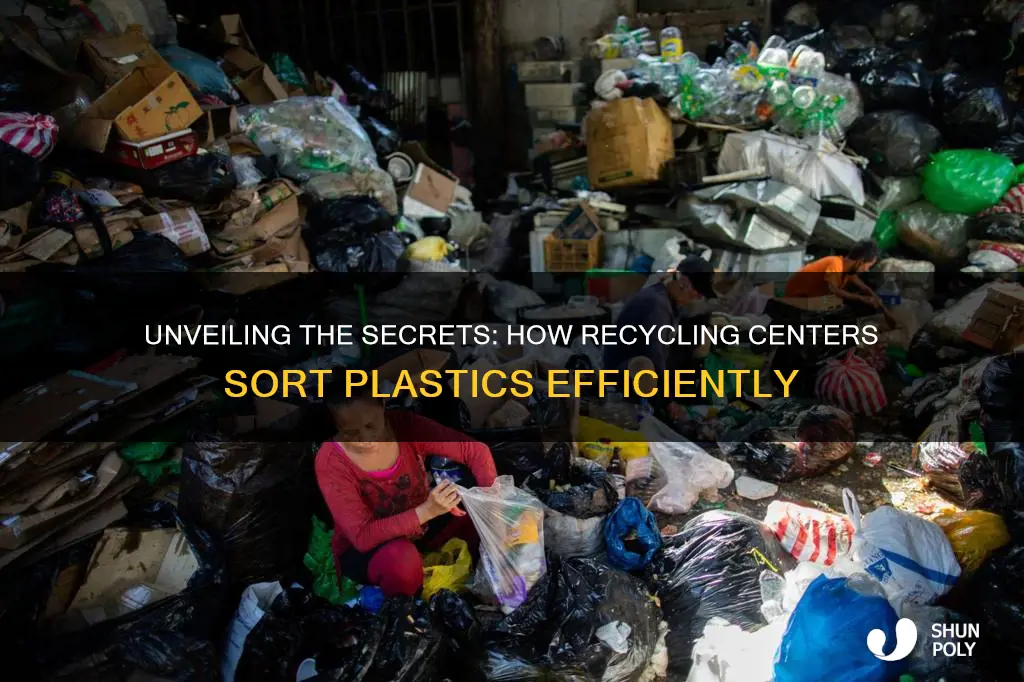
Recycling centers play a crucial role in the plastic waste management process, and their ability to efficiently sort plastics is essential for the recycling chain. The sorting process begins with the arrival of plastic materials, which are then sorted into different categories based on their type and quality. This initial step is vital as it determines the feasibility of recycling each plastic type. Common methods include manual sorting, where workers visually inspect and separate plastics, and automated systems that use sensors and machines to identify and categorize materials. The goal is to streamline the recycling process, ensuring that each type of plastic is recycled appropriately, which is key to maintaining the integrity of the recycling stream and promoting a sustainable approach to waste management.
