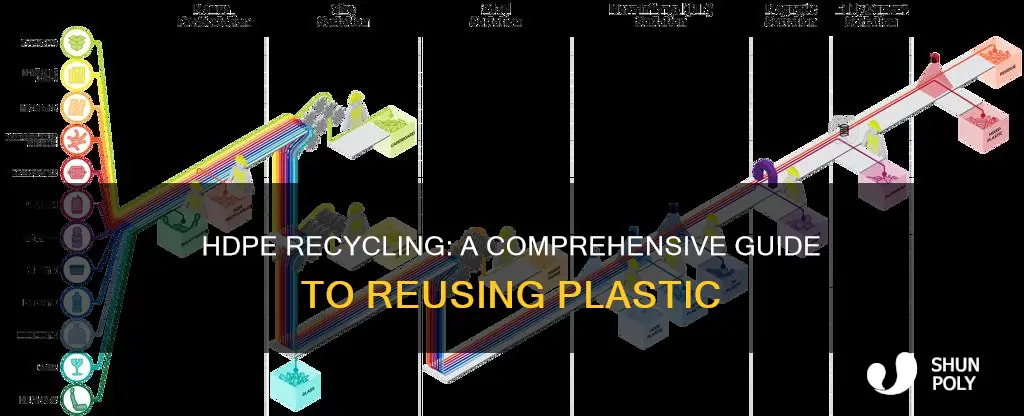
HDPE (High-Density Polyethylene) plastic is widely used in various products, from milk jugs to shampoo bottles. Recycling HDPE is crucial for environmental sustainability, as it helps reduce waste and conserve resources. This paragraph will explore the process of recycling HDPE plastic, including collection, sorting, and processing methods, as well as the benefits of this recycling practice.
Characteristics | Values |
---|---|
HDPE Plastic Type | High-density polyethylene |
Recycling Process | HDPE is typically recycled through a process called "chemical recycling" or "advanced recycling." This involves breaking down the plastic into its base chemicals, which can then be used to create new products. |
Recycling Symbols | The recycling symbol for HDPE is the number 2 inside a recycling triangle. |
Common Uses of Recycled HDPE | Recycled HDPE is commonly used to produce new containers, such as milk jugs, detergent bottles, and shampoo bottles. It can also be used in construction materials, furniture, and even clothing. |
Environmental Benefits | Recycling HDPE reduces the demand for new plastic production, which helps conserve natural resources and reduces energy consumption. It also diverts plastic waste from landfills and prevents it from polluting the environment. |
Collection and Sorting | HDPE is often collected through recycling programs and sorted by color to ensure the quality of the recycled material. |
Melting Point | HDPE has a relatively high melting point, typically around 131-139°C (270-282°F). |
Density | It has a density of approximately 0.97 g/cm³, making it one of the heaviest forms of polyethylene. |
Chemical Resistance | HDPE is resistant to many chemicals, including acids, bases, and solvents, making it suitable for various applications. |
Biodegradability | HDPE is not biodegradable, but it can be recycled multiple times without significant degradation in quality. |
What You'll Learn
- Collection: HDPE plastic is gathered from various sources, including recycling bins and waste streams
- Sorting: Materials are sorted by color and type to ensure proper processing
- Cleaning: HDPE items are cleaned to remove contaminants and ensure quality
- Shredding/Grinding: Plastic is shredded or ground into small pieces for easier processing
- Melting and Molding: The HDPE flakes are melted and molded into new products
Collection: HDPE plastic is gathered from various sources, including recycling bins and waste streams
The collection of HDPE (High-Density Polyethylene) plastic is a crucial step in the recycling process, ensuring that this versatile material can be transformed into new products. HDPE is widely used in various industries, from packaging to construction, and its proper collection is essential for a successful recycling journey.
One primary source of HDPE collection is recycling bins strategically placed in public areas, residential neighborhoods, and commercial facilities. These bins are designed to capture HDPE items that consumers might otherwise discard in regular trash. The bins are often color-coded, with HDPE typically identified by its distinctive milk-jug-like shape and the recycling symbol (a triangle with a number 2 inside) on the bottom. When residents and businesses dispose of their HDPE waste in these designated bins, it becomes a valuable resource for recycling centers.
In addition to public recycling bins, waste streams from various industries and commercial operations contribute significantly to HDPE collection. For instance, grocery stores, supermarkets, and convenience stores generate substantial amounts of HDPE from their packaging, including milk jugs, detergent bottles, and shampoo containers. These businesses often have their recycling systems in place, where HDPE waste is sorted and collected separately from other recyclables. Similarly, manufacturing plants and industrial facilities may have their own waste management systems, ensuring that HDPE is directed towards recycling rather than landfills.
