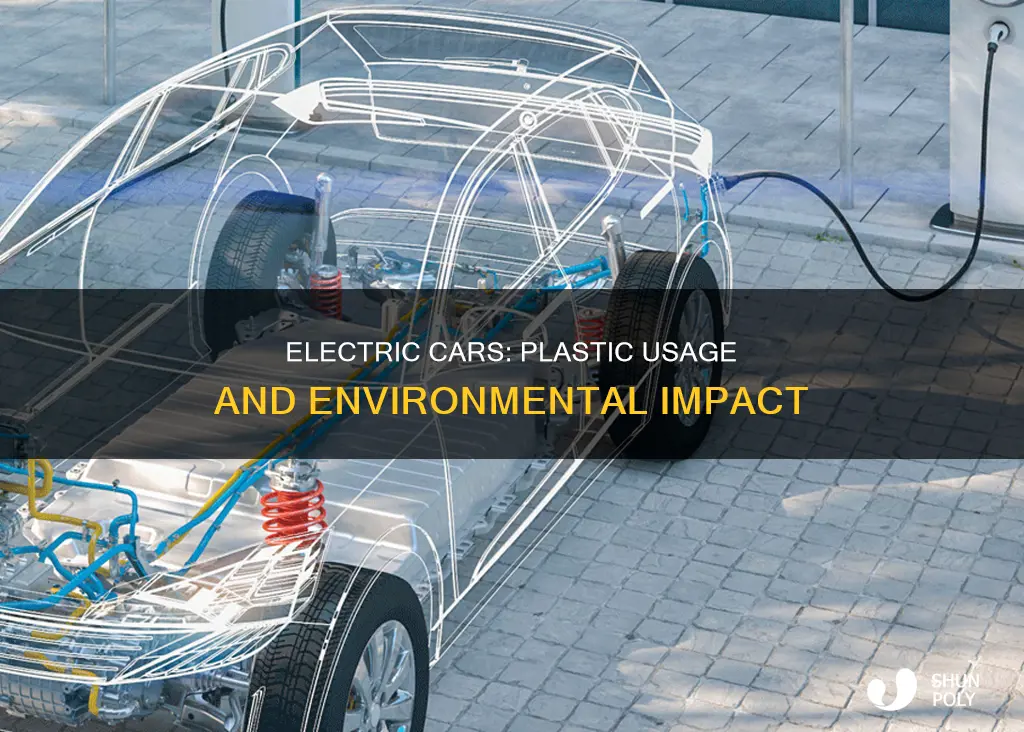
Electric vehicles (EVs) are becoming increasingly popular, and as a result, the auto industry is incorporating more plastic into the manufacturing process. Plastics are used in various components of electric vehicles, such as the chassis and battery casings, to offset the additional weight of EV batteries, which are much heavier than internal combustion engines. The use of plastics in EVs is driven by the need to reduce weight, improve fuel efficiency, enhance safety, and meet sustainability goals. From 2012 to 2021, the average mass of plastics in an automobile sold in the United States increased by 16% to 411 pounds (186 kg), making up less than 10% of the vehicle's weight but accounting for approximately 50% of its volume. This trend towards increased plastic usage in EVs is expected to continue as the market share of electric vehicles expands.
Characteristics | Values |
---|---|
Average amount of plastics in automobiles from 2012 to 2021 | 411 lbs (186 kg) |
Percentage increase in the average mass of plastics in an automobile sold in the US from 2012 to 2021 | 16% |
Percentage of an average vehicle's weight that plastics account for | <10% |
Percentage of a vehicle's volume that plastics account for | 50% |
Average amount of plastic in the typical car in 2016 | 151 kg |
Average amount of plastic predicted to be used in the average car in 2020 | 775 lbs |
Percentage of weight reduction required for every 5% to 7% improvement in fuel economy | 10% |
Number of hybrid and electric vehicles on the road in 2023 | 2 million |
Number of plug-in hybrid and fully electric vehicles sold worldwide in 2022 | 750,000 |
Number of hybrid and electric vehicles expected on the road by 2020 | 9-20 million |
Number of hybrid and electric vehicles expected on the road by 2025 | >30 million |
Percentage of "chemistry value per vehicle" that has grown over the past decade | 20% |
Average weight of polypropylene used in automobiles | 97 lbs (44 kg) |
Average weight of polyurethane foam used in automobiles | 84 lbs (38 kg) |
Average weight of polyamide used in automobiles | 41 lbs (18.5 kg) |
Average weight of high-density polyethylene used in automobiles | 34 lbs (15 kg) |
What You'll Learn
Plastic demand in electric vehicles
Electric vehicles (EVs) have seen a huge increase in sales in recent years, with projections showing that up to 50% of the market will be electric or hybrid by 2030. This shift in the automotive industry has also brought about a change in the materials used in vehicles.