Characteristics | Values |
---|---|
Sorting Methods | Hand Sorting, Optical Sorters, Near-Infrared (NIR) Sorters, Density-Based Sorting, Water Jets |
Plastic Types | PET (Polyethylene Terephthalate), HDPE (High-Density Polyethylene), LDPE (Low-Density Polyethylene), PP (Polypropylene), PS (Polystyrene), PVC (Polyvinyl Chloride) |
Color Sorting | Red, Green, Blue, Clear, Black, White |
Size and Shape | Flakes, Pellets, Granules, Sheets, Film |
Contamination Removal | Magnetic Separators, Eddy Current Separators, Air Classifiers, Water Wash Systems |
Density Differences | Buoyancy in Water, Gravity Separation |
Near-Infrared (NIR) Technology | Identifies plastic types based on molecular structure |
Hand Sorting | Manual separation by trained workers |
Optical Sorters | Use cameras and sensors to identify colors and types |
Water Jets | Wash and separate plastics based on density |
Magnetic Separators | Remove ferrous metals from plastic waste |
Eddy Current Separators | Separate non-ferrous metals from plastics |
Air Classifiers | Use air currents to separate plastics by size and density |
Buoyancy in Water | Separate plastics based on their density in water |
Gravity Separation | Utilize gravity to separate materials of different densities |
What You'll Learn
- Sorting by Type: Recycling centers use color-coded systems to separate plastics into types like PET, HDPE, and LDPE
- Density Separation: Conveyor belts and air classifiers separate plastics based on their density, allowing for more efficient processing
- Optical Sorting: Advanced machines use light sensors to identify different types of plastics based on their unique optical properties
- Magnetic Separation: Metals and ferrous materials are removed from plastics using magnetic separators, ensuring cleaner end products
- Manual Sorting: Human workers may be involved in the final stages to identify and remove any remaining contaminants or non-plastic items
Sorting by Type: Recycling centers use color-coded systems to separate plastics into types like PET, HDPE, and LDPE
Recycling centers employ a systematic approach to sorting plastics, utilizing color-coded systems to categorize different types of plastic materials. This method is crucial for efficient recycling processes and ensuring that each type of plastic is processed appropriately. The primary goal is to separate plastics into various categories, such as PET (polyethylene terephthalate), HDPE (high-density polyethylene), and LDPE (low-density polyethylene), each with its unique properties and applications in recycling.
PET, commonly known as the plastic used in beverage bottles, is easily recognizable by its clear or slightly tinted appearance. Recycling centers often use a green or blue color-coding system to identify PET. This type of plastic is widely accepted in recycling streams and has a high value in the recycling market due to its versatility and ease of processing. PET is often used to create new containers, textiles, and even furniture, showcasing its sustainability potential.
HDPE, on the other hand, is a sturdy and rigid plastic commonly found in milk jugs, shampoo bottles, and some grocery bags. It is typically identified by its white or slightly translucent color. Recycling centers use a yellow or brown color code to distinguish HDPE from other plastics. This type of plastic is highly recyclable and can be transformed into various products, including new containers, outdoor furniture, and even carpet fibers.
LDPE, a flexible and lightweight plastic, is prevalent in shopping bags, film wraps, and some food containers. Its characteristic transparency and softness make it easily identifiable. Recycling centers often use a black or dark blue color-coding system for LDPE. This plastic type is valuable in recycling as it can be recycled into new products like garbage bags, bin liners, and even outdoor furniture, demonstrating its versatility in the recycling process.
The color-coded system employed by recycling centers is a simple yet effective method to ensure proper sorting and processing of plastics. By categorizing plastics into distinct types, recycling centers can optimize their operations, increase recycling efficiency, and reduce contamination. This approach also allows for better management of the recycling stream, ensuring that each type of plastic is directed to the appropriate recycling facility or process, ultimately contributing to a more sustainable and environmentally friendly recycling system.
Unraveling Minneapolis's Plastic Recycling Mystery: 5 Key Insights
You may want to see also
Density Separation: Conveyor belts and air classifiers separate plastics based on their density, allowing for more efficient processing
Density separation is a crucial process in recycling centers, enabling the efficient sorting of plastics based on their unique physical properties. This method takes advantage of the fact that different types of plastics have varying densities, which can be utilized to separate them effectively. The process begins with the arrival of mixed plastic waste at the recycling facility. Conveyor belts, an essential component of the density separation system, are employed to transport the waste along a series of channels or lanes. These belts are strategically designed with different speeds and angles to facilitate the separation process.
As the waste moves along the conveyor, air classifiers are used in conjunction with the belts to further enhance the sorting process. Air classifiers utilize air pressure to separate plastics based on their density. Lighter plastics, such as those used in packaging and film, are given a gentle upward air current, causing them to move away from the heavier materials. This technique effectively creates a physical barrier, allowing for the separation of plastics with minimal manual intervention. The air classifiers are designed to create a controlled environment where the air pressure and velocity are optimized to separate the plastics efficiently.
The conveyor belts play a critical role in this process by providing a continuous and controlled movement of the waste. They are often equipped with sensors and monitoring systems to ensure precise control over the sorting process. By adjusting the speed and direction of the belts, operators can guide the plastics along specific paths, separating them into different categories. This method is particularly useful for sorting a wide range of plastic types, including PET, HDPE, LDPE, and more.
