density-based separation is the distinction between PET (polyethylene terephthalate) and HDPE (high-density polyethylene). PET is known for its relatively low density, which is a key factor in its widespread use in beverage bottles. These bottles are often made from PET due to its lightweight nature, making it an ideal choice for packaging drinks. On the other hand, HDPE has a higher density, which contributes to its strength and rigidity. This higher density also makes HDPE suitable for applications like milk jugs and shampoo bottles.
The process of separating these plastics begins with the collection of waste. Recycling centers use specialized equipment to sort the incoming plastic waste stream. One common method is the use of air tables, which utilize the difference in density between PET and HDPE. When the waste is fed onto the air table, the lower-density PET bottles tend to float, while the higher-density HDPE items sink. This simple yet effective technique allows for the initial separation of these two types of plastics.
After the initial separation, further processing may be required to ensure a clean and sorted product. For instance, PET and HDPE can be further divided into their respective colors, as PET is commonly clear or slightly tinted, while HDPE is often translucent or opaque. This additional step ensures that the recycled materials can be used for specific applications, such as PET for food packaging and HDPE for containers that require more structural integrity.
Density-based separation is a critical aspect of plastic recycling, enabling the efficient sorting of various plastic types. It allows recycling facilities to handle different plastics appropriately, ensuring that each material is recycled in a way that maximizes its potential for reuse. By understanding and utilizing the density differences, the recycling process becomes more streamlined, contributing to a more sustainable approach to waste management.
Styrofoam and Plastic Recycling: What You Need to Know
You may want to see also
Color: Visual inspection and sorting by color is a common method
Visual inspection and sorting by color is a fundamental and widely used technique in the recycling process of plastics. This method relies on the human eye to identify and separate different types of plastic materials based on their color. While it may seem simple, this process is crucial for effective recycling as it helps to maintain the purity of the plastic streams, ensuring that each type of plastic is recycled appropriately.
The process begins with a thorough visual inspection of the incoming plastic waste. Recyclers often sort plastics by color due to the inherent properties of certain plastics, which are often color-coded. For instance, clear or transparent plastics like PET (polyethylene terephthalate) and HDPE (high-density polyethylene) are easily identifiable by their color. Similarly, colored plastics like PS (polystyrene) and PVC (polyvinyl chloride) can be sorted based on their distinct colors. This initial visual sorting step is often done by trained personnel who have a keen eye for detail and can quickly identify the various plastic types.
The human eye is a powerful tool for this task, as it can detect subtle differences in color that might be missed by automated systems. For example, a recycler can distinguish between different shades of green or blue, ensuring that similar-looking plastics are sorted correctly. This level of precision is essential to prevent contamination, as mixing different types of plastics can lead to recycling challenges and reduced material quality.
Once sorted by color, the plastics can then be further processed according to their specific types. For instance, clear PET bottles can be sent to a facility for cleaning and processing into new PET products, while colored PS packaging might be directed to a different recycling stream for transformation into other products. This color-based sorting method is a critical step in the recycling chain, enabling the efficient recovery and reuse of valuable plastic resources.
However, it's important to note that visual inspection alone may not be sufficient for all recycling processes. Some plastics, especially those with complex colors or blends, might require additional sorting techniques. In such cases, advanced technologies like near-infrared (NIR) spectroscopy can be employed to provide more accurate identification and sorting of plastic materials. Nonetheless, visual inspection and sorting by color remain a primary and essential practice in the recycling industry, contributing significantly to the overall efficiency and effectiveness of plastic recycling efforts.
Can Plastic Flowers Be Recycled? Unveiling the Truth
You may want to see also
Chemical Composition: Advanced techniques identify plastics by their chemical makeup
The identification of different types of plastics for recycling is a crucial step in the recycling process, ensuring that materials are sorted correctly and can be effectively processed. One of the most advanced methods for achieving this is through chemical analysis, which focuses on the unique chemical composition of each plastic type. This technique is particularly useful as it can identify plastics even when they are heavily contaminated or have been processed into a different form.
Advanced chemical techniques, such as mass spectrometry and infrared spectroscopy, are employed to analyze the molecular structure of plastics. Mass spectrometry, for instance, can provide detailed information about the chemical bonds and functional groups present in a plastic sample. By comparing the spectral data with known standards, it becomes possible to identify the specific type of plastic, even if it has been ground into flakes or pellets. This method is highly accurate and can distinguish between closely related polymers, such as PET (polyethylene terephthalate) and PBT (polybutylene terephthalate).
