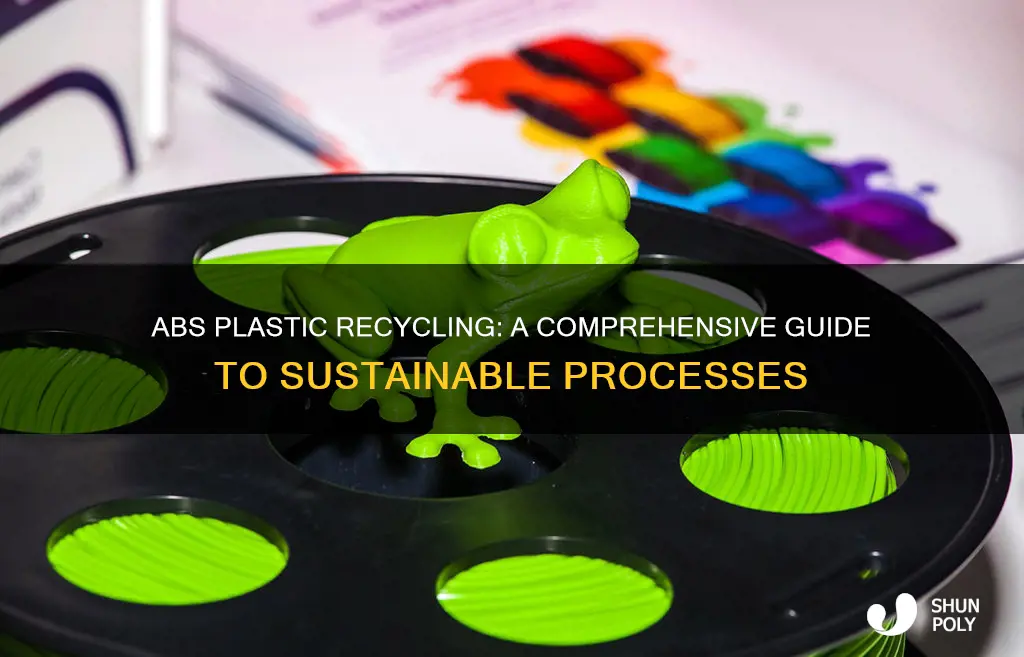
ABS (acrylonitrile butadiene styrene) plastic is a common material used in various products, from electronics to automotive parts. Recycling ABS is crucial to reducing waste and conserving resources. The process begins with collecting used ABS items, which are then sorted and cleaned to remove contaminants. The sorted ABS is shredded into small pieces, and these flakes are washed to eliminate any remaining dirt or debris. After washing, the flakes are dried and ground into a fine powder. This powder can be used in various ways, such as manufacturing new ABS products or as a raw material for other industries. The recycling process ensures that ABS plastic is given a new life, contributing to a more sustainable approach to waste management.
What You'll Learn
- Collection: ABS plastic is gathered from various sources, including recycling bins and waste streams
- Sorting: Materials are sorted by color and type to ensure proper processing
- Shredding: Plastic is shredded into small pieces to facilitate further processing
- Melting: Shredded ABS is melted down to a liquid state for reprocessing
- Molding: The molten plastic is shaped into new products using molding techniques
Collection: ABS plastic is gathered from various sources, including recycling bins and waste streams
The process of recycling ABS (acrylonitrile butadiene styrene) plastic begins with the collection of this material from various sources. ABS is a common type of plastic used in a wide range of products, from automotive parts to consumer electronics, and its recycling is crucial for environmental sustainability. The collection phase is a critical step in the recycling process, ensuring that the plastic can be effectively sorted, processed, and transformed into new products.
One primary source of ABS plastic collection is recycling bins specifically designated for plastic waste. These bins are often color-coded or labeled to indicate that they accept ABS or other types of plastic. When individuals and businesses dispose of their plastic items, they place them in these designated bins, making it easier for waste management companies to collect and sort the materials. Public awareness campaigns and educational programs can encourage proper waste segregation, ensuring that ABS plastic ends up in the correct recycling stream.
In addition to household recycling bins, waste streams from various industries and commercial activities contribute significantly to ABS plastic collection. Manufacturing facilities, construction sites, and electronic waste disposal centers generate substantial amounts of plastic waste, including ABS. These sources often have dedicated collection systems in place to separate and collect different types of plastics. For instance, construction companies might have separate bins for general plastic waste and specific bins for engineering plastics like ABS, ensuring that the material is collected and recycled efficiently.
Another important aspect of ABS plastic collection is the involvement of waste management companies and recycling centers. These facilities have specialized equipment and processes to handle and process plastic waste. They collect ABS plastic from various sources, including residential, commercial, and industrial areas. Through their collection efforts, they ensure that the plastic is sorted and prepared for the next stage of recycling, which typically involves cleaning, shredding, or granulating the material to create a usable feedstock for manufacturing new products.
