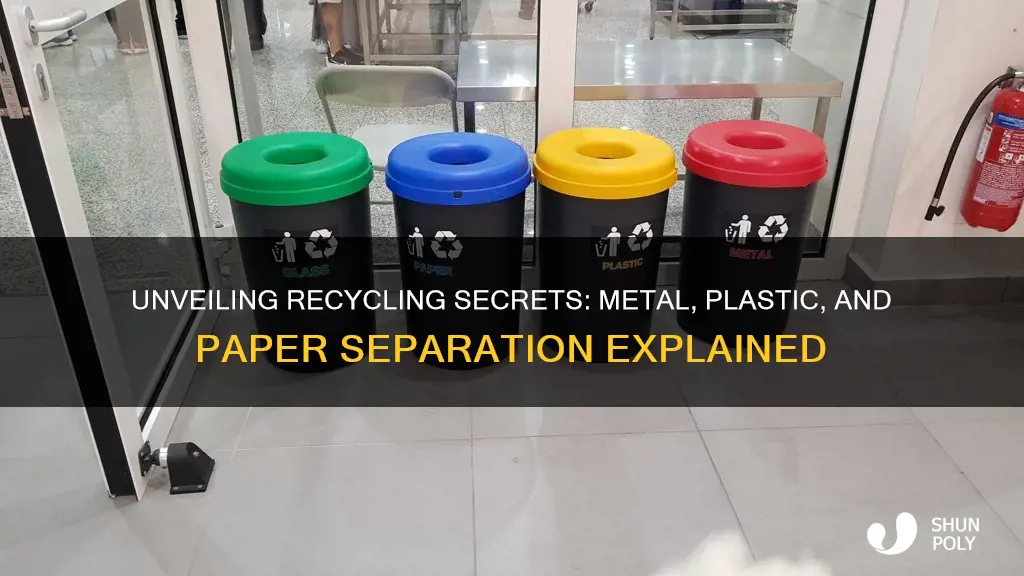
Recycling plays a crucial role in separating different materials, such as metal, plastic, and paper, to ensure effective waste management. Understanding the processes behind these separations is essential for optimizing recycling systems and promoting sustainable practices. Metal, plastic, and paper are distinct materials with unique properties, and recycling facilities employ various methods to separate them. Metal recycling often involves magnetic separation, where ferrous metals are attracted to a magnet, while non-ferrous metals are separated through manual or automated processes. Plastic recycling, on the other hand, utilizes density differences, as plastics have varying densities, allowing for their separation through water flotation or air classification. Paper recycling typically begins with mechanical pulping, which separates the paper fibers, and then employs de-inking processes to remove contaminants, ensuring the production of high-quality recycled paper. This introduction sets the stage for exploring the specific techniques and technologies used in recycling to efficiently separate these materials, contributing to a more sustainable and environmentally friendly approach to waste management.
What You'll Learn
- Sorting and Collection: Recycling centers use specialized equipment to separate materials based on their physical properties
- Magnetic Separation: Metals like iron and steel attract magnets, making them easy to extract from other materials
- Density Differences: Paper and plastic have different densities, allowing for separation through water flotation or air tables
- Chemical Processes: Advanced recycling techniques use chemicals to break down and separate materials
- Manual Sorting: Human workers may still be involved in the final stages of sorting to ensure high-quality materials
Sorting and Collection: Recycling centers use specialized equipment to separate materials based on their physical properties
Recycling centers employ a variety of specialized equipment and processes to efficiently separate different types of materials, ensuring that each stream is collected and processed appropriately. This meticulous sorting process is crucial for maintaining the quality of recycled materials and facilitating their reuse in manufacturing new products. Here's an overview of how recycling centers achieve this separation:
Material Handling and Conveyor Systems: The first step in the sorting process involves the collection of recyclable materials from various sources, such as residential, commercial, or industrial facilities. These materials are often conveyed on belts or through automated systems to a central sorting area. Modern recycling centers utilize advanced conveyor belts equipped with sensors and cameras to identify and separate materials. For instance, infrared sensors can detect the heat signatures of different materials, allowing for the separation of plastics, metals, and paper.