Infrared spectroscopy is another powerful tool for plastic identification. This technique relies on the absorption of infrared light by the plastic's molecular vibrations. Each type of plastic has a unique absorption spectrum, allowing for identification. For example, the absorption bands of polypropylene (PP) and high-density polyethylene (HDPE) are distinct, making it easier to separate these plastics from one another. This non-destructive testing method is valuable as it can provide information about the plastic's composition without altering its physical state.
Additionally, techniques like gas chromatography-mass spectrometry (GC-MS) can be used to analyze the monomer units and additives present in plastics. By separating and identifying these components, it becomes possible to determine the type of plastic, especially when dealing with blends or composites. This level of detail is essential for efficient recycling, as it ensures that the right processes and equipment are applied to each plastic type.
The use of these advanced chemical techniques in plastic recycling facilities is vital for maintaining the quality and integrity of the recycled materials. It enables the recycling industry to meet the demands of manufacturers who require specific types of plastics for their products. Furthermore, proper identification can help reduce contamination and improve the overall sustainability of the recycling process.
Plastic Clothes Covers: Can They Be Recycled in Ravenna, Ohio?
You may want to see also
Size: Grinding and sorting by particle size for better processing
The process of recycling plastics begins with the collection and sorting of various plastic types, which is crucial for efficient recycling. One critical step in this process is the size reduction of plastic materials through grinding and sorting by particle size. This technique is employed to enhance the recyclability and processing of different plastics.
Grinding is an essential process that involves reducing the size of plastic waste into smaller particles or pellets. This method is particularly useful for materials that are not easily recyclable in their original form. By breaking down larger plastic items, such as bottles, containers, or even plastic-based packaging, into smaller fragments, the subsequent sorting process becomes more manageable. The goal is to create a consistent and uniform particle size distribution, which is essential for the next stage of recycling.
Sorting by particle size is a critical step to ensure that plastics are separated effectively. This process involves classifying the ground plastic particles based on their size, density, and other physical properties. Different plastics have unique characteristics, and their separation is often based on these inherent differences. For instance, high-density polyethylene (HDPE) and low-density polyethylene (LDPE) have distinct density levels, making them separable through size-based sorting. This technique allows for the creation of clean streams of specific plastic types, which is vital for downstream processing and manufacturing.
Advanced sorting technologies, such as air classification and optical sorting, are employed to achieve precise particle size separation. Air classification uses air currents to separate particles based on their size and density, while optical sorting utilizes advanced imaging systems to identify and separate different plastics based on their visual characteristics. These methods ensure that the sorted plastics are of high quality and purity, meeting the requirements for various recycling applications.
By implementing size reduction and sorting processes, recycling facilities can improve the overall efficiency and effectiveness of plastic recycling. This enables the production of high-quality recycled materials, which can then be used in new products, reducing the demand for virgin plastic production and contributing to a more sustainable and circular economy. Proper size management and sorting are, therefore, integral to the successful recycling of various plastic types.
Louisiana's Plastic Recycling Incentives: Cashing In on Green Initiatives
You may want to see also
Frequently asked questions
Plastic recycling often begins with visual identification. Different types of plastics are typically color-coded or labeled with a resin identification code (RIC), which is a number inside a triangle on the bottom of the plastic item. These codes help recyclers and consumers understand the type of plastic and its potential recyclability. For example, PET (polyethylene terephthalate) is commonly used for beverage bottles and has the RIC 1. HDPE (high-density polyethylene) is used for milk jugs and has RIC 2.
Recycling facilities employ various techniques to separate plastics efficiently. One common method is manual sorting, where trained workers visually inspect and separate plastics based on their RICs. This process can be time-consuming but ensures accurate sorting. Another approach is automated sorting, which uses machines like optical sorters and eddy current separators. Optical sorters identify plastics by color and shape, while eddy current separators detect non-ferrous materials, allowing for more efficient separation.
Not all plastics are recyclable in the same way. Recycling processes vary depending on the type of plastic and its intended use. For instance, PET and HDPE are widely accepted in most recycling programs and can often be recycled into new containers or other products. However, some plastics, like PVC (polyvinyl chloride) and polystyrene, have specific recycling streams due to their unique properties. These plastics may require specialized recycling facilities or processes to ensure proper handling and potential reuse.