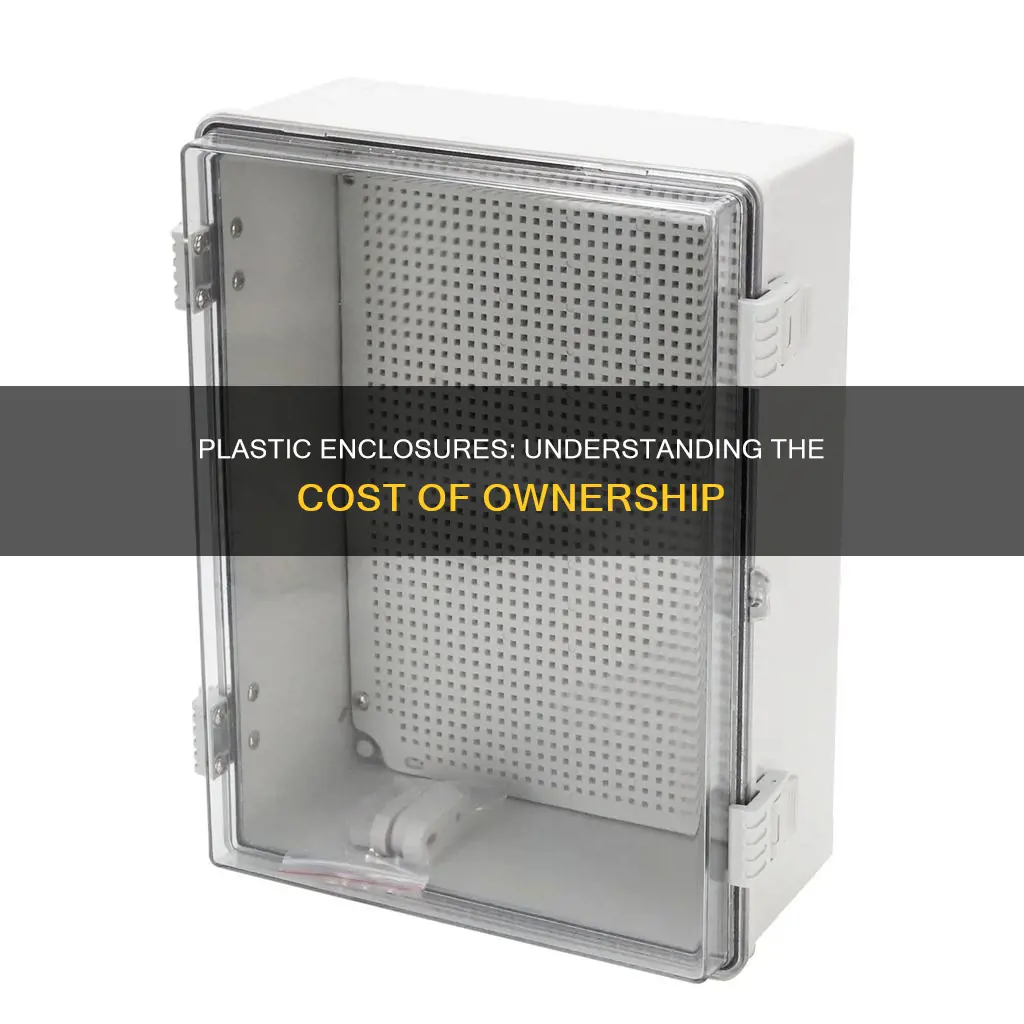
The cost of buying plastic enclosures depends on a number of factors, including the type of plastic used, the size of the enclosure, and whether it is custom-made or bought off-the-shelf. For example, the cost of materials for a custom plastic enclosure can be as low as $2 if ABS plastic is used, but the overall cost will depend on the complexity of the design and the manufacturing process. Off-the-shelf plastic enclosures may be more cost-effective for low-volume production, but custom enclosures can offer greater flexibility and a lower recurring cost for larger production runs.
Characteristics | Values |
---|---|
Material cost | $2 |
Cost of customisation | Double the moulded plastic case cost |
Cost of marking processes | Additional recurring cost |
Cost of standard enclosure | Recommended for low annual production volume |
What You'll Learn
Custom plastic enclosures can be costly and labour-intensive
There are also additional costs associated with marking and labelling custom plastic enclosures. These processes, which include hot stamping, pad printing and sublimation printing, can add recurring costs to the overall price. However, these costs can be minimised if the moulder sets up a marking work cell at the injection moulding press, allowing the cases to be marked during the slack time of the moulding cycle.
The cost of a custom plastic enclosure can also be affected by the choice of plastic material. For example, ABS plastic is relatively inexpensive and can be machined quickly, making it a cost-effective choice for custom enclosures. However, other types of plastic may be more expensive or require additional processing, increasing the overall cost.
It's worth noting that the cost of a custom plastic enclosure can be offset by the potential marketing benefits. A unique case can give a product a distinctive appearance that sets it apart from the competition and increases market appeal. This can result in a lower recurring cost advantage and make it more difficult for competitors to enter the market.
The Plastic Car: How Much of Your Vehicle is Polymer?
