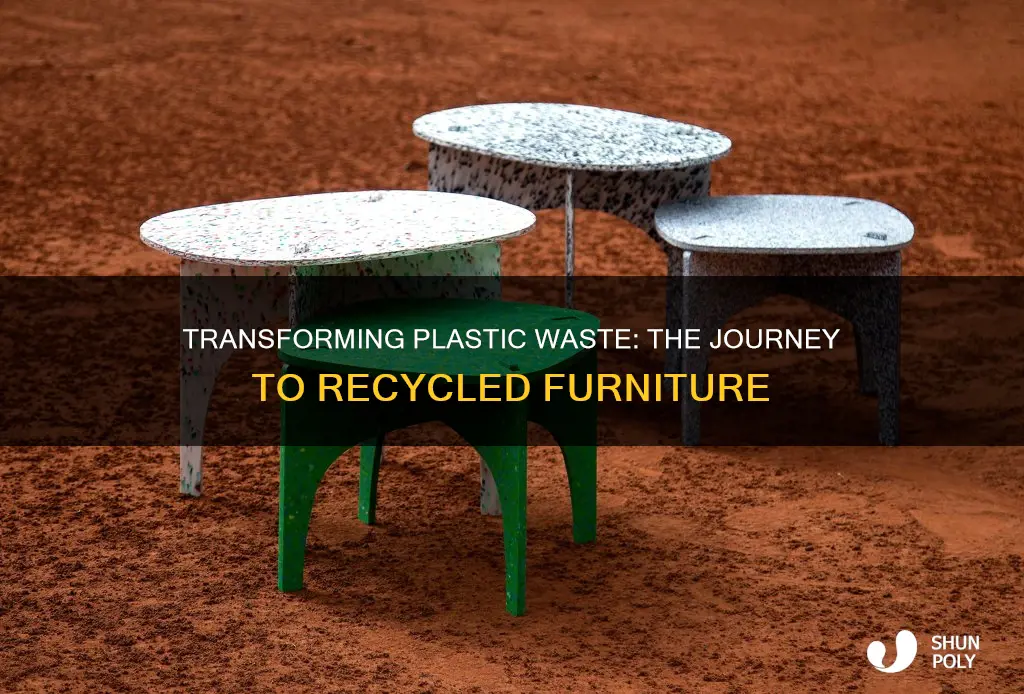
Recycled plastic furniture is an eco-friendly alternative to traditional outdoor seating and decor, offering durability and a unique aesthetic. The process of creating this furniture involves several steps. First, plastic waste, such as bottles and containers, is collected and sorted. These materials are then cleaned and shredded to break them down into smaller pieces. The shredded plastic is heated and mixed with other additives to form a molten mass, which is then extruded into a specific shape. This shaped plastic is then cooled and cut into the desired size and design. Finally, the plastic pieces are assembled using various methods, such as welding or screws, to create the final product. This entire process is an innovative way to give new life to plastic waste, reducing environmental impact and promoting sustainability.
What You'll Learn
- Collection: Sorting and cleaning plastic waste is the first step
- Shredding: Plastic is shredded into small pieces for processing
- Melting: The shredded plastic is melted into a molten state
- Molding: Molten plastic is shaped into furniture pieces using molds
- Finishing: Final touches like painting or upholstery are applied
Collection: Sorting and cleaning plastic waste is the first step
The process of transforming plastic waste into furniture begins with a crucial initial step: the collection and sorting of plastic materials. This phase is essential as it sets the foundation for the entire recycling process and ensures the quality of the final product.
Collection involves gathering plastic waste from various sources, including residential areas, commercial spaces, and industrial sites. It is important to encourage proper waste segregation at the source to facilitate efficient recycling. Residents and businesses should be educated on the importance of separating plastic items, such as bottles, containers, and packaging, from other waste streams. This can be achieved through community initiatives, educational programs, and the implementation of color-coded recycling bins.
Once collected, the plastic waste undergoes sorting, which is a critical process to ensure that only suitable materials are used for furniture production. Sorting can be done manually or through automated systems. Manual sorting involves trained personnel carefully examining each piece of plastic waste to identify different types and colors. Common types of plastic used in furniture include polypropylene (PP), high-density polyethylene (HDPE), and polystyrene (PS). Each type has unique properties, and proper identification is crucial for subsequent processing.
Automated sorting systems utilize advanced technologies such as infrared (IR) sensors and near-infrared (NIR) spectroscopy. These systems can quickly analyze the chemical composition of plastic items, allowing for efficient sorting. IR sensors detect the heat emitted by different plastics, while NIR spectroscopy identifies specific polymer types based on their unique molecular structures. By employing these technologies, recycling facilities can process large volumes of waste efficiently and accurately.
