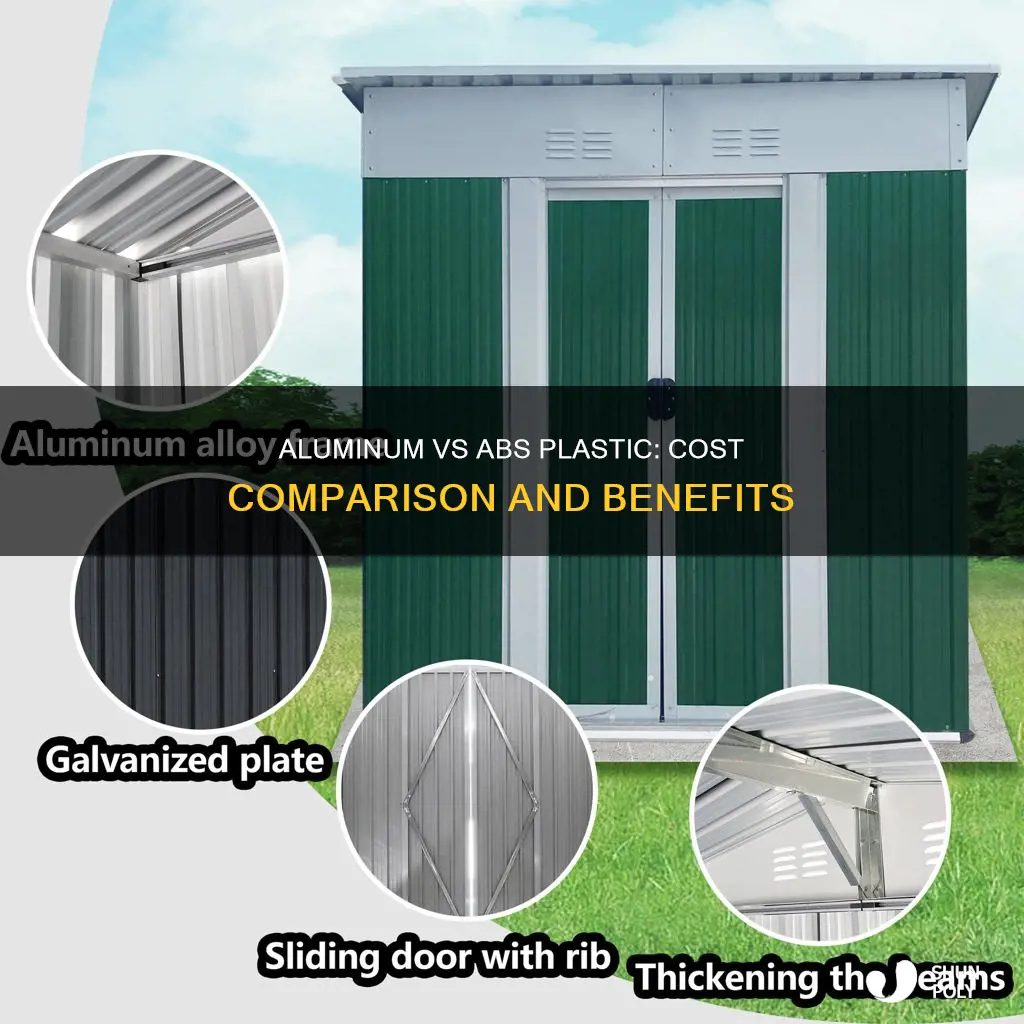
Aluminium and ABS plastic are both commonly used materials, but they differ in price. Aluminium is a metal that is often used in fabrication, but it can be expensive. ABS plastic, on the other hand, is a more affordable option that offers substantial cost benefits. It is also highly durable and has a lower density than aluminium, making it a lightweight alternative.
Characteristics | Values |
---|---|
Cost | ABS plastic is cheaper than aluminium |
Durability | ABS plastic is highly durable, resisting cracking and deforming over years of use |
Density | ABS plastic has a density of around 1.05 g/cm^3, which is less than aluminium |
Fabrication time | ABS plastic fabrication is 80% faster than CNC machining aluminium |
Part costs | ABS plastic parts cost 50-75% less than aluminium parts |
What You'll Learn
ABS plastic is a lot cheaper than aluminium
ABS plastic is highly durable, resisting cracking and deforming over years of use. Its yield strength and tensile strength properties allow it to withstand high loads and forces. It also demonstrates high impact resistance, absorbing shocks and impacts much better than materials like glass or brittle plastics.
ABS plastic has a density of around 1.05 g/cm^3, which translates to weight savings compared to metals like steel and aluminium. Redesigning parts to use lightweight yet strong ABS can benefit industries where reducing mass is critical, like automotive and aerospace.
For manufacturers looking to reduce expenses and improve profit margins, transitioning even partial production to ABS plastic can provide measurable cost reductions.
Plastic Cup Decomposition: The Long Goodbye
You may want to see also
ABS plastic is more durable than aluminium
Aluminium is a strong and durable metal that is used in many applications, but it is expensive to produce. ABS plastic is a cost-effective alternative to aluminium that offers substantial cost benefits. ABS plastic fabrication pricing is approximately 40% lower per part, and net shaping via injection moulding is 80% faster than CNC machining aluminium.
