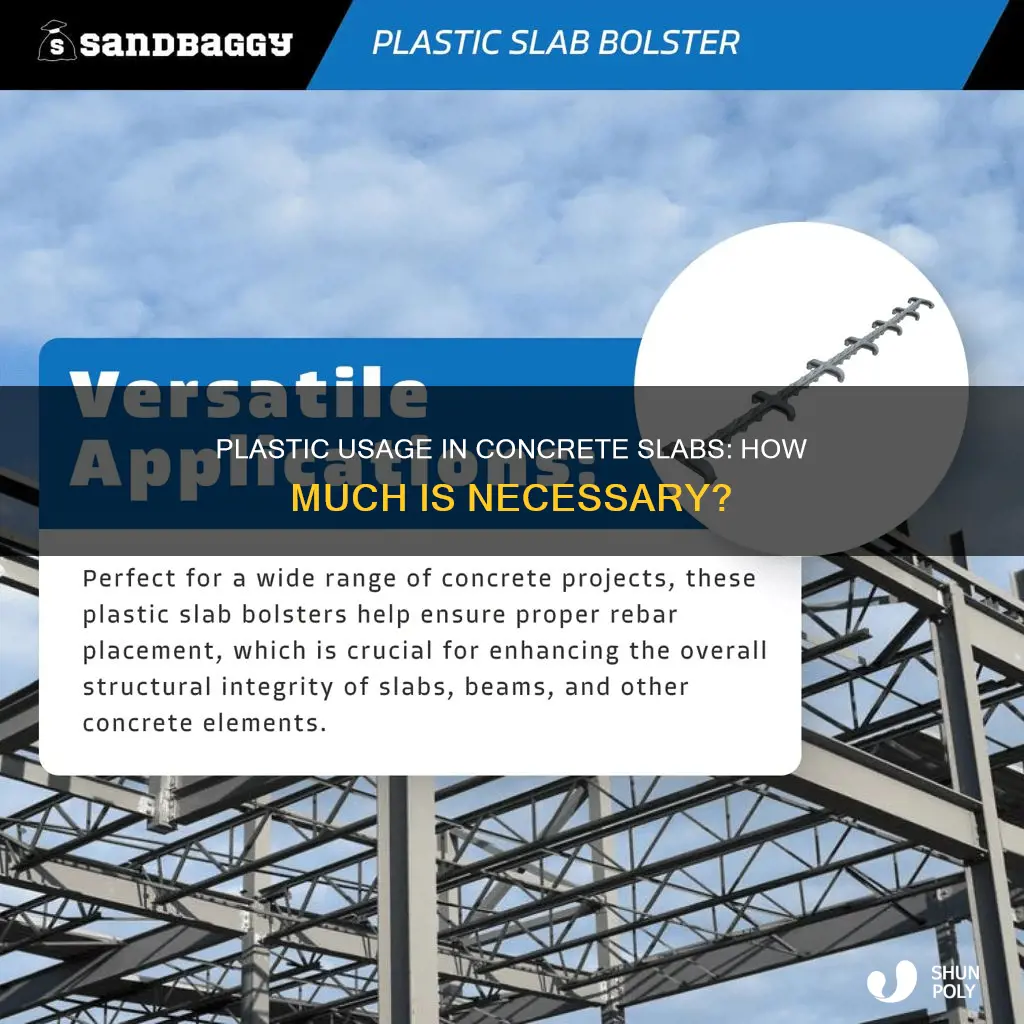
Concrete is a versatile construction material used for various purposes, including flooring. However, concrete is porous, allowing rainwater and moisture from the soil to permeate the surface and cause damage to the slab and the building on top of it. To prevent this, a vapour barrier, such as plastic sheeting, can be placed underneath the concrete slab. The thickness of the plastic sheeting and the type of vapour barrier used depend on the specific requirements and standards of the building project.
