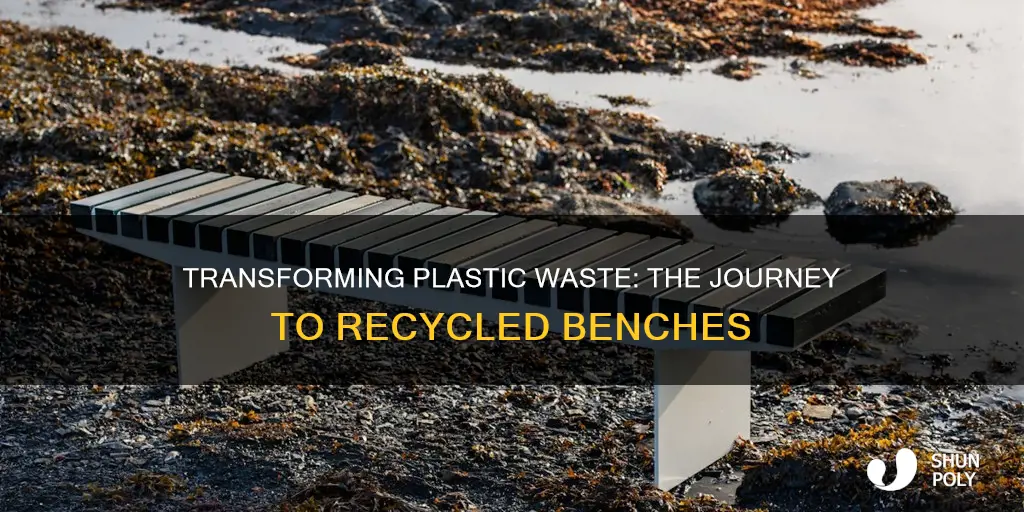
Recycled plastic benches are an innovative and sustainable solution for public spaces, offering a durable and low-maintenance alternative to traditional wooden or metal benches. The process of creating these benches involves several steps, starting with the collection and sorting of plastic waste. Once sorted, the plastic is cleaned, shredded, and melted into pellets, which are then heated and extruded into a continuous sheet. This sheet is then cut into the desired shape and size of the bench, often using a mold to ensure consistency. Finally, the benches are cooled, cleaned, and inspected before being installed in parks, gardens, and other public areas, providing a long-lasting and eco-friendly seating option.
What You'll Learn
- Collection: Plastic waste is gathered from various sources, including recycling centers and public drop-off points
- Sorting: Materials are sorted by type and color to ensure quality
- Cleaning: Recycled plastic is cleaned to remove contaminants and impurities
- Shredding: Plastic is shredded into small pieces for easier processing
- Molding: Shredded plastic is heated and formed into bench shapes using molds
Collection: Plastic waste is gathered from various sources, including recycling centers and public drop-off points
The process of creating recycled plastic benches begins with the meticulous collection of plastic waste, a crucial step in transforming discarded materials into functional and sustainable furniture. This initial phase involves a systematic approach to gathering plastic waste from multiple sources, ensuring a steady supply of raw materials for the recycling process.
Recycling centers play a pivotal role in this collection process. These centers are equipped to handle various types of plastic waste, including bottles, containers, and other plastic items that have been discarded by consumers. The waste is sorted and processed to separate different types of plastics, ensuring that only clean and dry plastic materials are used in the recycling process. This step is essential to maintain the quality and integrity of the recycled plastic.
In addition to recycling centers, public drop-off points are another vital source of plastic waste collection. These points are strategically placed in communities, making it convenient for residents to contribute their used plastic items. Public awareness and participation are key to the success of this collection method. Educational campaigns and initiatives can encourage citizens to properly dispose of their plastic waste, ensuring a continuous supply of materials for recycling.
The collection process is a collaborative effort between local authorities, recycling facilities, and the community. It requires efficient waste management systems and infrastructure to handle the volume of plastic waste generated. By establishing a robust collection network, the process ensures that plastic waste is not only gathered but also sorted and prepared for the next stage of recycling, which involves processing and transforming the collected plastic into raw materials for manufacturing recycled plastic benches.
This initial collection step is fundamental to the entire recycling process, as it sets the foundation for the quality and quantity of plastic waste available for recycling. The more efficient and comprehensive the collection, the higher the potential for successful recycling and the creation of durable, eco-friendly plastic benches.
