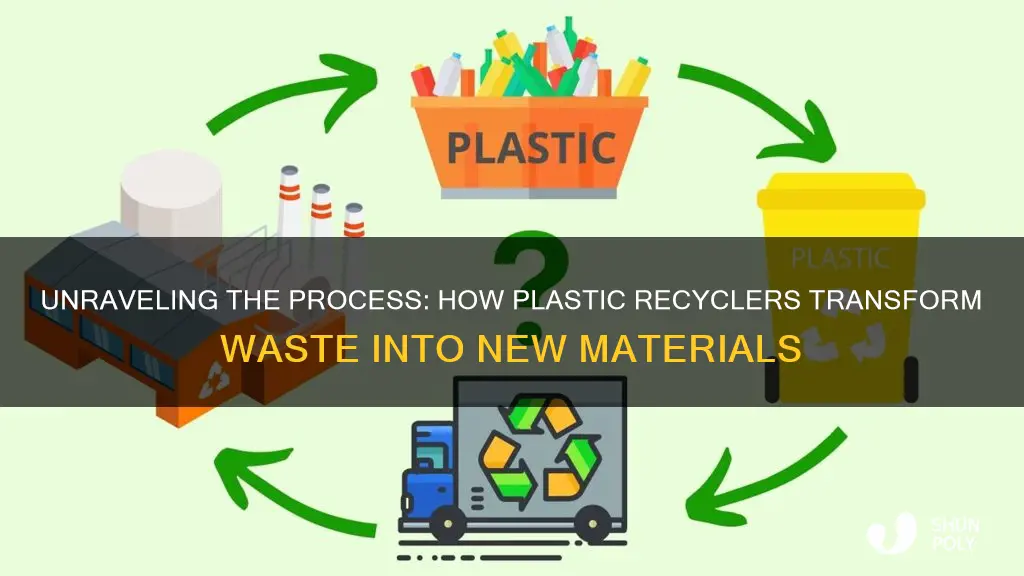
Plastic recycling is a crucial process in managing waste and reducing environmental impact. It involves transforming used plastic materials into new products, which can be achieved through various methods. The process typically begins with the collection and sorting of plastic waste, which is then cleaned and processed to remove contaminants. Different types of plastics are identified and sorted based on their resin identification codes, ensuring proper recycling. This initial step is followed by shredding or granulating the plastic into smaller pieces, which are then melted and molded into new forms. The efficiency and success of plastic recycling depend on the specific techniques used, such as chemical recycling, mechanical recycling, or a combination of both, each with its own advantages and limitations. Understanding these processes is essential to optimize recycling efforts and promote a more sustainable approach to plastic waste management.
What You'll Learn
Sorting: Plastic recyclers separate materials based on type and color
The process of recycling plastic begins with sorting, a crucial step that ensures the efficiency and effectiveness of the recycling system. Plastic recyclers employ various methods to separate different types of plastic materials, a task that is both complex and essential. The primary goal is to categorize plastics based on their resin identification codes, which are typically found on the bottom of plastic containers. These codes, ranging from 1 to 7, indicate the type of plastic used, allowing for precise sorting.
One common technique used in sorting is near-infrared (NIR) spectroscopy. This technology utilizes a spectrometer to analyze the light absorbed by the plastic material. Each type of plastic has a unique absorption spectrum, enabling the machine to identify and separate them. For instance, PET (polyethylene terephthalate), a common plastic used in beverage bottles, has a distinct absorption pattern, allowing it to be easily distinguished from other plastics. This method is highly accurate and can process large volumes of plastic waste efficiently.
Color separation is another critical aspect of the sorting process. Plastic recyclers often use color-sorting machines that employ optical sensors to detect and separate plastics based on their color. This is particularly important because certain colors, like clear and green, are more valuable in the recycling market due to their higher demand. For example, clear PET bottles are highly sought after for their use in making new containers, while green high-density polyethylene (HDPE) bottles are recycled into various products like brooms and brushes.
Advanced sorting systems may also incorporate machine learning algorithms to enhance their capabilities. These algorithms can learn from the data collected during the sorting process, improving their accuracy over time. By analyzing the characteristics of the plastic materials, such as their shape, size, and color, the machines can make more informed decisions, leading to a more efficient and precise sorting process.
In summary, the sorting process in plastic recycling is a sophisticated operation that relies on a combination of technologies. From NIR spectroscopy to color-sorting machines and machine learning, these methods ensure that plastic materials are separated effectively, preparing them for the next stage of the recycling journey. This detailed and meticulous approach is vital to the success of plastic recycling programs, contributing to a more sustainable and environmentally friendly future.
