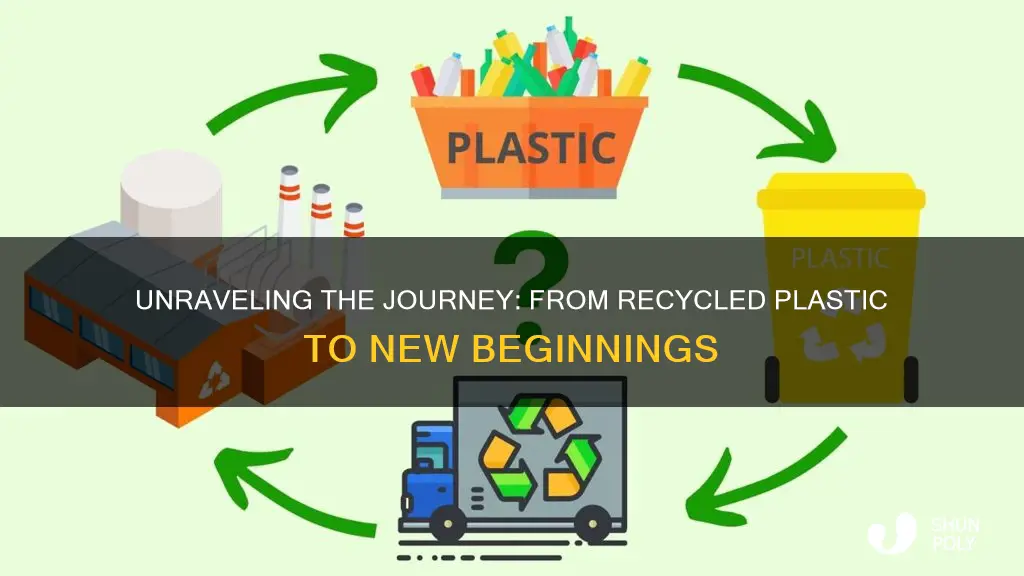
Recycling new recyclable plastics involves a process that begins with collecting and sorting the materials. Once sorted, the plastics are cleaned and shredded into small pieces called flakes. These flakes are then washed to remove any contaminants, such as labels or dirt. After washing, the flakes are sorted again to ensure only the correct types of plastic are used. The sorted and cleaned flakes are then melted and molded into new products, such as new containers or packaging, completing the recycling cycle. This process helps reduce waste and conserve resources, making it an essential part of sustainable practices.
What You'll Learn
- Collection: Sorting and collecting plastic waste from various sources
- Cleaning: Removing contaminants like food residue and labels
- Shredding: Breaking down plastic into small flakes or pellets
- Melting: Heating and softening the plastic for reprocessing
- Molding: Forming the molten plastic into new products
Collection: Sorting and collecting plastic waste from various sources
The process of recycling new recyclable plastics begins with the careful collection and sorting of plastic waste from various sources. This initial step is crucial as it sets the foundation for the entire recycling process and ensures the quality of the recycled material. Here's a detailed breakdown of the collection and sorting process:
Collection: Plastic waste collection is a critical phase in recycling. It involves gathering plastic materials from residential, commercial, and industrial sources. This can be achieved through various methods:
- Curbside Collection: Many cities and municipalities implement recycling programs where residents can place recyclable plastics, such as bottles and containers, in designated bins or bags for collection. This method is convenient and widely used, ensuring that plastic waste is separated at the source.
- Drop-Off Centers: Public or privately operated facilities where individuals can bring their plastic waste for recycling. These centers often provide a dedicated space for sorting and processing, allowing for better control over the materials collected.
- Business and Industrial Waste Streams: Recycling programs can target commercial and industrial facilities, encouraging them to separate and collect plastic waste generated during their operations. This includes items like packaging, containers, and even industrial-grade plastics.
- Specialized Collection Events: Organize community events or campaigns to collect plastic waste. These events can be particularly effective in raising awareness and engaging the public in recycling efforts.
Sorting and Categorization: Once the plastic waste is collected, the next step is to sort and categorize it based on the type of plastic and its intended use. Plastic recycling is complex due to the various types of plastics available, each with unique properties. Here's how sorting is typically done:
- Color and Resin Identification: Plastic items are often sorted by color and resin type. For example, PET (polyethylene terephthalate) is commonly used for beverage bottles and has a specific resin code. HDPE (high-density polyethylene) is used for milk jugs and has another code. Sorting by color and resin ensures that the recycling process can be tailored to specific materials.
- Size and Shape: Plastic items are also sorted by size and shape. For instance, large plastic containers, small packaging, and thin film plastics like shopping bags require different processing methods. This step ensures that the recycling facility can handle the materials efficiently.
- Contamination Removal: During sorting, any non-plastic contaminants, such as labels, caps, or food residue, are removed. This process ensures that the recycled plastic is of high quality and free from impurities.
