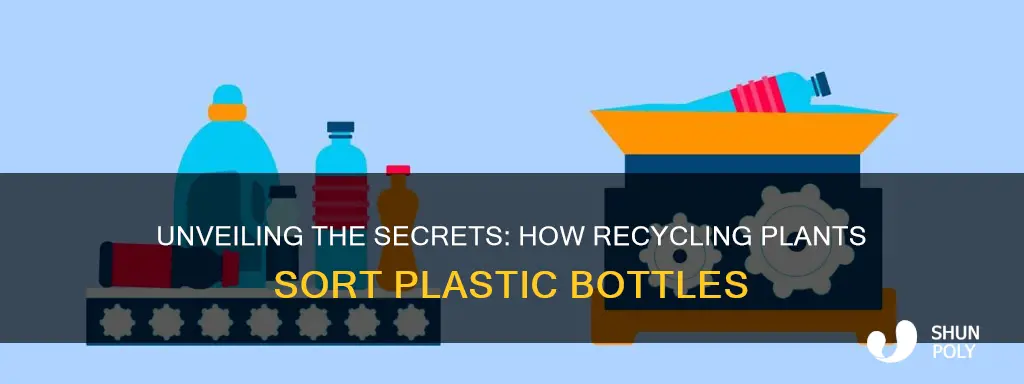
Recycling companies employ various methods to efficiently separate plastic bottles, a crucial step in the recycling process. One common technique is manual sorting, where trained workers visually inspect and separate bottles based on their color and type. Advanced technologies, such as optical sorters and near-infrared (NIR) spectroscopy, are also utilized to identify and categorize different types of plastics. These machines can detect variations in color, material density, and chemical composition, ensuring accurate separation. Additionally, some facilities use air classifiers to separate plastic bottles based on their size and shape. The goal is to streamline the recycling process, making it more efficient and effective in transforming used plastic bottles into raw materials for new products.
What You'll Learn
- Sorting Technology: Advanced machines use infrared and optical sensors to identify plastic types
- Manual Sorting: Workers visually inspect and separate plastics by color and type
- Density Separation: Water or air currents separate plastics based on their density
- Shredding and Grinding: Plastic bottles are shredded or ground into flakes for easier processing
- Melting and Molding: Recycled plastics are melted and molded into new products
Sorting Technology: Advanced machines use infrared and optical sensors to identify plastic types
In the world of recycling, the efficient separation of plastic bottles is a crucial process that enables the recovery of valuable materials. One of the most innovative methods employed by recycling companies is the use of advanced sorting technology, which utilizes infrared and optical sensors to identify and categorize different types of plastics. This sophisticated approach has revolutionized the recycling industry, ensuring a more precise and effective separation process.
Advanced sorting machines are designed to handle a high volume of plastic waste, making them essential in large-scale recycling operations. These machines employ a combination of infrared and optical sensors, each serving a unique purpose in the identification process. Infrared sensors detect the heat signatures of various plastic materials, allowing them to differentiate between different types based on their thermal properties. For instance, PET (polyethylene terephthalate) bottles, commonly used for beverages, emit a distinct heat signature, enabling the machine to separate them from other plastic types. This method is particularly useful for identifying and sorting PET bottles, which are highly recyclable and valuable in the recycling market.
Optical sensors, on the other hand, analyze the visual characteristics of plastic items. These sensors can detect differences in color, shape, and surface patterns, which are often unique to specific plastic types. For example, HDPE (high-density polyethylene) bottles, often used for milk and cleaning products, have a distinct appearance that optical sensors can identify. By combining infrared and optical sensing, these machines create a comprehensive profile of each plastic item, ensuring accurate sorting.
The process begins with a feed of mixed plastic waste, which is then guided through a series of conveyor belts and sensors. As the waste moves along, the infrared and optical sensors work in tandem to analyze each item. The sensors provide real-time data, allowing the machine to make immediate decisions on the type and quality of the plastic. This technology enables the machine to separate plastics into different streams, such as PET, HDPE, and others, with remarkable precision. The sorted plastics are then directed to respective collection areas, ready for further processing or recycling.
This advanced sorting technology has significantly improved the efficiency and accuracy of plastic recycling. It reduces the reliance on manual sorting, which can be time-consuming and prone to errors. By automating the process, recycling companies can process larger volumes of waste, contributing to a more sustainable and environmentally friendly approach to waste management. Moreover, the use of infrared and optical sensors ensures that the sorted plastics are of high quality, meeting the standards required for various recycling applications.
