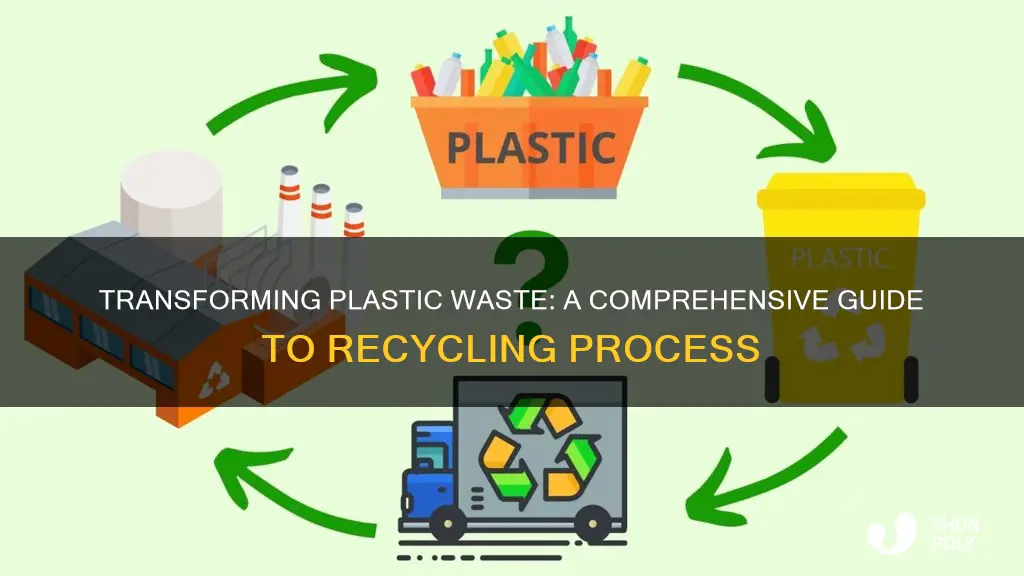
Plastic recycling is a crucial process to address the growing plastic waste crisis. It involves transforming used plastic items into new products, reducing the demand for virgin plastic production and minimizing environmental impact. The recycling process typically begins with the collection of plastic waste, which is then sorted based on its type and color. After sorting, the plastic is cleaned and shredded into small pieces called flakes. These flakes are further processed through a series of steps, including washing, drying, and melting, to create a raw material known as resin. The resin is then used to manufacture new products, such as bottles, containers, and even clothing, through a process called pelletizing. This step-by-step process ensures that plastic waste is given a new life, contributing to a more sustainable and circular economy.
What You'll Learn
- Collection: Plastic waste is gathered from various sources, including recycling bins and collection centers
- Sorting: Materials are sorted by type (PET, HDPE, etc.) using mechanical and manual methods
- Cleaning: Items are cleaned to remove contaminants and non-plastic materials
- Shredding/Grinding: Plastic is broken down into small pieces or flakes
- Melting/Reforming: The plastic flakes are melted and reformed into new products
Collection: Plastic waste is gathered from various sources, including recycling bins and collection centers
The collection of plastic waste is a crucial initial step in the recycling process, and it involves a systematic approach to ensure that plastic materials are properly sorted and prepared for recycling. This process begins with the placement of designated recycling bins in various locations, such as homes, offices, schools, and public spaces. These bins are typically color-coded or labeled to indicate the types of plastics they can accept, such as PET (polyethylene terephthalate) for beverage bottles or HDPE (high-density polyethylene) for milk jugs. By providing clear guidelines, residents and businesses are encouraged to separate their plastic waste accordingly, making the collection process more efficient.
Collection centers, also known as material recovery facilities (MRFs), play a vital role in the recycling chain. These centers are equipped with advanced machinery and trained personnel to sort and process the collected plastic waste. When plastic waste arrives at these facilities, it undergoes a series of processes to separate different types of plastics. This separation is essential because not all plastics are recyclable in the same way, and some may have different chemical compositions that require specific recycling methods.
At the collection center, the plastic waste is first sorted by type using various techniques. One common method is manual sorting, where workers carefully examine each item and separate it based on its material. For example, they might identify PET bottles by their unique shape and color, while HDPE containers are recognized by their rigid structure. Advanced MRFs also utilize optical sorters, which use light sensors to differentiate between different types of plastics based on their color and transparency. This automated process increases efficiency and reduces the risk of human error.
After sorting, the plastic waste is further processed to ensure it meets the quality standards required for recycling. This may involve additional steps such as cleaning, shredding, or granulating the plastic to prepare it for the next phase of the recycling process. The goal is to create a consistent and high-quality feedstock that can be used to manufacture new products.