Air Classifiers: One of the most common methods for separating materials is through air classification. This process involves using air streams to separate materials based on their size and density. Air classifiers work by blowing air through a series of screens or sieves, which separates materials into different streams. For example, lightweight materials like paper and plastic can be separated from heavier items like metal and glass. This method is highly effective and often used in combination with other sorting techniques.
Magnetic Separators: Metals are an essential component of the recycling stream, and specialized equipment is used to extract them. Magnetic separators are powerful tools in this regard. These machines use strong magnetic fields to attract and separate ferrous metals (like iron, steel, and nickel) from the recycling stream. Non-ferrous metals, such as aluminum and copper, can be separated using different magnetic strengths or by employing eddy current separators, which use electromagnetic induction to separate non-ferrous metals from other materials.
Optical Sorters: The visual properties of materials play a significant role in their separation. Optical sorters are designed to identify and separate materials based on their color, shape, and texture. These machines use advanced imaging technology to detect and classify materials with precision. For instance, optical sorters can distinguish between different types of plastics, glass, and paper, ensuring that each material is directed to the appropriate processing stream. This technology is particularly useful for identifying and removing contaminants from the recycling stream.
Manual Sorting and Quality Control: Despite the advanced equipment, some materials may still require manual sorting and inspection. This step is crucial for ensuring the quality of the recycled products. Trained staff inspect the sorted materials, removing any non-recyclable items, contaminants, or mixed materials. They may also perform additional sorting based on specific requirements, such as separating different types of plastics or ensuring a consistent size for paper recycling.
The efficiency and accuracy of these sorting methods are vital to the success of recycling programs. By employing specialized equipment and trained personnel, recycling centers can effectively separate metal, plastic, and paper, ensuring that each material is recycled responsibly and contributes to a sustainable circular economy. This process also helps in reducing the environmental impact of waste and promotes the conservation of natural resources.
Transforming Plastic Straws: The Journey to Recycling Success
You may want to see also
Magnetic Separation: Metals like iron and steel attract magnets, making them easy to extract from other materials
Magnetic separation is a fundamental process in recycling that utilizes the unique properties of certain materials to separate them from others. When it comes to recycling, one of the primary goals is to recover valuable materials like metals while ensuring that waste is minimized. This is particularly crucial in the context of mixed waste streams, where various materials such as metals, plastics, and paper are combined.
Metals, especially those containing iron and steel, have a distinct characteristic that makes them ideal candidates for magnetic separation. These metals possess a strong magnetic field, which allows them to be attracted to and separated by powerful magnets. The process begins with the waste material being fed into a specialized machine, often a conveyor belt or a screening system, designed to handle the recycling process. As the material moves along, powerful magnets are strategically placed to attract and capture the metallic components.
The magnetic field generated by these magnets interacts with the magnetic domains within the metal particles. Each metal atom has tiny magnetic domains, and when exposed to a magnetic field, these domains align, creating a collective magnetic effect. This alignment is what makes metals responsive to magnetic forces. As a result, the metal particles become magnetized and are drawn towards the magnet, leaving behind non-magnetic materials like plastics and paper.
This method of separation is highly efficient and effective, especially when dealing with large volumes of waste. The separated metals can then be further processed, melted, or recycled into new products, ensuring a continuous cycle of resource recovery. It is a crucial step in modern recycling practices, contributing to a more sustainable and environmentally friendly approach to waste management.
In summary, magnetic separation is a powerful technique in recycling, enabling the extraction of metals like iron and steel from a mixture of materials. By leveraging the magnetic properties of these metals, recycling facilities can efficiently sort and recover valuable resources, playing a vital role in the circular economy. This process highlights the ingenuity of recycling technologies in addressing the challenges of waste management and resource conservation.
Unveiling the Truth: Does Plastic Labeling Matter for Recycling?
