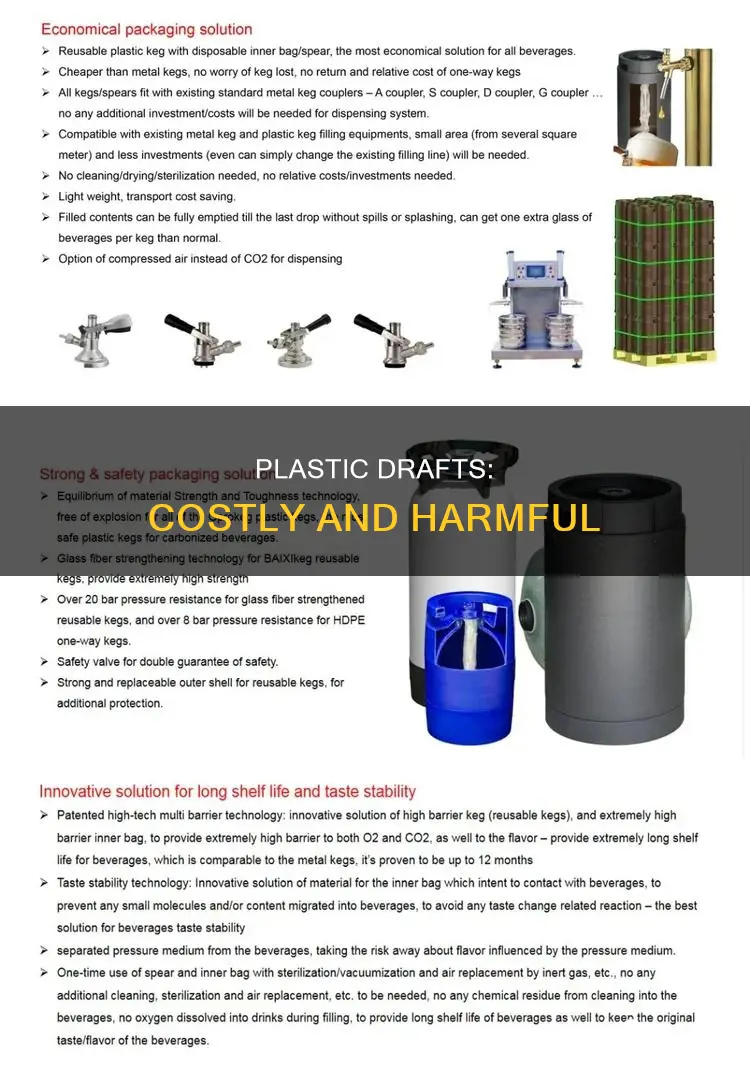
Draught-proofing is a simple and cost-effective way to improve the energy efficiency of your home. The cost of draught-proofing will depend on how much of your home you want to draught-proof and which areas you choose to target. Professional draught-proofing could cost around £250 for your whole house, but DIY draught-proofing is a cheaper option if you're happy to carry out the work yourself.
Characteristics | Values |
---|---|
Definition | Draft is the angle applied to the vertical walls of parts in injection moulding. |
Importance | Without draft, parts won't eject cleanly from the mould and are susceptible to damage. |
Benefits | Draft can decrease tool wear and reduce cooling times, both of which help to control costs. |
Draft Angle | There is no single draft angle that is adequate for all injection-moulded parts. Each part has its own unique requirements. |
General Rule of Thumb | Parts up to 2" long require 2° of draft. Anything longer than 2" should have an additional degree of draft for each inch of mould depth. |
Minimum Draft Angle | 0.5° on all vertical faces is strongly advised. |
Draft Angle for Shutoff | 3° is the minimum for a shutoff (metal sliding on metal). |
What You'll Learn
Draft angles in injection moulding
There is no single draft angle that is adequate for all injection-moulded parts. Each individual part has its own unique draft requirements. Generally, parts up to 2” long require 2° of draft. Anything longer than 2” should have an additional degree of draft for each inch of the mould depth. However, this is just a rule of thumb and there are exceptions. For instance, you may need as much as 5° of draft for a small part, and in some cases, you may be able to use as little as 1/2° of draft.
The amount of draft angle required depends on a number of factors, including wall thickness, material selection, ejection, shrink rates, finish/texture, wall depth, and manufacturing capabilities. It is recommended to apply as much draft angle as possible at the wall side. A general rule of thumb is 1 degree of draft per 1 inch of cavity depth, but that can change with the aforementioned factors. For example, 0.5 degrees on all vertical faces is strongly advised. 1 to 2 degrees works very well in most situations. 3 degrees is the minimum for a shutoff (metal sliding on metal).
Large parts require more draft than small parts. Thin-walled parts that are moulded at high pressures require more draft than parts moulded at lower injection pressures. As the plastic material cools, it shrinks and pulls away from cavities while gripping the core pins. Theoretically, core pins require more draft than cavities. The amount that a plastic material shrinks must be considered in selecting a suitable draft angle. Large draft angles and a smooth polish are required for parts moulded in strong, brittle, abrasive, and sticky materials.
Plastic Hangers: How Much Do They Weigh?
You may want to see also
Draft angle guidelines
There is no single draft angle that is ideal for all injection-moulded plastic parts. Each part has its own unique requirements, which are influenced by factors such as wall thickness, material selection, ejection, shrink rates, finish/texture, wall depth, and manufacturing capabilities.
As a general rule of thumb, it is recommended to apply 1 degree of draft for every 1 inch of cavity depth. However, this can vary depending on the specific requirements of the part. For instance, parts up to 2 inches long typically require 2 degrees of draft, while longer parts should have an additional degree of draft for each additional inch of mould depth.
