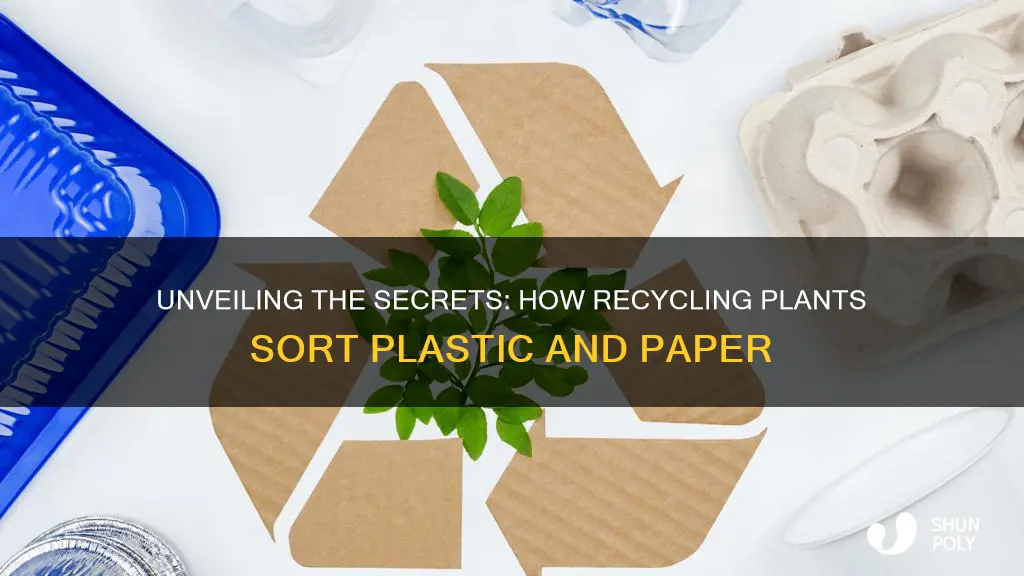
Recycling plants employ various methods to efficiently separate plastic and paper, ensuring a streamlined recycling process. These techniques include mechanical sorting, where materials are separated based on size and density, and optical sorting, which uses sensors to identify different types of paper and plastic. Additionally, eddy current separators can separate ferrous and non-ferrous metals, while water flotation systems can distinguish between materials based on their buoyancy. These advanced technologies play a crucial role in maximizing recycling efficiency and minimizing contamination, ultimately contributing to a more sustainable waste management system.
What You'll Learn
- Sorting Technology: Advanced machines use optical scanners and infrared sensors to identify materials
- Conveyor Belts: These transport materials through various processes, separating plastic and paper
- Magnetic Separation: Metal detectors and magnets remove ferrous materials, leaving plastic and paper
- Water Flotation: Paper floats on water, while plastic sinks, aiding in separation
- Human Inspection: Workers verify and adjust the process, ensuring accurate material separation
Sorting Technology: Advanced machines use optical scanners and infrared sensors to identify materials
In the intricate process of recycling, the separation of materials is a critical step to ensure the quality and efficiency of the recycling stream. Advanced recycling plants have embraced cutting-edge technology to enhance their sorting capabilities, particularly when it comes to distinguishing between plastic and paper. One of the key innovations in this field is the utilization of optical scanners and infrared sensors, which have revolutionized the way these materials are identified and sorted.
Optical scanners are powerful tools in the recycling plant's arsenal. These devices employ advanced imaging technology to analyze the visual characteristics of materials. When a piece of paper or plastic enters the scanner, it captures high-resolution images, examining the color, texture, and patterns unique to each material. For instance, paper often has a distinct white color and a certain level of transparency, while plastic can vary in color and may have a more opaque appearance. By comparing these visual cues against a vast database of known materials, the scanner can accurately determine the type of material being processed. This method is highly effective for identifying different types of paper, such as newspapers, magazines, and cardboard, which may have similar physical properties but differ in their composition.
Infrared sensors take the sorting process a step further by targeting the material's thermal properties. These sensors emit infrared light, which interacts with the objects in the recycling stream. Each material has a unique absorption and emission pattern when exposed to infrared radiation. For example, paper and plastic have different thermal signatures, allowing the sensors to differentiate between the two. Plastic often absorbs and emits infrared energy differently compared to paper, providing a clear indication of the material's type. This technology is particularly useful in identifying mixed materials, where the visual appearance might be similar, but the thermal properties can reveal the underlying composition.
The combination of optical and infrared scanning technologies offers a comprehensive approach to material identification. By analyzing both visual and thermal characteristics, these advanced machines can achieve high accuracy in sorting plastic and paper. This precision is crucial in recycling plants, as it ensures that the materials are directed to the appropriate processing streams, optimizing the recycling process and minimizing contamination. Moreover, the use of such advanced sorting technology contributes to the overall sustainability of recycling operations, enabling plants to handle larger volumes of waste more efficiently while maintaining the integrity of the recycled materials.