Bic Plastic Recycling: Unraveling the Mystery of Its Sustainability
You may want to see also
Manual Sorting: Workers visually inspect and separate plastics by color and type
Manual sorting is a crucial step in the recycling process, especially when it comes to separating plastic bottles. This method relies on the keen eyes and skilled hands of human workers to ensure the highest level of precision and quality control. Here's a detailed breakdown of this process:
In the recycling facility, a team of trained workers is assigned to the manual sorting area. This area is often a well-lit, organized space with designated stations for each type of plastic. The workers are equipped with gloves and protective gear to ensure their safety and comfort during the sorting process. The primary goal is to visually inspect each plastic bottle and categorize them based on their color and type.
The process begins with a thorough inspection. Workers carefully examine each bottle, looking for any signs of contamination, damage, or incorrect labeling. For instance, they identify PET (polyethylene terephthalate) bottles, which are commonly used for beverages, and HDPE (high-density polyethylene) bottles, often used for milk and shampoo. The workers also pay close attention to colors; clear, green, and brown bottles are separated to ensure they are recycled accordingly. This visual identification is a critical step as it prevents the mixing of different plastic types, which can lead to contamination and recycling challenges.
Once the inspection is complete, the workers employ various techniques to separate the plastics. They use their hands to gently squeeze and feel the bottles, distinguishing between the different types of plastic. For example, PET bottles are typically more flexible and have a distinct feel compared to HDPE bottles, which are stiffer. Workers also rely on their sense of touch to identify any lightweight or heavy bottles, further categorizing them. This tactile approach, combined with visual inspection, ensures an efficient and accurate sorting process.
Color-coded systems are often employed to make the sorting process more efficient. Workers may be assigned specific color-coded bins or areas, allowing them to quickly place the bottles in the correct category. This method streamlines the process, especially when dealing with large volumes of plastic. Additionally, workers may be trained to recognize specific patterns or markings on the bottles, further aiding in their identification and separation.
Manual sorting is a labor-intensive process but is essential for maintaining the integrity of the recycling stream. It allows for the removal of contaminants and ensures that the recycled plastics are of high quality. This method is particularly important when dealing with mixed plastic streams, where different types of plastics are combined, and advanced sorting technologies might not be feasible or cost-effective. By employing skilled workers, recycling companies can achieve a high level of purity in their recycled plastic materials.
Unraveling the Mystery: Can Plastic Zip Ties Be Recycled?
You may want to see also
Density Separation: Water or air currents separate plastics based on their density
Density separation is a crucial process in recycling plastic bottles, allowing for the efficient sorting and recovery of different types of plastics. This method takes advantage of the unique physical properties of various plastic materials, particularly their density, to separate them from one another. The process involves the use of water or air currents to gently guide and separate the plastics based on their weight and buoyancy.
In this technique, a stream of water or air is directed at the plastic bottles, which are often pre-sorted by color or type. The higher the density of the plastic, the more it will resist the force of the water or air current and remain in place. Conversely, lower-density plastics will be more easily carried away by the current. This simple yet effective method allows for the initial separation of plastics into different categories.
For instance, high-density polyethylene (HDPE) bottles, which are commonly used for milk and water containers, have a higher density and will settle at the bottom of a water-filled container. On the other hand, lower-density plastics like polypropylene (PP) and polystyrene (PS) will float to the top. By utilizing this principle, recycling facilities can quickly and accurately separate these materials.
Air currents can also be employed in a similar manner. As air is blown through a stream of mixed plastics, the denser materials will be pushed back, while the lighter ones will move forward. This method is particularly useful for separating plastics with very similar densities, as the air current can provide a more precise and gentle separation.
Density separation is an essential step in the recycling process, as it enables the subsequent steps of cleaning, processing, and manufacturing new products from the sorted plastics. It is a cost-effective and environmentally friendly approach, ensuring that the recycling stream is clean and organized, ready for further use in creating new plastic items. This method plays a vital role in the circular economy, promoting sustainability and reducing waste.
The Surprising Truth: Only a Fraction of Our Plastic Waste Gets Recycled
You may want to see also
Shredding and Grinding: Plastic bottles are shredded or ground into flakes for easier processing
Plastic bottle recycling is a crucial process in the journey towards a more sustainable future, and the initial step of shredding and grinding plays a pivotal role in preparing these bottles for further processing. This method is employed by recycling companies to transform plastic bottles into a more manageable and valuable form, known as plastic flakes.
The shredding process begins with the collection of used plastic bottles, which are then sorted by color and type to ensure efficient recycling. These bottles are fed into specialized machines designed for shredding. The machines use sharp blades or rotating knives to cut the bottles into small, uniform pieces, typically in the form of flakes. This step is essential as it reduces the volume of the plastic waste, making it easier to handle and transport. The shredded flakes are then cleaned to remove any contaminants, such as labels, caps, or other non-plastic materials, ensuring that the final product meets the required quality standards.
