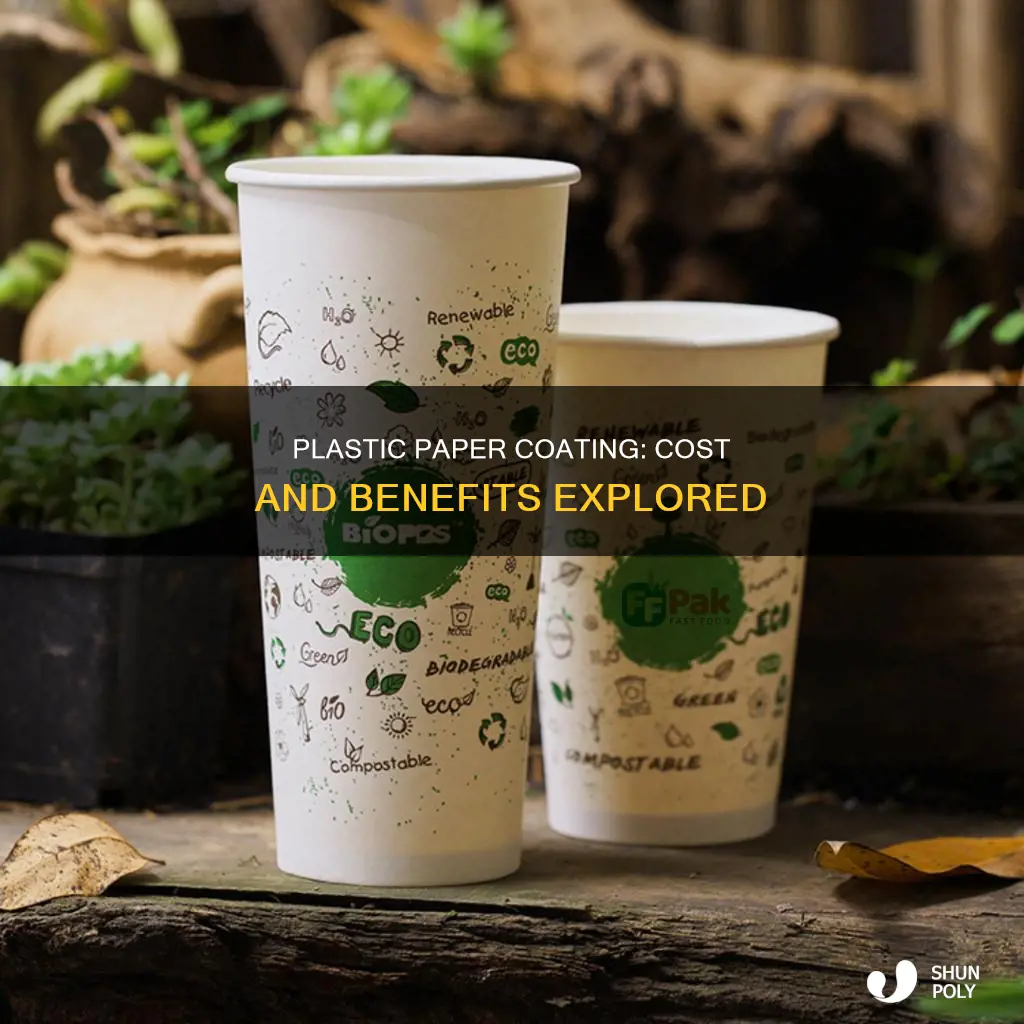
Plastic-coated paper is used to improve functions such as water resistance, tear strength, and the ability to be heat-sealed. It is most commonly used in the food and drink packaging industry, where it is used for single-use disposable food packaging. Plastic-coated paper is made by coating one side of the paper with a PE (polyethylene) layer, which provides an excellent barrier against water and grease. The plastic coating can also be made from polyolefin extrusion, silicone, or wax.
Characteristics | Values |
---|---|
Grammage | 100 to 230 g/m2 |
Coating weight | 20–40 g/m2/side |
Finish | Matte or glossy |
Composition | Polyethylene or polyolefin extrusion coating, silicone, or wax coating |
Alternative composition | Biopolymer coatings |
Function | Water resistance, tear strength, abrasion resistance, heat sealability |
Applications | Paper cups, photographic paper, food and drink packaging, liquid packaging board cartons, frozen food cartons |
Composition of liquid packaging board cartons | 74% paper, 22% plastic, 4% aluminium |
Composition of frozen food cartons | 80% paper, 20% plastic |
What You'll Learn
- Plastic-coated paper is used for single-use disposable food packaging
- The coating is usually polyethylene (LDPE) or polyolefin extrusion
- The paper can be customised with a printed logo
- It can also be reinforced with mesh to provide greater resistance to tearing
- Plastic-coated paper is used for printing magazines
Plastic-coated paper is used for single-use disposable food packaging
The most common applications of plastic-coated paper in the food industry are for liquid packaging boards for milk and juice cartons, and frozen food cartons. These cartons typically contain a combination of paper and plastic, with the percentage of each material varying depending on the specific application. For example, liquid packaging board cartons usually contain 74% paper, 22% plastic, and 4% aluminium, while frozen food cartons are made up of 80% paper and 20% plastic.
The plastic coating on the paper can be customised with a printed logo or design, and additional treatments such as mesh reinforcement and anti-corrosion treatments are also available to further enhance the functionality of the packaging.
While polyethylene (LDPE) is the most commonly used plastic coating in the packaging industry, there are also more sustainable alternatives available, such as biopolymer coatings, which can provide similar functionality in terms of water resistance, tear strength, and heat sealability. These sustainable alternatives are becoming increasingly popular as consumers and businesses seek more environmentally friendly options for food packaging.