When designing a part, it is important to apply as much draft angle as possible. While it may seem like a part would look or function better without any draft, there are very few instances where a perfectly straight, zero-degree draft angle is required. Even a small amount of draft can help to ensure the part ejects cleanly from the mould and is less susceptible to damage.
To ensure easy ejection of undamaged parts, it is important to maintain draft angle discipline throughout the design process. Draft angles can vary, but it is important to avoid parallel faces, as these can create difficulties in ejection. Additionally, it is recommended to minimise undercuts and bumped features, as these can become hang-up points and require expensive additional tooling.
Plastic Surgery: Who Pays for These Expensive Procedures?
You may want to see also
Factors influencing draft angle selection
There are many factors that influence the draft angle selection for plastic injection moulding. The general rule of thumb is 1 degree of draft per 1 inch of cavity depth, but this can change depending on other factors.
Firstly, the size of the part matters. Large parts require more draft than small parts. Parts up to 2 inches long require 2 degrees of draft, and anything longer should have an additional degree of draft for each inch of mould depth.
Secondly, the wall thickness and depth of the part are important. Thin-walled parts that are moulded at high pressures require more draft than parts moulded at lower injection pressures. The deeper the wall, the more draft is required.
Thirdly, the material used for the part affects the draft angle. The amount that a plastic material shrinks must be considered when selecting a draft angle. Large draft angles and a smooth polish are required for parts moulded in strong, brittle, abrasive, and sticky materials.
Finally, the manufacturing capabilities and design of the mould will also influence the draft angle selection. It is recommended to apply as much draft angle as possible at the wall side. A minimum of 3 degrees is required for a shutoff (metal sliding on metal).
It is important to note that there is no single draft angle that is ideal for all injection-moulded parts. Each part has its own unique requirements, and even a small amount of draft can help to avoid design flaws and ensure parts eject cleanly from the mould.
PLA Plastic: Affordable 3D Printing Material Cost Analysis
You may want to see also
Adequate draft angle
There is no single draft angle that is adequate for all injection-moulded parts. Each individual part has its own unique draft requirements. Generally, parts up to 2” long require 2° of draft. Anything longer than 2” should have an additional degree of draft for each inch of the mould depth. However, this is just a general rule of thumb, and in some instances, you may need as much as 5° of draft for even a small part, and in some cases, you may be able to use as little as 1/2° of draft.
Wall thickness, material selection, ejection, shrink rates, finish/texture, wall depth, and manufacturing capabilities will influence the draft angle selection. When designing a part or before mould design, apply as much draft angle as possible at the wall side. A general rule of thumb is 1 degree of draft per 1 inch of cavity depth, but that can change with the aforementioned factors. Try following these general guidelines: 0.5 degrees on all vertical faces is strongly advised. 1 to 2 degrees works very well in most situations. 3 degrees is the minimum for a shutoff (metal sliding on metal).
Large parts require more draft than small parts. Thin-walled parts that are moulded at high pressures require more draft than parts moulded at lower injection pressures. As the plastic material cools, it shrinks and pulls away from cavities while gripping the core pins. Theoretically, core pins require more draft than cavities. The amount that a plastic material shrinks must be considered in selecting a suitable draft angle. Large draft angles and a smooth polish are required for parts moulded in strong, brittle, abrasive, and sticky materials.
Plastic Pollution: Ocean Crisis
You may want to see also
Draft and texture in plastic injection moulding
There is no single draft angle that is adequate for all injection-moulded parts. Each part has its own unique requirements. Generally, parts up to 2 inches long require 2 degrees of draft. Anything longer than 2 inches should have an additional degree of draft for each inch of mould depth. However, this is just a rule of thumb. In some instances, you may need as much as 5 degrees of draft for a small part, and in others, you may be able to use as little as 0.5 degrees of draft.
Wall thickness, material selection, ejection, shrink rates, finish/texture, wall depth, and manufacturing capabilities will influence the draft angle selection. When designing a part or before mould design, apply as much draft angle as possible at the wall side. A general rule of thumb is 1 degree of draft per 1 inch of cavity depth, but that can change with the aforementioned factors. Try following these general guidelines: 0.5 degrees on all vertical faces is strongly advised. 1 to 2 degrees works very well in most situations. 3 degrees is the minimum for a shutoff (metal sliding on metal).
Large parts require more draft than small parts. Thin-walled parts that are moulded at high pressures require more draft than parts moulded at lower injection pressures. As the plastic material cools, it shrinks and pulls away from cavities while gripping the core pins. Theoretically, core pins require more draft than cavities. The amount that a plastic material shrinks must be considered in selecting a suitable draft angle. Large draft angles and a smooth polish are required for parts moulded in strong, brittle, abrasive, and sticky materials.
In injection moulding, draft is the angle that you apply to the vertical walls of parts. Without adding draft to your design, parts won’t eject cleanly from the mould and are susceptible to damage. Draft can also decrease tool wear and reduce cooling times, both of which help to control costs.
The First Plastic Lego Set: What Was the Cost?
You may want to see also
Frequently asked questions
Draught-proofing costs vary depending on how much of your home you want to draught-proof and which areas. Professional draught-proofing could cost around £250 for your whole house. DIY draught-proofing will be cheaper.
Professional draught-proofing is likely to save more energy because the installer will know exactly the right materials to use and where to use them. However, some homes, especially older homes with single glazing, will be more difficult to draught-proof.
This will depend on the size of the room and the materials used. It is likely to be cheaper than professional draught-proofing for your whole house, which costs around £250.
Draught-proofing can save energy and money on your energy bills. However, it is important to ensure that air can still flow in and out of your house to keep it fresh, dry and healthy.