After sorting, the cleaned plastic waste is prepared for the next stage of recycling. This involves removing any contaminants, such as labels, caps, or non-plastic debris, to ensure the purity of the material. Cleaning processes may include washing, shredding, or melting the plastic to create a consistent and usable feedstock for furniture manufacturing. Proper sorting and cleaning are vital to producing durable and aesthetically pleasing recycled plastic furniture.
Unraveling the Mystery: Can Plastic Balloons Be Recycled?
You may want to see also
Shredding: Plastic is shredded into small pieces for processing
The process of recycling plastic into furniture begins with shredding, a crucial step in preparing the plastic for further processing. This initial stage involves breaking down larger plastic items or waste into smaller, manageable pieces. The shredding process is designed to reduce the size of the plastic material, making it easier to handle and process in subsequent steps.
Shredding machines, often equipped with sharp blades or rotating drums, are employed to cut, tear, or grind the plastic into tiny fragments. These machines can vary in size and capacity, depending on the scale of the recycling operation. For instance, industrial-scale shredders might be used to process large quantities of plastic waste from manufacturing or consumer sources. In contrast, smaller, more compact shredders could be utilized for local recycling initiatives or small-scale production.
The shredded plastic pieces are typically categorized by size, with finer shreds being used for certain applications and coarser shreds for others. This classification is essential as it determines the quality and functionality of the final product. Finer shreds might be more suitable for creating lightweight, flexible plastic materials, while coarser shreds could be used for structural elements or to add texture to the furniture.
After shredding, the plastic pieces are often sorted and cleaned to remove any contaminants or impurities. This step ensures that the recycled plastic is of high quality and meets the necessary standards for furniture production. The cleaning process might involve washing the shredded plastic to remove any residual dirt or debris, followed by drying to prevent moisture-related issues.
Once the shredded plastic is processed and cleaned, it can be further transformed into various forms, such as pellets, flakes, or sheets, depending on the desired application. These processed plastic materials can then be utilized in the manufacturing of recycled plastic furniture, contributing to a more sustainable and environmentally friendly approach to furniture production.
Bellevue's Plastic Recycling: Unveiling the 5-Step Process
You may want to see also
Melting: The shredded plastic is melted into a molten state
The process of transforming recycled plastic into furniture begins with the collection and sorting of plastic waste. Once sorted, the plastic is shredded into small pieces, ensuring a consistent size for the next stage. This step is crucial as it prepares the plastic for the melting process, where it will be transformed into a usable material.
Melting is a critical phase in the production of recycled plastic furniture. The shredded plastic is fed into a specialized machine, often a plastic granulator or a single-screw extruder. These machines are designed to heat the plastic to its melting point, typically around 200-250 degrees Celsius, depending on the type of plastic. The heat softens the plastic, allowing it to flow and take on a molten state. This molten plastic is then extruded through a die, which shapes it into long strands or pellets. The extrusion process is carefully controlled to ensure the plastic is not overheated, as this can lead to degradation and loss of quality.
During the melting process, it is essential to maintain a precise temperature and mixing to ensure the plastic's chemical structure remains intact. This is a delicate step as it requires expertise to avoid burning or under-melting the plastic. Once melted, the plastic is often cooled and then cut into uniform sizes, creating a raw material ready for furniture production. This molten state is crucial as it allows the plastic to be molded, formed, or extruded into various shapes and structures, which will later be used to create the legs, seats, and other components of the furniture.
The molten plastic can be further processed through a process called 'pelletizing', where it is cut into small, uniform pellets. These pellets are then used as a raw material for manufacturing furniture, ensuring consistency and ease of use in the production process. This step is often done in a controlled environment to maintain the quality and purity of the recycled plastic.
In summary, the melting process is a vital stage in recycling plastic into furniture. It requires precise temperature control and specialized machinery to transform shredded plastic into a usable, molten state. This molten plastic can then be shaped, formed, and used to create durable and sustainable furniture pieces.
Blosburg Recycling: Unraveling the Mystery of 5 & 6 Plastic Cups
You may want to see also
Molding: Molten plastic is shaped into furniture pieces using molds
The process of molding recycled plastic into furniture is a fascinating transformation that gives new life to waste materials. It begins with the collection and sorting of plastic waste, ensuring that only suitable materials are used. Once sorted, the plastic is cleaned and shredded into small pieces, a crucial step to ensure the plastic can be molten and shaped effectively.