Characteristics | Values |
---|---|
Use of plastic under concrete slab | To protect the slab from moisture damage and prevent water vapours from entering the building |
Type of plastic | Polyethylene sheeting |
Thickness | Between 10 and 15 millimetres |
Durability | More durable than most plastic sheeting and almost impermeable to water |
Building requirements | Class 1 buildings require plastic and vapour barriers of at least 0.2 millimetres thickness |
Alternatives | Felt and asphalt |
What You'll Learn
Plastic sheets as a vapour barrier
Concrete is a porous material, which means that rainwater or moisture from the ground can easily permeate the surface. This can cause damage to the concrete slab and any flooring or structures on top of it. To prevent this, a vapour barrier is often installed underneath the concrete slab.
Plastic sheets are commonly used as a vapour barrier under concrete slabs. The plastic prevents moisture from the soil from permeating up through the slab and into the building, which is known as rising damp. It also reduces the amount of water that wet concrete sucks up from the ground when it is first poured, leading to a stronger concrete bond.
The recommended thickness of plastic sheeting for use under concrete slabs varies. Some sources recommend a thickness of 10 to 15 millimetres, while others suggest a minimum thickness of 15 millimetres. The American Concrete Institute (ACI) states that 10-mil poly or plastic with a 0.03 Perms IMP score is the lowest barrier that should be used under residential concrete. Thicker plastic will create a better barrier and be more puncture-resistant. For commercial projects, thicker plastic of 10 to 20 millimetres is often specified.
To install a vapour barrier, roll out the plastic sheeting on top of a compacted sand subbase and before placing the slab on ground reinforcement. If multiple sheets are required, they can be taped together with vapour barrier tape. It is important to seal any joints or seams in the barrier to prevent moisture from penetrating through.
Americans' Obsession with Anti-Aging Plastic Surgery: The Costly Affair
You may want to see also
Thickness of plastic sheets
The thickness of plastic sheets is an important consideration when installing a vapour barrier under a concrete slab. Concrete is a porous material, and moisture from the soil can easily penetrate it, leading to structural damage over time. Therefore, it is crucial to use plastic sheets with an appropriate thickness to act as a moisture barrier.
The recommended thickness of plastic sheets for a concrete slab varies depending on the specific requirements and applications. The American Concrete Institute (ACI) recommends using plastic sheeting with a thickness of at least 10-mil (0.0254 cm) for residential concrete. Thicker plastic sheets, such as 15-mil (0.0381 cm) or 20-mil (0.0508 cm), offer increased durability and are less absorbent. For indoor slabs, it is particularly important to use thicker plastic to provide an effective moisture protection layer.
The thickness of plastic sheets can range from 1 to 10 mil (0.00254-0.0254 cm) or more, depending on the intended use. Plastic sheeting with a thickness of 1 to 3 mil is considered light-duty and suitable for temporary applications. Medium-duty plastic sheeting ranges from 4 to 6 mil and is commonly used in construction as a vapour barrier or for temporary protection. For heavy-duty applications, such as construction sites or agricultural purposes, plastic sheeting of 8 mil (0.0203 cm) or higher is recommended for superior strength and resilience.
When determining the appropriate thickness of plastic sheets for a concrete slab, it is essential to consider factors such as the environment, anticipated stress, and duration of use. For example, if the plastic will be exposed to harsh weather conditions or heavy machinery, opting for a thicker gauge is crucial for long-lasting performance. Additionally, thicker plastic sheets can provide better vapour barrier properties, as suggested by ASTM E-1745.
Overall, the thickness of plastic sheets for a concrete slab should be chosen based on the specific requirements of the project, ensuring optimal protection and performance while also considering the environmental impact and sustainability of the materials used.
Plastic Bowl Weights: What You Need to Know
You may want to see also
Plastic rebar chairs
These rebar chairs are available in a variety of sizes and styles to accommodate different rebar sizes and spacing requirements. They typically feature a base with a central protrusion or "seat" upon which the rebar rests, maintaining the desired rebar elevation within the concrete slab.
When using plastic rebar chairs, it is crucial to consider the load-bearing capacity of the chairs to ensure they can withstand the weight of the rebar and concrete without failing. Additionally, proper spacing and arrangement of the chairs are essential to provide adequate support to the rebar, preventing sagging or displacement during the concrete pouring process.