The collection and sorting process is a meticulous task, requiring trained personnel and efficient systems to handle the volume of waste. It is essential to have well-organized collection points and clear guidelines for the public to ensure that the sorted plastics are of good quality and suitable for recycling. This initial step significantly impacts the overall success and sustainability of the recycling program.
Blosburg Recycling: Unraveling the Mystery of 5 & 6 Plastic Cups
You may want to see also
Cleaning: Removing contaminants like food residue and labels
The process of recycling recyclable plastics begins with cleaning and sorting, which is a crucial step to ensure the quality of the recycled material. When it comes to removing contaminants, the focus is primarily on eliminating food residue and labels, as these can significantly impact the recyclability and quality of the plastic.
Food residue, such as leftover crumbs, sauces, or liquids, can be challenging to remove due to its sticky and often greasy nature. To address this, a thorough cleaning process is essential. Start by rinsing the plastic containers or items under running water to remove any loose particles. Use a mild detergent or dish soap to create a soapy solution, ensuring it is gentle enough not to damage the plastic. Scrub the containers with a soft brush or sponge, paying extra attention to crevices and areas where food residue might accumulate. Rinse thoroughly again to eliminate any soap residue. For stubborn stains, a small amount of baking soda mixed with water can be applied and left to sit for a few minutes before scrubbing, which can help break down the residue.
Labels, often made of a different material than the plastic itself, require a slightly different approach. Start by removing any visible glue or residue from the label with a sharp knife or a label remover tool. If the label is particularly stubborn, you can soak the item in warm water to soften the glue, making it easier to peel off. For any remaining label residue, use a small amount of acetone or nail polish remover on a cloth to carefully wipe away the remaining parts. Ensure that all traces of the label are removed to prevent any contamination during the recycling process.
After cleaning, it is crucial to dry the plastic items thoroughly. Moisture can attract bacteria and cause issues during recycling. Use a clean towel to pat the items dry, ensuring no water spots remain. Proper drying helps maintain the integrity of the plastic and reduces the risk of contamination.
By following these cleaning procedures, you contribute to the overall efficiency and effectiveness of the recycling process, ensuring that the recycled plastic can be transformed into new products with minimal waste. This step is vital in maintaining the quality and sustainability of the recycling system.
Rio Linda's Plastic Recycling: A Community Effort
You may want to see also
Shredding: Breaking down plastic into small flakes or pellets
The process of recycling recyclable plastics begins with shredding, a crucial step in transforming these materials into reusable resources. This initial phase involves breaking down larger plastic items, such as bottles, containers, and packaging, into smaller, more manageable pieces. The goal is to reduce the size of the plastic waste, making it easier to handle and process further. Shredding machines, often equipped with sharp blades or rotating knives, are employed to cut, tear, or grind the plastic into flakes or pellets. These machines can process various types of plastics, including PET, HDPE, and LDPE, ensuring a versatile recycling process.
During the shredding process, the plastic is subjected to intense mechanical forces. The blades or knives rotate at high speeds, slicing through the plastic material. This action not only reduces the size of the plastic but also helps to remove any contaminants or impurities that may be present. The shredded plastic is then separated into different sizes, with finer particles creating smaller flakes and coarser ones resulting in larger pieces. This separation is essential to ensure that the subsequent recycling processes can be tailored to specific plastic types.
The shredded plastic flakes or pellets are now ready for further processing. These small pieces are more manageable and can be easily transported and stored. They are often sorted by type and color to facilitate the recycling chain. The sorting process can be automated, using optical scanners to identify different plastic resins, or it may involve manual inspection to ensure high-quality recycling. This step is critical to maintaining the integrity of the recycled material and ensuring it meets the required standards for reuse.
After shredding and sorting, the plastic flakes or pellets can be sold to manufacturers who use them to create new products. These manufacturers often have specific requirements for the size, color, and purity of the recycled plastic. By meeting these standards, the recycled material can be used in various industries, such as automotive, construction, and consumer goods. This final stage of the recycling process completes the loop, transforming waste plastic back into valuable resources, reducing the demand for virgin materials, and contributing to a more sustainable and circular economy.
In summary, shredding is a vital step in the recycling of recyclable plastics, enabling the breakdown of larger items into smaller, more versatile pieces. This process, combined with sorting, ensures that the recycled plastic meets the necessary specifications for reuse. By understanding and implementing these recycling techniques, we can effectively manage plastic waste, promote sustainability, and contribute to a greener future.
Apple Sauce, Plastic Dilemma: Recycling or Not?
You may want to see also
Melting: Heating and softening the plastic for reprocessing
The process of recycling recyclable plastics begins with the collection and sorting of these materials, ensuring they are free from contaminants. Once sorted, the plastics are prepared for the recycling process, which involves a crucial step known as melting. This technique is employed to transform the collected plastic waste into a usable form for reprocessing.
