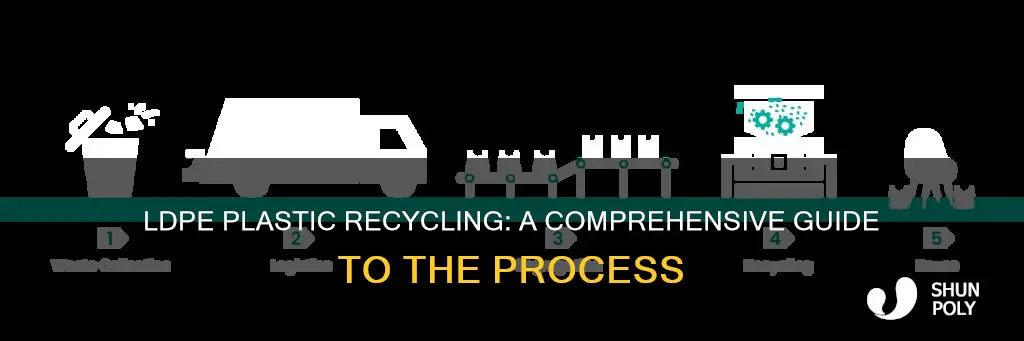
LDPE (Low-Density Polyethylene) plastic recycling is a crucial process in managing and reusing this common type of plastic. It involves transforming used LDPE products into new materials, reducing waste and conserving resources. The recycling process typically begins with collecting and sorting LDPE items, such as plastic bags, film wraps, and containers. These materials are then cleaned, shredded, or melted to create a raw material that can be remolded into new products. The recycled LDPE can be used to produce various items, including new plastic bags, containers, and even furniture, contributing to a more sustainable approach to plastic waste management.
What You'll Learn
- Collection: LDPE plastic is gathered from recycling bins and waste streams
- Sorting: Materials are sorted by color and type to ensure purity
- Shredding: Plastic is shredded into small pieces for easier processing
- Cleaning: Contaminants are removed to prevent cross-contamination during recycling
- Melting and Reforming: LDPE is melted and reformed into new products
Collection: LDPE plastic is gathered from recycling bins and waste streams
The collection of Low-Density Polyethylene (LDPE) plastic is a crucial step in the recycling process, ensuring that this versatile material can be transformed into new products. LDPE is commonly found in various household items, such as shopping bags, film wraps, and some containers, making its collection an essential part of waste management.
When LDPE plastic is discarded, it is typically sorted and collected from recycling bins and waste streams. These bins are strategically placed in public areas, residential neighborhoods, and commercial spaces to encourage proper waste segregation. The collection process begins with the diligent work of waste management personnel or volunteers who ensure that LDPE items are separated from other types of waste. This separation is vital as it prevents contamination and makes the recycling process more efficient.
During collection, LDPE items are identified and sorted based on their color, size, and shape. Common LDPE products include plastic bags, film wraps used for covering items, and certain types of containers like yogurt cups and detergent bottles. These items are carefully gathered and placed into designated LDPE streams or bins, ensuring they are kept separate from other plastics and materials. The goal is to create a clean and consistent feedstock for the recycling facility.
The collected LDPE waste is then transported to specialized recycling centers or facilities. These centers have the infrastructure and equipment to handle and process LDPE effectively. Upon arrival, the LDPE waste undergoes further sorting and cleaning processes to remove any contaminants, ensuring the highest quality of the recycled material. This step is critical to producing high-grade LDPE pellets or granules, which can be used in various manufacturing processes.
By implementing efficient collection methods, LDPE plastic can be effectively gathered and prepared for recycling. This process not only reduces environmental impact but also contributes to the circular economy, allowing LDPE to be reused and repurposed, ultimately reducing the demand for virgin materials and minimizing waste.
Pyrex Lid Recycling: Unlocking the Mystery of Plastic Waste
You may want to see also
Sorting: Materials are sorted by color and type to ensure purity
The initial step in the LDPE (Low-Density Polyethylene) recycling process is sorting, a critical phase that ensures the purity and quality of the recycled material. This process involves a meticulous examination and separation of various types of plastics and their colors, a task that is both essential and challenging. The goal is to create a clean and consistent feedstock for the recycling machinery, which can then be transformed into new products.
