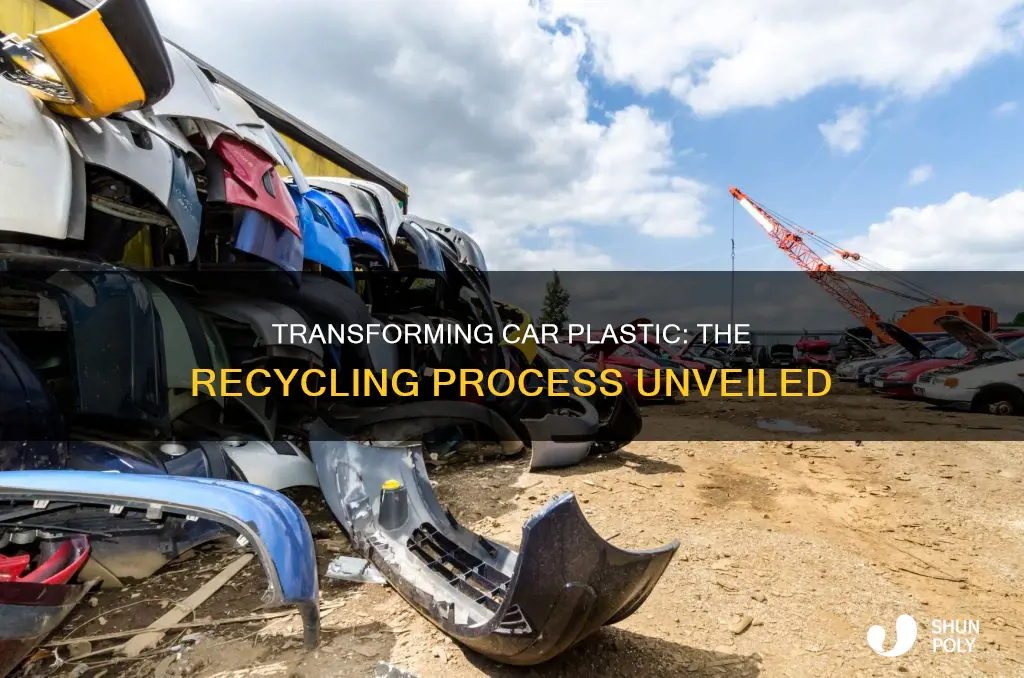
Plastic recycling in the automotive industry is a crucial process to address the growing environmental concerns associated with vehicle manufacturing. Plastic components in cars, such as interior trim, dashboards, and exterior panels, are often made from various types of polymers, each requiring specific recycling methods. The recycling process begins with the collection and sorting of plastic waste, which is then shredded or granulated to prepare it for further processing. Different recycling techniques, such as chemical recycling and mechanical recycling, are employed to transform the plastic into raw materials that can be used to produce new car parts or other products. Understanding these recycling methods is essential for optimizing the sustainability of the automotive industry and reducing the environmental impact of plastic waste.
What You'll Learn
- Collection and Sorting: Plastic waste from cars is collected and sorted by type and color
- Cleaning and Shredding: Materials are cleaned, shredded, and processed to remove contaminants
- Melting and Molding: Plastic is melted and molded into new products like car parts
- Quality Control: Recycled plastic is tested for durability and performance before use
- End-of-Life Management: Proper disposal and recycling methods ensure a sustainable car industry
Collection and Sorting: Plastic waste from cars is collected and sorted by type and color
The process of recycling plastic from cars begins with the collection of plastic waste, which is a crucial step in ensuring the effectiveness and sustainability of the recycling program. Plastic waste from vehicles, such as car interiors, dashboards, and various components, is carefully gathered from various sources. This includes end-of-life vehicles, where the plastic parts are removed and prepared for recycling, as well as automotive manufacturing facilities that generate plastic scraps during production. The collection process aims to gather a wide range of plastic types and colors, as different plastics have unique properties and recycling methods.
Once collected, the plastic waste undergoes a meticulous sorting process. This step is essential to separate the plastics into different categories, ensuring that each type is recycled appropriately. The sorting process typically involves manual labor and advanced machinery. Workers carefully examine the plastic materials, identifying their types based on their appearance, texture, and feel. Common plastic types found in cars include polypropylene (PP), high-density polyethylene (HDPE), and polycarbonate (PC), each requiring specific recycling techniques.
During sorting, plastics are categorized into groups such as clear, green, black, and white, or by their chemical composition. For instance, polycarbonate is often identified by its distinct green color, while polypropylene may be recognized by its slightly gritty texture. This classification is vital as it determines the recycling path for each plastic type. Different colors and types of plastics may have varying recycling potentials and end-use applications.
Advanced recycling facilities employ various methods to enhance the sorting process. Optical sorters use light sensors to identify and separate plastics based on their color and transparency. These machines can quickly process large volumes of plastic waste, improving efficiency. Additionally, eddy current separators are utilized to detect and remove non-plastic materials, such as metal scraps, ensuring a cleaner feedstock for recycling. The sorted plastics are then stored separately, ready for the next stage of the recycling journey.