Melting is a thermal process that requires precise control of temperature and time. The plastic waste is fed into a specialized machine, often a granulator or a shredder, which reduces it into smaller pieces or flakes. These smaller pieces are then heated to a specific temperature, typically between 200°C and 300°C, depending on the type of plastic. The heat softens the plastic, allowing it to be molded and reshaped without losing its structural integrity. This softening process is a critical stage as it enables the plastic to be remolded into new products, such as fibers, pellets, or even new containers.
During the melting process, the plastic is often agitated or mixed to ensure even heating and to prevent the formation of large, uneven lumps. This agitation can be achieved through various methods, including mechanical stirring or the use of specialized equipment like a vacuum mixer. The goal is to create a homogeneous mixture, ensuring that the recycled plastic has consistent properties, which is essential for its successful reprocessing.
Once the plastic has been softened and mixed, it is ready for the next stage of recycling. The molten plastic can be extruded into thin strands, which are then cooled and cut into small pellets, known as 'nurdles' or 'plastic pellets.' These pellets are the raw material for manufacturing new products, such as packaging, furniture, and even new containers, thus completing the recycling loop.
The melting process is a vital step in plastic recycling, as it enables the transformation of waste into a valuable resource. By softening and reshaping the plastic, this technique allows for the creation of new products, reducing the demand for virgin plastic production and contributing to a more sustainable approach to waste management.
Unveiling the Fate of Plastic Container Caps: Do They Get Recycled?
You may want to see also
Molding: Forming the molten plastic into new products
The process of recycling recyclable plastics involves a series of steps to transform them into new products, and molding is a crucial stage in this journey. Once the plastic waste has been sorted, cleaned, and shredded, it enters the molding phase, where the real magic happens.
In this step, the shredded plastic, often in the form of flakes or pellets, is heated to a molten state. This process is typically carried out in specialized equipment called extruders, which apply heat and pressure to melt the plastic. The temperature and duration of this heating process depend on the type of plastic being recycled. For example, high-density polyethylene (HDPE) and polypropylene (PP) require different melting temperatures compared to polyvinyl chloride (PVC).
Once the plastic is molten, it is fed into a molding machine, which is the heart of the molding process. These machines come in various types, including injection molding, blow molding, and compression molding, each suited for different applications. The molten plastic is then shaped and formed into the desired product using a mold. The mold is a critical component, as it defines the final shape and structure of the recycled product.
Injection molding is one of the most common methods, where the molten plastic is injected into a closed mold under high pressure. This process allows for the creation of intricate and complex shapes, making it ideal for manufacturing items like bottles, containers, and automotive parts. The mold is heated to a specific temperature to ensure the plastic flows easily, and then the plastic is rapidly cooled, solidifying it in the desired form.
Blow molding, on the other hand, is used for producing hollow objects like bottles and containers. Here, the molten plastic is first formed into a parison (a partially shaped piece) and then blown into the mold, which expands and sets the shape. Compression molding is another technique where the plastic is heated and compressed into a mold, often used for creating thicker and more rigid products.
After the molding process, the final products are removed from the molds and may undergo additional finishing processes, such as trimming excess material or adding labels. These recycled products can then be used in various industries, reducing the demand for virgin plastic and contributing to a more sustainable and circular economy.
Are UPS Plastic Envelopes Recyclable? Uncover the Truth
You may want to see also
Frequently asked questions
The recycling process begins with collecting and sorting the plastic waste. This is typically done through curbside recycling programs, drop-off centers, or specialized collection events. Once collected, the plastic is cleaned and sorted by type, as different types of plastics have varying recycling methods. The sorted plastics are then shredded or granulated to reduce their size and prepare them for the next stage. The shredded or granulated plastic is heated and mixed with other materials to create a molten mixture, which is then shaped into new products or pellets, forming the basis for new recyclable plastic items.
Recycling facilities employ various techniques to maintain the quality of recycled plastic. After the initial sorting, plastics are further classified based on their color, type, and purity. This classification helps in creating homogeneous batches, ensuring that the recycled material meets the required standards. Facilities also use advanced technologies like infrared spectroscopy and X-ray fluorescence to identify and separate contaminants, such as metals or other plastics, from the plastic stream. This meticulous process ensures that the final recycled product is of high quality and suitable for reuse.
While many new recyclable plastics can be recycled, the process becomes more complex and challenging with each recycling cycle. Most plastics are classified into different types, such as PET (polyethylene terephthalate) and HDPE (high-density polyethylene), each with its own recycling method. Over time, the plastic can degrade and lose its structural integrity, making it unsuitable for certain applications. Additionally, the presence of contaminants or mixed materials can hinder the recycling process. Therefore, it is essential to maintain proper waste management practices and educate the public on the correct disposal and recycling of plastics to ensure a more sustainable approach to recycling.