Unraveling Calgary's Plastic Straw Recycling Mystery: A Comprehensive Guide
You may want to see also
Sorting: Materials are sorted by type and color to ensure quality
The process of creating recycled plastic benches begins with the collection and sorting of plastic waste. This initial step is crucial as it sets the foundation for the entire production process. When plastic waste is gathered, it is essential to separate it into different types and colors to maintain quality and ensure the benches' durability.
Sorting by type is a critical process. Plastic materials can vary widely, including common types like PET (polyethylene terephthalate) and HDPE (high-density polyethylene), as well as less common varieties. Each type has unique properties and melting points, so sorting ensures that the right materials are used for the right parts of the bench. For instance, PET is often used for the bench's frame due to its strength and flexibility, while HDPE might be more suitable for the seat or backrest for its impact resistance.
Color sorting is equally important. Recycled plastic can come in various colors, and maintaining a consistent color palette is key to creating aesthetically pleasing benches. By sorting plastics by color, manufacturers can ensure that the final product has a uniform appearance. This process involves skilled workers who visually inspect the plastic and separate it into different color categories, ensuring that the raw materials are ready for the next stage of production.
Advanced sorting techniques are also employed, especially in large-scale recycling operations. Optical sorters use sensors to identify and separate plastics based on their color and type. These machines can process large volumes of waste quickly and accurately, improving efficiency and reducing human error. The sorted materials are then ready for further processing, where they are cleaned, shredded, and melted to create the raw material for the benches.
In summary, the sorting process is a critical and meticulous phase in the creation of recycled plastic benches. It ensures that the final product meets quality standards, both in terms of material composition and visual appeal. This initial step sets the tone for the entire manufacturing process, making it an essential aspect of sustainable and eco-friendly furniture production.
Recycling Plastic Plant Pots: A Green Gardening Guide
You may want to see also
Cleaning: Recycled plastic is cleaned to remove contaminants and impurities
The process of creating recycled plastic benches involves a crucial step in ensuring the quality and durability of the final product: cleaning. This step is essential to remove any contaminants and impurities that may have accumulated during the recycling process, which can significantly impact the performance and longevity of the benches. Here's an overview of the cleaning process:
Sorting and Separation: Before cleaning, the recycled plastic materials are typically sorted and separated based on their types and colors. This initial step helps in identifying and targeting specific contaminants associated with different plastic types. For instance, certain plastics may have higher levels of contaminants due to their manufacturing processes or previous use.
Washing and Rinsing: The cleaned plastic is then subjected to a thorough washing process. This involves using high-pressure water jets or mechanical washing systems to remove any visible dirt, debris, and residual contaminants. The washing process aims to break down and dislodge any impurities that may be adhered to the plastic surface. After washing, a thorough rinsing is performed to eliminate any remaining soap, detergent, or loose particles.
Chemical Cleaning: In some cases, chemical cleaning agents are employed to address specific contaminants. This method is particularly useful for removing oil, grease, or other organic materials that may be present on the plastic. Chemical cleaners are carefully selected based on their compatibility with the plastic type to ensure no degradation or damage occurs. The plastic is immersed in the cleaning solution for a controlled period, allowing the chemicals to break down and dissolve the contaminants.
Filtration and Drying: After cleaning, the plastic material is often subjected to filtration to remove any remaining small particles or contaminants. This can be done using screens or filters with specific mesh sizes to capture different-sized particles. Once filtered, the plastic is thoroughly dried to eliminate moisture, which can affect the bonding and overall quality of the benches.
Quality Control: Throughout the cleaning process, quality control measures are implemented to ensure the effectiveness of the cleaning procedures. This includes visual inspections to check for any remaining contaminants and the use of specialized testing equipment to analyze the cleaned plastic's chemical composition. These steps guarantee that the recycled plastic meets the required standards before being formed into benches.
Portland's Plastic Recycling: A Green Revolution or a Misstep?
You may want to see also
Shredding: Plastic is shredded into small pieces for easier processing
The process of recycling plastic into benches begins with the collection and sorting of plastic waste. Once sorted, the plastic is prepared for the next stage, which is shredding. This initial step is crucial as it transforms the large, bulky plastic items into smaller, manageable pieces, making the subsequent processes more efficient.