The collection of ABS plastic is a collaborative effort involving individuals, businesses, and waste management systems. By ensuring that ABS plastic is properly sorted and collected, the recycling process can be optimized, leading to the creation of new products and reducing the environmental impact of plastic waste. This collection phase is a vital step in the journey towards a more sustainable and circular economy.
Unveiling Oakland's Plastic Recycling Mystery: Does It Work?
You may want to see also
Sorting: Materials are sorted by color and type to ensure proper processing
The process of recycling ABS (acrylonitrile butadiene styrene) plastic begins with meticulous sorting, a crucial step to ensure the efficiency and effectiveness of the recycling process. This initial stage involves a careful classification of ABS materials based on their color and type, which is essential for the subsequent recycling procedures. The sorting process is designed to separate ABS plastics into distinct categories, allowing for a more targeted and controlled recycling environment.
When ABS plastic items are collected, they are first sorted by color. ABS is commonly available in various colors, including white, black, and various shades of grey. Sorting by color is a fundamental practice as it enables the recycling facility to handle different colors separately, preventing potential contamination. For instance, black ABS, often used in automotive parts, may have different recycling requirements compared to white ABS, which is frequently utilized in consumer electronics. This color-based sorting ensures that the recycling process can be tailored to the specific needs of each color group.
In addition to color sorting, materials are also categorized by type. ABS plastic can be found in various forms, such as solid sheets, tubes, or complex shaped parts. Each of these forms may have unique properties and recycling challenges. For example, solid sheets might require different processing methods compared to hollow tubes or intricate components. By sorting ABS materials by type, recycling facilities can employ specialized techniques to handle each category effectively. This type-specific sorting ensures that the recycling process is optimized for the diverse range of ABS products available.
The sorting process is a meticulous and labor-intensive task, requiring skilled personnel to identify and separate the materials accurately. Workers use their expertise to distinguish between different colors and types of ABS, ensuring that no valuable material is wasted. This attention to detail is vital as it sets the foundation for the entire recycling process, allowing for the efficient recovery of valuable resources from the ABS waste stream.
Once sorted, the ABS materials are ready for the next phase of recycling, which may involve shredding, washing, and further processing to create new products. The sorting step is a critical quality control measure, ensuring that the recycling process is tailored to the specific characteristics of ABS plastic, ultimately contributing to the production of new, sustainable materials.
Plastic ID Holders: Can They Be Recycled?
You may want to see also
Shredding: Plastic is shredded into small pieces to facilitate further processing
The process of recycling ABS (acrylonitrile butadiene styrene) plastic begins with shredding, a crucial step that prepares the material for subsequent recycling procedures. ABS, commonly used in electronics, automotive, and consumer goods, is shredded into small, uniform pieces to ensure efficient recycling. This initial step is essential as it reduces the size of the plastic, making it easier to handle and process. The shredding process involves specialized machinery that breaks down the ABS plastic into manageable fragments, typically ranging from 0.5 to 2 inches in size. These shredded pieces are then sorted and classified based on their size and quality, ensuring a consistent feedstock for the recycling plant.
Shredding offers several advantages in the recycling of ABS plastic. Firstly, it increases the surface area of the plastic, exposing more material to the recycling process. This is particularly important for ABS, as it is known for its durability and impact resistance, which can make it challenging to recycle without proper preparation. By shredding the plastic, the recycling process can more effectively separate the ABS from any contaminants, such as fillers or additives, ensuring a higher-quality recycled product. Additionally, the shredded form of ABS is more versatile, allowing for various recycling techniques to be applied, including re-granulation and compounding.
The shredded ABS plastic is then transported to a recycling facility, where further processing takes place. At this stage, the material is often washed to remove any remaining contaminants and to ensure a clean feedstock. This washing process is crucial to maintaining the quality of the recycled ABS. After washing, the shredded plastic is dried to remove any moisture, which can interfere with the recycling process. The dried ABS is then ready for the next step, which may involve re-granulation or compounding, depending on the desired end product.
Re-granulation is a common method used to recycle shredded ABS plastic. In this process, the shredded material is melted and then extruded through a die to create small, uniform pellets, known as re-granules. These re-granules can then be used as a raw material for manufacturing new products, such as electronic components, automotive parts, or consumer goods. The re-granulation process ensures that the recycled ABS retains its original properties, making it a valuable resource for various industries.
In summary, shredding is a critical step in the recycling of ABS plastic, as it prepares the material for further processing and ensures a consistent and high-quality feedstock. By reducing the size of the plastic, shredding increases the efficiency of the recycling process, allowing for effective separation of contaminants and the production of re-granules. This process is an essential part of the circular economy, enabling the reuse of ABS plastic in various applications and contributing to sustainable waste management practices.
The Plastic Recycling Myth: Unveiling the Truth
You may want to see also
Melting: Shredded ABS is melted down to a liquid state for reprocessing
The process of recycling ABS (acrylonitrile butadiene styrene) plastic begins with the collection and sorting of ABS waste. Once sorted, the ABS material is shredded into small pieces to facilitate the recycling process. This shredding step ensures that the plastic is broken down into a manageable size, making it easier to handle and process.