You may want to see also
Density Differences: Paper and plastic have different densities, allowing for separation through water flotation or air tables
The process of recycling often involves separating various materials to ensure efficient processing and maximize resource recovery. One effective method for separating paper and plastic is based on their distinct physical properties, particularly their densities. Density refers to the mass per unit volume of a substance, and it plays a crucial role in the separation techniques used in recycling.
Paper and plastic have significantly different densities, which makes their separation a feasible and widely used practice. Paper, being a lightweight material primarily composed of cellulose fibers, has a relatively low density. When placed in water, paper floats due to its low specific gravity, which is the ratio of its density to the density of water. This property is harnessed in a process known as water flotation. In this method, paper materials are introduced into a body of water, and the lower density of paper causes it to float on the surface, allowing for easy separation from other recyclables.
On the other hand, plastic, especially common types like PET (polyethylene terephthalate) and HDPE (high-density polyethylene), has a higher density compared to paper. These plastics are denser and more buoyant in water, causing them to sink. By utilizing this density difference, recycling facilities can employ water flotation techniques to separate plastic from paper. The floating paper can be collected and directed to one side of the flotation system, while the denser plastic remains in the water, facilitating their individual collection and processing.
Another innovative approach to separating paper and plastic is through the use of air tables, also known as air classifiers. These machines utilize the difference in density between the two materials to achieve separation. Air tables work by creating a stream of air that carries lighter materials, such as paper, upwards, while denser plastics remain stationary or move at a slower pace. This method is particularly useful for high-volume recycling processes, ensuring efficient and accurate sorting.
In summary, the density differences between paper and plastic provide a practical basis for their separation in recycling. Water flotation and air table techniques are employed to take advantage of these density variations, allowing for the effective sorting of these materials. These methods contribute to the overall efficiency of recycling processes, ensuring that each material is directed to the appropriate stream for further processing and eventual reuse.
Unveiling Florida's Plastic Recycling Incentives: Are You Getting Paid?
You may want to see also
Chemical Processes: Advanced recycling techniques use chemicals to break down and separate materials
Chemical processes have revolutionized the field of recycling, offering advanced techniques to separate and recycle various materials, including metals, plastics, and paper. These methods are crucial in addressing the challenges of waste management and promoting a circular economy. Here's an overview of how chemical processes contribute to material separation:
Metal Recycling: One of the most common chemical processes for metal recycling is called 'hydrometallurgy.' This technique involves dissolving the metal-containing waste in a suitable chemical solution, typically an acidic or alkaline bath. For example, in the recycling of aluminum, the process begins by dissolving the aluminum-rich material in a hot sodium hydroxide (caustic soda) solution, which selectively dissolves the aluminum oxide while leaving impurities behind. This results in a solution containing dissolved aluminum, which can then be recovered through further chemical treatments. Similarly, other metals like copper, zinc, and lead can be extracted using specific chemical agents that target their unique properties.
Plastic Recycling: Advanced chemical recycling for plastics focuses on breaking down different types of polymers. One prominent method is chemical recycling through 'hydrolysis.' This process utilizes enzymes or chemicals to cleave the long polymer chains in plastics, converting them into smaller molecules or monomers. For instance, polyethyleneterephthalate (PET), commonly used in beverage bottles, can be chemically recycled to produce terephthalic acid and ethylene glycol, which are the building blocks for new PET products. Another approach is chemical recycling of plastics through 'depolymerization,' where plastics are treated with specific solvents or catalysts to break them down into their constituent parts, allowing for the recovery of valuable materials.
Paper Recycling: Chemical processes play a vital role in the recycling of paper, especially in removing ink and other contaminants. The process typically begins with a chemical treatment to break down the paper's cellulose fibers. One common method is the use of alkaline solutions, such as sodium hydroxide (caustic soda) and sodium carbonate, which help in dissolving the lignin (a complex polymer) that binds the cellulose fibers together. This treatment softens the paper, making it easier to separate the fibers. After chemical treatment, the paper fibers are cleaned and refined to produce recycled paper pulp, which can then be used to create new paper products.
