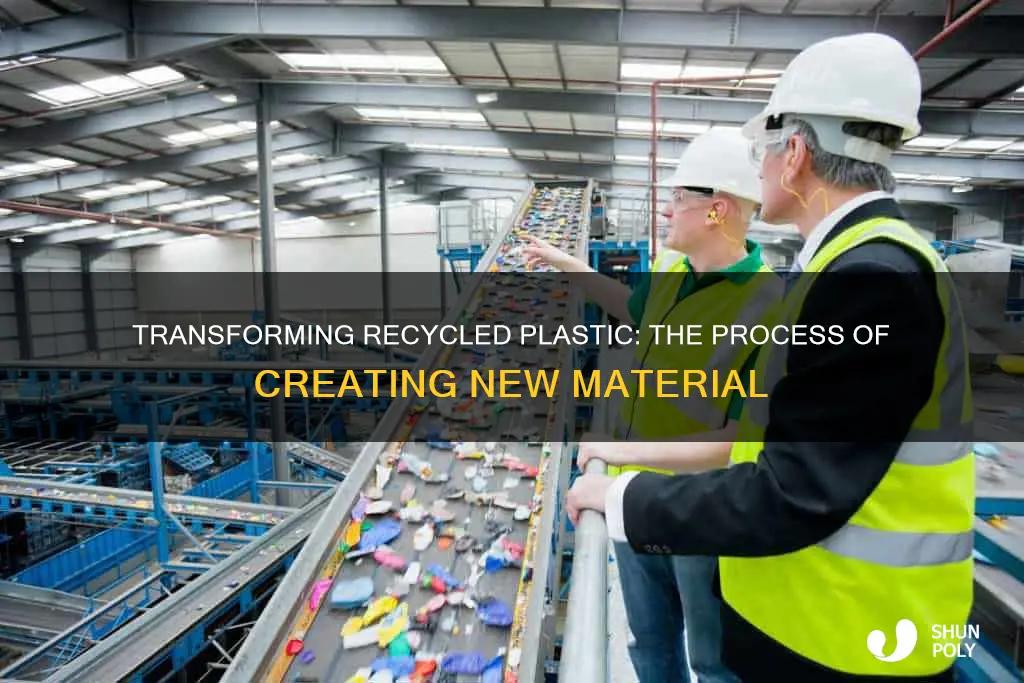
The process of recycling plastic involves transforming used or discarded plastic items into new materials, which can be a crucial step in reducing waste and promoting sustainability. This process begins with the collection and sorting of various types of plastic waste, ensuring that they are clean and free from contaminants. Once sorted, the plastic is then shredded or ground into small pieces, known as flakes or pellets. These flakes are further processed through a series of steps, including washing, drying, and melting, to create a raw material that can be used in manufacturing. The most common method is through a process called recycling, where the plastic flakes are heated and extruded into new shapes, which can then be molded into various products, such as furniture, construction materials, and even new packaging. This recycling process not only reduces the demand for virgin plastic production but also helps conserve energy and minimize the environmental impact of plastic waste.
What You'll Learn
- Collection and Sorting: Separate recycled plastics by type and color for efficient processing
- Cleaning and Shredding: Remove contaminants and break down plastic into small pieces
- Melting and Molding: Heat and shape shredded plastic into new products
- Additives and Reinforcement: Enhance properties with fillers, colors, and polymers for strength
- Molding and Forming: Shape molten plastic into desired products using molds and presses
Collection and Sorting: Separate recycled plastics by type and color for efficient processing
The process of creating new plastic from recycled materials begins with a crucial step: efficient collection and sorting of the used plastic items. This initial phase is vital as it sets the foundation for the entire recycling process and ensures the quality of the final product. When collecting recycled plastics, it is essential to focus on source separation, where different types of plastic are kept separate from each other. This is because not all plastics are created equal and have distinct properties that determine their suitability for specific applications. For instance, PET (polyethylene terephthalate) bottles are commonly used for beverages and can be identified by their unique resin identification code, which is typically a number 1 inside a triangle. On the other hand, HDPE (high-density polyethylene) containers, often used for milk and shampoo bottles, are identified by the number 2.
Once collected, the plastic waste undergoes a sorting process to separate it into different categories. This is a critical step to ensure that the recycling process is efficient and effective. Sorting can be done manually or through automated systems, depending on the scale of the operation. Manual sorting involves trained personnel who visually inspect and separate the plastics based on their type and color. This method is often used in small-scale recycling operations or when dealing with a diverse range of plastic items. For instance, a worker might separate PET bottles from HDPE containers, ensuring that each type of plastic is kept in its own designated pile.
Automated sorting systems, on the other hand, utilize advanced technologies to streamline the process. These systems employ various techniques such as near-infrared (NIR) spectroscopy, which can identify different types of plastics based on their molecular structure. NIR spectroscopy can differentiate between PET, HDPE, and other common plastics, allowing for precise sorting. Additionally, optical sorting methods use cameras and sensors to detect differences in color and shape, further enhancing the accuracy of the sorting process. These automated systems are highly efficient and can process large volumes of plastic waste in a short time, making them ideal for large-scale recycling operations.