Acetone's Power: Dissolving Plastic Completely
You may want to see also
The coating is usually polyethylene (LDPE) or polyolefin extrusion
Plastic-coated paper is a paper with one side coated with a PE (polyethylene) layer. This provides an excellent barrier against water and grease. The outer PE layer makes the packaging watertight and waterproof. The coating is usually polyethylene (LDPE) or polyolefin extrusion. Polyethylene is also used to make paper cups and photographic paper.
Polyethylene is the most common plastic coating in the packaging industry. It is used to improve functions such as water resistance, tear strength, abrasion resistance, and the ability to be heat-sealed. Frozen food cartons are usually made up of an 80% paper and 20% plastic combination. Liquid packaging board cartons typically contain 74% paper, 22% plastic, and 4% aluminium.
The plastic-coated paper can be customised with a printed logo of the customer. It is also available with mesh reinforcement to provide greater resistance to tearing. Plastic-coated paper can be supplied with VCI anti-corrosion treatment upon request.
Biopolymer coatings are available as more sustainable alternatives to common petrochemical coatings like low-density polyethylene (LDPE) or mylar.
Plastic Hangers: How Much Do They Weigh?
You may want to see also
The paper can be customised with a printed logo
Plastic-coated paper is a paper with one side coated with a PE (polyethylene) layer. This provides an excellent barrier against water and grease. The outer PE layer makes the packaging watertight and waterproof. The paper can be customised with a printed logo.
The plastic-coated paper can be customised with a printed logo of the customer's choice. This is a great way to add a personal touch to the paper and make it unique. The logo can be printed on the paper before or after the plastic coating is applied. If you choose to print the logo before the coating is applied, the ink may be covered by the plastic layer, depending on the type of coating used. If you choose to print the logo after the coating is applied, the ink will sit on top of the plastic layer and may be more susceptible to smudging or wear and tear.
There are a few different methods for printing a logo on plastic-coated paper. One common method is offset printing, where the ink is transferred from a plate to a rubber blanket and then to the paper. Another method is digital printing, where the ink is applied directly to the paper using a digital printer. Screen printing is also an option, where ink is pushed through a mesh screen onto the paper. The best method for printing a logo on plastic-coated paper will depend on the specific requirements of the project, such as the desired print quality, the quantity of prints needed, and the budget.
In addition to customising the paper with a printed logo, there are also other options for further customisation. For example, the paper can be supplied with mesh reinforcement to provide greater resistance to tearing. This is a great option for applications where the paper needs to be durable and withstand a lot of wear and tear. Another option is to add a VCI anti-corrosion treatment to the paper, which can help protect metal products from corrosion during storage or transport. This treatment can be applied upon request and is a great way to further customise the paper to meet specific needs.
Plastic Surgery: Female Surgeons' Salary Insights
You may want to see also
It can also be reinforced with mesh to provide greater resistance to tearing
Plastic-coated paper is used to improve functions such as water resistance, tear strength, and abrasion resistance. It is most commonly used in the food and drink packaging industry. The plastic coating is usually polyethylene (LDPE) or polyolefin extrusion coating, although biopolymer coatings are available as a more sustainable alternative.
The plastic-coated paper can be customised with a printed logo of the customer. It can also be reinforced with mesh to provide greater resistance to tearing. This is an optional extra that can be supplied upon request. The mesh reinforcement is ideal for packaging that needs to be particularly durable, such as cartons for frozen food.
The plastic coating can be applied to either smooth or crepe paper. The grammage varies from 100 to 230 g/m2. The paper is usually coated with a melted plastic layer, and some coatings are processed by UV curing for stability.
The most notable applications for plastic-coated paper are single-use disposable food packaging, such as liquid packaging board for milk and juice folding cartons.
Old Plastic Dolls: Worth a Fortune or Not?
You may want to see also
Plastic-coated paper is used for printing magazines
The most common method of coating paper is curtain coating. The paper is coated with a melted plastic layer. The top coat is a protective polymer to seal the print, provide scuff resistance, and sometimes gloss. Some coatings are processed by UV curing for stability.
Machine-finished coated paper (MFC) is commonly used for printing magazines. It has a basis weight of 48–80 g/m2.
Plastic-coated paper is also used for single-use disposable food packaging, such as liquid packaging board for milk and juice folding cartons. Frozen food cartons are usually made up of an 80% paper and 20% plastic combination.
Cost Analysis of Plastic Lenses: How Much Do They Cost?
You may want to see also
Frequently asked questions
The price of plastic-coated paper depends on the type of paper and the type of plastic coating. For example, polyethylene or polyolefin extrusion coating, silicone, and wax coating are all types of plastic coatings for paper.
Plastic-coated paper is used in the food and drink packaging industry, as it is water-resistant, tear-resistant and can be heat-sealed. It is also used for single-use disposable food packaging, such as milk and juice cartons.
Plastic-coated paper has several benefits, including improved water resistance, tear strength, and abrasion resistance. It can also be heat-sealed and is therefore useful for packaging liquids.
Other types of coated paper include art papers, which are triple-coated and have a matte or glossy finish. These are used for illustrated books, calendars and brochures. Plastic-coated paper, on the other hand, is coated with a layer of polyethylene (PE) or polyolefin, which provides an excellent barrier against water and grease.
Yes, biopolymer coatings are available as more sustainable alternatives to common petrochemical coatings like low-density polyethylene (LDPE). These coatings provide the same benefits as plastic coatings, such as water resistance and tear strength, but are made from renewable resources.