Alexandria's Plastic Recycling: Unveiling the 5-Item Mystery
You may want to see also
Cleaning: Removing contaminants like food residue and labels
The process of cleaning plastic recyclables is a crucial step in the recycling chain, ensuring that the materials are ready for the next phase of processing. This step is essential to remove contaminants that can compromise the quality of the recycled plastic and potentially lead to contamination of the entire batch. One of the primary contaminants that need to be addressed is food residue, which can come from various sources, such as leftover food from containers, cups, or packaging.
To effectively clean plastic items, a thorough washing process is required. This involves using warm water and a mild detergent or dish soap. The warm water helps to soften any dried-on food particles, making them easier to remove. It is important to scrub the inside and outside of the containers, ensuring that no residue remains. For items with complex shapes or hard-to-reach areas, a soft-bristled brush can be used to gently clean these surfaces without causing damage. After scrubbing, the plastic items should be rinsed thoroughly with clean water to remove any soap residue.
Another critical aspect of cleaning is removing labels and stickers. These can often be a significant source of contamination, especially if they are not removed properly. Labels are typically made of a different material than the plastic itself, and they can contain inks, glues, or other substances that are not recyclable. To remove labels, start by soaking the item in warm water for a few minutes to soften the label's adhesive. Then, gently peel the label off, taking care not to tear the plastic. If the label is stubborn and doesn't come off easily, a small amount of vegetable oil or cooking oil can be applied to the label's edge, allowing it to be lifted off without damaging the plastic.
Once the food residue and labels are removed, it is crucial to ensure that the plastic items are completely dry before the next step. Moisture can lead to mold growth and other issues during storage and transportation. A clean, dry environment can be created by placing the cleaned items on a drying rack or using a hairdryer on a low setting to speed up the drying process. Proper drying is essential to maintain the quality of the recycled plastic and to prevent any further contamination.
In summary, the cleaning process for plastic recyclables involves a meticulous approach to removing food residue and labels. By using warm water, detergents, and gentle cleaning tools, the goal is to ensure that the plastic items are free from any contaminants. Proper drying techniques are also vital to prevent mold and maintain the integrity of the recycling process. These steps contribute to the overall efficiency and effectiveness of plastic recycling, making it an essential practice in sustainable waste management.
Big Y's Plastic Recycling: Uncovering the Truth
You may want to see also
Shredding: Reducing plastic waste to flakes or pellets
Shredding is a crucial step in the recycling process of plastic waste, transforming it into a more manageable and valuable form. This process involves reducing large plastic items, such as bottles, containers, and packaging, into smaller pieces, typically flakes or pellets. The primary goal is to increase the surface area of the plastic, making it easier to handle and process while also enhancing its recyclability.
The shredding process begins with the collection and sorting of plastic waste. Different types of plastics require specific shredding techniques, so proper sorting is essential. For instance, high-density polyethylene (HDPE) and polypropylene (PP) are commonly shredded into flakes, while low-density polyethylene (LDPE) and polyvinyl chloride (PVC) might be shredded into smaller pellets. Once sorted, the plastic waste is fed into a shredder, which can be a mechanical shredder or a granulator.
Mechanical shredders are widely used and operate by rotating blades or rollers that tear and cut the plastic into smaller pieces. These machines can handle various plastic types and are capable of producing flakes or pellets, depending on the desired output size. The shredded plastic is then conveyed and often washed to remove any remaining contaminants, ensuring a cleaner and more consistent product.
Granulators, on the other hand, use a different mechanism. They involve a rotating drum with a series of blades or teeth that grind and compress the plastic waste. This process reduces the plastic to a fine powder or small pellets. Granulators are particularly useful for producing high-quality, uniform pellets, which can then be further processed or sold to manufacturers.
After shredding, the plastic flakes or pellets are further processed to remove any remaining impurities. This may include washing, drying, and sorting to ensure the final product meets the required standards. The cleaned and sorted plastic flakes or pellets can then be used in various applications, such as manufacturing new plastic products, creating composite materials, or even being sold back to the original plastic producers for reprocessing.
Transform Old CD Cases: A Guide to Plastic Recycling
You may want to see also
Melting: Heating and transforming plastic into a usable form
The process of recycling plastic begins with the collection and sorting of plastic waste, ensuring that different types of plastics are separated to facilitate the recycling process. Once sorted, the plastic is prepared for the melting stage, which is a crucial step in transforming it into a reusable material.
Melting involves heating the plastic to a specific temperature, causing it to change from a solid state to a liquid. This process requires specialized equipment, such as industrial-grade ovens or melters, designed to handle the unique properties of various plastic types. The temperature and duration of heating are carefully controlled to ensure the plastic's chemical structure remains intact while achieving a molten state. Different plastics have varying melting points, so precise temperature control is essential to avoid damaging or altering the material.