These chemical processes offer efficient and targeted ways to separate materials, ensuring that recycled products meet the required quality standards. By employing specific chemical agents and reactions, recyclers can effectively break down and transform waste materials into valuable resources, contributing to a more sustainable and environmentally friendly approach to recycling.
Can Plastic Drink Rings Be Recycled? Lexington, KY, Explains
You may want to see also
Manual Sorting: Human workers may still be involved in the final stages of sorting to ensure high-quality materials
In the intricate process of recycling, manual sorting plays a crucial role, especially in the final stages, where human workers ensure the separation of various materials to maintain high-quality standards. This step is essential as it directly impacts the efficiency and effectiveness of the recycling process, ensuring that the end products are of the highest caliber.
The process begins with the collection of recyclable materials, which are then transported to a recycling facility. Here, the initial sorting often involves automated systems that separate materials based on their physical properties. For instance, magnetic separators are used to extract ferrous metals, while eddy currents separate non-ferrous metals. This initial stage is critical as it sets the foundation for the subsequent manual work.
However, the complexity of recycling mixed waste streams means that complete automation is not always feasible. This is where human intervention becomes vital. Manual sorting is a meticulous process that requires trained workers to identify and separate materials that are not easily distinguishable by machines. For example, workers might need to differentiate between various types of plastics, such as PET (polyethylene terephthalate) and HDPE (high-density polyethylene), which have different properties and uses. Similarly, they must identify and separate metals from plastics and paper, ensuring that each material is directed to the appropriate stream for further processing.
The human eye is adept at recognizing subtle differences that machines might miss. Workers can identify the color, texture, and feel of materials, ensuring that the recycling process is as precise as possible. This level of detail is crucial for maintaining the integrity of the recycling stream, especially when preparing materials for specific end-uses. For instance, ensuring that all plastics are free from metal contaminants is essential for the production of food-grade packaging.
Moreover, manual sorting allows for the immediate rejection of non-recyclable or contaminated materials, preventing them from entering the recycling stream. This quality control aspect is vital to maintaining public trust in recycling programs and ensuring that the end products meet the required standards. Human workers can also provide feedback to improve the overall efficiency of the recycling process, suggesting improvements to the automated systems or process flows.
In conclusion, while automation plays a significant role in recycling, manual sorting remains an indispensable step. Human workers are essential in the final stages, ensuring that materials are correctly identified, separated, and directed for appropriate recycling or reuse. This meticulous process contributes to the overall quality and sustainability of the recycling industry.
Recycling Plastic Utensils in NYC: What You Need to Know
You may want to see also
Frequently asked questions
Recycling facilities employ various methods to separate different materials. For metal recycling, the process often begins with shredding or baling the collected items to create smaller, more manageable pieces. These shredded metals are then fed into a magnetic separator, which attracts and separates ferrous metals (like iron and steel) from non-ferrous metals (such as aluminum, copper, and brass). This separation is crucial as it allows for more efficient processing and recycling of each metal type.
Plastic recycling involves several steps to ensure effective separation. One common method is density separation, where plastics are sorted based on their density. Lighter plastics, such as those used in packaging (PET and HDPE), float, while heavier plastics, like those in bottles and containers (PVC and LDPE), sink. This process is often facilitated by water baths or air tables, allowing for the physical separation of different plastic types.
Paper recycling typically starts with the collection and transportation of used paper products to a recycling plant. The paper is then cleaned and sorted to remove any non-paper contaminants. One of the key processes in paper recycling is de-inking, where ink and other impurities are removed from the paper fibers. This is often done using screens or air classifiers. After de-inking, the paper fibers are cleaned further and mixed with water to create a slurry. The slurry is then cleaned and refined to produce recycled paper pulp, which can be used to make new paper products.
Yes, recycling facilities often face challenges in separating materials effectively. Contamination is a significant issue, especially with plastic recycling, where food residue, labels, and other non-plastic materials can make separation difficult. Additionally, some metals and plastics have similar properties, making it hard to distinguish between them. Advanced recycling technologies, such as optical sorters and near-infrared (NIR) spectroscopy, are used to overcome these challenges and improve the efficiency of material separation.