In summary, recycling plants employ sophisticated methods to separate plastic and paper, with optical scanners and infrared sensors playing pivotal roles. These technologies enable the identification of materials based on their visual and thermal properties, ensuring a more efficient and accurate sorting process. As recycling practices continue to evolve, the integration of such advanced machinery will be essential in achieving higher recycling rates and promoting a more sustainable approach to waste management.
Buncombe County Recycling: Rinsed Plastics Accepted?
You may want to see also
Conveyor Belts: These transport materials through various processes, separating plastic and paper
Conveyor belts play a crucial role in recycling plants, facilitating the efficient separation of plastic and paper materials. These belts are an integral part of the recycling process, providing a continuous and controlled transport system for various materials. The primary function of conveyor belts in this context is to move and guide the incoming waste, ensuring a smooth and organized flow through the recycling machinery.
In the initial stages of recycling, conveyor belts receive the sorted waste, which is typically a mix of plastic and paper. The belts are designed with specific features to handle these materials effectively. For plastic, conveyor belts often use a smooth, lightweight surface to prevent entanglement and ensure that the plastic items glide smoothly along the belt. This is particularly important for items like plastic bottles and containers, which can be lightweight and easily caught by other machinery. The belts may also be equipped with sensors to detect and separate different types of plastics based on their unique properties.
For paper, conveyor belts require a more robust and textured surface to ensure proper grip and separation. The belt's surface is often made of durable materials like rubber or a specialized polymer, which provides the necessary friction to hold the paper in place. This is crucial to prevent paper from being carried away by the wind or being damaged by the impact of other materials. Additionally, some conveyor belts are designed with a slightly inclined surface to aid in the separation process, allowing paper to slide off the belt and into specialized collection bins.
The separation process continues as the materials move along the conveyor belt. Advanced recycling plants employ various techniques to further refine the separation. For instance, magnetic separators can be integrated into the belt system to attract and remove any ferrous metals that might be present in the paper or plastic waste. Similarly, air blowers can be used to gently lift and separate lightweight paper items from the plastic, ensuring a more precise and efficient sorting process.
Conveyor belts are also crucial for quality control. After separation, the materials are often inspected to ensure they meet the required standards. Conveyor belts can be equipped with cameras and sensors to detect any contaminants or incorrectly sorted items, allowing for immediate adjustments and improvements in the recycling process. This level of precision ensures that the final products are of high quality and meet the necessary recycling standards.
Black Plastic DVD Cases: Can They Be Recycled?
You may want to see also
Magnetic Separation: Metal detectors and magnets remove ferrous materials, leaving plastic and paper
Magnetic separation is a crucial process in recycling plants, especially when it comes to separating ferrous materials from non-ferrous ones. This method is highly effective in the recycling industry as it allows for the efficient removal of metal contaminants from various waste streams, ensuring that the final products are clean and of high quality. Here's how it works:
Metal detectors and powerful magnets are employed in recycling facilities to identify and extract ferrous materials. Ferrous metals, such as iron and steel, are attracted to magnets and can be easily separated from other waste components. The process begins with a series of conveyer belts or sorting lines where the incoming waste is fed. As the waste moves along, metal detectors scan the material, identifying any ferrous objects or contaminants. These detectors can sense the unique magnetic properties of metals, allowing for precise detection. Once detected, the ferrous materials are then directed towards a separate collection area or conveyor belt.
The use of magnets further enhances the separation process. Strong magnets are strategically placed along the sorting line, attracting and capturing ferrous particles. These magnets can be permanent or electromagnetic, with the latter offering more flexibility in terms of adjustment and control. Electromagnetic magnets can be turned on and off, allowing operators to selectively remove metal items while processing large volumes of waste. The ferrous materials, now separated, are collected and bunched together, forming recyclable metal bales or bundles.
After the magnetic separation, the remaining waste stream consists primarily of plastic and paper. This non-ferrous fraction is then directed to further processing steps. Plastic and paper are not attracted to magnets, so they continue on their path through the recycling plant. This separation is vital as it ensures that the final recycled products, such as paper and plastic pellets, are free from any metal impurities, maintaining their quality and market value.
The magnetic separation process is an efficient and reliable method used in recycling plants to enhance the purity of recycled materials. By employing metal detectors and magnets, recycling facilities can effectively remove ferrous contaminants, leaving behind clean plastic and paper streams, which are then ready for further processing and recycling into new products. This technique plays a significant role in the overall sustainability and efficiency of the recycling industry.
Santa Rosa's Plastic Bag Recycling: Unraveling the Mystery
You may want to see also
Water Flotation: Paper floats on water, while plastic sinks, aiding in separation
Water flotation is a widely used technique in recycling plants to separate paper and plastic materials efficiently. This method takes advantage of the inherent properties of these materials, specifically their buoyancy and density. When paper and plastic are exposed to water, their behavior differs significantly, allowing for easy separation.
