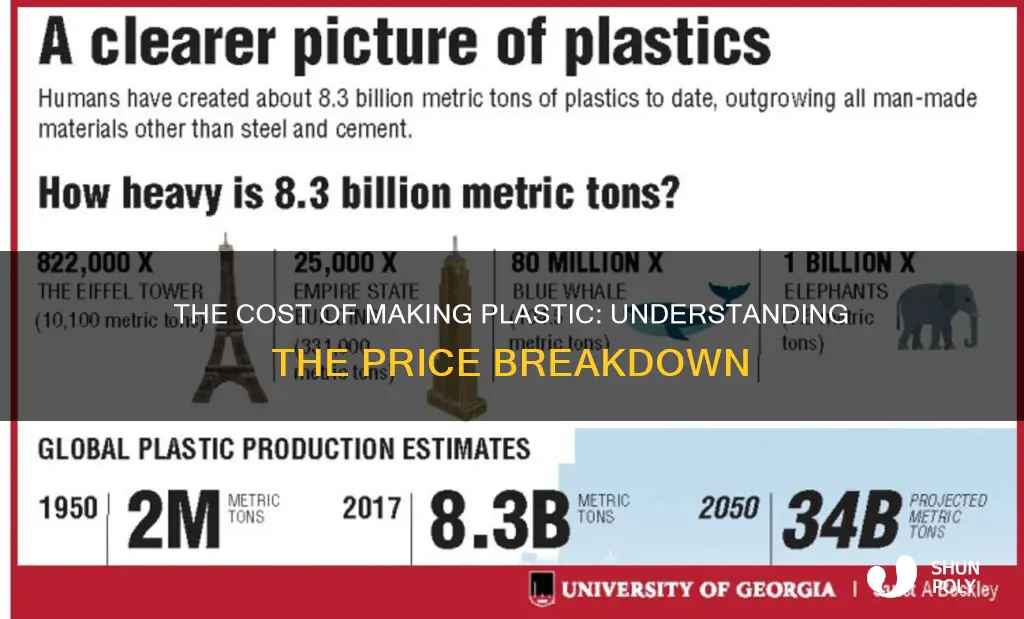
Plastic is a cheap material to produce, costing around $1 per kg. However, the true cost of plastic is more complex. The price of a plastic mould can vary from $1,000 to $5,000, depending on the size and type of plastic. The health and environmental costs of plastic are also significant, with endocrine-disrupting chemicals (EDCs) in plastics posing a serious threat to public health and costing the U.S. an estimated $250 billion in increased healthcare costs in 2018.
Characteristics | Values |
---|---|
Cost of plastic per kg | ~$1/kg |
Cost of a simple mould | $1,000 |
Cost of a small production run (500-1000 units) | $5,000 |
Cost of a unit | $5 |
What You'll Learn
Plastic packaging costs around $1/kg
The affordability of plastic packaging is largely due to the low upfront costs of the materials. A simple mould for plastic products can cost as little as $1,000, and the cost per unit for mass-produced plastic products can be very low, with some manufacturers quoting prices as low as $5 per unit for 1000 units.
However, the cost of plastic moulds can quickly escalate based on various factors, including the size and complexity of the mould. Additionally, the finished product will typically be comprised of multiple plastic components, further adding to the upfront cost.
Despite the low cost of plastic, there are growing concerns about the health and environmental impacts of plastic packaging. Endocrine-disrupting chemicals (EDCs) in plastics pose a serious threat to public health and cost the U.S. an estimated $250 billion in increased healthcare costs in 2018, according to research published in the Journal of the Endocrine Society.
Plastic's Costly Pound: Exploring the True Price of Plastic
You may want to see also
Injection moulding is costly upfront, but costs can be reimbursed by factories
Injection moulding can be costly upfront, but these costs can be reimbursed by factories depending on the production quantities milestones. A simple mould can cost as little as $1,000, but prices can quickly escalate based on a series of factors, including the size of the mould. The overall size of the mould will determine the cost, so it is important to consider the dimensions of the product. For example, a plastic product that is 30 cm by 30 cm will be more expensive to produce than a smaller product.
The cost of injection moulding can also depend on the number of units produced. For a small production run of 500-1000 units, the total cost is typically around $5000. However, for larger production runs, the cost per unit can be as low as $5. It is worth noting that the finished product will typically be comprised of multiple plastic components, further adding to the upfront cost.