During melting, the plastic is subjected to intense heat, typically in a controlled environment to prevent contamination. The heat energy is transferred to the plastic, breaking the intermolecular bonds and allowing the polymer chains to move freely. This transformation enables the plastic to take on a more fluid form, making it easier to manipulate and mold into new shapes. The molten plastic can then be extruded, molded, or shaped into various products, such as pellets, sheets, or even new containers.
This stage of the recycling process requires expertise to ensure the quality and purity of the recycled material. Impurities or contaminants must be removed to maintain the integrity of the final product. Advanced filtration and purification techniques are employed to separate any non-plastic substances, ensuring the recycled plastic meets the required standards for reuse.
After melting, the plastic is cooled and solidified, ready for further processing or direct use in manufacturing. This step allows the material to retain its new shape and form, which can then be utilized in the production of new items, contributing to a more sustainable and circular economy. The melting process is a critical aspect of plastic recycling, enabling the transformation of waste into valuable resources.
Transforming Recycled Plastic: A Journey from Waste to Warrior Gear
You may want to see also
Molding: Shaping molten plastic into new products
The process of molding is a crucial step in the transformation of recycled plastic into new products, allowing for the creation of a wide range of items from packaging to automotive parts. This method involves shaping molten plastic, which is a semi-liquid state of the material, into the desired form using a mold. The mold is essentially a cavity or a form that dictates the shape of the final product. Here's an overview of the molding process:
Melting and Preparation: The recycling process begins with collecting and sorting plastic waste. This sorted plastic is then shredded or granulated to reduce its size and make it easier to handle. The next step is to melt the plastic, which is typically done in a specialized machine called a plasticizer or an extruder. During melting, the plastic is heated to its glass transition temperature, a specific temperature at which the material changes from a hard, brittle state to a soft, malleable one. This process ensures that the plastic can be easily shaped without losing its structural integrity.
Injection Molding: This is one of the most common molding techniques used in the plastic industry. In this process, the molten plastic is injected into the mold at high pressure. The mold is designed with a specific cavity that matches the desired shape of the product. As the plastic fills the mold, it takes the form of the cavity, creating a precise and consistent shape. Once the plastic has cooled and hardened, the mold is opened, and the finished product is removed. This method is highly efficient and can produce a large volume of products with minimal waste.
Compression Molding: Another molding technique is compression molding, which is often used for producing solid, homogeneous parts. In this process, the plastic, in the form of a sheet or a pre-formed part, is placed in the mold. The mold is then closed, and the plastic is subjected to heat and pressure to force it into the mold's cavity. This method is particularly useful for creating products with complex shapes and multiple cavities in a single mold.
Advantages of Molding: Molding offers several advantages in the recycling and production of plastic goods. Firstly, it allows for the creation of intricate and precise shapes, making it suitable for manufacturing a wide variety of products. The process can be highly automated, increasing efficiency and productivity. Additionally, molding can produce large quantities of products in a short time, making it cost-effective for mass production. The use of molds also ensures consistency in the final products, meeting the required specifications.
Post-Molding Processes: After the molding process, additional steps may be required to finish the product. This can include trimming excess material, adding fasteners or inserts, and performing surface treatments to enhance the product's appearance and functionality. These post-molding processes contribute to the overall quality and performance of the final plastic item.
Unraveling the Mystery: Can Plastic Binder Dividers Be Recycled?
You may want to see also
Frequently asked questions
Plastic recycling involves collecting, sorting, and processing plastic waste to create new products. It typically begins with the collection of used plastic items, which are then sorted by type and color. The sorted plastics are cleaned, shredded, or melted to create raw materials that can be used in manufacturing.
Plastic recyclers use various methods to identify and separate different types of plastics. One common method is to look at the resin identification code, a number usually found on the bottom of plastic containers. This code, ranging from 1 to 7, indicates the type of plastic. For example, PET (polyethylene terephthalate) has a code 1, while HDPE (high-density polyethylene) has a code 2.
Not all plastics are recyclable. The recyclability of plastic depends on its type and the recycling infrastructure available. Common recyclable plastics include PET, HDPE, and some types of PVC. However, plastics like styrofoam (polystyrene) and certain types of flexible plastics may have limited recycling options.
After processing, the recycled plastic is transformed into raw materials or pellets, which can then be used by manufacturers to create new products. These products can range from packaging materials, bottles, and containers to furniture, construction materials, and even clothing. The process helps reduce the demand for virgin plastic production and promotes a circular economy.
Yes, plastic recycling faces several challenges. One major issue is contamination, where non-plastic materials or food residue are mixed with plastic waste, making it difficult to process. Additionally, the recycling process can be energy-intensive, and not all plastics are easily recyclable. Educating the public about proper waste segregation and supporting advanced recycling technologies are crucial to improving the efficiency of plastic recycling.