ABS plastic is highly durable, resisting cracking and deforming over years of use. Its yield strength and tensile strength properties allow it to withstand high loads and forces. ABS demonstrates high impact resistance, absorbing shocks and impacts much better than materials like glass or brittle plastics. It has a density of around 1.05 g/cm^3, which translates to weight savings compared to metals like steel and aluminium.
ABS plastic is commonly used in car interiors, such as dashboards and door panels, as well as in electronics, appliances, and toys. Its unique combination of strength, chemical resistance, and easy formability makes it a versatile choice for many industries.
While aluminium is a strong and durable metal, ABS plastic offers comparable strength and durability at a lower cost. Its resistance to cracking and deforming, high impact resistance, and weight savings make it a more durable alternative to aluminium in many applications.
Retainer Replacement: Cost of New Plastic Retainers
You may want to see also
ABS plastic is lighter than aluminium
Aluminium is a stronger and more durable material than ABS plastic, but it is also more expensive and heavier. ABS plastic is a more cost-effective option, with a 40% lower part fabrication pricing than aluminium. It is also a more lightweight material, with a density of around 1.05 g/cm^3, which can be beneficial for industries where reducing mass is critical, such as automotive and aerospace.
The weight difference between aluminium and ABS plastic can be significant, with plastic parts being more than six times lighter than their steel counterparts and approximately half the weight of aluminium parts. This weight difference can lead to cost reductions in fuel efficiency, maintenance, logistics, and installation.
One case study from a major car company found that switching from aluminium alloy to ABS plastic for interior trim components resulted in a 28% drop in manufacturing costs. The transition reduced part fabrication time from one hour to seven minutes and decreased scrap waste by 75%highly durable, resisting cracking and deforming over years of use. It has high impact resistance and can absorb shocks and impacts much better than materials like glass or brittle plastics.
Overall, while aluminium has its strengths, ABS plastic offers significant cost and weight savings, making it a more lightweight and cost-effective alternative.
Plastic Fencing: Cost-Effective Barrier Solution
You may want to see also
ABS plastic is faster to manufacture than aluminium
Aluminium is a metal that is commonly used in fabrication. However, it can be expensive to machine and often requires secondary finishing and coatings. ABS plastic, on the other hand, is a thermoplastic polymer that is widely used for machining purposes on an industrial scale. It is highly durable and can withstand high loads and forces, making it suitable for structural components. ABS plastic is also versatile and can be easily moulded and shaped through various services, such as injection moulding.
Injection moulding is the most common process used to manufacture ABS plastic parts. This process is suitable for producing high volumes of complex parts with precise dimensions and intricate details. It is much faster than CNC machining aluminium, with one case study showing that it reduced part fabrication time from 1 hour to just 7 minutes. ABS plastic is also 80% faster than CNC machining aluminium, according to the International Society for Plastics Engineers.
The recyclability of ABS plastic and the efficient injection techniques used in its manufacturing also help to minimise its environmental impact. ABS plastic has a lower density than aluminium, which translates to weight savings. This makes it a good choice for industries where reducing mass is critical, such as automotive and aerospace.
Overall, ABS plastic offers significant cost and time savings compared to aluminium, making it a more efficient and economical choice for manufacturers.
Plastic Surgeons' Work Hours: How Much is Too Much?
You may want to see also
ABS plastic is better for the environment than aluminium
Aluminium is widely known as the 'green metal' due to its sustainability and recyclability. However, ABS plastic is better for the environment than aluminium for several reasons. Firstly, ABS plastic is recyclable, which helps to minimise its environmental impact. In addition, the injection moulding process used to create ABS plastic parts is much faster than the subtractive fabrication process used for aluminium, reducing manufacturing times and costs. This technique also produces virtually no material scrap or waste, further reducing environmental impact.
ABS plastic is also more durable than aluminium, resisting cracking and deforming over years of use. Its yield strength and tensile strength properties allow it to withstand high loads and forces, making it ideal for applications where reducing mass is critical, such as in the automotive and aerospace industries.
Furthermore, ABS plastic has a lower density than aluminium, resulting in weight savings. This can lead to fuel savings in applications such as automotive and aerospace, where weight is a critical factor.
While aluminium is a strong and lightweight metal with excellent resistance to corrosion, warping and flexing, it still requires energy to produce and recycle. ABS plastic, on the other hand, can be recycled with minimal energy consumption, making it a more environmentally friendly choice.
Plastic Surgeons in Florida: High-Paying Career Options
You may want to see also
Frequently asked questions
A 2019 study found that ABS plastic part fabrication pricing was approximately 40% lower per part than aluminium.
ABS plastic is highly durable, resisting cracking and deforming over years of use. It also has a high impact resistance, absorbing shocks and impacts much better than materials like glass or brittle plastics.
Yes, ABS plastic has a density of around 1.05 g/cm^3, which is lower than that of aluminium. This makes it a good choice for industries where reducing mass is critical, such as automotive and aerospace.
Yes, ABS plastic can be used for 3D printing. It is a popular alternative to traditional manufacturing materials like metal and wood due to its durability, strength, and ease of fabrication at a lower overall cost.