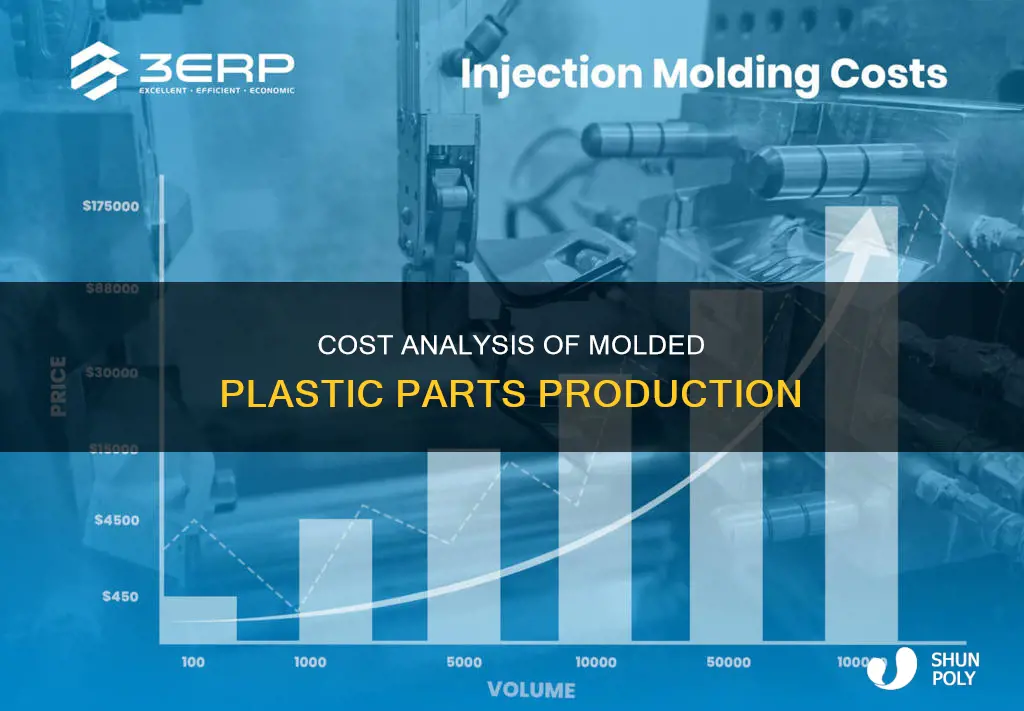
The cost of producing moulded plastic parts depends on a number of factors, including the type of plastic being used, the number of parts required, and the complexity of the mould design. The initial cost of building a mould can range from $1,000 to $80,000, depending on the size and complexity of the mould, with ongoing production costs of around $1 per set of parts. The type of plastic being used can also impact the cost, with high-performance plastics like PEEK requiring special equipment and being more expensive to produce.
Characteristics | Values |
---|---|
Cost of building a mold | $60,000-$80,000 |
Cost of production parts | $1 per set |
Cost of building a 12-cavity mold | $1,000-$2,000 |
Cost of building an 8-cavity mold | 5 million parts per year |
Cost of building a 32-cavity mold | 20 million parts per year |
Cost of mass manufacture | $10,000-$100,000 |
Cost of production per part | $6.85 |
What You'll Learn
The cost of building a mould
The material being moulded can significantly impact the cost of building a mould. For example, PEEK (polyetheretherketone) is a high-performance plastic that requires special heating equipment and is tough on injection moulds. As a result, moulding tools used for PEEK can only produce a few hundred parts before needing to be replaced, increasing the overall cost of mould production.
The number of cavities in a mould also affects the cost. A mould with more cavities can produce a higher volume of parts, but it comes at a higher upfront cost. For instance, an 8-cavity mould can provide approximately 5 million parts per year, while a 32-cavity mould can produce around 20 million parts annually. However, investing in a larger mould may not always be financially feasible or necessary, especially if the projected sales volume can be met with a smaller mould.
The required production volume is another critical factor in determining the cost of building a mould. If a high volume of parts is needed, it may be more cost-effective to invest in a larger mould with more cavities. On the other hand, if the production volume is low, a smaller mould with fewer cavities may be sufficient and more economical.
Additionally, the setup fee for moulding machines can be expensive, and manufacturers typically charge an hourly rate for the use of their equipment. This hourly rate is then converted into a cost per part to make it more meaningful to customers.
In terms of specific costs, building a mould can range from $1,000 to $2,000 for a small mould to $60,000 to $80,000 for a larger, more complex mould. Once the mould is built, the cost per part is relatively low, typically around $1 per set.