After shredding, the ABS plastic is prepared for the melting stage. This involves heating the shredded ABS to a specific temperature, typically around 250-275°C (482-527°F), in a controlled environment. The heating process is crucial to ensure that the plastic is softened and becomes a viscous liquid. The molten ABS is then carefully poured into a mold or a designated container, where it will be allowed to cool and solidify.
Melting ABS plastic is a precise and controlled process. The temperature and duration of heating are critical factors to achieve the desired liquid state. The molten ABS can be further refined and purified to remove any impurities or residual materials. This step ensures that the recycled ABS meets the required quality standards for its intended applications.
Once the molten ABS is ready, it can be reprocessed into new products. The liquid state allows for various manufacturing techniques, such as injection molding, to create new ABS-based items. This recycling process not only reduces waste but also provides a sustainable alternative to producing new ABS products from virgin materials.
The melting and reprocessing of shredded ABS plastic is an essential step in the recycling chain, transforming waste into a valuable resource. It showcases the potential for recycling ABS, encouraging a circular economy and reducing the environmental impact of plastic waste. With proper recycling practices, ABS plastic can be continuously reused, contributing to a more sustainable future.
Unraveling the Mystery: A Guide to Recycling Plastic Like a Pro
You may want to see also
Molding: The molten plastic is shaped into new products using molding techniques
The process of recycling ABS (acrylonitrile butadiene styrene) plastic involves several stages, and molding is a crucial step in transforming recycled ABS into new products. ABS is a popular thermoplastic known for its impact resistance, durability, and ease of processing, making it widely used in various industries, including automotive, electronics, and construction. When ABS products reach the end of their life, they can be recycled through a process that includes molding to create new items.
Molding is a manufacturing process that utilizes heat and pressure to shape molten plastic into desired forms. In the context of ABS recycling, the process begins with collecting and sorting ABS waste, which can include post-consumer and post-industrial materials. The collected ABS is then shredded or granulated to reduce its size and facilitate further processing. The shredded or granulated ABS is fed into a hopper, where it is heated to a specific temperature, typically around 250-275°C (482-527°F), to make it molten and malleable.
Once the ABS is molten, it is ready for the molding stage. This process involves several techniques, each offering unique advantages depending on the desired product:
- Injection Molding: This is a common method where the molten ABS is injected into a closed mold under high pressure. The mold is designed with the specific shape and dimensions of the desired product. As the plastic cools and solidifies, it takes the shape of the mold, creating a wide range of objects, from simple components to complex automotive parts. Injection molding is highly versatile and can produce large quantities of products efficiently.
- Extrusion Molding: In this process, the molten ABS is forced through a die to create a continuous shape. Extrusion molding is often used for producing hollow objects, such as pipes, profiles, or even furniture. The molten plastic is pushed through the die, and as it cools, it takes the shape of the die's internal structure. This method is energy-efficient and can handle large volumes of material.
- Compression Molding: Here, the molten ABS is placed in an open mold, and pressure is applied to shape it. This technique is suitable for creating products with intricate details or complex geometries. The mold is closed, and the plastic is compressed and heated to form the desired shape. Compression molding is often used for manufacturing precision components and can produce high-quality, consistent results.
After molding, the recycled ABS products are cooled and solidified. These products can then be used in various applications, such as automotive parts, electronic enclosures, construction materials, or even consumer goods. The molding process allows for the creation of new, high-quality items from recycled ABS, contributing to a more sustainable and circular economy. It is important to note that the specific molding techniques and parameters may vary depending on the desired product and the recycling facility's capabilities.
Unveiling America's Recycling Reality: Plastic and Glass
You may want to see also
Frequently asked questions
ABS plastic recycling involves a multi-step process. First, the plastic waste is collected and sorted to ensure it is free from contaminants. Then, it is shredded or granulated to reduce its size. The shredded ABS is cleaned to remove any remaining impurities, and then it undergoes a process called "recycling," where it is melted and reformed into new products. This process can be done through various methods, including injection molding, extrusion, or blow molding, depending on the desired end product.
Recycling facilities employ specific techniques to process ABS plastic. The waste is typically sorted by color and type to ensure the highest quality of the recycled material. After sorting, the ABS is cleaned to remove any non-plastic materials, such as labels or contaminants. The cleaned ABS is then ground into small pellets or flakes, which can be used as a raw material for manufacturing new products. This process helps reduce the demand for virgin plastic production and promotes a circular economy.
ABS plastic recycling does face some challenges. One issue is the potential for color degradation during the recycling process, as ABS is known for its bright, vibrant colors. To address this, some recycling facilities use advanced sorting and cleaning techniques to maintain color consistency. Another challenge is the potential for material degradation over multiple recycling cycles, as ABS may lose its structural integrity with repeated processing. Therefore, it is essential to use high-quality ABS waste and employ proper recycling methods to minimize these limitations.