Color separation is another crucial aspect of the sorting process. Different colors of plastic often have distinct properties and applications. For example, clear PET bottles are commonly used for food packaging, while colored HDPE containers are often used for personal care products. By separating plastics by color, recyclers can ensure that the materials are directed to the appropriate processing streams, maximizing their value and potential for reuse. This attention to detail in sorting not only improves the efficiency of the recycling process but also contributes to the overall quality of the recycled plastic products.
In summary, the collection and sorting of recycled plastics are fundamental steps in the journey from waste to new products. Proper separation by type and color ensures that the recycling process is optimized, and the resulting recycled plastics can be utilized effectively in various industries. This initial phase sets the stage for the subsequent steps in recycling, where the sorted plastics are processed, cleaned, and transformed into new materials, ultimately contributing to a more sustainable and circular economy.
Can Plastic Drop Cloths Be Recycled? Unraveling the Mystery
You may want to see also
Cleaning and Shredding: Remove contaminants and break down plastic into small pieces
The process of recycling plastic begins with cleaning and shredding, which are crucial steps to ensure the quality of the recycled material. This initial phase aims to remove any contaminants and break down the plastic into smaller, manageable pieces, setting the foundation for the subsequent recycling stages.
Cleaning is a meticulous process that involves sorting and separating different types of plastics, as not all plastics are recyclable in the same way. This step is often done manually or with the help of specialized machinery. For instance, single-use plastics like water bottles and food containers are typically sorted based on their resin identification codes (e.g., PET, HDPE, LDPE). This classification is essential because different types of plastics have varying chemical compositions and melting points, which affect their recyclability and the final product's quality.
During the cleaning process, any non-plastic materials, such as labels, caps, or contaminants like dirt and food residue, are removed. This is crucial because these impurities can compromise the integrity of the recycled plastic. For example, food residue can lead to unpleasant odors and affect the material's strength, while labels and caps might contain different types of plastics that need to be separated. Advanced recycling facilities use optical sorters and eddy current separators to efficiently identify and separate these contaminants.
Once the plastics are sorted and cleaned, the next step is shredding. Shredding machines are designed to break down the plastic into small, uniform pieces, typically ranging from 2 to 4 inches in size. This process is essential because it reduces the volume of the plastic, making it easier to handle and transport. Smaller pieces also increase the surface area, allowing for better mixing and processing in the subsequent stages of recycling. The shredded plastic is then stored or further processed, depending on the specific recycling method being employed.
The cleaning and shredding process is a critical phase in plastic recycling, as it sets the foundation for the entire recycling journey. By removing contaminants and breaking down the plastic, this step ensures that the recycled material is of high quality and can be used to create new products, contributing to a more sustainable and circular economy.
Eco-Friendly Choice: Compostable or Recyclable? The Ultimate Cup Comparison
You may want to see also
Melting and Molding: Heat and shape shredded plastic into new products
The process of transforming recycled plastic into new products involves a fascinating technique known as melting and molding. This method is a crucial step in recycling and repurposing plastic waste, allowing it to be given new life and functionality. Here's an overview of the process:
Shredding is the initial step, where the collected plastic waste is carefully sorted and cleaned to remove any contaminants. Once sorted, the plastic is shredded into small, uniform pieces. This shredded plastic is then fed into a specialized machine called a granulator, which further reduces the size of the plastic flakes, ensuring a consistent and controlled particle size. The goal is to create a fine, powdery substance that can be easily processed.
Melting is the next critical phase. The shredded plastic is heated to a specific temperature, typically around 250-300 degrees Celsius, depending on the type of plastic. This temperature is carefully controlled to ensure the plastic melts without burning or degrading. The melted plastic is then poured into a mold, which gives it the desired shape. The mold is a crucial component as it determines the final form of the product. It can be a simple flat sheet or a complex, intricate design, depending on the intended use.
During the molding process, the melted plastic is carefully poured into the mold and then heated again to facilitate the shaping process. The heat and pressure applied to the plastic cause it to take the shape of the mold. This step requires precision and skill to ensure the final product meets the required specifications. Once the plastic has cooled and hardened within the mold, it is carefully removed, revealing the newly formed product.
This method of melting and molding allows for the creation of a wide range of products, from simple household items like containers and bottles to more complex structures like furniture, automotive parts, and even construction materials. The process is energy-intensive and requires specialized equipment, but it is an efficient way to recycle plastic and reduce waste. By utilizing this technique, we can minimize the environmental impact of plastic waste and move towards a more sustainable future.
Unraveling the Mystery: Can Plastic Tarps Be Recycled?
You may want to see also
Additives and Reinforcement: Enhance properties with fillers, colors, and polymers for strength
The process of recycling plastic and transforming it into a usable material involves several steps, and one crucial aspect is the use of additives and reinforcements to enhance the properties of the recycled plastic. This technique is essential to improve the mechanical, thermal, and aesthetic qualities of the final product, making it suitable for various applications.
