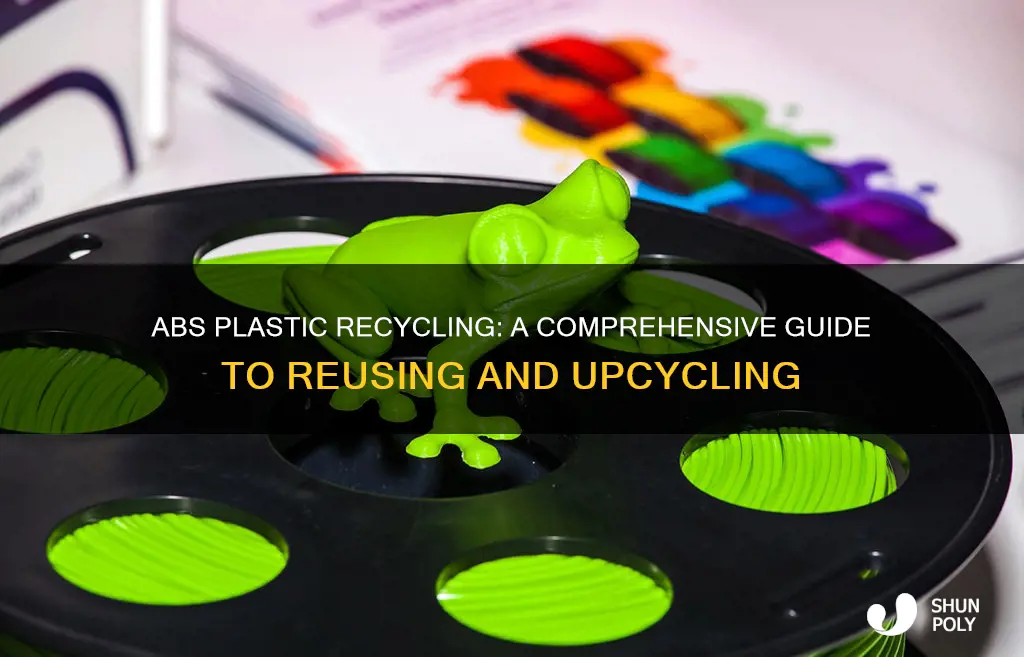
ABS plastic, commonly used in electronics, automotive, and consumer goods, can be recycled through various methods. Recycling ABS involves breaking down the material into its base components, which can then be repurposed for new products. One common process is shredding the plastic into small pieces, which are then washed to remove contaminants. These cleaned pieces are melted and remolded into new products, such as garden benches, park benches, and even new electronic components. Proper recycling of ABS plastic is crucial for reducing waste and conserving resources, ensuring a more sustainable approach to manufacturing and product disposal.
What You'll Learn
- Collection: ABS plastic is collected from various sources, including recycling bins and waste streams
- Sorting: Materials are sorted by color and type to ensure proper processing
- Shredding: Plastic is shredded into small pieces to facilitate further processing
- Melting: Shredded ABS is melted down to form a molten plastic mass
- Molding: Molten plastic is shaped into new products using molds
Collection: ABS plastic is collected from various sources, including recycling bins and waste streams
The process of recycling ABS (acrylonitrile butadiene styrene) plastic begins with efficient collection methods. ABS is commonly found in various products, such as electronics, automotive parts, and consumer goods, making it a prevalent material in waste streams. To initiate the recycling process, ABS plastic must be gathered from different sources.
One primary source of ABS collection is recycling bins specifically designated for plastic waste. These bins are often color-coded or labeled to indicate the type of plastic they accept. Households, offices, and public spaces should have these bins readily available to encourage proper waste segregation. When individuals dispose of their ABS-containing items, they place them into these designated bins, ensuring that the plastic is separated from other waste materials. This initial step is crucial as it prevents contamination and makes the subsequent recycling process more efficient.
In addition to recycling bins, waste streams from various industries and commercial activities are valuable sources of ABS plastic. These waste streams can include discarded products, manufacturing scraps, and end-of-life items from factories and businesses. Specialized collection services or partnerships with local businesses can facilitate the gathering of ABS plastic from these sources. By engaging with industries that produce ABS-based products, recycling centers can secure a steady supply of raw materials for the recycling process.
Another strategy for ABS collection is the implementation of take-back programs. Manufacturers and retailers can encourage consumers to return used or discarded ABS products by offering convenient drop-off points or mail-in services. This approach ensures that ABS plastic is collected in a controlled manner, allowing for better quality control and preparation for recycling. Take-back programs can be particularly effective for electronic devices and automotive parts, where ABS is commonly used.
