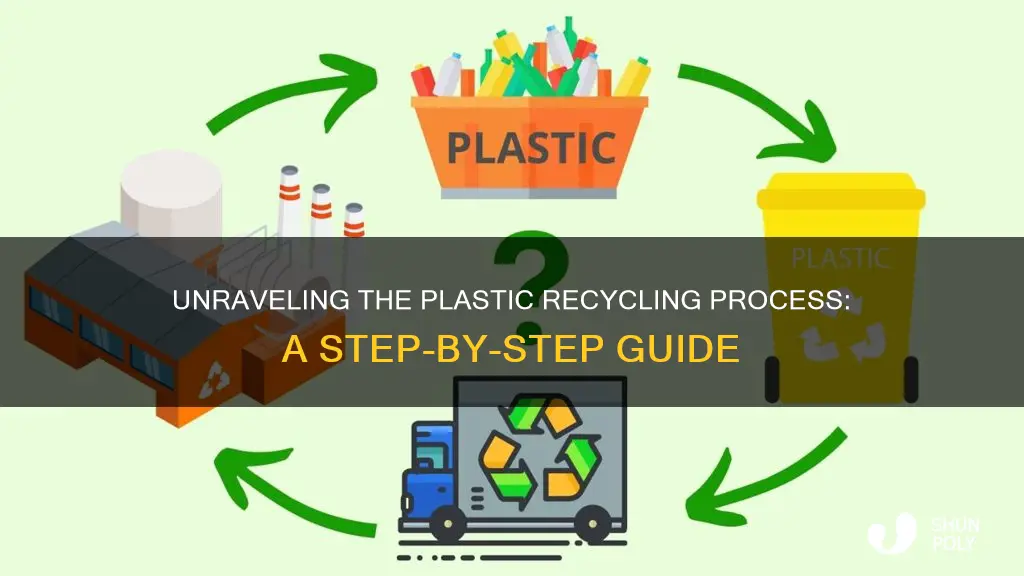
Plastics recycling is a crucial process to address the growing environmental concerns associated with plastic waste. It involves a series of steps to transform used plastic materials into new products, reducing the demand for virgin plastic production and minimizing the impact of plastic pollution. The process typically begins with the collection of plastic waste, which is then sorted and cleaned to remove contaminants. After sorting, the plastics are shredded or ground into small pieces called flakes. These flakes are further processed through washing to remove any remaining dirt or impurities. The cleaned plastic flakes are then classified based on their type and color, ensuring they meet the requirements for specific applications. Finally, the sorted and cleaned plastic flakes are melted and molded into new products, such as pellets or sheets, which can be used to manufacture various items, contributing to a more sustainable approach to managing plastic waste.
What You'll Learn
- Collection: Sorting and collecting plastic waste from homes, businesses, and recycling centers
- Processing: Shredding, washing, and melting plastic to create new raw materials
- Sorting: Categorizing plastics by type (PET, HDPE, etc.) for specific recycling methods
- Reclaiming: Transforming recycled plastics into pellets or flakes for new products
- Manufacturing: Using recycled plastics to produce new items like bottles, containers, and textiles
Collection: Sorting and collecting plastic waste from homes, businesses, and recycling centers
The process of recycling plastics begins with the collection and sorting of plastic waste, which is a crucial step in ensuring the effectiveness and efficiency of the recycling process. This initial phase involves a systematic approach to gather and organize plastic materials, setting the foundation for the subsequent recycling stages.
Collection: Plastic waste is collected from various sources, including homes, offices, businesses, and dedicated recycling centers. It is essential to have a well-organized collection system to ensure that plastic items are separated from other waste streams. Local governments, waste management companies, or community initiatives often implement collection programs. These programs may involve weekly or bi-weekly collections, drop-off points, or special events where residents can deposit their plastic waste. During collection, it is important to educate the public about the proper disposal of plastics to minimize contamination and maximize the quality of the sorted materials.