Paper, being a lightweight and porous material, has a relatively low density. When placed in water, it floats due to its air-filled structure, which is a result of the manufacturing process and the natural properties of the fibers. The air pockets within the paper create a buoyant force, causing it to rise to the surface. This characteristic makes paper an ideal candidate for water flotation separation.
On the other hand, plastic, particularly common types like PET (polyethylene terephthalate) and HDPE (high-density polyethylene), has a higher density compared to paper. When submerged in water, plastic sinks because it is denser than the water. This density difference is crucial for the separation process. The plastic materials, which often have a smoother and more compact structure, displace less water compared to paper, resulting in a stronger downward force.
The water flotation process involves feeding the mixed paper and plastic waste into a large tank or flotation cell. The tank is filled with water, and the materials are agitated, allowing the paper to float to the top while the plastic sinks to the bottom. This separation is based on the principle that the denser materials will sink, and the less dense materials will float. The floating paper can then be easily collected and directed to one side of the plant, while the sinking plastic is collected separately.
This method is highly effective and environmentally friendly, as it enables the recycling of both paper and plastic, reducing waste and promoting sustainable practices. By utilizing the natural properties of these materials, recycling plants can efficiently separate and process different types of waste, contributing to a more sustainable and circular economy.
Plastic Straws in Florida: Can They Be Recycled?
You may want to see also
Human Inspection: Workers verify and adjust the process, ensuring accurate material separation
In the intricate process of recycling, human inspection plays a critical role, especially in the separation of plastic and paper, which are commonly recycled materials. This step is essential to ensure the quality and efficiency of the recycling process, as it involves meticulous verification and adjustment by trained workers.
Upon arrival at the recycling plant, the raw materials, including plastic and paper, undergo a series of processes to be sorted. Human inspectors are strategically positioned at various stages of this journey. Their primary task is to visually inspect the materials, identifying any contaminants or items that do not belong in the respective streams. For instance, a worker might notice a piece of plastic with a paper label still attached, indicating that the material needs to be sorted further. This level of detail is crucial, as it prevents the incorrect mixing of materials, which could lead to contamination and reduced recycling quality.
The inspection process is not limited to visual assessment alone. Workers are trained to use specialized tools to further analyze the materials. For paper, this might involve checking the thickness and integrity of the sheets, ensuring they are not damaged or mixed with non-paper items. Similarly, for plastic, inspectors may examine the type and quality, separating different grades of plastic to ensure they are recycled appropriately. This hands-on approach allows for a more nuanced understanding of the materials, enabling workers to make informed decisions.
One of the key responsibilities of human inspection is to fine-tune the separation process. Based on their observations, inspectors can adjust the machinery and equipment to optimize material separation. For example, if a particular type of plastic is consistently being misidentified, workers can recalibrate the sensors or adjust the conveyor belts to improve accuracy. This real-time adjustment is vital for maintaining high standards and ensuring that the recycling plant operates efficiently.
Moreover, human inspection provides an opportunity for quality control. Workers can manually remove any items that were not correctly separated during the automated process. This might include small pieces of plastic that were missed or paper fragments that could compromise the integrity of the final product. By doing so, the inspection team ensures that only the highest quality materials are used in the recycling stream, contributing to a more sustainable and environmentally friendly process.
In summary, human inspection is an indispensable component of recycling plants, particularly in the separation of plastic and paper. Through their keen eye for detail and specialized knowledge, workers verify and refine the separation process, ensuring that the end products are of the highest caliber. This human-led approach adds a layer of precision and control, making the recycling process more effective and environmentally beneficial.
Unveiling Utah's Plastic Recycling Tax: A Case Study on St. George
You may want to see also
Frequently asked questions
Recycling facilities employ various methods to distinguish between plastic and paper. One common technique is using optical sorters, which utilize light to identify different materials based on their reflectivity. Plastic often has a higher reflectivity, allowing it to be separated from paper. Additionally, magnetic separators are used to attract and remove ferrous metals, ensuring that only non-metal materials remain for further processing.
One significant challenge is the physical similarity between certain types of plastic and paper. For instance, both can be thin and flexible, making it difficult for machines to differentiate them. To address this, advanced optical sorting systems with enhanced resolution and color recognition capabilities are employed. Another challenge is the presence of contaminants, such as labels or non-paper materials attached to paper, which require additional sorting steps to ensure clean and recyclable materials.
Yes, several cutting-edge technologies are revolutionizing plastic and paper separation. One such innovation is the use of near-infrared (NIR) spectroscopy, which analyzes the molecular structure of materials to identify different types of plastics and paper. This technology can detect even minor variations, ensuring a more accurate separation. Additionally, machine learning algorithms are being integrated into sorting systems to improve their efficiency and accuracy over time, allowing for better identification and separation of various materials.