Sorting by color is a primary method used to categorize LDPE. LDPE is typically white or translucent, and the sorting process aims to separate this material from other types of plastics that may have a different appearance. For instance, HDPE (High-Density Polyethylene) is often a brighter, more opaque plastic, and HDPE-contaminated LDPE batches can lead to issues in the recycling stream. By sorting by color, recyclers can ensure that the LDPE is free from other types of plastics, maintaining its integrity.
Beyond color, the sorting process also involves categorizing LDPE by type. LDPE is a versatile plastic used in a wide range of products, from grocery bags to containers. It is important to separate LDPE from other forms of polyethylene, such as HDPE, as well as from other types of plastics like PET (Polyethylene Terephthalate) or PVC (Polyvinyl Chloride). Each type of plastic has unique properties and recycling requirements, and mixing them can lead to contamination and reduced quality of the recycled material.
Advanced sorting techniques are employed to enhance the efficiency and accuracy of this process. Optical sorters, for example, use light sensors to identify the color and type of plastic. These machines can quickly separate LDPE from other materials, ensuring that only the desired type of plastic is fed into the recycling stream. Additionally, manual sorting, where trained personnel inspect and separate materials, is still a crucial part of the process, especially for small-scale recycling operations.
The purity of the sorted LDPE is vital for the success of the recycling process. Contaminated LDPE can lead to issues in the downstream recycling stages, affecting the quality and performance of the final recycled product. Therefore, meticulous sorting by color and type is a critical step that ensures the LDPE is clean, consistent, and ready for the next phase of recycling, contributing to a more sustainable and efficient waste management system.
Unraveling the Mystery: Can Plastic Containers Be Recycled?
You may want to see also
Shredding: Plastic is shredded into small pieces for easier processing
The process of recycling LDPE (Low-Density Polyethylene) plastic begins with the collection and sorting of plastic waste. Once sorted, the LDPE plastic is prepared for recycling by a crucial step: shredding. This initial step is essential as it transforms the large, bulky plastic items into smaller, more manageable pieces, making the subsequent recycling process more efficient and effective.
Shredding is a mechanical process that involves breaking down the LDPE plastic into tiny fragments. This is typically done using specialized machinery designed for plastic shredding. The shredded plastic is then sorted by size, creating a range of particle sizes that can be further processed. The shredded LDPE can vary in size from small flakes to larger pellets, depending on the desired end product and the specific recycling process.
The shredding process is crucial for several reasons. Firstly, it reduces the volume of plastic waste, making it easier to store and transport. This is particularly important in large-scale recycling operations where tons of plastic waste need to be processed efficiently. By shredding the plastic, it becomes more compact and easier to handle, reducing storage costs and logistical challenges.
Secondly, shredding allows for better control over the quality of the recycled LDPE. Smaller pieces provide a more uniform material, ensuring consistency in the final product. This is vital for manufacturers who rely on LDPE for various applications, as it guarantees a reliable supply of raw material. The shredded LDPE can then be further processed through various methods, such as washing, drying, and pelletizing, to create a high-quality recycled plastic product.
After shredding, the LDPE plastic is ready for the next stage of recycling, which may involve additional processes to transform it into a usable form. This could include melting and molding for creating new products or compounding to enhance its properties. The shredded LDPE can be used in various applications, such as manufacturing new containers, packaging materials, or even construction products, contributing to a circular economy and reducing the environmental impact of plastic waste.
Unveiling Utah's Plastic Recycling Tax: A Case Study on St. George
You may want to see also
Cleaning: Contaminants are removed to prevent cross-contamination during recycling
The process of recycling LDPE (Low-Density Polyethylene) plastic begins with the collection and sorting of LDPE materials. Once sorted, the LDPE items are cleaned to ensure they are free from contaminants, which is a crucial step to prevent cross-contamination during recycling. Cleaning LDPE involves several methods to remove any impurities that could hinder the recycling process.
One common cleaning technique is washing the LDPE items with water and detergents. This process helps to eliminate dirt, food residues, and other organic materials that may be present on the plastic. High-pressure water jets and specialized cleaning solutions are often used to ensure thorough cleaning. After washing, the LDPE is typically rinsed with clean water to remove any remaining detergent and to further reduce the risk of contamination.