The collection and sorting process is a critical phase in plastic car recycling, as it sets the foundation for successful recycling and the potential for creating new products. Proper sorting ensures that each plastic type is recycled accordingly, maximizing resource recovery and minimizing environmental impact. This step also contributes to the overall sustainability of the automotive industry, allowing for the efficient reuse of materials and the reduction of waste.
Unleash the Potential: Can 5-Gallon Buckets Be Recycled?
You may want to see also
Cleaning and Shredding: Materials are cleaned, shredded, and processed to remove contaminants
The process of recycling plastic from cars begins with meticulous cleaning, a crucial step to ensure the material is free from contaminants and ready for further processing. This initial phase involves removing any non-plastic components, such as metal fasteners, glass, and other debris, from the plastic parts. The cleaning process can vary depending on the type of plastic and the specific requirements of the recycling facility. For instance, some facilities might use water jets or mechanical brushes to dislodge dirt and grime. In more specialized cases, chemicals might be employed to dissolve or break down stubborn contaminants, ensuring a thorough clean.
Once cleaned, the plastic materials are prepared for the next stage: shredding. Shredding is a process that reduces the plastic into smaller, more manageable pieces. This step is essential because it increases the surface area of the plastic, making it easier to process and recycle. The shredded plastic can then be further sorted and classified based on its type and quality. This classification is vital as it determines the potential end-use of the recycled material. For instance, high-quality shredded plastic might be used for manufacturing new car parts, while lower-grade material could be utilized for other applications, such as construction or packaging.
The shredded plastic is then subjected to additional processing to remove any remaining contaminants. This step is critical to ensure the recycled material meets the required standards and can be used in various applications. One common method is the use of air classifiers, which separate the plastic particles based on their size and density. This process helps to remove any light-weight contaminants, such as fibers or small particles, that might remain after the initial cleaning and shredding. Another technique is the use of magnetic separators, which can extract metal contaminants, ensuring a pure and consistent plastic product.
After these processes, the plastic is ready for the final stages of recycling, which may include compounding, where the plastic is melted and mixed with other materials to create a new, usable product. This step can involve adding colorants, fillers, or other additives to enhance the material's properties. The final product can then be used in various industries, contributing to a more sustainable approach to manufacturing and waste management. The cleaning and shredding process is a critical and intricate phase in the recycling journey, ensuring that the plastic derived from cars can be effectively transformed into new products, reducing waste and promoting environmental sustainability.
Unraveling the Mystery: Are All 7 Plastics Recyclable?
You may want to see also
Melting and Molding: Plastic is melted and molded into new products like car parts
The process of recycling plastic in cars involves a crucial step known as melting and molding, which transforms old plastic components into new, reusable parts. This method is an essential part of the recycling cycle for the automotive industry, ensuring that plastic waste is given a new lease of life. Here's a detailed breakdown of this process:
When a car reaches the end of its useful life or is deemed for salvage, the plastic components are carefully removed and sorted. These plastics can vary in type, including ABS (acrylonitrile butadiene styrene), polypropylene, and polycarbonate, each with unique properties. The first step in the recycling process is to shred or grind these plastics into small, uniform pieces, often referred to as 'flakes' or 'granules'. This step is crucial as it prepares the plastic for the subsequent stages.
The shredded plastic is then sent to a recycling facility where it undergoes a process called melting. This involves heating the plastic flakes to extremely high temperatures, typically between 200°C and 300°C, depending on the type of plastic. The heat softens the plastic, allowing it to be shaped and molded without breaking down chemically. Specialized equipment, such as extruders, is used to melt the plastic efficiently and ensure a consistent temperature throughout the batch.
Once melted, the plastic is now in a molten state and is ready for molding. This stage is where the magic happens, as the molten plastic is shaped into new products. The process begins by feeding the melted plastic into a mold, which is designed to create a specific car part, such as a dashboard, door panel, or interior trim. The mold is typically made of metal and is heated to a temperature that allows the plastic to flow easily into the desired shape. This step requires precision and control to ensure the final product meets the required specifications.
After the plastic solidifies within the mold, it is carefully removed, and the newly formed car part is inspected. This molding process can be repeated multiple times, creating a continuous cycle of recycling. The molded parts are then cleaned, finished, and prepared for installation in new vehicles or for use in the manufacturing of replacement parts for existing cars. This method of recycling not only reduces waste but also helps conserve resources and minimizes the environmental impact of the automotive industry.
The Surprising Truth: Should You Recycle Plastic Plates?
You may want to see also
Quality Control: Recycled plastic is tested for durability and performance before use
Quality control is an essential step in the recycling process for plastic components in automobiles, ensuring that the recycled material meets the required standards and performs as expected. When it comes to recycling plastic in cars, the process involves several stages, and quality control is a critical aspect that cannot be overlooked.
After the plastic waste is collected and sorted, it undergoes a series of tests to ensure its quality and suitability for reuse. The first step in quality control is material inspection. This involves examining the plastic for any contaminants, such as dirt, debris, or other non-plastic materials. Contaminants can compromise the performance and integrity of the recycled plastic, so thorough cleaning and sorting are necessary. Advanced techniques like near-infrared spectroscopy can be employed to identify and separate different types of plastics, ensuring a pure and homogeneous material.