In summary, the collection phase of plastic recycling is a critical step that relies on proper waste segregation and the use of specialized facilities. By implementing effective collection methods, including the provision of recycling bins and the operation of collection centers, the recycling process can begin, ultimately leading to the transformation of plastic waste into valuable resources for new product creation.
Unraveling the Mystery: Can Plastic Shower Curtains Be Recycled?
You may want to see also
Sorting: Materials are sorted by type (PET, HDPE, etc.) using mechanical and manual methods
The initial step in the plastic recycling process is sorting, a crucial phase that ensures the efficiency and quality of the recycling stream. This process involves the careful separation of different types of plastics, each with its unique properties and recycling methods. The primary goal is to group plastics by their resin identification codes, commonly known as the Resin Identification Code (RIC) or the Plastic Resin Identification Symbol. These codes, typically found on the bottom of plastic containers, range from 1 to 7 and indicate the type of plastic used in the product.
Mechanical sorting is often the first line of defense in this process. It employs various techniques to separate plastics based on their physical characteristics. One common method is air classification, where plastic materials are sorted using air currents. This technique is particularly effective for larger plastic items like bottles and containers. The materials are fed into a system where air is blown at different angles, causing the plastics to separate based on their density and size. For instance, PET (polyethylene terephthalate) bottles, known for their lightweight and clarity, tend to float and are separated from denser materials like HDPE (high-density polyethylene) containers.
Conveyor belts and vibratory screens are also utilized in mechanical sorting. Conveyor belts transport plastic items along a series of belts with varying angles and speeds, allowing for the separation of different plastics. Vibratory screens, on the other hand, use mechanical vibrations to separate materials based on their size and shape. These mechanical methods are highly efficient and can process large volumes of plastic waste quickly.
However, mechanical sorting alone may not be sufficient to achieve a high level of purity in the recycling stream. This is where manual sorting comes into play. Manual sorting involves human operators who carefully examine and separate plastics based on their visual appearance and feel. This method is particularly useful for identifying and removing contaminants, such as non-plastic items or heavily soiled materials, that might have been missed by mechanical processes. Trained workers can also identify specific types of plastics, like PET and HDPE, by their unique characteristics, ensuring they are directed to the appropriate recycling streams.
The combination of mechanical and manual sorting ensures a more comprehensive and accurate separation of plastics. This step is vital as it sets the foundation for the subsequent stages of recycling, where different types of plastics are processed and transformed into new products. By sorting plastics by type, the recycling process becomes more efficient, cost-effective, and environmentally friendly, contributing to a more sustainable approach to waste management.
Sustainable Building: Top Sources for Recycled Plastic Bricks
You may want to see also
Cleaning: Items are cleaned to remove contaminants and non-plastic materials
The cleaning process is a crucial step in plastic recycling as it ensures the purity and quality of the recycled material. When plastic items are collected, they often contain various contaminants and non-plastic materials that need to be removed to facilitate the recycling process. This step is essential to ensure the final recycled product meets the required standards and can be used for its intended purpose.
The cleaning process typically begins with sorting and categorizing the plastic items. Different types of plastics have distinct properties and melting points, so they need to be separated accordingly. This initial sorting helps in identifying and removing non-plastic materials that are often mixed with the plastic waste. For example, a plastic bottle might contain a metal cap, paper labels, or food residue, all of which need to be removed before recycling.
One common method of cleaning is washing the plastic items with water and detergents. This process helps to remove dirt, grease, and other surface contaminants. The use of water and detergents is carefully controlled to ensure that no harmful chemicals remain on the plastic, which could affect its quality during recycling. After washing, the plastic items are often dried to remove excess moisture, ensuring they are ready for the next stage of the recycling process.
In some cases, more specialized cleaning techniques are employed. For instance, plastic items with food residue or grease might require steam cleaning or high-pressure water jets to ensure thorough cleaning. This is especially important for plastics used in food packaging to prevent any contamination. Advanced recycling facilities might also use infrared or ultraviolet light to identify and remove non-plastic materials, such as labels or stickers, from the plastic items.
After cleaning, the plastic items are often inspected to ensure they meet the required standards. This inspection helps to identify any remaining contaminants or damage that could affect the recycling process. Once cleaned and inspected, the plastic items are ready for the next step, which is typically shredding or granulating to create small, uniform pieces of plastic that can be used in the production of new products.
Unraveling the Mystery: Can Plastic Straws Be Recycled?
You may want to see also
Shredding/Grinding: Plastic is broken down into small pieces or flakes
The process of recycling plastic begins with the collection and sorting of plastic materials. Once sorted, the plastic is then shredded or ground into small pieces or flakes. This initial step is crucial as it prepares the plastic for further processing and helps to reduce its volume, making it easier to handle and transport.