Another important aspect of cleaning LDPE is removing any non-plastic components that might be attached. This includes labels, caps, and other non-LDPE materials. These items are carefully separated and disposed of appropriately to ensure they do not contaminate the LDPE during recycling. For example, metal caps might be collected separately and recycled through their respective streams, while paper labels can be recycled with other paper waste.
In some cases, LDPE items may require additional cleaning steps. For instance, if the LDPE is heavily contaminated with grease or oil, a more intensive cleaning process might be necessary. This could involve using steam or specialized cleaning agents to break down and remove these stubborn contaminants. The goal is to ensure that the LDPE is clean and free from any harmful substances before it is recycled.
By implementing these cleaning processes, recycling facilities can maintain high standards of purity in the LDPE recycling stream. This is essential to ensure that the recycled LDPE meets the required quality standards and can be effectively reused in various applications, contributing to a more sustainable and efficient recycling system. Proper cleaning also helps to reduce the environmental impact of recycling by minimizing the risk of cross-contamination and potential pollution.
Unrecyclable Plastics: Understanding the Non-Recyclable Waste
You may want to see also
Melting and Reforming: LDPE is melted and reformed into new products
The process of recycling Low-Density Polyethylene (LDPE) involves a method known as "melting and reforming," which is a crucial step in transforming used LDPE materials into new, usable products. This technique is particularly effective for LDPE, as it is a thermoplastic material that can be easily reshaped when heated. Here's an overview of this recycling process:
LDPE, a common type of plastic used in various products like shopping bags, film wraps, and containers, is collected and sorted according to recycling standards. Once sorted, the LDPE waste is prepared for the melting process. This involves cleaning the LDPE to remove any contaminants, such as labels, dirt, or other non-LDPE materials, ensuring the purity of the feedstock. After cleaning, the LDPE is shredded or granulated into small pieces, making it easier to handle and melt.
The melting process begins by feeding the shredded LDPE into a specialized machine called an extruder. This machine applies heat and pressure to the LDPE, softening it and eventually melting it into a viscous liquid. The temperature and duration of the melting process are carefully controlled to ensure the LDPE's chemical structure remains intact. Once melted, the LDPE is often filtered to remove any remaining impurities.
After melting, the LDPE is reformed into new products. This is achieved through a process called "re-pelletizing" or "re-granulating." The molten LDPE is forced through a die, which shapes it into small pellets or granules. These pellets are then cooled and solidified, creating a new form of LDPE that can be used for various applications. The reformed LDPE pellets can be used as a raw material for manufacturing new LDPE products, such as containers, packaging, or even new shopping bags.
This recycling method is highly efficient and cost-effective, allowing for the reuse of LDPE multiple times without significant loss of quality. It is an essential process in the circular economy, reducing waste and promoting sustainable practices in the plastic industry. By melting and reforming LDPE, recycling facilities can contribute to a more sustainable future, ensuring that valuable resources are conserved and reused.
Unraveling the Mystery: Can Plastic Card Sleeves Be Recycled?
You may want to see also
Frequently asked questions
LDPE stands for Low-Density Polyethylene, a type of thermoplastic polymer commonly used in various products like grocery bags, film wraps, and some containers. Recycling LDPE is crucial because it helps reduce environmental impact, conserve resources, and promote a circular economy.
The recycling process for LDPE typically involves several steps. First, LDPE waste is collected and sorted to ensure it is free from contaminants. Then, it is shredded or granulated into small pieces. These pieces are cleaned and melted to form pellets, which can be used to create new products. The process is energy-intensive, but it significantly reduces the demand for virgin materials and minimizes the amount of plastic ending up in landfills or the environment.
Yes, several methods are employed in LDPE recycling. One common technique is mechanical recycling, where LDPE is processed through shredding, washing, and pelletizing. Another approach is chemical recycling, which involves breaking down LDPE into its base chemicals using various processes like solvent extraction or thermal decomposition. These methods aim to recover the polymer's original properties for reuse.
Recycling LDPE faces challenges such as ensuring proper sorting and cleaning of waste, as LDPE can be mixed with other plastics. Additionally, the process requires significant energy input, which is a concern for environmentalists. However, the benefits include reducing greenhouse gas emissions, conserving non-renewable resources, and minimizing the need for new plastic production, thus decreasing pollution and waste accumulation.