Once collected, the ABS plastic undergoes a series of processes to be recycled. These processes may include sorting, cleaning, and reprocessing to create new products. The collected ABS is typically sorted by color and grade to ensure compatibility with the desired end-use applications. Proper sorting prevents color degradation and maintains the integrity of the recycled material. After sorting, the ABS may be cleaned to remove any contaminants or impurities, ensuring a higher quality recycled product.
The Evolution of Plastic Recycling: Past, Present, and Future
You may want to see also
Sorting: Materials are sorted by color and type to ensure proper processing
The process of recycling ABS (acrylonitrile butadiene styrene) plastic begins with meticulous sorting, a crucial step to ensure effective recycling. This initial phase involves categorizing materials based on color and type, which is essential for the subsequent recycling procedures. The sorting process aims to separate ABS plastic from other types of plastics and different colors, as this distinction is vital for maintaining the quality of the recycled material.
When sorting ABS plastic, the primary focus is on identifying and grouping the material by type. ABS is often used in various applications, including electronics, automotive parts, and consumer goods. By sorting it by type, recyclers can ensure that the plastic is processed appropriately, considering its specific properties and potential contaminants. For instance, ABS used in electronic devices might contain traces of metals or other additives, requiring specialized handling to prevent contamination during recycling.
Color sorting is another critical aspect of this process. ABS plastic can vary in color, ranging from white to various shades of grey, depending on the additives and manufacturing processes. Sorting by color is essential because different colors may have distinct chemical compositions, which can affect the recycling methods. For example, a bright yellow ABS plastic might require a different recycling technique compared to a dark grey variant, ensuring that the end product meets the required standards.
During the sorting process, advanced techniques and equipment are employed to enhance efficiency and accuracy. Optical sorters, for instance, use light sensors to identify and separate materials based on color. These machines can quickly process large volumes of plastic, ensuring that ABS is isolated from other plastics and contaminants. Additionally, manual sorting by trained personnel is often utilized for more intricate tasks, such as identifying and removing non-plastic items or identifying specific types of ABS.
Proper sorting by color and type is fundamental to the success of ABS recycling. It enables recyclers to employ the most suitable recycling methods, ensuring that the final product is of high quality and meets the necessary standards. This initial step sets the foundation for the entire recycling process, contributing to the sustainability and efficiency of ABS plastic recycling efforts.
Unraveling the Mystery: Can ABS Plastic Be Recycled?
You may want to see also
Shredding: Plastic is shredded into small pieces to facilitate further processing
Shredding is a crucial step in the recycling process for ABS (acrylonitrile butadiene styrene) plastic, a common thermoplastic known for its durability and impact resistance. When ABS plastic is shredded, it undergoes a transformation that prepares it for subsequent recycling stages. This process involves reducing the size of the plastic material, making it easier to handle and process further.
The shredding process typically begins with the collection of ABS plastic waste, which can include various items such as electronic enclosures, automotive parts, or even consumer goods. These items are then sorted to ensure that only ABS plastic is processed, as it requires specific recycling methods. Once sorted, the plastic waste is fed into a shredding machine, which is designed to break down the material into smaller, uniform pieces. The shredder's rotating blades cut and tear the plastic, creating a consistent and manageable size reduction.
The shredded ABS plastic is then sorted again to separate it into different sizes and types. This classification is essential because it allows for the creation of a raw material that can be used in various recycling processes. Smaller pieces, often referred to as 'flakes' or 'pellets,' are more suitable for reprocessing into new products. These flakes can be further cleaned, dried, and treated to remove any contaminants, ensuring a high-quality recycled material.
This initial shredding step is a critical phase in the recycling journey of ABS plastic. It enables the material to be more easily processed, cleaned, and transformed into new products, reducing waste and promoting sustainability. By breaking down the plastic into smaller pieces, the recycling process becomes more efficient, and the potential for creating new, valuable products from recycled ABS increases.
In summary, shredding ABS plastic is a vital process that prepares the material for further recycling and reprocessing. It ensures that the plastic is reduced to a manageable size, facilitating the creation of high-quality recycled products and contributing to a more sustainable approach to waste management.
Denver's Plastic Recycling Journey: Unveiling the 7-Step Process
You may want to see also
Melting: Shredded ABS is melted down to form a molten plastic mass
The process of recycling ABS (acrylonitrile butadiene styrene) plastic begins with the collection and sorting of ABS waste. This waste can come from various sources, such as electronic devices, automotive parts, or construction materials. Once sorted, the ABS waste is prepared for the recycling process.