Density separation offers several advantages in recycling operations. Firstly, it significantly reduces the manual labor required for sorting, making the process more efficient and cost-effective. Secondly, it allows for a higher degree of purity in the separated plastics, which is essential for downstream processing and the production of new products. The sorted plastics can then be directed to specific areas or machines for further processing, such as washing, granulating, or manufacturing new items.
In summary, density separation, utilizing conveyor belts and air classifiers, is a powerful technique employed by recycling centers to sort plastics efficiently. This method takes advantage of the natural variations in density among different plastic types, providing a more automated and precise approach to recycling. By implementing this process, recycling facilities can improve the overall quality of recycled materials and contribute to a more sustainable waste management system.
Plastic Planters: Can They Be Recycled?
You may want to see also
Optical Sorting: Advanced machines use light sensors to identify different types of plastics based on their unique optical properties
In the world of recycling, efficient sorting of plastics is crucial to ensure that materials are properly processed and can be effectively reused. One of the most advanced techniques employed by recycling centers is optical sorting, which revolutionizes the way plastics are identified and separated. This method utilizes the unique optical properties of various plastic types, allowing for precise classification.
Optical sorting machines are equipped with sophisticated light sensors that play a pivotal role in the sorting process. These sensors detect and analyze the interaction of light with different plastics, as each type of plastic has distinct characteristics in terms of color, transparency, and reflectivity. For instance, high-density polyethylene (HDPE) bottles appear more opaque and have a higher reflectivity compared to polypropylene (PP) containers, which are often translucent. By measuring these optical properties, the machines can differentiate between various plastic types with remarkable accuracy.
The process begins when a stream of mixed plastics is fed into the optical sorter. The light sensors emit a beam of light, which interacts with the incoming materials. The sensors then analyze the reflected or transmitted light, creating a detailed profile of each plastic item. This profile includes information about color, intensity, and other optical characteristics. Through advanced algorithms, the machine learns to recognize the unique patterns associated with different plastic types, enabling it to make accurate sorting decisions.
Once the optical sensors have analyzed the plastics, the sorted materials are conveyed to different output bins. For example, clear HDPE bottles might be directed to one bin, while green PP yogurt cups are sorted into another. This level of precision ensures that the recycling process becomes more efficient, reducing the likelihood of contamination and improving the overall quality of the sorted plastics.
Optical sorting technology has significantly enhanced the capabilities of recycling centers, allowing them to handle larger volumes of plastic waste with greater accuracy. This method not only streamlines the sorting process but also contributes to a more sustainable approach to recycling, making it an invaluable tool in the global effort to manage and reduce plastic waste.
The Recycling Myth: Unveiling America's Plastic Waste Crisis
You may want to see also
Magnetic Separation: Metals and ferrous materials are removed from plastics using magnetic separators, ensuring cleaner end products
Magnetic separation is a crucial process in recycling centers, especially when it comes to sorting and processing plastics. This method is primarily employed to separate ferrous metals and other magnetic materials from plastic waste, ensuring a cleaner and more efficient recycling stream. The process is designed to enhance the quality of the end products and facilitate the recycling of plastics more effectively.
Recycling centers often receive a mixed stream of plastic waste, which can contain various types of plastics, colors, and contaminants. Among these contaminants, ferrous metals and other magnetic materials are of particular concern. These metals can interfere with the recycling process and the quality of the recycled plastic. Magnetic separation is an effective way to address this issue.
The process begins with the use of powerful magnetic separators, which are strategically placed in the recycling line. These separators generate a strong magnetic field that attracts and captures ferrous metals and other magnetic materials. As the plastic waste passes through the magnetic field, the metals are drawn towards the separator, effectively separating them from the plastic stream. This initial separation step is vital as it prevents metals from contaminating the recycled plastics, ensuring a higher-quality end product.
After the magnetic separation, the plastic waste continues through the recycling process. Non-ferrous metals, such as aluminum and copper, are typically removed through other methods like eddy current separation or air tables. However, the initial magnetic separation has already contributed to a cleaner stream, making subsequent processes more efficient. The separated metals are then collected and recycled separately, while the plastic material continues its journey towards being transformed into new products.
