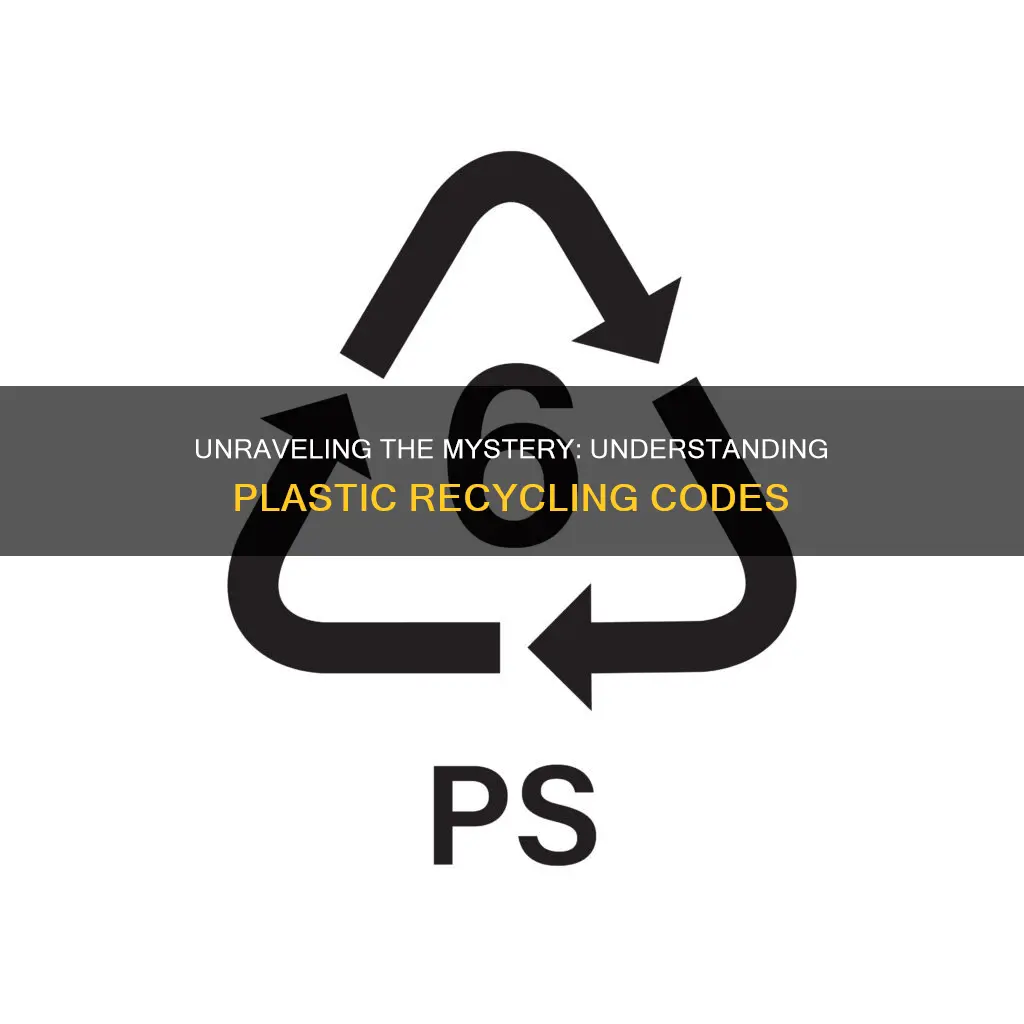
Understanding the recycling process for plastic is crucial for promoting environmental sustainability. Plastic recycling identification is a system designed to categorize and manage different types of plastic materials, ensuring they are recycled effectively. This process involves assigning a numerical code to each plastic type, ranging from 1 to 7, which indicates the resin used in its manufacturing. These codes help recycling facilities and consumers identify the appropriate methods for sorting, processing, and reusing plastic waste, contributing to a more sustainable approach to plastic consumption and disposal.
