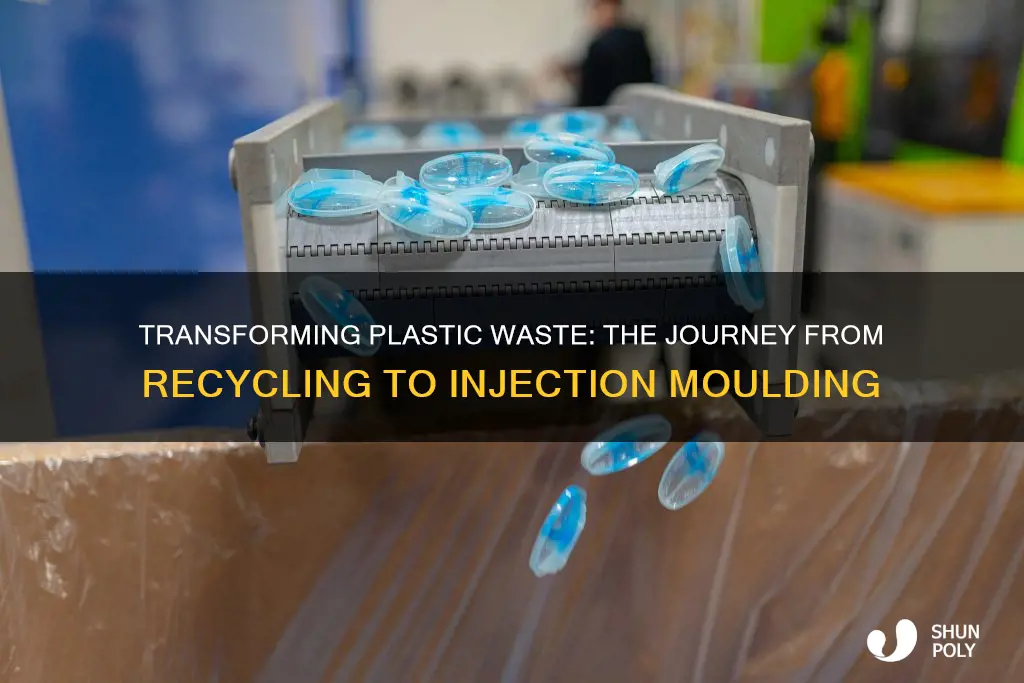
Plastic recycling is a crucial process in the journey towards sustainable manufacturing, and injection moulding is a key technique that utilizes recycled plastic materials to create a wide range of products. This paragraph will explore the intricate relationship between these two processes, detailing how plastic recycling plays a vital role in providing the raw materials necessary for injection moulding. It will also highlight the environmental benefits of this recycling loop, as it reduces waste, conserves resources, and minimizes the need for virgin plastic production, thereby contributing to a more sustainable and circular economy.
What You'll Learn
- Plastic Collection and Sorting: Efficient sorting methods ensure high-quality feedstock for injection molding
- Shredding and Granulating: Plastic waste is reduced to small, uniform particles for easy processing
- Melt and Injection: Molten plastic is injected into molds to create new products
- Mold Design and Optimization: Custom molds enhance production efficiency and product quality
- Post-Processing and Finishing: Additional steps like trimming and polishing complete the final product
Plastic Collection and Sorting: Efficient sorting methods ensure high-quality feedstock for injection molding
The process of transforming recycled plastic into usable injection-molded parts begins with efficient collection and sorting, which are critical steps in ensuring the quality and consistency of the feedstock. Plastic collection involves gathering used plastic items from various sources, including residential, commercial, and industrial areas. This step requires a well-organized system to capture a wide range of plastic types and colors, as different plastics have unique properties and applications in injection molding. A comprehensive collection program should aim to collect all common plastic types, such as PET (polyethylene terephthalate), HDPE (high-density polyethylene), LDPE (low-density polyethylene), PP (polypropylene), and PS (polystyrene), as well as various colors to meet specific customer requirements.