Los Angeles' Plastic Waste: A Troubling Overview
You may want to see also
Alternative methods to plastic
Concrete is a versatile construction material, especially for supporting structures with concrete bases. Concrete is permeable, and moisture from the soil can easily enter a concrete slab and cause damage. This is why a protective layer of plastic is often placed underneath a concrete slab to act as a vapour barrier.
However, there are alternative methods and materials to using plastic as a vapour barrier. Here are some methods that can be used as alternatives to plastic:
Curing Concrete with Water
Curing concrete with water is a traditional method to prevent excessive moisture loss. This process involves maintaining a layer of water on top of the concrete slab. This can be done through various techniques such as immersion, ponding, fogging or misting, and wet covering. Each technique is suited to different environmental conditions and the specific requirements of the concrete slab. For example, ponding is suitable for flat surfaces, while fogging is used in warmer temperatures and low humidity.
Membrane-Forming Curing Compounds
Curing compounds are chemical products that are sprayed directly over the concrete surface and allowed to dry. These compounds form an impermeable membrane that prevents moisture loss from the concrete. It is important to note that curing compounds should be applied when the concrete has hardened but still retains some water content.
Epoxy
Epoxy can be applied on top of the concrete slab for basic moisture control. However, it is important to wait for the concrete to cure and pass the moisture test before applying epoxy.
Aluminum Foil
Aluminum foil can be used as a vapour barrier due to its impermeability to air and water vapour. It has a 0.00 Perms IMP score, which indicates its effectiveness in blocking moisture transfer.
Other Vapour Barriers
Alternative vapour barriers can be used instead of plastic. For example, a vapour retarder is a type of barrier that prevents water from passing through concrete. It is important to select a vapour barrier with low permeability and high durability. The American Concrete Institute (ACI) recommends using a vapour barrier with a Perms IMP score of at least 0.03 for residential concrete. Thicker barriers are generally more effective and durable.
Plastic Weight Calculation: Square Inch to Ounces
You may want to see also
Required thickness according to building codes
The required thickness of plastic, or more specifically, a vapor retarder or barrier, depends on the building code in your region. In the United States, the 2021 International Residential Code (IRC) requires a 10-mil vapor retarder conforming to the ASTM E 1745 Class A standard for under-slab vapor retarders. This is an upgrade from the previous requirement of a 6-mil vapor retarder.
ASTM E 1745 classifies materials as Class A, B, or C based on puncture resistance, tensile strength, and water vapor permeance. Class A vapor retarders and barriers have the highest puncture resistance and tensile strength, while Class C is on the lower end of the scale. The water vapor permeance requirement is currently set at 0.1 perms for all three classifications, making puncture resistance and tensile strength the differentiating factors.
It is important to note that generic poly sheeting, often referred to as Visqueen, has been commonly used in residential construction to meet the minimum code requirements. However, this type of sheeting is now considered defective for under-slab applications due to its low quality and inability to withstand the installation process and degradation over time.
To ensure the best protection for your concrete slab, it is recommended to use high-performance vapor barriers made from 100% virgin resin. These products are typically manufactured in a multi-layer or co-extruded fashion, providing superior performance compared to generic poly sheeting.
By installing a high-performance vapor barrier, you can protect your concrete slab from moisture infiltration, improve indoor air quality, and increase the longevity of your structure. It is a wise investment that can save you from costly repairs and legal issues in the future.
The Expense of Hard Plastic: Understanding the Cost
You may want to see also
Frequently asked questions
The amount of plastic required for a concrete slab depends on the project and local regulations. The recommended thickness of polyethylene plastic sheeting for a concrete slab is between 10 and 15 millimetres. This thickness provides an effective barrier against moisture and is durable.
Plastic is used as a vapour barrier to protect concrete slabs from moisture damage. Concrete is porous, allowing moisture to seep through and damage the slab and any structures above it. Plastic sheets under the slab prevent moisture from permeating through and help reduce the amount of water absorbed by the wet concrete when it is first poured.
Yes, while plastic is commonly used, there are alternative options. Felt and asphalt have been used since the 1800s, and in some cases, a clear sealer coat is applied to the concrete instead of using a plastic vapour barrier.