Sorting: Once collected, the plastic waste undergoes a sorting process to separate different types of plastics. This step is critical as it determines the feasibility of recycling each plastic type. Sorting can be done manually or through automated systems. Manual sorting involves trained personnel who visually inspect and separate plastics based on their type and quality. Common methods include hand-picking, using sieves, or employing color-coded bins for different plastic types. Automated sorting, on the other hand, utilizes machines like optical sorters, which use infrared technology to identify and separate plastics based on their molecular structure. This method is faster and more efficient, especially for large-scale recycling operations.
During sorting, it is crucial to identify and separate common plastic types, such as PET (polyethylene terephthalate), HDPE (high-density polyethylene), PVC (polyvinyl chloride), LDPE (low-density polyethylene), and PP (polypropylene). Each plastic type has specific recycling processes and applications, so proper sorting ensures that they are recycled appropriately. For instance, PET is widely used for beverage bottles and can be recycled into fibers for clothing or new bottles, while HDPE is commonly found in milk jugs and can be recycled into items like outdoor furniture or trash bins.
Quality Control: After sorting, a quality control process is essential to ensure that the separated plastics meet the recycling standards. This step involves inspecting the sorted materials for any contaminants, such as food residue, labels, or non-plastic items. Contaminants can compromise the recycling process and the quality of the recycled product. Quality control may include visual inspections, moisture content testing, and weight analysis to ensure that the sorted plastics are clean, dry, and free from impurities.
In summary, the collection and sorting of plastic waste are fundamental steps in the recycling process. Effective collection systems and thorough sorting methods ensure that plastics are properly identified and separated, enabling their recycling into new products. Quality control measures further enhance the efficiency and sustainability of plastic recycling, contributing to a circular economy where waste is minimized, and resources are conserved.
Unveiling US Plastic Recycling Costs: A Financial Analysis
You may want to see also
Processing: Shredding, washing, and melting plastic to create new raw materials
The process of recycling plastics involves several stages, each crucial in transforming used plastic items into new raw materials. One of the initial steps in this journey is shredding. Plastic waste, whether it's bottles, containers, or other items, is collected and sorted according to its type. This sorting is essential as different types of plastics require specific recycling methods. Once sorted, the plastic waste is shredded into small pieces. This process is carried out using specialized machinery that can handle the varying sizes and shapes of plastic items. Shredding helps reduce the volume of plastic waste, making it easier to manage and process further.
After shredding, the plastic pieces undergo a thorough washing process. This step is critical to remove any contaminants, such as dirt, labels, or other debris, that may be present on the plastic. The washing process typically involves sorting the shredded plastic by type again, as different plastics have different washing requirements. The sorted plastic is then cleaned using various methods, including mechanical washing, where water and brushes are used to scrub the plastic, and chemical washing, which employs solvents to dissolve and remove impurities. This washing stage ensures that the final recycled product is clean and free from any unwanted substances.
The cleaned and sorted plastic pieces are then ready for the next phase: melting. This process involves heating the plastic to its melting point, transforming it from a solid state into a liquid. The melting is done in specialized equipment called extruders, which apply heat and pressure to the plastic. The temperature and duration of the melting process depend on the type of plastic being processed. For example, PET (polyethylene terephthalate), commonly used in beverage bottles, has a different melting point and process compared to HDPE (high-density polyethylene) used in milk jugs.
During the melting stage, the plastic is often mixed with other recycled materials or additives to create a consistent and usable raw material. This mixture is then cooled and solidified, forming what is known as 'recycled plastic granulate' or 'recycled plastic resin.' This final product can be used in various industries, such as manufacturing, construction, and automotive, to create new products, from toys and furniture to car parts and construction materials. The process of shredding, washing, and melting plastic is a complex and precise art, requiring specialized equipment and knowledge to ensure the quality and purity of the recycled material.
