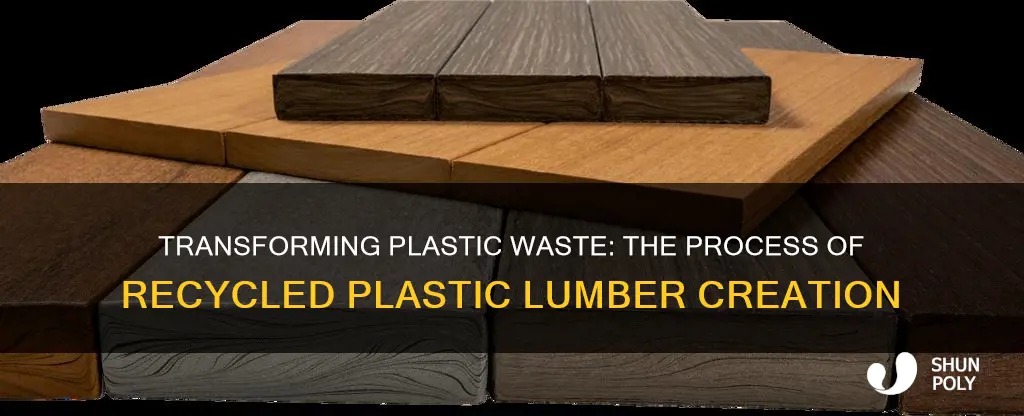
Recycled plastic lumber is an innovative and sustainable alternative to traditional wood, offering a unique solution to waste management and construction needs. This material is created through a process that transforms plastic waste into a durable and long-lasting building product. The process begins with the collection and sorting of various types of plastic, which are then cleaned and shredded to create a uniform raw material. This shredded plastic is heated and combined with other additives, such as colorants and stabilizers, to enhance its strength and durability. The mixture is then extruded into a lumber-like shape, allowing for the creation of planks, beams, and other structural elements. This method not only reduces the amount of plastic waste in landfills but also provides a lightweight, weather-resistant, and low-maintenance material suitable for various outdoor applications.
Characteristics | Values |
---|---|
Raw Materials | Recycled plastic waste, such as plastic bottles, containers, and film |
Process | 1. Collection and sorting of plastic waste 2. Cleaning and shredding the plastic 3. Melting and reforming the shredded plastic into pellets 4. Extrusion of the pellets into lumber shape 5. Curing and drying the lumber |
Properties | - High durability and weather resistance - Resistance to rot, insects, and moisture - Low maintenance - Lightweight and easy to install - Can be produced in various colors and textures |
Applications | Decking, fencing, landscaping, outdoor furniture, signage, and construction materials |
Environmental Benefits | Reduces plastic waste in landfills and oceans Decreases the demand for virgin plastic production Promotes sustainable and eco-friendly building practices |
Challenges | Initial high production costs Limited availability of consistent recycled plastic feedstock Potential for microplastic pollution during manufacturing |
What You'll Learn
- Plastic Collection: Sorting and cleaning plastic waste is crucial for the recycling process
- Shredding and Grinding: Plastic is shredded and ground into small pieces
- Melting and Molding: The plastic is melted and molded into lumber shapes
- Curing and Hardening: The molded plastic is cured and hardened for durability
- Finishing and Treatment: The lumber is treated and finished for various applications
Plastic Collection: Sorting and cleaning plastic waste is crucial for the recycling process
The initial step in the journey of recycled plastic lumber is the collection and sorting of plastic waste, a process that plays a pivotal role in ensuring the quality and effectiveness of the final product. This phase is critical as it sets the foundation for the entire recycling process, influencing the efficiency and sustainability of the entire operation.
When it comes to plastic collection, the goal is to gather a diverse range of plastic materials, ensuring they are free from contaminants. This involves a meticulous process of sorting, which is essential to separate different types of plastics. Common household plastics, such as PET (polyethylene terephthalate) from beverage bottles and HDPE (high-density polyethylene) from milk jugs, are easily identifiable and can be sorted accordingly. However, more complex materials like multi-layer packaging and mixed plastics require advanced sorting techniques, often involving specialized equipment and trained personnel.
Sorting plastic waste is a meticulous task that requires attention to detail. It involves categorizing plastics based on their type, color, and even the specific resin code, which is a numerical identifier found on the bottom of plastic containers. This coding system, ranging from 1 to 7, indicates the type of resin used, with each number corresponding to a specific plastic material. For instance, PET bottles are typically coded as 1, while HDPE containers are coded as 2. Accurate sorting ensures that the recycled plastic lumber will be made from homogeneous materials, enhancing its structural integrity and performance.