Another critical aspect of HDPE collection is the involvement of waste management companies and recycling centers. These organizations play a vital role in gathering HDPE from various sources, including residential, commercial, and industrial sectors. They employ efficient collection methods, such as curb-side pickup, drop-off centers, and mobile recycling units, to ensure that HDPE waste is promptly and conveniently collected. Once collected, the HDPE is transported to recycling facilities, where it undergoes processing to be transformed into new, usable materials.
The collection process for HDPE is designed to be efficient and accessible, encouraging widespread participation in recycling efforts. By utilizing a combination of public recycling bins, industry-wide waste management systems, and specialized collection services, HDPE waste is effectively gathered and prepared for recycling. This comprehensive approach ensures that HDPE plastic, a valuable resource, is given a second life, contributing to a more sustainable and environmentally friendly future.
Milk Carton Recycling: Paper or Plastic? Unraveling the Mystery
You may want to see also
Sorting: Materials are sorted by color and type to ensure proper processing
The process of recycling HDPE (High-Density Polyethylene) plastic begins with meticulous sorting, a crucial step to ensure the efficiency and effectiveness of the recycling process. HDPE is a versatile plastic used in various products, from milk jugs and shampoo bottles to pipe and fiber production. Proper sorting is essential to separate HDPE from other plastics and contaminants, ensuring it can be recycled into new products.
Sorting HDPE materials involves a systematic approach, often done by hand or with the help of specialized machinery. The first step is to separate HDPE items based on their color. HDPE is typically clear or slightly translucent, so sorting by color is relatively straightforward. Clear HDPE items, such as water bottles, are easily identifiable and can be grouped together. Similarly, items with a slight green or brown tint, often used for milk jugs, can be sorted into their respective categories. This initial color-based sorting helps streamline the recycling process and ensures that HDPE materials are not contaminated with other colors.
Beyond color, HDPE items are also sorted by type. HDPE has a specific resin identification code (RIC) of 2, which is a key identifier. This code is usually found on the bottom of HDPE containers and helps recyclers and manufacturers identify the type of HDPE used. For example, HDPE-2 is commonly used for containers like milk jugs and detergent bottles, while HDPE-4 is used for shampoo bottles and other personal care products. Sorting by type ensures that HDPE materials are processed according to their specific properties and applications, maximizing their recycling potential.
Advanced recycling facilities employ various techniques to enhance the sorting process. One method is the use of optical sorters, which utilize light sensors to identify and separate HDPE items based on their color and transparency. These machines can quickly and accurately separate HDPE from other plastics, ensuring a higher purity of the recycled material. Additionally, some facilities use magnetic separators to remove any metal contaminants that may be present in the HDPE stream, further ensuring the quality of the recycled product.
Proper sorting is a critical aspect of HDPE recycling, as it enables the development of a closed-loop recycling system. By sorting HDPE by color and type, recyclers can create a more efficient process, reducing the risk of contamination and maximizing the potential for HDPE to be transformed into new products. This meticulous approach to sorting contributes to the overall sustainability of HDPE recycling, making it an essential step in the journey towards a circular economy.
Unraveling the Mystery: Can Plastic Cake Containers Be Recycled?
You may want to see also
Cleaning: HDPE items are cleaned to remove contaminants and ensure quality
HDPE (High-Density Polyethylene) recycling begins with a crucial step: cleaning. This process is essential to ensure the quality of the recycled material and to prepare HDPE items for the recycling stream. Cleaning HDPE items is a meticulous process that aims to remove any contaminants, ensuring that the final recycled product meets the required standards.
The cleaning process typically involves several stages. Firstly, HDPE items are sorted based on their color and type to facilitate the cleaning process. This initial sorting step is vital as it helps in identifying and removing specific contaminants that may be associated with certain colors or types of HDPE. For example, items like milk jugs and detergent bottles might have different cleaning requirements compared to water bottles.
Once sorted, the HDPE items undergo a thorough washing process. This often includes mechanical washing, where the items are agitated in large tanks filled with water and cleaning agents. The cleaning agents used are specifically designed to break down and remove any residual contaminants, such as food particles, labels, and other debris. High-pressure water jets and brushes are employed to ensure that every nook and cranny of the HDPE items is cleaned effectively.
After mechanical washing, the HDPE items may go through a process called 'de-watering'. This step involves removing excess water from the items, often using centrifugal force or air blowers. De-watering is crucial to prevent water retention in the recycled HDPE, which could lead to quality issues during the manufacturing process.
Finally, the cleaned HDPE items are inspected to ensure they meet the required cleanliness standards. This inspection may involve visual checks and, in some cases, more advanced techniques like near-infrared spectroscopy to detect any remaining contaminants. The goal is to guarantee that the HDPE material is free from any impurities that could compromise its quality and performance in the recycling process.
Unraveling the Mystery: What Plastics Can't Be Recycled
You may want to see also
Shredding/Grinding: Plastic is shredded or ground into small pieces for easier processing
The process of recycling HDPE (High-Density Polyethylene) plastic begins with shredding or grinding the material, which is a crucial step in preparing it for further recycling. This initial stage aims to reduce the size of the plastic items, making it more manageable and efficient to process. HDPE is commonly found in various household items such as milk jugs, shampoo bottles, and some containers. When these items are collected for recycling, they are often sorted and then shredded or ground to facilitate the recycling process.