Greenville's Plastic Recycling: Unlocking the Power of 6
You may want to see also
Sorting: Categorizing plastics by type (PET, HDPE, etc.) for specific recycling methods
The process of recycling plastics begins with proper sorting, a crucial step to ensure effective recycling and the production of high-quality recycled materials. Plastic recycling involves various types of polymers, each with unique properties and applications, so categorizing them is essential. This initial sorting process is typically done by hand or through automated systems in recycling facilities.
One common method of sorting is by color and type. Different types of plastics have distinct characteristics, and these can be identified through their resin identification codes, which are typically found on the bottom of plastic containers. For example, PET (polyethylene terephthalate) is commonly used for beverage bottles and has a resin code of 1. HDPE (high-density polyethylene) is often used for milk jugs and shampoo bottles, identified by the code 2. Other types include LDPE (low-density polyethylene, code 4), PP (polypropylene, code 5), and PS (polystyrene, code 6). Each type of plastic has specific recycling methods and applications.
PET bottles, for instance, are widely accepted in most recycling programs. They are sorted and collected, then sent to a recycling facility where they are cleaned, shredded, and transformed into small pellets called 'repellets'. These repellets can be used to create new products like carpet fibers, clothing, and even new bottles. HDPE, on the other hand, is often used for durable items like containers for cleaning products and detergents. These HDPE items are sorted and processed similarly to PET, but the end products may vary, such as outdoor furniture, brooms, or even new containers.
The sorting process also considers the purity of the plastic. Contaminants like food residue, labels, or other non-plastic materials can affect the quality of the recycled product. For instance, food-contaminated PET bottles may be unsuitable for making new food containers but can still be used for other applications like outdoor gear or insulation. Proper sorting ensures that the recycled plastics are of sufficient quality for their intended purposes.
In some cases, advanced sorting techniques are employed to enhance efficiency. Optical sorters use infrared light to identify different types of plastics based on their unique light absorption properties. This method is particularly useful for separating PET and HDPE, which have similar colors but different properties. Another advanced technique is near-infrared (NIR) spectroscopy, where a light source is used to analyze the molecular structure of plastics, allowing for precise identification and sorting. These advanced methods contribute to a more sustainable recycling process by maximizing the quality and quantity of recycled materials.
Unraveling NYC's Plastic Fork Recycling Mystery: A Comprehensive Guide
You may want to see also
Reclaiming: Transforming recycled plastics into pellets or flakes for new products
The process of reclaiming and transforming recycled plastics into usable materials is a crucial step in the recycling journey. Once collected and sorted, the plastic waste undergoes a series of processes to be transformed into a raw material suitable for new products. This step involves several key techniques to ensure the plastic is cleaned, shredded, and processed into a form that can be easily utilized in manufacturing.
The first stage in this process is cleaning the plastic waste. This is essential to remove any contaminants such as dirt, labels, and non-plastic materials. The cleaning process often involves washing the plastic with water and sometimes using chemicals to break down any stubborn residues. After cleaning, the plastic is typically dried to remove any moisture, ensuring it is ready for the next phase.
Next, the cleaned plastic is shredded or granulated. Shredding involves breaking down larger plastic items, such as bottles and containers, into small pieces. This step increases the surface area of the plastic, making it easier to process and ensuring a more consistent material. Granulation is a similar process but specifically turns the plastic into small, uniform pellets. These pellets are the raw material for many industries.
The shredded or granulated plastic is then sorted and classified based on its type and quality. Different types of plastics have varying properties and uses, so proper sorting is essential. This classification helps in determining the best application for the recycled plastic. For instance, high-quality plastics might be used for packaging, while lower-grade materials could be suitable for construction or other industrial applications.
Finally, the sorted and classified plastic pellets or flakes are ready to be sold to manufacturers. These materials can be used in various industries, including automotive, construction, and consumer goods. By transforming recycled plastics into pellets or flakes, we create a sustainable cycle where used plastics are given new life, reducing the demand for virgin materials and minimizing the environmental impact of plastic production. This process is a vital link in the recycling chain, ensuring that plastic waste is not only managed but also contributes to a more circular economy.