Once sorted, the plastic waste undergoes a cleaning process to remove any remaining contaminants, such as labels, caps, and other non-plastic materials. This step is crucial as it ensures the purity of the plastic, which is essential for the recycling process. Cleaning involves washing the sorted plastics to eliminate dirt and debris, followed by drying to remove any moisture. Advanced cleaning methods may include the use of industrial-grade detergents and water-washing systems to ensure a thorough clean.
The cleaning and sorting process is a critical aspect of waste management, as it directly impacts the quality of the recycled plastic lumber. By ensuring that the input materials are clean and properly sorted, the recycling process becomes more efficient, and the final product is more durable and versatile. This meticulous approach to plastic collection and sorting is a cornerstone of sustainable waste management, contributing to a circular economy where resources are reused and recycled effectively.
Unraveling the Mystery: Can Plastic Loofahs Be Recycled?
You may want to see also
Shredding and Grinding: Plastic is shredded and ground into small pieces
The process of transforming recycled plastic into lumber begins with the collection and sorting of plastic waste. Once sorted, the plastic is prepared for the next stage, which involves shredding and grinding. This initial step is crucial as it reduces the size of the plastic material, making it easier to handle and process further.
Shredding is the first mechanical process in this stage. Plastic waste is fed into a shredder, which is a machine designed to cut and tear the material into smaller pieces. The shredder's rotating blades or teeth break down the plastic into flakes or strips, significantly reducing its volume. This process is essential to prepare the plastic for further processing and to ensure it can be combined with other materials or processed into a usable form.
After shredding, the plastic flakes or strips are then ground into even smaller particles. Grinding is typically done using a hammer mill or a similar type of grinder. These machines use rotating blades to further reduce the size of the plastic pieces, creating a fine powder or a consistent-sized granule. The grinding process ensures that the plastic is in a manageable form, allowing for easier mixing and blending with other materials during the production of recycled plastic lumber.
The shredded and ground plastic is now in a state that can be further processed and combined with other ingredients to create the final product. This initial step of shredding and grinding is a critical phase in the recycling process, as it sets the foundation for the subsequent stages of manufacturing recycled plastic lumber. It requires precision and specialized equipment to ensure the plastic is reduced to the desired size and consistency.
Plastic Hanger Recycling: Where to Find the Right Drop-Off Points
You may want to see also
Melting and Molding: The plastic is melted and molded into lumber shapes
The process of transforming recycled plastic into lumber involves a fascinating technique known as melting and molding. This method is a crucial step in the creation of sustainable building materials, offering an eco-friendly alternative to traditional lumber. Here's a detailed breakdown of this process:
Once the plastic waste is collected and sorted, the journey towards recycled lumber begins. The selected plastic, often a blend of various types, is fed into a specialized machine designed for this purpose. These machines are typically large, industrial-grade melters, capable of handling substantial amounts of plastic. The initial step is to heat the plastic to its melting point, which varies depending on the type of plastic. For instance, high-density polyethylene (HDPE) melts at around 265°C (509°F), while polypropylene (PP) requires a slightly lower temperature of approximately 167°C (333°F). This melting process is crucial to ensure the plastic can be shaped and molded effectively.
As the plastic melts, it becomes a viscous liquid, often referred to as a 'plastic syrup'. This molten plastic is then carefully poured or fed into a molding machine. The molding process is an art and science, requiring precision and control. The molten plastic is injected into a mold, which is designed to mimic the desired shape of the lumber. These molds can vary in size and complexity, depending on the intended application of the recycled lumber. For example, a mold for outdoor furniture might have intricate details, while a mold for structural beams could be simpler and more uniform.
The injection of molten plastic into the mold is a precise operation. The pressure and temperature are carefully controlled to ensure the plastic fills the mold evenly and without defects. Once the mold is filled, it is typically cooled rapidly to solidify the plastic. This cooling process is critical to the success of the molding, as it determines the final dimensions and quality of the lumber. After cooling, the mold is opened, revealing the newly formed plastic lumber.
This method of recycling plastic into lumber offers several advantages. Firstly, it provides a durable and long-lasting alternative to traditional wood, making it suitable for various applications, including outdoor structures, landscaping, and even indoor design. Secondly, the process diverts plastic waste from landfills, reducing environmental impact. The melted and molded plastic lumber can be further processed and treated to enhance its performance and appearance, making it a versatile and sustainable building material.
Unraveling the Mystery: Can Plastic Drink Pouches Be Recycled?
You may want to see also
Curing and Hardening: The molded plastic is cured and hardened for durability
The process of transforming recycled plastic into lumber involves a crucial step: curing and hardening the molded plastic to ensure its durability and structural integrity. This phase is essential to enhance the material's strength and longevity, making it suitable for various construction and landscaping applications.