The next stage involves the actual molding process. Molten plastic, derived from the shredded waste, is carefully heated to a specific temperature, making it pliable and ready for shaping. This molten state is essential as it allows the plastic to take the form of the mold, which is a crucial step in creating the desired furniture pieces. The mold itself is a carefully crafted tool, designed to give the plastic its final shape, whether it's a sleek chair, a sturdy table, or a decorative planter.
When the molten plastic is poured into the mold, it fills the cavity, taking on the mold's shape. This process requires precision and control to ensure the plastic sets correctly and retains the desired form. The mold is then placed in a controlled environment, often a specialized machine, to facilitate the cooling and solidification of the plastic. As the plastic cools, it hardens, and the mold is carefully removed, revealing the newly formed furniture piece.
This molding technique is highly versatile, allowing for the creation of a wide range of furniture styles and designs. From intricate patterns to smooth, modern shapes, the molding process can accommodate various aesthetic preferences. Additionally, the use of molds enables mass production, making recycled plastic furniture an accessible and sustainable option for consumers.
In summary, molding is a critical step in the journey of recycled plastic furniture, where waste is transformed into functional and stylish pieces. It showcases the ingenuity of recycling processes, combining science and art to create durable and environmentally friendly furniture solutions.
Can Plastic Champagne Flutes Be Recycled? Unveiling the Truth
You may want to see also
Finishing: Final touches like painting or upholstery are applied
The final stage of creating recycled plastic furniture involves meticulous finishing techniques to ensure durability and aesthetic appeal. Once the raw materials have been processed and the desired shape is achieved, the furniture pieces undergo a series of finishing processes.
Painting is a common and effective way to enhance the appearance of recycled plastic furniture. The surface of the plastic is typically cleaned and prepared to ensure proper adhesion. A primer is often applied to create a uniform base, followed by a choice of colors or finishes. Acrylic or latex paints are popular choices due to their durability and resistance to outdoor elements. The painting process may involve multiple coats to achieve the desired color intensity and coverage. Sanding between coats helps create a smooth finish and ensures the paint adheres well to the plastic surface.
Upholstery is another crucial aspect of finishing, especially for items like chairs, benches, and sofas. Recycled plastic furniture can be designed with removable or integrated seat and backrest panels. The upholstery process involves cutting and fitting fabric or synthetic materials onto these panels. The fabric is carefully stretched and secured, ensuring a tight and comfortable fit. This step requires precision and attention to detail to create a seamless and aesthetically pleasing appearance. Upholstery can be customized with various patterns, colors, and textures to suit individual preferences and design themes.
In some cases, additional treatments may be applied to enhance the furniture's performance. For outdoor furniture, a protective coating or sealant might be applied to the painted surface to prevent UV damage, fading, and weathering. This step ensures the longevity of the furniture, especially in harsh environmental conditions.
Finishing techniques also include quality control checks to ensure the furniture meets the desired standards. This involves inspecting the furniture for any defects, such as scratches, imperfections, or uneven paint application. Any necessary touch-ups or adjustments are made during this stage to guarantee a high-quality end product.
The finishing process is a critical phase in the manufacturing of recycled plastic furniture, as it determines the overall appearance, comfort, and durability of the final piece. Skilled artisans and craftsmen play a vital role in applying these final touches, ensuring that the furniture is not only environmentally friendly but also aesthetically pleasing and functional.
Unraveling the Mystery: Can Plastic Shower Curtains Be Recycled?
You may want to see also
Frequently asked questions
The process begins with collecting and sorting plastic waste, which is then cleaned and shredded into small pieces. These plastic flakes are melted and molded into the desired furniture shape using injection molding or blow molding techniques. The final product is a durable and eco-friendly piece of furniture.
Not all plastics are suitable for furniture production. Recycled plastic furniture is typically made from high-density polyethylene (HDPE) or polypropylene (PP) plastics, which are known for their strength and durability. These plastics are often derived from milk jugs, detergent bottles, and other household items, ensuring a sustainable source.
The recycling and manufacturing processes are designed to maintain high standards. The plastic is cleaned to remove contaminants, and the melting and molding stages are carefully controlled to ensure consistency. This results in furniture that is sturdy, weather-resistant, and free from any harmful chemicals.
Absolutely! By using recycled plastic, manufacturers reduce the demand for virgin plastic production, which often relies on fossil fuels. This process helps conserve natural resources, lowers carbon emissions, and diverts plastic waste from landfills or oceans, contributing to a more sustainable and eco-conscious approach to furniture making.