Once collected, the plastic waste undergoes sorting, which is a crucial process to separate different types of plastics and remove contaminants. Efficient sorting methods can significantly impact the quality of the final product. One common approach is manual sorting, where trained personnel visually inspect and separate plastics based on their type and color. This method is particularly useful for identifying and removing contaminants like food residue, labels, or non-plastic items. Manual sorting can be time-consuming but is essential for maintaining high standards. Advanced facilities may also employ automated sorting systems, utilizing near-infrared (NIR) spectroscopy or optical sorting technologies. NIR spectroscopy identifies plastic types by analyzing their unique molecular structures, while optical sorting uses cameras to distinguish between different colors and types based on visual characteristics.
Automated sorting systems offer increased speed and accuracy, especially when dealing with large volumes of plastic waste. These systems can sort plastics into multiple streams simultaneously, improving efficiency. However, it is important to note that automated sorting may require more initial investment and ongoing maintenance. Another efficient sorting technique is density separation, which takes advantage of the different densities of various plastics. This method uses water or air tables to separate plastics based on their buoyancy, allowing for the collection of specific plastic types. Density separation is particularly useful for separating PET and HDPE, which have distinct density characteristics.
Efficient sorting ensures that only high-quality plastics reach the injection molding stage, reducing the risk of defects and improving overall productivity. Proper sorting also helps in maintaining the consistency of the feedstock, which is crucial for achieving uniform and reliable injection-molded parts. By implementing effective collection and sorting methods, recycling facilities can produce a clean and diverse plastic stream, ready for the next stage of the recycling-to-injection molding process. This attention to detail in the initial stages significantly contributes to the success and sustainability of the entire recycling initiative.
Pepperell's Plastic Wrap Recycling: Unveiling the Green Initiative
You may want to see also
Shredding and Granulating: Plastic waste is reduced to small, uniform particles for easy processing
The process of transforming plastic waste into raw material for injection moulding begins with shredding and granulating, a crucial step in plastic recycling. This method involves reducing plastic waste into small, uniform particles, making it easier to handle and process. The shredded plastic is then granulated, creating a consistent and manageable material that can be further utilized in manufacturing.
Shredding is the initial step where plastic waste, such as post-consumer or post-industrial plastic scraps, is fed into a shredding machine. These machines, often equipped with sharp blades or rotating knives, cut the plastic into various sizes, typically ranging from 1 to 50 mm in diameter. The goal is to produce a uniform particle size, ensuring that the shredded plastic has a consistent texture and appearance. This uniformity is essential for the subsequent granulating process and the overall quality of the recycled material.
After shredding, the plastic flakes are then conveyed to the granulating stage. Granulating involves further processing the shredded plastic to create a granular form. This is typically done using a granulator, which can be a single-shaft or double-shaft type. The shredded plastic is fed into the granulator, where it is subjected to high-speed rotation, causing the plastic to melt and then solidify into small, uniform granules. The granulator's design and settings are crucial to achieving the desired particle size and quality.
The granulated plastic offers several advantages. Firstly, it provides a clean and consistent feedstock for the injection moulding process. The uniform particle size ensures that the plastic can be easily fed into the moulding machine without causing blockages or inconsistencies. Secondly, granulation allows for better control over the material's properties. By adjusting the granulating process, recyclers can influence the final product's characteristics, such as density, colour, and impact resistance.
Furthermore, granulating plastic waste enables the recycling industry to handle and store the material more efficiently. The granules can be easily transported and stored, making it convenient for distribution to manufacturers. This step is particularly important in large-scale recycling operations, where efficient processing and handling of materials are essential to meet production demands.
In summary, shredding and granulating are vital processes in plastic recycling, transforming waste into a valuable resource for injection moulding. These methods ensure the production of small, uniform particles, facilitating the recycling process and enabling the creation of high-quality recycled plastic products. By optimizing these steps, recyclers can contribute to a more sustainable and efficient circular economy in the plastic industry.