Plastic's Paradox: From Recycling to Rubbish
You may want to see also
Manufacturing: Using recycled plastics to produce new items like bottles, containers, and textiles
The process of recycling plastics to create new products is a fascinating journey that transforms waste into valuable resources. Here's an overview of how recycled plastics are utilized in manufacturing:
Collection and Sorting: The journey begins with the collection of plastic waste from various sources, such as households, businesses, and recycling centers. These plastics are then sorted based on their type and quality. Common types include PET (polyethylene terephthalate), HDPE (high-density polyethylene), and PVC (polyvinyl chloride). Proper sorting is crucial as it determines the feasibility of recycling and the final product's quality.
Cleaning and Shredding: Once sorted, the plastics undergo a cleaning process to remove any contaminants like labels, caps, or dirt. This step ensures that the recycled material is pure and free from impurities. After cleaning, the plastics are shredded into small pieces, often referred to as 'flakes' or 'granules'. This process reduces the size of the plastic waste, making it easier to handle and process further.
Melting and Molding: The shredded plastic flakes are then sent to a recycling plant. Here, they are heated to high temperatures, causing them to melt and become a molten mass. This molten plastic is then shaped and molded into new forms using various techniques. One common method is extrusion, where the plastic is forced through a die to create specific shapes and sizes. For example, PET bottles can be recycled into new bottles, containers, or even textile fibers.
Reforming and Reinventing: In this stage, the recycled plastics are transformed into a usable form. For bottles and containers, the molten plastic is cooled and solidified, then cut into the desired dimensions. These new pieces can then be used to manufacture various products. Textiles, on the other hand, are created by spinning the recycled plastic fibers into yarns, which are then woven or knitted to produce fabrics. This process not only reduces waste but also provides an eco-friendly alternative to virgin materials.
Quality Control and Distribution: Before the final products are packaged and distributed, they undergo rigorous quality control checks. This ensures that the recycled plastics meet the required standards and specifications. Once approved, the products are ready to be sold to manufacturers who will use them to create new items, completing the recycling loop. This process not only reduces the demand for virgin plastics but also minimizes the environmental impact of plastic production.
Eco-Friendly Christmas: Can Plastic Trees Be Recycled?
You may want to see also
Frequently asked questions
Plastic recycling is a process that involves collecting, sorting, cleaning, and reprocessing plastic waste to create new products. It is an essential step towards reducing environmental pollution and conserving resources. The process typically begins with the collection of plastic waste from various sources, such as households, businesses, and recycling centers. This waste is then sorted based on the type of plastic, as different types have distinct properties and recycling methods. Common types of plastic include PET (polyethylene terephthalate), HDPE (high-density polyethylene), PVC (polyvinyl chloride), LDPE (low-density polyethylene), and PP (polypropylene).
Preparing plastic for recycling involves several steps to ensure the material is clean, dry, and sorted correctly. First, plastic waste is collected and transported to a recycling facility. Here, it undergoes a sorting process to separate different types of plastics. This can be done manually or using automated systems. After sorting, the plastic is cleaned to remove contaminants like food residue, labels, and non-plastic materials. Cleaning methods may include washing, shredding, or using specialized cleaning agents. Once cleaned, the plastic is dried to remove any moisture, as this can affect the recycling process.
There are several methods used to recycle plastic, each with its own advantages and applications. One common method is mechanical recycling, which involves processing plastic waste into new products without changing its chemical structure. This process typically includes shredding or granulating the plastic, melting it, and then molding it into new shapes. Another approach is chemical recycling, which breaks down the plastic's chemical bonds to create new materials. This method is often used for recycling certain types of plastics, such as PET, to produce new fibers or chemicals. Advanced recycling techniques also exist, like gasification and pyrolysis, which convert plastic waste into valuable resources like oil and gas.