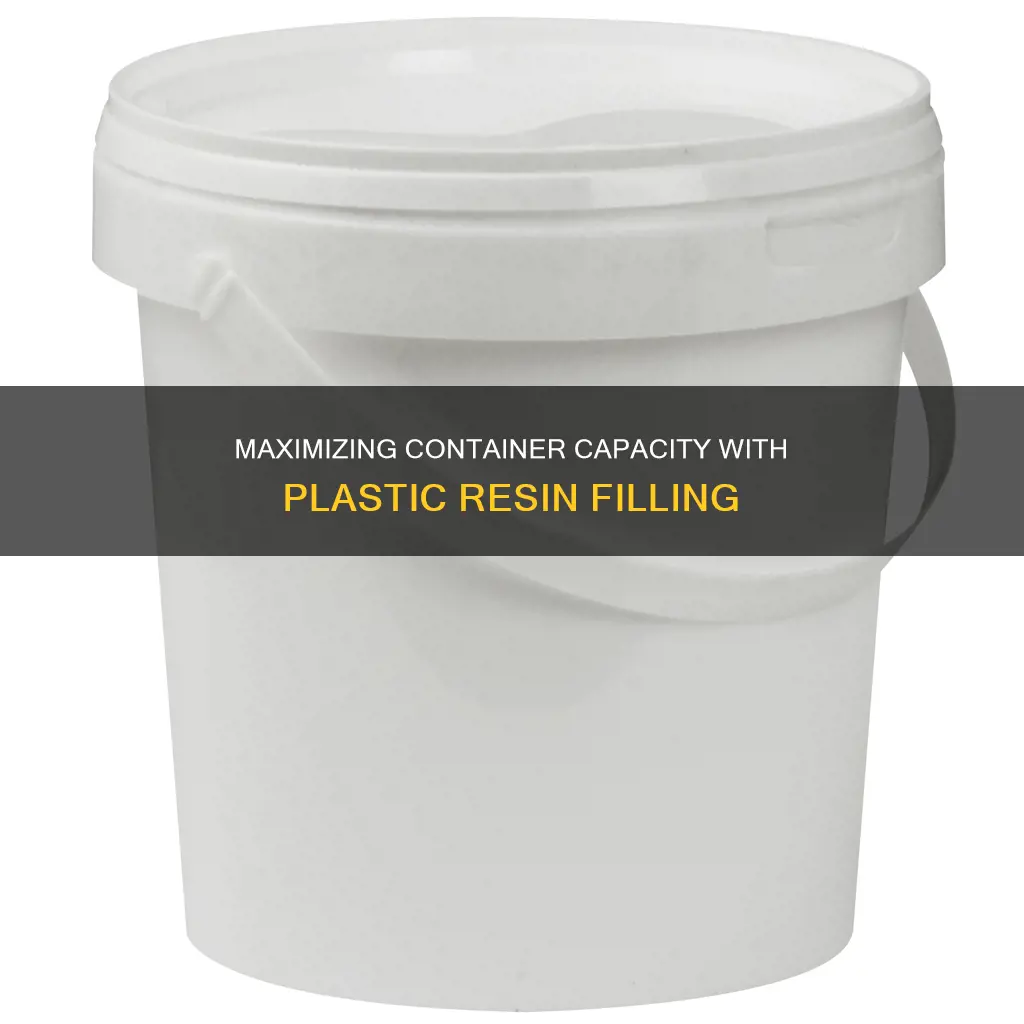
The volume of plastic resin that fits in a container depends on several factors, including the type of resin, the size and shape of the container, and the desired thickness of the resin layer. Different resins have different viscosities and curing properties that affect the volume required to fill a container. The size and shape of the container also play a role, as larger and irregularly shaped containers will require more resin to fill. Additionally, the desired thickness of the resin layer can vary, with some applications requiring thin layers, while others may need thicker applications. Other factors to consider are the curing time and potential chemical reactions between the resin and the container material.
Characteristics | Values |
---|---|
Container volume | 1.5 cubic inches |
Container shape | Spherical |
Wall thickness | 1/4 inch, thinning to 2mm at the top edge |
Lip diameter | 1 inch |
Resin type | Clear resin with glow-in-the-dark powder |
Curing time | 72 hours at room temperature |
Curing method | UV light |
Container material | Acrylic plastic |
What You'll Learn
Resin storage containers
When it comes to resin storage containers, there are a few things to consider. Firstly, resin should be stored in a container that is made of a suitable material, such as glass or plastic, and it is important to ensure that the container is clean and dry before filling it with resin. Additionally, it is recommended to store resin in a warm, dry environment, as temperature and humidity can affect the curing process.