Starbucks Plastic Cups: How Much Do They Cost?
You may want to see also
The cost of the plastic material
The number of cavities in the mould also affects the price per part. A mould with more cavities can produce more parts per cycle, but it also increases the initial fabrication cost. For instance, an 8-cavity mould can provide approximately 5 million parts per year, while a 32-cavity mould can produce around 20 million parts annually. The choice of mould depends on the sales forecast and the expected demand for the plastic parts.
The setup fee for the moulding machine is another cost to consider. This fee covers the expenses incurred while the machine is offline and not producing parts. Manufacturers aim to minimise the number of setups as they are expensive and disruptive to the normal manufacturing process. They typically charge an hourly rate for the moulding machine, which is then converted to a cost per part for the customer.
Creating Plastic Silverware: Understanding the Cost of Production
You may want to see also
The cost of the machine
The second factor is the number of cavities in the mould. The more cavities, the higher the cost, as this increases the production capacity. For example, an 8-cavity mould will provide approximately 5 million parts per year, while a 32-cavity mould will provide approximately 20 million parts per year.
The third factor is the size and complexity of the part being moulded. Larger and more complex parts will require a larger and more expensive machine.
The fourth factor is the hourly rate of the machine. This is typically charged by the manufacturer and can vary depending on the machine's specifications and capabilities.
Finally, there may be additional costs associated with the setup and maintenance of the machine. For example, several pounds of plastic may be consumed to purge old material from the machine barrel, and the machine may be offline during setup, resulting in lost production time.
Taking all these factors into consideration, the cost of a moulding machine can range from a few thousand dollars to several hundred thousand dollars.
Antioxidants in Plastic: Costly Protection or Worth the Price?
You may want to see also
The cost of labour
Another factor that can affect the cost of labour is the complexity of the mould design. More complex moulds may require more skilled workers who are able to operate specialised equipment and ensure that the mould is produced to the exact specifications. This can increase the cost of labour, as these workers may command higher wages due to their specialised skills.
Additionally, the cost of labour can be affected by the volume of parts being produced. In some cases, it may be more cost-effective to produce a large volume of parts in a single run, as this can reduce the setup time and labour costs associated with each individual part. However, this may require a larger upfront investment in mould fabrication, which can be a significant expense.
Overall, the cost of labour is a critical component of the total cost of producing moulded plastic parts. By considering factors such as location, experience level, mould complexity, and production volume, manufacturers can optimise their labour costs and ensure a more competitive final product.
Car Bottom Plastic: How Much Protection Does It Offer?
You may want to see also
The cost of the number of cavities in the mould
The cost of producing moulded plastic parts depends on several factors, including the number of cavities in the mould. The more cavities a mould has, the higher the production cost and lead time. For example, an 8-cavity mould can produce approximately 5 million parts per year, while a 32-cavity mould can produce 20 million parts per year. However, investing in a larger mould with more cavities may not always be financially feasible or necessary, especially if it exceeds the forecasted demand.
The number of cavities in a mould is determined by the sales projections and the mould fabrication strategy. Manufacturers aim to strike a balance between meeting sales targets and minimising setup costs. Setup fees are typically charged to cover expenses, and customers may be averse to high setup charges. Therefore, manufacturers strive to reduce the number of setups as they are costly and disruptive to the normal production process.
The material being moulded also influences the overall cost. Certain high-performance plastics, such as PEEK (polyetheretherketone), require specialised heating equipment and are harder on injection moulds, leading to higher costs. In contrast, CNC machined plastic parts can reduce waste and lead times, resulting in faster and more cost-effective production compared to injection moulding.
The cost of moulding can vary significantly, ranging from $60,000 to $80,000 as a non-recurring expense to build the mould. Once the mould is built, the cost per part decreases, with some parts costing around $1 per set. The moulding machine's hourly rate is also a factor, but this is typically converted to a cost per part for customer clarity.
Ocean Plastic Crisis: Millions of Pounds and Counting
You may want to see also
Frequently asked questions
The cost of building a mould depends on the number of cavities. A 12-cavity mould costs $1,000-2,000, while an 8-cavity mould costs $60,000-80,000.
The cost of producing parts is usually around $1 per set. However, the cost per part will vary depending on the material being used. For example, using thermoplastic elastomers can add $.50 for a 100-gram part when compared to ABS.
The manufacturer typically has an hourly rate that they charge per moulding machine. This rate is then converted to a cost per part.