5 Simple Steps to Recycle Plastic: A Guide to Environmental Action
You may want to see also
Melt and Injection: Molten plastic is injected into molds to create new products
The process of transforming recycled plastic into new products through injection molding is a fascinating and sustainable manufacturing technique. It begins with the collection and sorting of plastic waste, ensuring that only suitable materials are selected for recycling. This initial step is crucial as it determines the quality and type of recycled plastic available for the production process. Once the plastic waste is sorted, it undergoes a series of processes to prepare it for injection molding.
The first stage involves cleaning and shredding the plastic waste. This step helps to remove any contaminants and ensures that the plastic is in a consistent and manageable form. After shredding, the plastic is typically dried to eliminate moisture, which can affect the quality of the final product. The dried plastic is then ground into a fine powder, creating a raw material known as 'regrind' or 'regrinded plastic'. This regrind can be used directly in the injection molding process or further processed to enhance its quality.
Next, the regrinded plastic is melted and prepared for injection. This is done in a specialized machine called an extruder, which heats the plastic to its melting point and mixes it thoroughly. The extruder ensures that the plastic is homogeneous and free from any residual contaminants. Once melted, the plastic is injected into a mold, which is a critical component of the process. The mold is designed with specific cavities or shapes to create the desired product, and it is here that the magic happens.
Injection molding involves forcing the molten plastic into the mold under high pressure. This pressure ensures that the plastic fills the entire mold cavity, taking the shape of the desired product. The mold is typically heated to maintain the plastic's pliability and to facilitate the removal of the finished product once it has cooled. After the plastic has been injected, the mold is closed, and the plastic is allowed to cool and solidify. This cooling process is carefully controlled to ensure the product's dimensional accuracy and integrity.
Once the plastic has cooled, the mold is opened, and the newly formed product is ejected. This product can then be further processed, assembled, or packaged as required. The beauty of this process lies in its ability to create a wide range of products, from simple household items to complex automotive parts, all from recycled plastic. Injection molding offers a sustainable and cost-effective solution for manufacturing, reducing the environmental impact of plastic production while also minimizing waste.
China's Plastic Recycling Trade: A Global Perspective
You may want to see also
Mold Design and Optimization: Custom molds enhance production efficiency and product quality
The process of recycling plastic and transforming it into injection-molded products requires careful mold design and optimization to ensure efficient production and high-quality end products. Custom molds play a pivotal role in this transformation, offering several advantages that contribute to overall production efficiency and product excellence.
One of the key benefits of custom mold design is the ability to tailor the mold to the specific requirements of the recycled plastic material. Different types of plastics have unique properties, and a well-designed mold can accommodate these variations. For instance, some plastics may have a higher viscosity, requiring specific cooling systems and gating strategies to ensure proper filling and solidification. Mold designers can optimize the geometry of the mold, including the cavity, core, and runner systems, to match the plastic's flow characteristics, thus minimizing defects and maximizing material utilization.
Optimization of the mold's cooling system is another critical aspect. Efficient cooling is essential to control the cooling rate of the plastic, which directly impacts the dimensional accuracy and surface finish of the molded part. Custom molds can incorporate advanced cooling techniques such as direct cooling channels, forced air cooling, or even liquid cooling, depending on the specific plastic and production requirements. By precisely managing the cooling process, manufacturers can reduce warping, improve dimensional stability, and enhance the overall quality of the injection-molded products.
Furthermore, mold design considerations extend to the choice of materials and surface treatments. Custom molds can be fabricated using high-quality steel alloys or even advanced composite materials, ensuring durability and longevity, especially in high-volume production. Surface treatments, such as electroplating or PVD coatings, can be applied to the mold's cavity to improve release characteristics, reduce wear, and enhance the surface finish of the molded parts. These design choices contribute to a more efficient production process and a consistent, high-quality product.
In the context of plastic recycling, custom molds also enable the implementation of specialized features. For example, incorporating vents, vents, or air-assisted gates can help control the flow of plastic and reduce the formation of voids or sink marks. These design elements are particularly important when dealing with recycled materials that may have varying levels of contaminants or additives. By optimizing the mold design, manufacturers can ensure that the recycled plastic is processed effectively, resulting in a consistent and reliable product.