One common practice is to transfer resin from its original large container into smaller containers for easier handling and storage. This can be done by pouring the resin into smaller glass or plastic bottles, jars, or containers. Some people even get creative and reuse ketchup or mustard squeeze bottles for this purpose. It is important to keep these containers upright and placed on a tray to catch any possible spills.
The size of the resin storage container will depend on the amount of resin you need to store. Resin is typically sold in containers ranging from cartridges or refill bottles of 1 litre to larger cans or gallons. If you are using smaller containers for storage, you can estimate the amount of resin you need and fill the containers accordingly.
Proper storage of resin is crucial to ensure its longevity and maintain its quality. Resin should be stored in a well-ventilated area, away from direct sunlight, and protected from extreme temperatures. It is also important to seal the containers tightly and store them in a location that is easy to access and safe from any elements that could affect the resin's performance.
Additionally, it is worth noting that epoxy resin and polyester resin are two common types of resin that may have specific storage requirements. For example, epoxy resin can be stored in glass or plastic containers, while polyester resin may require more specialised storage solutions due to its unique characteristics. It is always recommended to refer to the manufacturer's instructions for specific storage guidelines.
Plastic Remington Pellet Weight: One Shot, One Kill?
You may want to see also
Resin hardening issues
Resin is a versatile material used in a variety of projects, from jewellery to home decor. However, it can be tricky to work with, and issues with hardening are common. Here are some tips to address these problems:
Incorrect Resin-to-Hardener Ratio
An inaccurate resin-to-hardener ratio is a primary cause of hardening issues. The ratio typically needs to be equal parts resin and hardener, measured by volume, not weight. Adding too little or too much of either can alter the chemical reaction, resulting in a sticky or incomplete cure. Always follow the manufacturer's instructions for the specific ratio and mixing duration, which is usually at least 3-7 minutes.
Insufficient Curing Time
Resin may not have been given enough time to cure. Allow the resin to sit longer in a warm, dry space, as recommended for deep-pour resin. If the resin is still sticky after 48 hours, try applying a thin coat of regular epoxy resin to seal and harden it.
Mixing Issues
Inadequate mixing can also cause hardening issues. It is crucial to mix slowly and thoroughly, scraping the sides and bottom of the mixing container, to ensure all material is catalyzed to cure. Mixing too vigorously, however, can introduce air bubbles, so always mix smoothly and consistently.
Temperature and Humidity
Resin needs a warm environment to cure properly. Cold temperatures can cause cloudiness and hinder the curing process, resulting in sticky or tacky resin. Work in a space between 72°-85°F, ideally closer to 78°F. Similarly, humidity above 65% can interfere with curing, so ensure your workspace is well-ventilated and dry.
Incompatible Additives
Adding liquid pigments, paints, or dyes can disrupt the chemistry of the resin and prevent proper curing. Always use non-water-based, resin-specific colourants, and ensure you do not exceed the recommended amount of colourant (typically no more than 6% of the total volume of resin and hardener combined).
The True Cost of Plastic Forks: Manufacturing Price Analysis
You may want to see also
Resin shrinkage
Shrinkage can occur in two ways: volume shrinkage and axial shrinkage. Volume shrinkage refers to the overall reduction in the volume of the resin as it cures. Axial shrinkage, on the other hand, refers to the reduction in dimensions along specific axes (X, Y, and Z) during the curing process. While volume shrinkage is a global measurement, axial shrinkage focuses on how the material contracts in different directions. For example, shrinkage in the Z-direction may be compensated by the next layer, which will be slightly thicker.
The amount of shrinkage can vary depending on the resin used and the curing speed. For instance, Siraya Tech UV resins have about a 6% shrinkage per volume (1.5-2% per axis) when fully cured. Additionally, the curing environment, such as temperature and humidity, can impact the curing process and, consequently, the shrinkage.
To manage resin shrinkage and improve the accuracy of prints, several steps can be taken:
- Select low shrinkage materials: Choose resins with lower volume shrinkage rates, such as PLA-based or PETG-based resins, for applications requiring high precision.
- Use high-quality resins: Opt for resins that have been certified and tested for consistency and stability.
- Design parts with uniform wall thickness: Minimise the effects of shrinkage by designing parts with uniform thickness.
- Post-curing: Post-curing resin prints with UV light can ensure complete polymerization and reduce residual stress.
- Calibration and testing: Regularly calibrate your printer and test for shrinkage to adjust settings accordingly.