Once the plastic is cleaned and sorted, it is subjected to various mechanical and physical tests. These tests evaluate the material's strength, flexibility, and overall durability. For instance, tension and compression tests are conducted to assess the plastic's ability to withstand forces without breaking or deforming. Impact resistance tests are also performed to simulate real-world conditions and ensure the plastic can handle sudden shocks and vibrations. These tests provide valuable data on the material's performance, allowing engineers to make informed decisions about its suitability for specific automotive applications.
In addition to mechanical tests, recycled plastic is also evaluated for its chemical properties. This includes analyzing the material's molecular structure and composition. Techniques like Fourier-transform infrared spectroscopy (FTIR) are used to identify any potential degradation or contamination that may affect the plastic's performance. By understanding the chemical changes that occur during the recycling process, manufacturers can optimize their methods and ensure the final product meets the required specifications.
Furthermore, the performance of recycled plastic is compared to that of virgin plastic to ensure it meets or exceeds industry standards. This comparison involves rigorous testing and analysis, often conducted in controlled laboratory settings. By subjecting the recycled material to the same rigorous standards as its virgin counterpart, manufacturers can guarantee the quality and reliability of the final product. This process of quality control is vital to maintaining the integrity of the automotive industry and promoting sustainable practices.
China's Plastic Recycling Shift: A Global Impact
You may want to see also
End-of-Life Management: Proper disposal and recycling methods ensure a sustainable car industry
The end-of-life management of vehicles is a critical aspect of ensuring a sustainable car industry, especially when considering the environmental impact of plastic components. As cars reach the end of their useful lives, proper disposal and recycling methods become essential to minimize waste and promote resource conservation. Plastic, in particular, is a significant material in automobiles, used in various forms such as interior trim, dashboards, door panels, and even in the engine bay for insulation. When these vehicles are retired, the plastic components must be managed carefully to prevent environmental degradation.
One of the primary methods of recycling plastic in cars is through the process of granulation. This involves shredding the plastic components into small pieces, which are then washed to remove any contaminants. The cleaned plastic fragments are further processed to remove any remaining impurities, and finally, they are granulated into a uniform size. These plastic granules can then be used in various manufacturing processes, such as producing new car parts or other automotive components, ensuring a closed-loop recycling system.
Another approach to managing plastic waste from cars is through chemical recycling. This method utilizes advanced technologies to break down the plastic into its original monomers or building blocks. By doing so, the plastic can be repurposed and reused in the production of new materials, reducing the demand for virgin plastic production. Chemical recycling processes are particularly useful for certain types of plastics that are challenging to recycle through traditional mechanical methods.
Proper disposal and recycling of plastic in cars also contribute to the overall sustainability of the automotive industry. By implementing effective end-of-life management practices, manufacturers can reduce their environmental footprint and promote a circular economy. This involves designing vehicles with recyclability in mind, using easily separable materials, and ensuring that end-of-life vehicles are processed through established recycling channels.
In summary, the recycling of plastic in cars is a crucial aspect of end-of-life management, ensuring that valuable resources are recovered and reused. Through processes like granulation and chemical recycling, plastic components can be transformed into new materials, reducing the industry's reliance on virgin resources. By adopting these recycling methods and promoting sustainable practices, the automotive sector can contribute to a more environmentally friendly and circular economy.
Bic Plastic Recycling: Unraveling the Mystery of Its Sustainability
You may want to see also
Frequently asked questions
Plastic recycling in the automotive industry involves a series of steps to process and reuse plastic components. It begins with collecting and sorting the plastic waste, which can include various types of polymers used in car manufacturing, such as ABS (acrylonitrile butadiene styrene), polypropylene, and polycarbonate. The collected plastic is then cleaned and shredded to reduce its size, making it easier to process. Next, the shredded plastic is sorted by type and color to ensure proper recycling. The sorted plastic is melted and formed into pellets, which can be used as raw materials for manufacturing new car parts or other products.
Not all plastics used in automobiles are recyclable in the same way. The automotive industry utilizes various types of plastics, and their recyclability depends on the specific polymer and manufacturing process. For example, ABS, a common plastic in car interiors and exteriors, is often recyclable through traditional recycling methods. However, some plastics, like certain types of polycarbonate or composite materials, may require specialized recycling processes due to their unique chemical structures or mixed material compositions. It's important to work with specialized recycling facilities that can handle these specific plastics to ensure proper recycling.
As an individual, you can play a significant role in promoting the recycling of plastic in cars. Firstly, ensure that you properly dispose of any plastic waste from your vehicle, such as old interior components or packaging materials. Many automotive shops and recycling centers accept these items for recycling. Additionally, when purchasing a new car, inquire about the manufacturer's recycling programs and policies. Some car manufacturers offer take-back programs for end-of-life vehicles, ensuring that the plastic and other materials are recycled responsibly. You can also support initiatives that focus on sustainable automotive materials and encourage the use of recyclable plastics in vehicle production.