Plastics are now being used more and more in vehicles, and this trend is expected to continue as EVs become more popular. Plastics are important in the automotive industry because they help to reduce the weight of vehicles, which improves fuel efficiency and reduces costs for drivers and carbon emissions from transportation. In 1960, the average car made in North America had only 8 kg of plastic and composite materials, but by 2016, the typical car was made with 151 kg of plastics and composites, making up about 8% of the car's weight and about 50% of its volume.
The use of plastics in EVs is particularly beneficial because the batteries that power them can be very heavy, often weighing over 1000 lbs. By using lightweight plastics in components like the chassis and battery casings, manufacturers can offset the additional battery weight. Plastics are also used in EV chargers, further increasing the demand for plastics in the EV industry.
The type of plastics used in EVs is also important. For example, some polymers, such as nylon, can absorb moisture and expand, which could be dangerous if used in sensors for autonomous vehicles. Other plastics, like polyphenylene sulfide, have high dimensional stability, making them more suitable for use in sensors. The development and use of specialized, high-performance plastics in EVs are driven by the need to improve sustainability, safety, and performance.
Pepsi's Plastic Problem: An Annual Overview
You may want to see also
Plastic's role in improving fuel efficiency
The role of plastics in improving fuel efficiency in electric vehicles is significant. Firstly, plastics contribute to weight reduction, which is a crucial factor in fuel efficiency. According to the Office of Energy Efficiency and Renewable Energy, a mere 10% reduction in vehicle weight can lead to a 6-8% improvement in fuel economy for conventional vehicles. This advantage applies equally to electric vehicles, where weight directly impacts their range and functionality for consumers.
Plastics are lightweight, with plastic components weighing up to 50% less than similar parts made from other materials. This property allows plastics to make up about 50% of a vehicle's volume while only contributing approximately 10% of its weight. By incorporating more plastic into various components, such as the chassis and battery casings, automakers can offset the additional weight of electric motors and batteries. This weight reduction is especially critical in electric vehicles, as their batteries can increase the overall weight by up to 35%.
The use of plastics in electric vehicles is becoming increasingly important as the demand for these cars grows. Electric vehicles rely on heavy lithium-ion batteries, and replacing the electric cells with lightweight plastic components can extend their driving range. Additionally, certain high-performance plastics can absorb four times the crush energy of steel, enhancing passenger safety in collisions.
Plastics also offer cost savings for automakers and car owners. Plastic parts can be moulded with multiple features, reducing the need for expensive assembly steps required with metal parts. Furthermore, plastics are durable and impact-resistant, contributing to vehicle safety.
The auto industry's increasing adoption of plastics in vehicles is driven by the need to improve fuel efficiency, reduce costs, and enhance safety. As the popularity of electric vehicles continues to rise, plastics will play an even more critical role in the auto industry's efforts to create sustainable and efficient transportation solutions.
The Reality of Plastic Recycling: Are We Doing Enough?
You may want to see also
Plastic usage in EV chargers
Electric vehicle (EV) chargers require plastics that can withstand countless use cycles, as well as outdoor conditions such as humidity, cold, sunlight, and vandalism. Polycarbonates, a type of engineering thermoplastic, are commonly used in EV chargers due to their strength, stiffness, toughness, and transparency. They can maintain their rigidity up to 140°C and toughness down to -20°C, with special grades capable of even lower temperatures. Polycarbonates are also lightweight, weighing up to 50% less than glass components, which improves the overall efficiency of the EV.
Polycarbonate films are versatile and commonly used in charger housings, covers, light and display lenses, and other components. They are highly impact-resistant, making them ideal for protecting against potential scratches and damage from vehicles. Additionally, polycarbonate resins are only one-seventh the density of steel and half the weight of aluminum, making them a lightweight solution for EV charger housings.
Other types of plastics used in EV chargers include ABS, acrylic, fluoropolymers, nylon, HDPE, LDPE, PBT, polypropylene, and PVC. Durethan polyamide (PA) and Pocan polybutylene terephthalate (PBT) are specifically used for components of charging plugs, sockets, and stations. Unreinforced materials are often chosen for charging plugs due to their dimensional stability, surface quality, impact resistance, and flame retardancy.