Shredding HDPE plastic involves passing it through specialized machinery that cuts it into small, uniform pieces. This process ensures that the plastic is broken down into a consistent size, making it easier to handle and process in subsequent stages. The shredded HDPE can then be further processed to create new products or used as a raw material for various applications. Grinding, on the other hand, is a similar process but often results in a finer and more powdered form of HDPE. This method is particularly useful when dealing with larger HDPE items that need to be reduced to a more manageable size.
The shredding or grinding process is essential as it helps to remove any contaminants or impurities from the HDPE plastic. During this step, any non-plastic materials, such as labels or caps, are separated and removed, ensuring that the recycled HDPE is of high quality. This process also helps to create a homogeneous material, which is crucial for the production of new products. After shredding or grinding, the HDPE pieces are typically cleaned and sorted to ensure they meet the required standards for recycling.
Once the HDPE plastic is shredded or ground, it can be further processed through various methods, such as pelletizing or compounding. Pelletizing involves heating and shaping the shredded HDPE into small, uniform pellets, which can then be used as a raw material for manufacturing new products. Compounding, on the other hand, involves mixing the ground HDPE with other materials or additives to create a specific product, such as insulation or composite materials. These processes ensure that the recycled HDPE can be utilized in a wide range of applications, promoting sustainability and reducing waste.
In summary, shredding or grinding HDPE plastic is a critical step in the recycling process, enabling the material to be reduced in size, cleaned, and prepared for further processing. This initial stage sets the foundation for the subsequent steps in recycling HDPE, allowing for the creation of new products and the reduction of waste. By following these detailed processes, the recycling of HDPE plastic becomes more efficient and environmentally friendly.
Recycling Plastic: A Money-Saving, Eco-Friendly Choice
You may want to see also
Melting and Molding: The HDPE flakes are melted and molded into new products
The process of recycling HDPE (High-Density Polyethylene) plastic involves transforming used HDPE products into new, usable materials. One of the most common methods is through a process known as "Melting and Molding." This technique is particularly effective for creating new containers, bottles, and various other plastic items.
HDPE flakes, which are small pieces of HDPE plastic, are collected and sorted according to color and size. This step is crucial to ensure the quality of the final product. Once sorted, the flakes are transported to a recycling facility where the melting process begins. The flakes are fed into a large industrial furnace, where they are heated to temperatures typically ranging from 200°C to 250°C. This controlled heating process ensures that the HDPE material is softened and becomes malleable.
As the HDPE flakes melt, they are carefully mixed and agitated to ensure a homogeneous mixture. This step is vital to create a consistent and high-quality end product. The molten HDPE is then transferred to an extruder, a machine designed to shape and mold the plastic. The extruder applies heat and pressure to the material, forcing it through a die or mold. This mold is designed with the specific shape and dimensions of the desired product in mind.
During the molding process, the molten HDPE is carefully guided and shaped by the mold's contours. The material is cooled rapidly as it exits the mold, causing it to solidify and retain the desired form. This step requires precise control of temperature and cooling rates to ensure the product's integrity. Once the HDPE has cooled and hardened, the mold is opened, revealing the newly formed product.
This method of recycling HDPE is highly efficient and allows for the creation of new products with various applications. It is an environmentally friendly approach to waste management, reducing the amount of plastic waste that ends up in landfills or pollutes natural environments. By reusing HDPE through melting and molding, we can contribute to a more sustainable and circular economy.
Unraveling the Mystery: Can Plastic Pastry Containers Be Recycled?
You may want to see also
Frequently asked questions
HDPE stands for High-Density Polyethylene, a type of plastic commonly used in various products like milk jugs, detergent bottles, and shopping bags. Recycling HDPE is crucial because it reduces waste, conserves resources, and helps prevent pollution.
Look for the recycling symbol on the bottom of the item, which is usually a number inside a triangle. If the number is 2, it indicates that the item is made from HDPE. You can also check the product label or packaging for specific HDPE mentions.
Recycling HDPE is relatively straightforward. Here's a simple process:
- Rinse the HDPE item to remove any food residue or contaminants.
- Break down large containers to save space.
- Place the cleaned and dried HDPE items in your recycling bin.
- Ensure your local recycling program accepts HDPE.
Most HDPE items are recyclable, but it's essential to check with your local recycling guidelines. Some HDPE products, like straws or small containers, might have specific recycling requirements. Always verify the recycling guidelines for your area.
Recycled HDPE plastic can be transformed into various new products. It is commonly used to create new containers, such as water bottles, shampoo bottles, and storage bins. It can also be utilized in the production of outdoor furniture, carpeting, and even new plastic shopping bags.