Shredding is a mechanical process that involves reducing the size of the plastic waste. The plastic is fed into a shredder, which is a machine designed to cut and tear the material into tiny fragments. The shredder's blades rotate at high speeds, effectively breaking down the plastic into small, uniform pieces. This process is often done in a controlled environment to ensure the safety of the operators and to maintain the quality of the shredded material.
The shredded plastic is then sorted again to separate different types of plastic. This is important because different types of plastic have varying properties and uses. For example, high-density polyethylene (HDPE) is commonly used for food containers, while polypropylene (PP) is often used for packaging. By sorting the shredded plastic, recyclers can ensure that the final product meets the required specifications and can be used for specific applications.
After sorting, the shredded plastic is cleaned to remove any contaminants. This step is vital to ensure the quality and durability of the recycled plastic benches. Cleaning involves removing dirt, debris, and any remaining non-plastic materials. This can be done through various methods, such as washing the shredded plastic with water or using air classifiers to separate lighter materials.
Once cleaned, the shredded plastic is ready for the next phase, which is often pelletizing or molding, depending on the desired end product. Pelletizing involves shaping the shredded plastic into small, uniform pellets, which can then be used as raw material for manufacturing various plastic products, including benches. Molding, on the other hand, involves shaping the plastic into the desired form, such as a bench, using specialized machinery.
Unraveling the Recycling Mystery: 5 Plastics and Their Fate
You may want to see also
Molding: Shredded plastic is heated and formed into bench shapes using molds
The process of creating recycled plastic benches begins with the collection and sorting of plastic waste. This waste is then shredded into small pieces, ensuring a uniform size for optimal molding. The shredded plastic is a crucial component, as its quality directly impacts the final product's durability and aesthetics.
Once the plastic is shredded, it is fed into a heating machine, where it is subjected to high temperatures. This heating process is a critical step, as it softens the plastic and makes it pliable, allowing it to take the desired shape. The heated plastic is then carefully poured or injected into molds, which are designed to create the specific shape of the bench. These molds can be of various sizes and designs, depending on the intended style and functionality of the bench.
The molding process involves precise control of temperature and pressure to ensure the plastic takes the mold's shape accurately. This step requires skill and expertise to achieve the desired dimensions and surface finish. After the plastic has cooled and hardened within the mold, it is carefully removed, revealing the bench's structure. This process is repeated for each bench, creating a series of identical or unique pieces, depending on the production requirements.
The molds used in this process can be made from various materials, including metal or plastic, and are designed to withstand the high temperatures and pressures involved. The choice of mold material is essential to ensure the longevity of the tool and the quality of the final product. Advanced molding techniques, such as injection molding, may be employed to achieve consistent and intricate designs.
After molding, the benches may undergo additional processes like surface treatment, painting, or the addition of decorative elements to enhance their appearance. This step allows for customization and ensures that the final product meets the desired specifications. The entire process of recycling plastic to create benches is an eco-friendly alternative to traditional bench-making methods, reducing waste and promoting sustainability.
Can Plastic-Windowed Boxes Be Recycled? Unraveling the Mystery
You may want to see also
Frequently asked questions
The process begins with collecting and sorting plastic waste, which is then cleaned and shredded into small pieces. These plastic flakes are melted and molded into the desired shape of the bench, often using a blow molding technique. The final product is a sturdy and durable bench made from recycled materials.
Manufacturers use high-density polyethylene (HDPE) or polypropylene (PP) plastics, which are known for their durability and weather resistance. The recycling process involves adding stabilizers and UV inhibitors to the plastic, ensuring it can withstand outdoor conditions. Additionally, the molding process is precise, creating a solid structure that can support weight and last for years.
Absolutely! Recycling plastic for benches reduces the demand for virgin plastic production, which often relies on fossil fuels. By reusing plastic waste, we can conserve natural resources, decrease pollution from manufacturing, and divert waste from landfills or incinerators. This eco-friendly approach also promotes a circular economy, encouraging sustainable practices.
Yes, absolutely! Recycled plastic benches can be customized to fit specific design requirements and aesthetic preferences. Manufacturers can offer a range of colors, patterns, and styles, allowing for creative freedom. These benches can be produced in different sizes, shapes, and configurations, making them versatile for various applications, from public parks to residential gardens.