Shredding and grinding are mechanical processes that involve breaking down the plastic into smaller fragments. The shredded plastic can be in the form of pellets, flakes, or even small, uniform pieces, depending on the desired end product. This step is often performed using specialized machinery designed for plastic recycling. For example, single-shaft shredders are commonly used to reduce the size of plastic items, such as bottles or containers, into larger flakes. These flakes are then further processed to create a more uniform product.
Grinding, on the other hand, involves using a more precise and controlled process to create smaller, more consistent pieces. This method is often used for creating fine plastic powders or granulates. The ground plastic can be further sorted and classified based on its type and color, ensuring that the recycled material meets the required standards. This step is essential to ensure that the recycled plastic can be used in various applications, from manufacturing new products to creating composite materials.
The shredded or ground plastic is then cleaned to remove any contaminants, such as labels, caps, or other non-plastic materials. This cleaning process is crucial to ensure the quality and purity of the recycled plastic. After cleaning, the plastic flakes or pellets are often dried to remove any moisture, which can affect the recycling process and the final product.
Once the plastic has been shredded, ground, and cleaned, it is ready for the next stage of recycling, where it can be used to create new products, reducing the demand for virgin plastic and contributing to a more sustainable and circular economy. This initial step of shredding and grinding is a critical and often overlooked part of the plastic recycling process, as it sets the foundation for the subsequent stages of recycling and the creation of valuable, reusable materials.
Unraveling the Mystery: Can Plastic Plates Be Recycled?
You may want to see also
Melting/Reforming: The plastic flakes are melted and reformed into new products
The process of recycling plastic through melting and reforming is a crucial step in the journey of transforming used plastic materials into new products. This method is particularly effective for certain types of plastics, such as those commonly used in packaging, like PET (polyethylene terephthalate) and HDPE (high-density polyethylene). Here's a detailed breakdown of this recycling technique:
Collection and Sorting: The recycling journey begins with the collection of used plastic items, which are then sorted based on their type and color. This initial step is vital as it ensures that the plastic flakes obtained are of a consistent type, making the subsequent processes more efficient. For instance, PET bottles and HDPE milk jugs are often sorted separately due to their different melting points and properties.
Flaking and Cleaning: Once sorted, the plastic items are shredded or granulated to produce plastic flakes. These flakes are then cleaned to remove any contaminants, such as labels, caps, or other non-plastic materials. Cleaning is essential to ensure the purity of the final product and to prevent any unwanted odors or colors. Advanced cleaning techniques might include washing, drying, and using air classifiers to separate different types of plastics.
Melting and Reforming: The cleaned plastic flakes are then fed into a melting machine, which can vary in design depending on the specific recycling process. In this stage, the plastic is heated to its melting point, typically between 230°C and 290°C for PET and HDPE. The melted plastic is then purified further to remove any remaining impurities. This purification process might involve using filters or centrifugal separators to ensure a high-quality end product.
Molding and Shaping: After melting and purification, the plastic is ready for reformation. This step involves shaping the molten plastic into new products. The process can be customized to create various items, such as pellets, sheets, or specific shapes, depending on the intended application. For instance, the reformed plastic can be extruded into thin films for packaging or molded into containers for storage.
Quality Control and Testing: Throughout the melting and reforming process, quality control measures are essential. Samples of the reformed plastic are tested to ensure they meet the required standards for strength, durability, and appearance. This step is critical to guarantee that the recycled plastic products are fit for their intended use and meet consumer expectations.
This method of recycling plastic is a sustainable approach to waste management, reducing the demand for virgin plastic production and minimizing the environmental impact of plastic waste. It showcases how innovative recycling processes can transform waste into valuable resources, contributing to a more circular economy.
Unlocking the Mystery: Can Hard Plastic Be Recycled?
You may want to see also
Frequently asked questions
Plastic recycling is a process that involves collecting, sorting, cleaning, and reprocessing plastic waste to create new products. It is an essential step towards reducing environmental pollution and promoting sustainability.
Before recycling, it's crucial to clean and sort plastic items. Rinse out any food residue, break down large items into smaller pieces, and separate different types of plastics (e.g., PET, HDPE) to ensure efficient processing.
Plastic recycling methods include mechanical recycling, where plastic is ground into flakes, washed, and then remolded into new products. Chemical recycling, on the other hand, breaks down plastics into their original monomers or building blocks, allowing for the creation of new materials.
One significant challenge is the lack of standardized recycling systems, making it difficult to collect and process plastic waste effectively. Additionally, some plastics are challenging to recycle due to their chemical composition, and contamination from non-plastic materials can also hinder the recycling process.