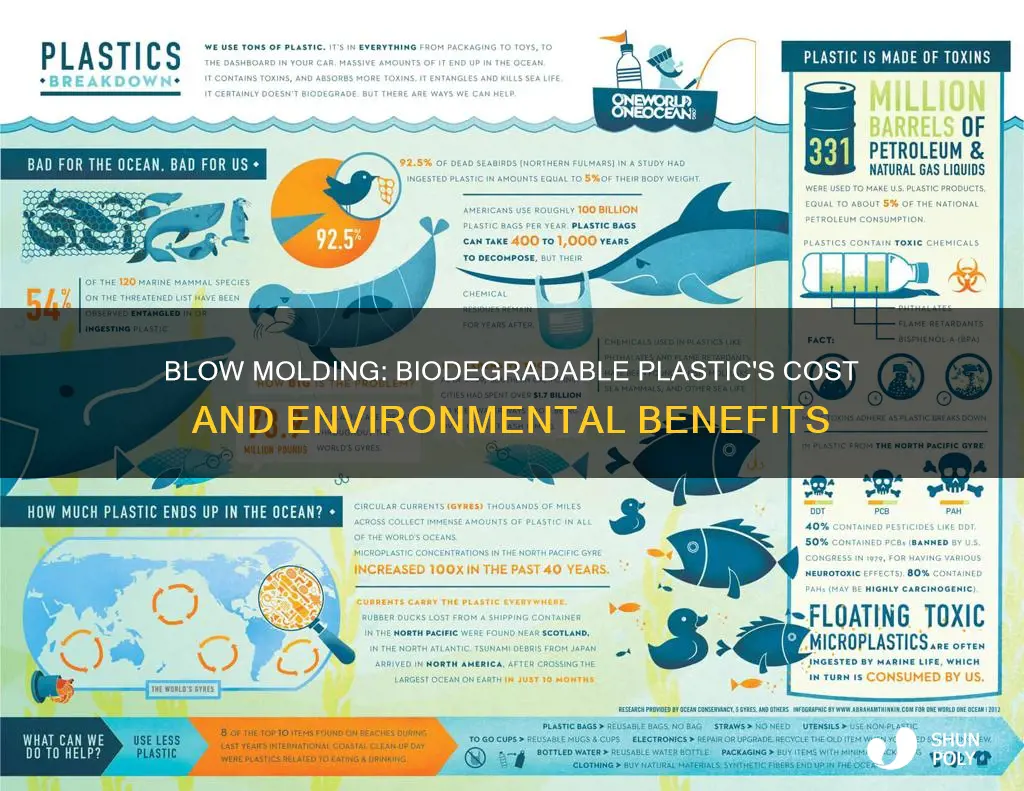
Plastic blow moulding is a popular manufacturing process that produces a lot of plastic waste. In recent years, there has been a growing concern about the environmental impact of plastic waste and the need for more sustainable manufacturing processes. Biodegradable and compostable plastics are gaining popularity, and the use of these in blow moulding processes is expected to gain traction in the coming years. One of the most common developments in bio blow-moulding is a simple, starch-based polymer. Vegetable starch from agricultural products such as corn, wheat, tapioca and potatoes is processed into biodegradable polymers.
Characteristics | Values |
---|---|
Environmental impact | Blow moulding processes that use biodegradable plastic can help reduce plastic waste. |
Energy costs | Using recycled plastics in blow moulding processes can save up to 70% of energy costs compared to using virgin materials. |
Starch-based polymers | Vegetable starch from agricultural products such as corn, wheat, tapioca and potatoes can be processed into biodegradable polymers. |
Additives | An additive called Reverte™ can be added to regular, petroleum-based polyethylenes to cause PET products to degrade into CO2 and water under UV light exposure. |
What You'll Learn
The environmental impact of plastic blow moulding
Plastic blow moulding is a popular manufacturing process that produces a lot of plastic waste. The process has had a significant economic impact around the world, contributing to the growth of the plastics industry. However, the environmental impact of plastic blow moulding is a growing concern.
The use of biodegradable and compostable plastics in blow moulding processes is expected to gain traction in the coming years as consumers and governments become more environmentally conscious. Biodegradable plastic is already in high demand in Japan and Europe. There are several variants of biodegradable blow-moulding PET resins, including starch-based polymers. These polymers are made from vegetable starch from agricultural products such as corn, wheat, tapioca and potatoes. They are processed into biodegradable polymers that require lower levels of heat for forming, saving manufacturers money on energy.
Another example of a biodegradable blow-moulding PET resin is Reverte™, an additive that can be added to regular, petroleum-based polyethylenes to cause PET products to degrade into CO2 and water under UV light exposure.
Using recycled plastics in blow moulding processes can also help reduce the environmental impact of plastic blow moulding. Recycling plastic bottles can save up to 70% of energy costs compared to using virgin materials.