What You'll Learn
- Sorting and Collection: Plastic waste is sorted by type and collected for recycling
- Resin Identification Codes: Codes on plastic items indicate their type and recyclability
- Cleaning and Shredding: Plastic is cleaned, shredded, and processed into flakes
- Melting and Molding: Recycled plastic is melted and molded into new products
- Quality Control: Recycled plastic is tested for purity and quality before reuse
Sorting and Collection: Plastic waste is sorted by type and collected for recycling
The process of recycling plastic begins with the crucial step of sorting and collecting plastic waste, which is a fundamental aspect of effective recycling. This initial phase is essential as it sets the foundation for the entire recycling process, ensuring that the materials are properly identified and prepared for their journey towards new products.
Sorting plastic waste is a meticulous task that requires careful attention to detail. It involves categorizing different types of plastic based on their resin identification codes, which are typically found on the bottom of plastic containers. These codes, ranging from 1 to 7, indicate the type of plastic used, such as PET (polyethylene terephthalate) for beverage bottles or HDPE (high-density polyethylene) for milk jugs. By sorting plastics according to their types, recyclers can ensure that each material is processed appropriately, maximizing the efficiency of the recycling stream.
Collection plays a vital role in this process, as it involves gathering plastic waste from various sources. This can include residential areas, where individuals separate their plastic waste for recycling, or commercial and industrial sites, where dedicated collection systems are often implemented. Efficient collection methods ensure that plastic waste is not only sorted but also readily available for the recycling process. Curbside recycling programs, drop-off centers, and mobile collection units are common methods used to facilitate the collection of plastic waste.
During the collection process, it is essential to maintain a clean and organized system to prevent contamination. Contaminants, such as food residue, labels, or other non-plastic materials, can compromise the quality of the sorted plastics. Therefore, proper collection methods should be employed to minimize these issues. This may include providing clear guidelines to the public on what items to include in the recycling bin and implementing quality control measures during the collection phase.
Once sorted and collected, the plastic waste is ready for the next stage of recycling, which involves processing and transforming it into reusable materials. This process ensures that plastic waste is given a new life, contributing to a more sustainable and environmentally friendly approach to waste management.
Unraveling the Mystery: Can Plastic Cups Be Recycled?
You may want to see also
Resin Identification Codes: Codes on plastic items indicate their type and recyclability
The world of plastic recycling can be complex, but one of the most crucial tools in understanding and managing plastic waste is the Resin Identification Code. These codes, often found on the bottom of plastic containers and items, are a universal system used to identify the type of plastic used in the product. This system is essential for recycling facilities and waste management systems to process and recycle plastic materials effectively.
Each number from 1 to 7 represents a different type of plastic resin, providing a quick and easy way to categorize plastics. For instance, a code of 1 indicates polyethylene terephthalate (PET), commonly used in water bottles and food containers. Code 2 represents high-density polyethylene (HDPE), often found in milk jugs and some shampoo bottles. Polyvinyl chloride (PVC) is identified by code 3, and this resin is used in pipes, plumbing fixtures, and some food packaging. Code 4 signifies low-density polyethylene (LDPE), which is used in grocery bags, some clothing, and flexible packaging. Polypropylene (PP) is indicated by code 5, and it is commonly used in food containers, bottle caps, and straws. Code 6 represents polystyrene (PS), often used in disposable cups, containers, and packaging. Lastly, code 7 is a catch-all category for other types of plastic, including some blends and composites.
Understanding these codes is vital for both consumers and recycling facilities. Consumers can use the codes to make informed choices about the products they purchase and how to dispose of them properly. For example, knowing that a plastic item with a code of 1 or 2 is highly recyclable can encourage proper disposal. Recycling facilities can also use these codes to ensure they have the correct processes in place to handle different types of plastics, improving the efficiency and effectiveness of recycling operations.