Grinding, often used in conjunction with shredding, takes the shredded plastic flakes and further processes them into even smaller particles. This step increases the surface area of the plastic, making it more susceptible to chemical treatments and subsequent recycling processes. Grinding machines use high-speed rotating blades to break down the flakes into a fine powder or granulate. This process is particularly useful for creating a consistent and homogeneous material, which is crucial for manufacturing new plastic products.
The shredded and ground plastic flakes are then washed to remove any remaining impurities, ensuring that the final product is clean and free from contaminants. This washing process is often done using water or specialized cleaning solutions. After washing, the flakes are dried to remove excess moisture, which is essential for their storage and transportation. The dried flakes are then stored in large bags or silos, ready for the next stage of the recycling process, where they will be melted and molded into new products.
This initial shredding and grinding process is a critical step in the recycling chain, as it sets the foundation for the entire recycling journey. By reducing the size and volume of plastic bottles, recycling companies can efficiently separate and process different types of plastics, ensuring a more sustainable and environmentally friendly approach to waste management.
Understanding Plastic Recycling: A Guide to What's Recyclable
You may want to see also
Melting and Molding: Recycled plastics are melted and molded into new products
The process of recycling plastic bottles involves several intricate steps, and one of the most crucial stages is indeed the melting and molding process. This phase transforms collected plastic waste into new, usable materials, showcasing the potential for a circular economy. Here's a detailed breakdown of this fascinating transformation:
Once plastic bottles are collected and sorted, they undergo a meticulous cleaning process to remove any contaminants. This step is vital as it ensures the quality of the recycled material. After cleaning, the plastic bottles are shredded into small pieces, a process that prepares them for the next stage. The shredded plastic is then sorted by type, a critical step to ensure compatibility with the molding process. Different types of plastics, such as PET (polyethylene terephthalate) and HDPE (high-density polyethylene), require specific melting temperatures and processes.
The sorted and prepared plastic flakes are now ready for melting. This is typically done in specialized equipment called extruders. The extruder heats the plastic to its melting point, transforming it into a molten state. The temperature and duration of this process vary depending on the type of plastic. For instance, PET melts at around 250-260°C, while HDPE requires a slightly lower temperature. The molten plastic is then extruded through a die, which shapes it into a continuous strand or sheet. This strand or sheet is cooled and cut into small pellets, known as 'nurdles' or 'plastic resin.'
These plastic pellets are the raw material for manufacturing new products. They are sold to manufacturers who use them to create a wide array of items. The molding process involves injecting the molten plastic into a mold, which gives it the desired shape. This can be done through various molding techniques, such as injection molding, blow molding, or compression molding, each suited for specific product requirements. Once the plastic solidifies in the mold, it is removed, and the cycle continues with new molds and designs.
The melting and molding process is a testament to the ingenuity of recycling companies, allowing them to breathe new life into old plastic bottles. It showcases the potential for sustainable practices, reducing waste and conserving resources. This method not only contributes to environmental conservation but also fosters a more efficient and circular approach to manufacturing, benefiting both the planet and the economy.
Blue Plastic Tarps: Unraveling the Recycling Mystery
You may want to see also
Frequently asked questions
Recycling facilities employ various methods to separate plastic bottles, primarily using a combination of mechanical and manual processes. The initial step involves a process called "material recovery," where different types of recyclables, including plastic, paper, glass, and metal, are sorted based on their physical properties. Plastic bottles are typically separated from other plastics and non-plastic materials through a process called "air classification," where air is blown through a series of screens, separating lighter materials like plastic from heavier items.
Advanced technologies like near-infrared (NIR) spectroscopy and optical sorters are employed to identify and separate different types of plastics. NIR spectroscopy uses light to analyze the molecular structure of materials, allowing it to distinguish between various plastic types, such as PET (polyethylene terephthalate) and HDPE (high-density polyethylene). Optical sorters use cameras and sensors to identify colors and shapes, ensuring that only the desired plastic types are collected.
Yes, the separation of plastic bottles can present several challenges. One significant issue is the presence of contaminants, such as labels, caps, or non-plastic materials, which can interfere with the recycling process. Recycling companies use additional sorting techniques, like eddy currents and magnetic separation, to remove these contaminants. Another challenge is the presence of different plastic types in a single stream, requiring advanced sorting technologies to ensure proper identification and separation.
After separation, the plastics are typically sorted into different streams based on their types and qualities. High-quality plastics, like PET bottles, are often sold to manufacturers who use them to produce new products. Lower-grade plastics may be downcycled into products like fleece jackets or used for industrial applications. The goal is to maximize the value of the recycled materials and minimize waste, contributing to a more sustainable and circular economy.