Additives play a vital role in modifying the behavior of recycled plastic. One common additive is a plasticizer, which is added to increase flexibility and reduce brittleness. This is particularly important for materials like PET (polyethylene terephthalate), which can become stiff and brittle during the recycling process. By incorporating plasticizers, the material becomes more pliable, making it easier to process and form into new products. Additionally, stabilizers are used to prevent degradation caused by heat, light, or oxygen, ensuring the longevity of the recycled plastic.
Fillers are another type of additive used to reinforce recycled plastic. These materials, such as calcium carbonate, talc, or clay, are incorporated into the plastic matrix to enhance its strength and stiffness. Fillers provide structural support, improve impact resistance, and can even reduce the overall cost of the material. For example, adding calcium carbonate to a recycled PET bottle can significantly increase its rigidity, making it suitable for applications requiring a sturdy structure.
Colorants are essential for achieving the desired aesthetic appeal in recycled plastic products. Dyes and pigments are added during the recycling process to impart specific colors to the material. This is crucial for applications where appearance is critical, such as in consumer goods or packaging. The choice of colorant must consider its compatibility with the plastic and the overall processing conditions to ensure optimal color retention and stability.
Furthermore, the use of polymers can significantly impact the performance of recycled plastic. By blending different types of polymers, engineers can tailor the material's properties to specific requirements. For instance, combining a rigid polymer with a flexible one can result in a material with improved impact resistance and dimensional stability. This technique is often employed in the production of automotive parts or electronic enclosures, where strength and durability are essential.
In summary, additives, fillers, colors, and polymers are powerful tools in the process of recycling and reprocessing plastic. These materials and techniques allow for the customization of recycled plastic's properties, making it versatile and suitable for a wide range of applications. Through careful selection and combination of these elements, manufacturers can create high-performance products while also promoting sustainability by utilizing recycled resources.
Unraveling the Mystery: Can Plastic Detergent Containers Be Recycled?
You may want to see also
Molding and Forming: Shape molten plastic into desired products using molds and presses
The process of molding and forming is a crucial step in transforming recycled plastic into new products. This method involves shaping molten plastic into the desired form using molds and presses, allowing for the creation of a wide range of items. Here's an overview of this fascinating process:
In the molding and forming process, the first step is to gather and sort the recycled plastic materials. These plastics are then cleaned and shredded to ensure a consistent feedstock. The shredded plastic is heated and melted in an extruder, a machine that applies heat and pressure to create a homogeneous molten mass. This molten plastic is then ready for the molding stage.
Molds, also known as dies, are designed with specific shapes and dimensions to create the intended product. These molds can be made from various materials, such as steel or aluminum, and are carefully crafted to ensure precision. When the molten plastic is ready, it is carefully poured into the mold, filling it to the desired level. The mold is then closed, creating a cavity that mirrors the desired product's shape.
After the mold is filled, it is placed in a press, which applies pressure to the molten plastic. This pressure helps to expel any air bubbles and ensures that the plastic takes the shape of the mold. The press also helps to solidify the plastic, making it rigid and ready for removal. Once the plastic has cooled and hardened, the mold is opened, and the newly formed product is extracted.
This process can be repeated multiple times, allowing for the mass production of various plastic items. The versatility of molding and forming enables the creation of complex shapes and structures, making it an essential technique in the recycling and manufacturing of plastic products. It is a sustainable approach to recycling, as it reduces waste and provides an eco-friendly alternative to traditional manufacturing methods.
Unraveling the Plastic Recycling Mystery: A Guide to Sorting Your Waste
You may want to see also
Frequently asked questions
Recycling plastic involves a series of steps to transform used plastic items into raw materials for new products. The process typically begins with collecting and sorting different types of plastic waste. This waste is then cleaned and shredded into small pieces called flakes. These flakes are further processed through washing and drying to remove any contaminants. The cleaned plastic flakes are then melted and extruded into pellets, which serve as the base material for manufacturing new plastic products.
Quality control is an essential aspect of recycling plastic. After the initial sorting and cleaning, the plastic flakes undergo a process called 'reprocessing' or 'regeneration'. This step involves heating the flakes to a specific temperature, which allows the plastic to be remolded without losing its structural integrity. Reprocessing ensures that the recycled plastic meets the required standards and can be used for various applications. Additionally, advanced recycling techniques, such as chemical recycling, can break down plastic into its original building blocks, creating a more consistent and high-quality feedstock for new plastic production.
While recycling plastic is an important practice, it does come with certain challenges. One major issue is the presence of contaminants, such as food residue or non-plastic materials, which can affect the quality of the recycled product. These contaminants need to be removed during the sorting and cleaning process. Another challenge is the potential for downcycling, where the recycled plastic may not meet the same quality standards as the original material, leading to a decrease in the number of times it can be recycled. Additionally, the availability and accessibility of recycling facilities and infrastructure play a crucial role in the success of plastic recycling programs.