You may want to see also
Off-the-shelf plastic enclosures are recommended for low annual production volume
Custom plastic enclosures are a more costly proposition, as well as being labour-intensive and prone to reliability shortcomings in UL/CSA drop and impact tests. The custom approach does, however, allow the enclosure to fit the PCB assembly perfectly, with no wasted space or plastic material. Connector openings and PCB retention features are moulded-in, as is any text such as FCC and UL/CSA nomenclature (no labels). If your product requires future engineering changes or model variations, since you own the mould, it can be modified to suit.
The cost of a custom plastic enclosure can be nearly doubled with any of the above shielding processes. Although a moulded-in conductive fibre eliminates further downstream handling for a secondary painting or plating process, such moulded parts are limited to low-level attenuation and the plastic materials have a cost that makes the overall shielded case as nearly costly as a case with a painting or plating process.
There is also the variable cost of purchasing labels and applying those labels to the enclosure. If a contrasting colour is desired, a variety of marking processes are usually offered by the custom injection moulder. These include hot stamping, pad printing and sublimation printing. Although these marking processes bring with them additional recurring costs, that cost can be minimised if the moulder sets up a marking work cell at the injection moulding press so that the cases are marked during the slack time of the moulding cycle as opposed to handling the moulded parts and moving them to a different department or to a subcontractor; as is often the practice if a standard case supplier offers the marking capability on their off-the-shelf case.
What's the Safe Weight Limit for Plastic Drywall Anchors?
You may want to see also
ABS is a cheap material for plastic enclosures
The cost of plastic enclosures varies depending on the type of plastic used and the design of the enclosure.
ABS plastic is a cheap material for plastic enclosures. It is a thermoplastic polymer with impressive strength, impact resistance and temperature performance properties. ABS is also easy to machine and holds a good tolerance for a plastic. It is commonly used for indoor applications, including desktop electronics, and is sufficiently sturdy for use as indoor electrical junction box enclosures. ABS is also recyclable and can go through several processes of recycling without significant degradation.
However, ABS is not suitable for every use. It is not inherently UV stable without added stabilizers, so it is not usually a good choice for outdoor enclosures. It also has lower resistance to extreme conditions and industrial chemicals than other plastics, such as polycarbonate.
If you are looking for a custom plastic enclosure, there are a few things to consider. Custom enclosures can be more costly and labour-intensive, but they allow for a better fit with the product and can be modified to suit future engineering changes or model variations. Standard enclosures, on the other hand, are recommended if the anticipated annual production volume is low (less than 3,000-5,000) or if customer orders have not yet materialized.
Lip Filler Cost at Midsota Plastic: How Much?
You may want to see also
Painting or plating processes can be costly
The cost of plastic enclosures depends on the type of enclosure and the volume of production. If the anticipated annual production volume is low (less than 3,000-5,000), an off-the-shelf standard enclosure is recommended. Even if the marketing forecast is greater than this, but customer orders have not yet materialized, going into initial production with a standard enclosure and its greater recurring cost is a good business decision.
There are a variety of marking processes that can be used to add a contrasting colour to the enclosure, including hot stamping, pad printing and sublimation printing. These processes bring additional recurring costs, but this cost can be minimised if the moulder sets up a marking work cell at the injection moulding press so that the cases are marked during the slack time of the moulding cycle.
Custom enclosures can be costly and labour-intensive, as they require spacers, screws, soldered wire connections and machining to accommodate the PCB. However, they have the advantage of fitting the PCB assembly perfectly, with no wasted space or plastic material.
Plastic Shopping Carts: Weighing the Options
You may want to see also
Printing on plastic enclosures can be expensive
The cost of plastic enclosures depends on a number of factors, including the type of plastic used, the size and complexity of the enclosure, and whether it is custom-made or off-the-shelf.
Custom plastic enclosures can be more costly than off-the-shelf options, especially if they require additional features such as spacers, screws, soldered wire connections and machining to accommodate a PCB. However, custom enclosures can also offer a number of benefits, such as a unique appearance that can give a product greater market appeal.
The cost of plastic enclosures can also be affected by the choice of material. For example, ABS is a relatively inexpensive material that can be machined quickly and holds a good tolerance.
Overall, the cost of plastic enclosures can vary significantly depending on the specific requirements and features desired.
The World's Plastic Problem: An Annual Tragedy
You may want to see also
Frequently asked questions
It depends on the type of plastic enclosure you are looking for. Off-the-shelf plastic enclosures are recommended for low annual production volumes (less than 3,000-5,000). Custom plastic enclosures, on the other hand, can be more costly but offer a better fit and finish. The cost of custom plastic enclosures can vary depending on the design, materials used, and additional processes such as marking or shielding.
Custom plastic enclosures offer a glove-like fit to the PCB assembly, eliminating wasted space and plastic material. They also allow for future engineering changes or model variations as you own the mold.
Yes, there can be additional recurring costs associated with custom plastic enclosures, such as the cost of purchasing and applying labels, as well as marking processes such as hot stamping, pad printing, and sublimation printing.
The additional cost of marking processes can be minimized by setting up a marking work cell at the injection molding press, marking the cases during the slack time of the molding cycle.
Yes, the cost of plastic enclosures can also depend on the marketing and demand for the product. A unique case can provide a lower recurring cost advantage over competitors and increase market appeal.
Please note that the information provided is based on the assumption that 'plastic enclosures' refer to custom or standard plastic cases for utility products.