Lucrative Facial Plastic Surgery: How Much Do Surgeons Earn?
You may want to see also
Resin and container material reactions
The reaction between resin and container materials depends on several factors, including the type of resin, the container material, and the processing conditions. Here is a detailed overview of the potential interactions between resin and container materials:
- Polyethylene (PE) and Polypropylene (PP) Resins: These resins are commonly used in containers, bottles, and packaging materials. The manufacturing process involves polymerization, where monomers like ethylene and propylene bond to form long polymer chains. The containers made from these resins can be moulded into various shapes, including bottles and hollow objects, through processes like blow moulding and rotational moulding.
- Thermoplastic Resins: Thermoplastics do not undergo a chemical reaction during processing and can be reheated and reformed. They are shaped by injection moulding or extrusion techniques. In injection moulding, the resin is heated, injected into a mould under pressure, and then cooled to solidify. This method is suitable for creating complex shapes with high precision. On the other hand, extrusion involves forcing molten resin through a die to create long continuous shapes like pipes and sheets.
- Thermoset Resins: These resins, including epoxy and polyester, are designed to react chemically to form a three-dimensional network. They require a curing agent or hardener to initiate the reaction and solidify the structure. The curing process is crucial for determining the performance characteristics of the finished part. Epoxy resins, for example, cure by reacting with amines or anhydrides, while polyester resins require a catalyst for curing.
- Container Material Compatibility: The choice of container material depends on the type of resin and its specific properties. For example, epoxy resins can be stored in plastic or glass containers, as seen in user forums. However, it is important to consider the potential for dermal exposure, as uncured epoxy resins can cause skin irritation and rashes. Additionally, some resins, like polyurethane, have a strong odour that may require sealed storage.
- Processing Conditions: The processing conditions, such as temperature and humidity, can impact the reaction between the resin and container materials. For instance, deep-pour resin requires a warm environment (at least 75°F/24°C) to cure properly, and high humidity can interfere with curing, leaving a sticky surface.
- Reinforcement Materials: Reinforcement materials, such as glass fibre or fibre reinforcement compounds, are often added to resins to enhance their strength and performance. These materials are combined with the resin during the laminating step, influencing the quality and performance properties of the composite.
In summary, the reaction between resin and container materials depends on the specific resin type, the container material's compatibility, processing conditions, and the presence of reinforcement materials. Understanding these factors is essential for ensuring the successful use and storage of resins in various containers.
Plastic Manufacturing: A Global Concern and Its Annual Impact
You may want to see also
Resin transfer to other containers
When transferring resin to other containers, there are a few things to keep in mind. Firstly, it is important to ensure that the new containers are clean and dry before transferring the resin. This helps prevent any contamination that could affect the quality of the resin.
Another consideration is the size of the new containers. While it is possible to transfer resin to smaller containers, it is important to be cautious about potential water contamination, especially towards the end of the bottle due to condensation under the lid. One way to mitigate this issue is to use containers with tight-fitting lids or seals that can minimise exposure to moisture.
Additionally, it is recommended to store resin in a cool, dry place, away from direct sunlight. This helps maintain the stability of the resin and prevents premature curing or degradation.
When transferring resin, it is also important to work in a well-ventilated area to avoid inhaling any fumes. Proper safety gear, such as gloves and eye protection, should also be worn to protect against any accidental spills or splashes.
Finally, it is crucial to label the new containers clearly to avoid confusion and to keep track of the resin's shelf life. This ensures that the resin is used within its recommended period and helps maintain the quality of the final product.
Plastic Surgeons in Miami: High-Paying Careers
You may want to see also
Frequently asked questions
The amount of resin that can fit in a small acrylic plastic container depends on the container's volume. For example, if the container has a volume of 1.5 cubic inches, you can fill it with clear resin.
No, not all resins are suitable. Polyester resin, for instance, reacts with acrylic plastic and causes crazing (tiny cracks) on the surface. A recommended option is MG Chemicals 832WC Water Clear Epoxy Potting Compound.
You can try using UV resins, which are commonly used for 3D printing and are available online. Another alternative is "bar top epoxy", which is often clear and can be applied in thin layers or thicker depths depending on the product.
Yes, you can transfer resin to smaller glass or plastic bottles for more convenient handling. Some people use ketchup or mustard squeeze bottles for this purpose.
There are several reasons why resin may not harden: incorrect resin-to-hardener ratio, low temperature, high humidity, uneven mixing, or thin application. Ensure you follow the manufacturer's instructions and store the resin properly to avoid these issues.