Moreover, the Resin Identification Codes provide an important aspect of transparency in the recycling process. They help educate the public about the recyclability of various plastic items, promoting a culture of responsible waste management. By knowing which plastics are recyclable and which are not, individuals can make a significant contribution to reducing plastic waste and promoting sustainability.
In summary, the Resin Identification Codes are a simple yet powerful tool in the recycling process. They enable a clear identification of plastic types, ensuring that recycling efforts are directed towards the appropriate materials. This system empowers consumers and recycling facilities alike, fostering a more sustainable approach to plastic waste management. With these codes, we can all play a part in making plastic recycling more accessible and efficient.
Unraveling the Mystery: Can Plastic Tags Be Recycled?
You may want to see also
Cleaning and Shredding: Plastic is cleaned, shredded, and processed into flakes
The process of recycling plastic begins with the collection and sorting of plastic waste. Once sorted, the plastic is cleaned to remove any contaminants, such as food residue, labels, or other debris. This cleaning process is crucial to ensure the quality of the recycled material. After cleaning, the plastic is shredded into small pieces, which is a process that can be done using various methods. Shredding helps to reduce the volume of the plastic and makes it easier to handle and process further.
Shredding machines are designed to break down the plastic into uniform-sized flakes or pellets. These flakes are then washed again to remove any remaining impurities and to ensure that the plastic is clean and free from contaminants. The washing process might involve using water or other cleaning agents, and it is essential to remove any residual dirt or debris.
Once the plastic flakes are thoroughly cleaned, they are dried to remove excess moisture. Drying is a critical step to ensure the stability and quality of the recycled material. The dried flakes are then ready for the next stage of the recycling process, where they are often melted and molded into new products or used as feedstock for various industrial applications.
The cleaning and shredding process is a fundamental step in plastic recycling, as it prepares the material for further processing and ensures that the final recycled product meets the required standards. This method of recycling is essential for maintaining the integrity of the plastic and making it suitable for reuse in various industries. By following these steps, recycled plastic can be transformed into new products, contributing to a more sustainable and circular economy.
Unraveling the Mystery: Can Plastic Photo Sleeves Be Recycled?
You may want to see also
Melting and Molding: Recycled plastic is melted and molded into new products
The process of recycling plastic involves a series of steps to transform used plastic items into new products, and one of the key methods is melting and molding. This technique is particularly useful for creating a wide range of items, from simple household objects to complex components for various industries. Here's an overview of how this process works:
When plastic waste is collected and sorted, it is often categorized based on its type and color, as different plastics have unique properties. The most common types of plastic used in recycling are PET (polyethylene terephthalate), HDPE (high-density polyethylene), and PVC (polyvinyl chloride). Once sorted, the plastic is prepared for the melting process. This involves shredding or granulating the plastic waste to reduce its volume and create a uniform material. The shredded plastic is then cleaned to remove any contaminants, such as labels, caps, or other non-plastic materials, ensuring a higher quality end product.
The cleaned and prepared plastic is fed into a melting machine, which can vary in design depending on the specific application. For example, a single-screw extruder is commonly used for lower-temperature processes, while a twin-screw extruder is more versatile and can handle a wider range of materials. In the melting process, the plastic is heated to its melting point, which varies depending on the type of plastic. For instance, PET melts at around 230-260°C (446-500°F), while HDPE melts at approximately 120-140°C (248-284°F). The heat is applied evenly to ensure the plastic is fully melted and becomes a homogeneous liquid.
After melting, the plastic is now in a viscous state and is ready for molding. This step involves shaping the molten plastic into the desired form using a mold. The mold is designed to create the specific shape and structure of the intended product. There are various molding techniques, including injection molding, blow molding, and compression molding, each with its own advantages and applications. For instance, injection molding is suitable for producing complex, hollow items, while blow molding is often used for creating large, hollow containers.