As the EV industry continues to evolve, the demand for higher-performance thermoplastics increases. These materials must meet stringent requirements, such as electromagnetic interference regulations (EMI), while also being recyclable to comply with tightening environmental regulations. Recycled plastics offer a marketing advantage, appealing to eco-conscious consumers and demonstrating corporate social responsibility.
Plastic Straws: What's Their Impact on Our Environment?
You may want to see also
Plastic's contribution to vehicle weight reduction
The automotive industry has embraced plastics as a means of reducing vehicle weight, improving fuel efficiency, safety, and performance. Plastics are particularly beneficial in electric vehicles (EVs), where weight reduction is a critical design factor.
Plastics are lightweight yet strong, making them ideal for reducing a vehicle's overall weight. This weight reduction further contributes to lower fuel consumption and improved fuel efficiency. For example, a nylon bracket under the hood of a car can integrate mounts and other features, eliminating the need for multiple metal pieces and their associated assembly costs.
The National Highway Traffic Safety Administration's 2012 investigation into lightweight vehicles using advanced plastics and composites found that a 30% plastic and composite content would reduce vehicle weight without compromising crashworthiness. Additionally, the substitution of metals with plastics has been shown to contribute to "lightweighting," helping with waste management and providing solutions for plastic disposal.
The use of plastics in vehicles is expected to increase with the growing popularity of EVs. This trend is driven by the need to meet fuel economy standards and the unique requirements of electric powertrains. For instance, plastics must withstand high temperatures from batteries, daily UV light exposure, and the wear and tear of regular use.
To further enhance the weight reduction capabilities of plastics, the industry is focusing on innovation and sustainability. Efforts are being made to develop next-generation technologies that make plastics even lighter, stronger, more efficient, and recyclable. This includes the use of innovative plastics like expanded polypropylene (EPP) and expanded polystyrene (EPS), which offer low weight, high strength, and safety for automotive components.
Recycling Rewards: Plastic Pays in Las Vegas
You may want to see also
Plastic safety and sustainability
The transportation sector is the largest contributor to US greenhouse gas emissions, responsible for over a quarter of the country's climate-damaging emissions. Electric vehicles (EVs) are seen as a sustainable alternative to traditional cars, primarily because they do not emit exhaust emissions such as carbon dioxide (CO2) and other pollutants like carbon monoxide and nitrogen oxides. However, the electricity used to charge EVs may create carbon pollution, depending on the energy mix of the region or country. For instance, while EVs in Iceland would result in almost no emissions due to the country's reliance on renewable energy sources, the situation in the US varies by state.
Plastics play a critical role in the sustainability and safety of electric vehicles. Lightweight plastics enable greater fuel efficiency, longer battery range, improved safety, enhanced performance, and increased lifespan of electric vehicles. Compared to similar components made from other materials, plastic components can weigh 50% less, making up 50% of a vehicle's volume but only about 10% of its weight. This helps offset the weight of electric motors and batteries, improving performance and making EVs more attractive to consumers. Additionally, plastics are used in innovative ways to make cars safer. For example, plastics are used in side doors, seat belts, airbags, and child safety seats due to their durable properties and high impact resistance.
The amount of plastic used in automobiles has increased over time. In 1960, the average car made in North America had only 8 kg of plastic and composite materials, while in 2016, the typical car was made with 151 kg of plastics and composites. This increase in plastic usage is linked to improved fuel efficiency, safety, and performance. As the auto industry embraces electric vehicles, the trend towards using more plastic is expected to continue, with plastics playing a crucial role in EV chargers as well.
To ensure the sustainability of plastic usage in EVs, the American Chemistry Council (ACC) is working towards making plastics lighter, stronger, more efficient, and more recyclable. Their goal is to have 100% of US plastic packaging reused, recycled, or recovered by 2040. This involves championing science-based policy solutions, fostering sustainability practices among member companies, and communicating authentically with communities about challenges and solutions for a safer and more sustainable future.
Copolymer Plastic Cost: Understanding the Price of This Material
You may want to see also
Frequently asked questions
The amount of plastic used in electric cars varies, but it can make up to 50% of the volume of materials in the car, while only accounting for around 10% of its weight. In 2016, the average car was made with 151 kg of plastics and composites. By 2020, the average car was predicted to use 775 lbs of plastic.
Plastics are used in electric cars to reduce their weight and improve their range and efficiency. Plastic components are also cheaper to manufacture than metal ones.
The most common types of plastics used in electric cars include polyurethanes, polypropylene, polyethylene, and engineering plastics (acrylonitrile butadiene styrene, acrylic-styrene-acrylonitrile, polybutylene terephthalate, polyoxymethylene, and polyamide).