One of the key steps in recycling ABS is melting. Shredded ABS, which has been processed into small pieces or flakes, is fed into a specialized melting machine. This machine is designed to handle the specific properties of ABS plastic. The shredded ABS is heated to its melting point, typically around 220-240°C (428-464°F), in a controlled environment. As the temperature rises, the ABS undergoes a phase change, transitioning from a solid state to a molten plastic mass.
During the melting process, the shredded ABS is agitated and mixed to ensure a homogeneous mixture. This is crucial to maintain the integrity of the recycled material. The molten ABS is then purified to remove any impurities or contaminants that may have accumulated during the initial collection and sorting stages. This purification step ensures that the final recycled product meets the required quality standards.
The molten plastic mass has a unique viscosity and consistency, which allows it to be shaped and molded into new products. It can be poured into molds or extruded into various forms, depending on the desired application. This versatility is one of the advantages of recycling ABS, as it can be transformed into new products with similar properties to the original material.
After the molten ABS is cooled and solidified, it can be further processed or used directly in manufacturing. The recycled ABS can be blended with other materials to enhance its properties or used as a raw material for creating new ABS products. This process not only reduces waste but also contributes to a more sustainable approach to plastic recycling, ensuring that valuable resources are conserved and reused.
Swartz Creek's Plastic Recycling: Unveiling the Truth
You may want to see also
Molding: Molten plastic is shaped into new products using molds
The process of recycling ABS (acrylonitrile butadiene styrene) plastic involves transforming it into new products through a technique known as molding. This method is a common and effective way to recycle various types of plastic materials. Here's an overview of how molding works in the context of ABS recycling:
When ABS plastic is ready for recycling, it begins as a waste stream of used or discarded products made from this material. The recycling process starts with sorting and collecting these ABS items, ensuring they are clean and free from contaminants. Once sorted, the ABS waste is shredded or granulated to break it down into smaller pieces, making it easier to handle and process. This initial step is crucial to ensure the quality of the recycled material.
The next stage involves melting the shredded ABS plastic. This is typically done using specialized equipment like a plasticizer or an extruder. The plastic is heated to its melting point, which is around 175-190 degrees Celsius for ABS. During this process, the molten plastic becomes a viscous liquid, ready to be shaped into new forms. The temperature and duration of heating are carefully controlled to maintain the integrity of the material.
Molding is the art and science of shaping this molten ABS plastic. It utilizes molds, which are specially designed cavities or forms, to create the desired shape of the new product. The process begins by placing the molten plastic into the mold, filling it to the required level. The mold is then closed, and the plastic is allowed to cool and solidify. This cooling process is critical, as it determines the final dimensions and quality of the recycled product.
After the plastic has cooled, the mold is opened, and the new product is released. This product can be anything from automotive parts, electronic enclosures, to consumer goods. The molding process allows for a wide range of applications, making it a versatile recycling method. The recycled ABS products often meet or exceed the performance of their virgin counterparts, proving that recycling can produce high-quality materials.
In summary, molding is a key step in recycling ABS plastic, enabling the transformation of waste into valuable new products. This process showcases the potential of recycling technologies to create sustainable solutions while maintaining the quality and functionality of materials. It is an essential practice in the circular economy, reducing waste and promoting the reuse of valuable resources.
Randall's Recycling: Unveiling the Plastic Waste Mystery
You may want to see also
Frequently asked questions
ABS (Acrylonitrile Butadiene Styrene) is a common thermoplastic polymer used in various applications, including electronics, automotive parts, and consumer goods. Recycling ABS involves processing the plastic to break it down into smaller particles or pellets, which can then be remolded into new products.
Before recycling, ensure the ABS items are clean and free from contaminants. Remove any non-plastic components, such as metal fasteners or electronic parts. Break down large items into smaller pieces to increase the surface area, making it easier for recycling facilities to process them.
ABS can be recycled through various methods, including granulation and compounding. Granulation involves shredding the plastic into small flakes, which are then washed, dried, and ground into fine particles. Compounding uses a process called "compounding" to melt and blend the ABS with other materials, creating a new material suitable for manufacturing.
Recycling options for ABS may vary depending on your location. Contact your local waste management authority or recycling centers to inquire about ABS plastic recycling programs in your area. Some specialized recycling facilities accept ABS, especially for industrial or commercial quantities.
Recycling ABS plastic offers several advantages. It reduces waste in landfills, conserves natural resources, and minimizes the need for raw material extraction. Recycling also helps to recover valuable materials, reducing energy consumption and greenhouse gas emissions associated with manufacturing new plastics.