Polycarbonate Plastic: Understanding the Cost of This Material
You may want to see also
The use of recycled plastics in blow moulding
Blow moulding is a popular manufacturing process that produces a lot of plastic waste. In recent years, there has been a growing concern about the environmental impact of plastic waste and the need for more sustainable manufacturing processes. The global market for plastic blow moulding is expected to grow steadily in the coming years, driven by the increasing demand for consumer products, industrial parts, and packaging containers.
In addition to using recycled plastic in blow moulding, the recycled pellets from blow-moulded materials can also be used in injection moulding, extrusion moulding, and blown film lines as recycled content to produce many different plastic products. By recycling production scraps, and using recycled contents in their production, blow moulding manufacturers can save costs, stay competitive, and improve their business reputation.
The use of biodegradable and compostable plastics in blow moulding processes is also expected to gain traction in the coming years as consumers and governments become more environmentally conscious. Various versions of biodegradable blow-moulding PET resins have emerged. The first, championed by Planet Green Bottle, has been trademarked Reverte™, and is essentially an additive which can be added to regular, petroleum-based polyethylenes to cause PET products to degrade into CO2 and water under UV light exposure. Another common development in bio blow-moulding is a simple, starch-based polymer. Vegetable starch from agricultural products such as corn, wheat, tapioca and potatoes are processed into biodegradable polymers which require lower levels of heat for forming, saving manufacturers money on energy.
The High Cost of Plastic: Price per Foot
You may want to see also
The use of biodegradable and compostable plastics in blow moulding
One of the most common developments in bio blow-moulding is a simple, starch-based polymer. Vegetable starch from agricultural products such as corn, wheat, tapioca and potatoes is processed into biodegradable polymers, which require lower levels of heat for forming, saving manufacturers money on energy.
There are also various versions of biodegradable blow-moulding PET resins. One example is Reverte™, an additive which can be added to regular, petroleum-based polyethylenes to cause PET products to degrade into CO2 and water under UV light exposure.
Using recycled plastics in blow moulding processes can also help reduce the environmental impact of plastic blow moulding. Recycling plastic bottles, for instance, can save up to 70% of energy costs compared to using virgin materials.
Plastic Surgery Consultations: NYC Surgeon Cost Insights
You may want to see also
The development of starch-based polymers for blow moulding
Blow moulding is a popular manufacturing process that produces a lot of plastic waste. There is a growing concern about the environmental impact of plastic waste and the need for more sustainable manufacturing processes. Biodegradable and compostable plastics are gaining popularity, which can help reduce plastic waste.
There are several variants of biodegradable blow-moulding PET resins. The first, Reverte™, is an additive which can be added to regular, petroleum-based polyethylenes to cause PET products to degrade into CO2 and water under UV light exposure. However, this perpetuates the problem of the continuing production of virgin petroleum materials.
Scientists from the American Chemical Society have set out to solve the problem of using renewable materials. Keratin from ground chicken feathers has been processed into a biodegradable polymer film with high tensility and 100% natural degradation. This film has been processed into a wide number of polymer items and is completely suitable for blow-moulding.
For packaging, starch blends with copolymers of ethylene and acrylic esters as well as methacrylates or vinyl acetates are used. The addition of polysaccharide promotes better water-vapour permeability, increased dimensional stability during injection moulding, and increased stiffness of materials during blow moulding.
The Cost of Installing Plastic Sash Windows
You may want to see also
The use of additives to make blow-moulded products biodegradable
One way to make blow-moulded products more environmentally friendly is to use biodegradable and compostable plastics in the blow moulding process. This can help reduce plastic waste and is gaining popularity among consumers and governments who are becoming more environmentally conscious.
There are several variants of biodegradable blow-moulding PET resins that have emerged. One example is Reverte™, an additive that can be added to regular, petroleum-based polyethylenes to cause PET products to degrade into CO2 and water when exposed to UV light. Reverte™ helps to solve the problem of inert, non-degrading plastic waste and contamination when recycling petrol-based polymers with bio-based polymers. However, it does not address the issue of the continued production of virgin petroleum materials.
Another common development in bio blow-moulding is the use of starch-based polymers. These polymers are made from vegetable starch from agricultural products such as corn, wheat, tapioca, and potatoes, which are processed into biodegradable polymers. Starch-based polymers require lower levels of heat for forming, which can save manufacturers money on energy costs.
The use of biodegradable additives in blow moulding processes can help to reduce the environmental impact of plastic waste and contribute to a more sustainable future.
Recycled Plastic: Degradation and Value Loss
You may want to see also
Frequently asked questions
The cost of biodegradable plastic blow moulding depends on many factors, such as the supplier, the wholesaler, the size of the supply, and any printing on the packaging. The market price of the most common biodegradable plastic is usually between 6 and 7 euros per kilo, or $2-$7 per kilogram.
Biodegradable plastic blow moulding is more expensive than traditional plastic blow moulding because it uses natural raw materials and complex production processes.
No, as production of biodegradable plastic scales up, the price is expected to level with that of traditional plastic.
Biodegradable plastic blow moulding can help to reduce plastic waste and is better for the environment. It also requires lower levels of heat for forming, which saves manufacturers money on energy.