During the molding process, the molten plastic is injected or blown into the mold under high pressure. The heat and pressure ensure that the plastic takes the shape of the mold. Once the plastic has cooled and solidified within the mold, it is removed, and the new product is formed. This process can be repeated multiple times, allowing for the continuous creation of new items from recycled plastic. The resulting products can be anything from food containers, bottles, and packaging to automotive parts, furniture, and even construction materials.
Melting and molding offer a sustainable approach to recycling plastic, reducing waste and giving new life to used materials. This method is a crucial step in the circular economy, where resources are reused and repurposed, minimizing the environmental impact of plastic production and consumption. By utilizing this process, we can contribute to a more sustainable future, reducing our reliance on virgin resources and minimizing the amount of plastic waste that ends up in landfills or the environment.
Unraveling the Mystery: Can Plastic Straws Be Recycled?
You may want to see also
Quality Control: Recycled plastic is tested for purity and quality before reuse
The process of recycling plastic is a complex journey, and ensuring the quality of recycled materials is a critical aspect that often goes unnoticed. Once plastic waste is collected, sorted, and processed, it undergoes rigorous quality control measures to meet the required standards for reuse. This step is essential to guarantee that the recycled plastic is safe, functional, and suitable for various applications.
Quality control in plastic recycling involves several testing procedures to assess the purity and integrity of the material. One common method is visual inspection, where trained personnel examine the plastic for any visible defects, contaminants, or foreign objects. This visual assessment helps identify any potential issues, such as residue, stains, or the presence of non-plastic materials, which could compromise the quality of the recycled product.
Laboratory analysis is another crucial aspect of quality control. Samples of recycled plastic are tested using various scientific techniques to determine their composition and properties. These tests may include spectrographic analysis to identify different types of plastics, ensuring that only the intended polymer is present. Additionally, measurements of plastic density, melt flow index, and molecular weight distribution provide insights into the material's quality and consistency.
Furthermore, recycled plastic is often subjected to physical and mechanical tests. These tests evaluate the material's strength, durability, and performance characteristics. For instance, impact resistance tests simulate real-world conditions to assess how the plastic can withstand shocks and vibrations. Similarly, tensile strength tests measure the material's ability to resist pulling forces, providing valuable data for quality assurance.
In the recycling industry, achieving high-quality recycled plastic is a continuous pursuit. Manufacturers and recyclers invest in advanced technologies and employ strict quality control protocols to meet industry standards and customer expectations. By ensuring the purity and reliability of recycled materials, they can promote a circular economy, reducing waste and encouraging the sustainable use of resources. This commitment to quality control is vital for the long-term success and acceptance of recycled plastic in various industries.
Recycling Plastic: Upcycling or Downgrading?
You may want to see also
Frequently asked questions
Plastic recycling identification involves sorting and categorizing different types of plastic materials based on their resin identification codes, which are typically found on the bottom of plastic products. These codes, ranging from 1 to 7, indicate the type of plastic and help determine the appropriate recycling methods.
You can identify the plastic type by checking the resin identification code on the product. Common household items like water bottles (PET, 1), milk jugs (HDPE, 2), and shampoo bottles (PP, 5) have specific codes. Understanding these codes is crucial for proper recycling.
No, not all plastics are recyclable. Only certain types of plastic, as indicated by the resin identification codes, are accepted in recycling programs. For example, PET (1) and HDPE (2) are widely recycled, while others like polystyrene (PS, 6) and certain types of plastic bags may have limited recycling options.
Once sorted, identified plastics are cleaned, shredded, or melted to create raw materials. These raw materials are then used to manufacture new products, such as fleece jackets, car parts, or new containers, reducing the demand for virgin plastic production.
Always check your local recycling guidelines to understand what types of plastic are accepted. Rinse plastic containers to remove food residue, and ensure they are empty and dry before placing them in the recycling bin. Proper sorting and preparation of plastic waste contribute to more efficient recycling processes.