After the molding process, the plastic lumber is typically in a semi-solid or soft state. It requires a treatment to transform it into a rigid and durable product. Curing is a critical process that involves subjecting the molded plastic to controlled conditions, often involving heat and pressure. The goal is to initiate a chemical reaction that cross-links the polymer chains, making the material harder and more resilient. This process can be achieved through various methods, such as autoclaving, where the molded pieces are placed in a high-pressure steam environment, or through specialized curing agents that are mixed with the plastic during the molding stage.
Hardening, often used interchangeably with curing in this context, refers to the process of increasing the material's density and strength. It involves further processing the cured plastic to ensure it meets the desired specifications. This might include additional heating, cooling, or exposure to specific environmental conditions. For instance, the molded plastic lumber might be subjected to a series of temperature fluctuations to simulate real-world conditions, ensuring it can withstand various weather changes. This hardening process is vital to create a product that can resist impact, abrasion, and environmental factors, making it a reliable and long-lasting alternative to traditional lumber.
The duration and intensity of the curing and hardening processes can vary depending on the specific requirements of the project and the desired properties of the final product. Longer curing times and higher temperatures generally result in a more robust and durable plastic lumber. This step is a critical quality control measure, ensuring that the recycled plastic lumber meets industry standards and can perform as expected in outdoor applications.
In summary, the curing and hardening process is a transformative stage in the production of recycled plastic lumber, turning a malleable plastic material into a robust and long-lasting building material. This phase requires careful control of temperature, pressure, and environmental conditions to achieve the desired level of durability and structural strength.
Recycling Revolution: Alaska's Plastic Waste Management Journey
You may want to see also
Finishing and Treatment: The lumber is treated and finished for various applications
The process of transforming recycled plastic into lumber involves several crucial steps, and one of the most important aspects is the finishing and treatment process. This stage is essential to ensure the durability, appearance, and functionality of the recycled plastic lumber for various applications.
After the plastic is cleaned, sorted, and processed into flakes or pellets, it is time to shape it into lumber. This is typically done through a process called extrusion, where the plastic is heated and forced through a die to create the desired shape and size of the lumber. The resulting plastic lumber can be in various forms, such as planks, beams, or profiles, depending on the intended use.
Finishing and treatment processes are applied to enhance the performance and aesthetics of the recycled plastic lumber. One common treatment is a protective coating or finish, which can be achieved through several methods. One popular technique is the application of a UV-resistant polymer coating. This coating provides an additional layer of protection against the sun's harmful rays, preventing fading, discoloration, and degradation over time. It also adds a smooth, sleek surface, improving the lumber's appearance and making it more appealing for outdoor applications.
Another important treatment is the process of sanitization and disinfection. Recycled plastic lumber is often used in environments where hygiene is critical, such as in healthcare facilities, playgrounds, or outdoor furniture. To ensure a safe and clean product, the lumber undergoes sanitization treatments. This may involve chemical disinfection or the use of antimicrobial agents that inhibit the growth of bacteria, mold, and mildew. Such treatments are crucial in maintaining a healthy and safe environment, especially in public spaces.
Additionally, the lumber can be treated with wood preservatives to enhance its resistance to insects and moisture. This is particularly important for outdoor applications where the lumber will be exposed to the elements. By incorporating insecticide and fungicide treatments, the recycled plastic lumber becomes more durable and long-lasting, ensuring it can withstand various environmental conditions without deterioration. These finishing and treatment processes collectively contribute to the versatility and reliability of recycled plastic lumber, making it a sustainable and practical choice for a wide range of construction and decorative projects.
Fort Collins' Plastic Recycling: Unveiling the 6-Step Process
You may want to see also
Frequently asked questions
Recycled plastic lumber, also known as plastic wood, is created from post-consumer and post-industrial plastic waste. This waste is typically derived from items like milk jugs, detergent bottles, and other plastic containers that have served their original purpose and are no longer in use.
The recycling process begins with the collection of plastic waste. This waste is then sorted and cleaned to remove any contaminants. After cleaning, the plastic is shredded into small pieces, which are then melted and formed into pellets. These pellets are the raw material for manufacturing plastic lumber.
Recycled plastic lumber offers several advantages. Firstly, it reduces the amount of plastic waste that ends up in landfills or is incinerated. By reusing plastic, we can conserve natural resources and decrease the demand for virgin plastic production, which often relies on fossil fuels. Additionally, plastic lumber is durable, weather-resistant, and requires minimal maintenance, making it a popular choice for outdoor applications.
Yes, one of the key benefits of using recycled plastic is that it can be recycled again and again. Plastic lumber products can be ground back into their original form and used to create new lumber, ensuring a continuous cycle of recycling and reducing the environmental impact of plastic waste.