This method of magnetic separation is an essential part of modern recycling infrastructure. It allows recycling centers to produce high-quality recycled plastics, which are essential for various industries. By removing metals and other contaminants, the process ensures that the recycled plastics meet the required standards and can be used in manufacturing, construction, and other applications. This not only benefits the recycling industry but also contributes to a more sustainable and environmentally friendly approach to waste management.
Aldi's Soft Plastic Recycling Initiative: A Green Revolution
You may want to see also
Manual Sorting: Human workers may be involved in the final stages to identify and remove any remaining contaminants or non-plastic items
In the intricate process of recycling plastics, manual sorting plays a crucial role, especially in the final stages of recycling centers' operations. Human workers are often the last line of defense, ensuring the highest quality of sorted materials. This step is essential as it involves meticulous identification and removal of any contaminants or non-plastic items that might have slipped through the initial automated processes.
The manual sorting process begins with trained personnel examining the sorted plastic materials. These workers are skilled in identifying different types of plastics, which is a critical task as it determines the end use of the recycled material. For instance, PET (polyethylene terephthalate) is commonly used for beverage bottles, while HDPE (high-density polyethylene) is ideal for milk jugs. The ability to distinguish between these types is vital for maintaining the integrity of the recycling stream.
During this stage, workers also look for and remove any non-plastic items that might have been missed during the automated sorting. This includes items like metal caps, labels, or any other foreign matter that could compromise the quality of the recycled plastic. The human eye is particularly adept at spotting small details, making it an invaluable asset in this process. For example, a worker might notice a small metal screw or a piece of paper that could potentially damage the machinery in the recycling process or reduce the value of the final product.
Contaminants, such as food residue or liquids, are also identified and removed during manual sorting. These items can affect the performance and quality of the recycled plastic, making this step essential for maintaining high standards. Workers use a combination of tools and their hands to carefully extract these contaminants, ensuring that the final product is clean and suitable for its intended purpose.
The manual sorting process is a labor-intensive but critical phase in recycling centers. It requires a high level of skill and attention to detail, as workers must make quick decisions about the suitability of each item. This final stage ensures that the recycled plastics are of the highest quality, contributing to the overall success of the recycling program and the sustainability of the materials.
Unraveling the Mystery: Can Plastic Beads Be Recycled?
You may want to see also
Frequently asked questions
Recycling centers employ various methods to sort plastics, ensuring efficient and effective processing. The initial step often involves manual sorting, where workers separate plastics based on their types and colors. This manual process helps in identifying different plastic resins, such as PET (polyethylene terephthalate), HDPE (high-density polyethylene), and LDPE (low-density polyethylene).
Identification of plastic types is crucial for proper recycling. Recycling centers use a combination of techniques, including visual inspection, density testing, and near-infrared (NIR) spectroscopy. Visual inspection allows workers to identify common plastic types like water bottles (PET) and milk jugs (HDPE) by their distinct colors and shapes. Density testing uses a platform to separate plastics based on their weight and buoyancy. NIR spectroscopy is a more advanced method, utilizing light to identify plastic resins by their unique molecular structures.
Sorting plastics can present challenges due to the vast number of plastic items and the need for accuracy. One challenge is the presence of mixed plastics, where items contain multiple resins. Recycling centers use advanced sorting machines, such as optical sorters and eddy current separators, to separate these mixed plastics. These machines can identify and separate different resins based on their properties, ensuring proper recycling. Additionally, some centers employ artificial intelligence and machine learning to improve sorting efficiency and accuracy.
Contamination is a significant issue in recycling, and recycling centers have measures to address it. When plastics are contaminated with food residue, labels, or other non-plastic materials, they are often removed and processed separately. This may involve manual sorting or using specialized equipment to separate contaminants. Recycling centers also educate the public on proper recycling practices to minimize contamination. Some centers implement contamination-sorting systems, where plastics are sorted based on their level of contamination, ensuring that clean plastics are recycled effectively.