To reduce costs, some manufacturers opt for aluminium moulds, which can be more cost-effective than other types of moulds. Additionally, factories may reimburse the upfront costs of injection moulding at certain production quantity milestones, so it is important to negotiate these terms during the negotiation stage.
While injection moulding can be costly upfront, there are ways to mitigate these costs, such as considering the size and dimensions of the product, the number of units produced, and negotiating with factories during the early stages of production.
The Cost of Plastic Retainers: How Much Do They Cost?
You may want to see also
The cost of a mould depends on its size
Plastic is marketed as an affordable material, costing around $1/kg. However, the cost of making plastic can vary depending on a number of factors, including the size of the mould required. A simple mould can cost as little as $1,000, but these prices can quickly escalate based on a series of factors, including the overall size of the mould. The larger the mould, the more expensive it will be to produce.
The cost of a mould is also driven by the number of plastic components in the finished product. A product that is made up of multiple plastic parts will require more moulds, which will increase the overall cost.
In addition, the cost of a mould can depend on the type of material used. For example, aluminium moulds are typically less expensive than moulds made from other materials.
Finally, the cost of a mould can be influenced by the production quantities. In some cases, the factory may reimburse the cost of the mould once certain production milestones are reached. Therefore, it is important to consider the overall production run when determining the cost of a mould.
Plastic Mold Cost: Understanding the Price of Molding
You may want to see also
A simple mould can cost $1,000
Plastic is marketed as an affordable material, costing around $1/kg. However, the true cost of plastic is much higher. Endocrine-disrupting chemicals (EDCs) in plastics pose a serious threat to public health and cost the U.S. an estimated $250 billion in increased healthcare costs in 2018.
The cost of making plastic products is driven by several factors, including the size of the mould and the number of components in the finished product. A simple mould can cost as little as $1,000, but these prices can quickly escalate. For example, a small plastic production run of 500-1000 units may cost around $5000 in total. The cost of the mould is driven in part by its overall size. Breaking a product down into sections and assembling the pieces as a secondary operation can help to reduce costs.
One way to keep costs down is to use an aluminium mould, which can be much cheaper than other types of moulds. For example, one manufacturer was able to produce 1000 units for about $5 each using an aluminium mould from a Chinese company.
Becoming a Plastic Surgeon: What's the Cost?
You may want to see also
The cost of plastic production can be reduced by using an aluminium mould
Plastic is marketed as an affordable material, with a price of around $1/kg. However, the true cost of plastic is more complex. For example, the health impact of endocrine-disrupting chemicals (EDCs) in plastics cost the US an estimated $250 billion in 2018.
The cost of plastic production is driven by a number of factors, including the size of the plastic and the number of components in the finished product. For example, a simple mould can cost as little as $1,000, but these prices can quickly escalate. The cost of the mould is driven in part by the overall size of the mould.
One way to reduce the cost of plastic production is to use an aluminium mould. Aluminium moulds can cost significantly less than other types of moulds. For example, one manufacturer was able to produce 1000 units for about $5 a unit using an aluminium mould, whereas other manufacturers quoted a much higher price.
Using an aluminium mould can also help to reduce the overall size of the mould, which can further reduce costs. By breaking a product down into sections, a smaller mould can be used, and the pieces can be assembled as a secondary operation. This can be a more cost-effective approach, especially for small production runs.
Retainer Replacement: Cost of New Plastic Retainers
You may want to see also
Frequently asked questions
It depends on the size of the plastic and the number of units being produced. A simple mould can cost as little as $1,000, but these prices can quickly escalate based on a number of factors. For example, a small plastic production run of 500-1000 units could cost $5,000 in total.
The cost per unit will depend on the total cost of production and the number of units being produced. For example, if the total cost of production is $5,000 and 1,000 units are being produced, the cost per unit would be $5.
The cost of making plastic is driven by a number of factors, including the size of the mould and the number of plastic components in the finished product. The cost may also be affected by the choice of material for the mould, with aluminium being a cheaper option.
Yes, there are potential hidden costs associated with the health and environmental impacts of plastic. Endocrine-disrupting chemicals (EDCs) in plastics pose a serious threat to public health and cost the U.S. an estimated $250 billion in increased healthcare costs in 2018.