In summary, custom mold design and optimization are essential components of the plastic recycling to injection molding process. By tailoring the mold to the specific characteristics of recycled plastic, manufacturers can achieve improved production efficiency, enhanced product quality, and better material utilization. This level of customization allows for the creation of high-performance, durable injection-molded products while contributing to the sustainability and economic viability of the recycling industry.
Nevada's Plastic Recycling: A Green Revolution or a Misstep?
You may want to see also
Post-Processing and Finishing: Additional steps like trimming and polishing complete the final product
The post-processing and finishing stage is crucial in transforming raw plastic parts into high-quality, market-ready products. This phase involves several meticulous steps to ensure the final product meets the required specifications and aesthetics. One of the primary processes is trimming, which involves removing excess material from the molded parts. This is particularly important for intricate designs where precision is essential. For instance, in the case of a complex electronic enclosure, trimming ensures that all protruding parts are flush with the main body, creating a seamless and professional appearance. This process is often done using specialized tools like band saws or water jet cutters, ensuring clean and precise cuts.
After trimming, polishing becomes the next critical step. Polishing serves multiple purposes, including enhancing the surface finish, improving part functionality, and contributing to the overall visual appeal. The method of polishing depends on the specific requirements of the product. For smooth surfaces, a fine-grit sandpaper or abrasive belt can be used to create a uniform and glossy finish. In contrast, for parts with specific textures or patterns, a different approach might be necessary, such as using a polishing compound or a vibratory finishing process to achieve the desired surface characteristics.
Additionally, some products may require further finishing touches, such as assembly or additional treatments. For example, in the production of automotive components, the finished plastic parts might need to be assembled with other components, requiring precise alignment and secure fastening. Furthermore, depending on the application, additional processes like painting, plating, or coating might be introduced to enhance the product's durability, corrosion resistance, or aesthetic appeal. These finishing steps are essential to ensure the final product not only functions as intended but also meets the desired standards of quality and appearance.
In summary, post-processing and finishing are integral to the plastic recycling to injection molding process, ensuring that the final product is not just functional but also aesthetically pleasing and ready for its intended market. Each step, from trimming to polishing and beyond, contributes to the overall quality and marketability of the product, making it essential to pay close attention to these details during manufacturing.
The Surprising Truth: What Happens to Your Single Plastic Item?
You may want to see also
Frequently asked questions
Plastic recycling to injection moulding is a process that involves collecting, sorting, and processing plastic waste to create raw materials for manufacturing. It begins with the collection of plastic scraps, bottles, or other waste materials. These are then sorted based on the type of plastic (e.g., PET, HDPE, PVC) to ensure proper recycling. The sorted plastics are cleaned, shredded, or granulated to reduce their size and prepare them for the next step. The granulated plastic is heated and melted in an injection moulding machine, which then injects the molten plastic into a mould to create a desired shape. This process allows for the production of new products, such as containers, automotive parts, or consumer goods, from recycled plastic materials.
Plastic recycling plays a crucial role in environmental conservation. By recycling plastic, we can reduce the demand for virgin plastic production, which often relies on fossil fuels and energy-intensive processes. This helps decrease the extraction of natural resources and minimizes the carbon footprint associated with plastic manufacturing. Additionally, recycling plastic waste prevents it from ending up in landfills or polluting natural habitats. It also reduces the amount of plastic waste that can potentially harm wildlife and ecosystems. The process of recycling and reusing plastic contributes to a more sustainable approach to manufacturing, promoting a circular economy and reducing environmental degradation.
While plastic recycling to injection moulding offers numerous benefits, there are some challenges to consider. One major issue is the quality and consistency of recycled plastic. Not all plastics are easily recyclable, and some may contain contaminants or impurities that affect the final product's quality. Sorting and identifying different types of plastics accurately is essential to ensure proper recycling. Another challenge is the potential for downcycling, where the recycled material is of lower quality than the original, leading to a decrease in product durability over time. Additionally, the process requires specialized equipment and knowledge to handle the recycling and moulding techniques, which may increase production costs. Despite these challenges, advancements in technology and recycling methods are continuously being developed to overcome these limitations.