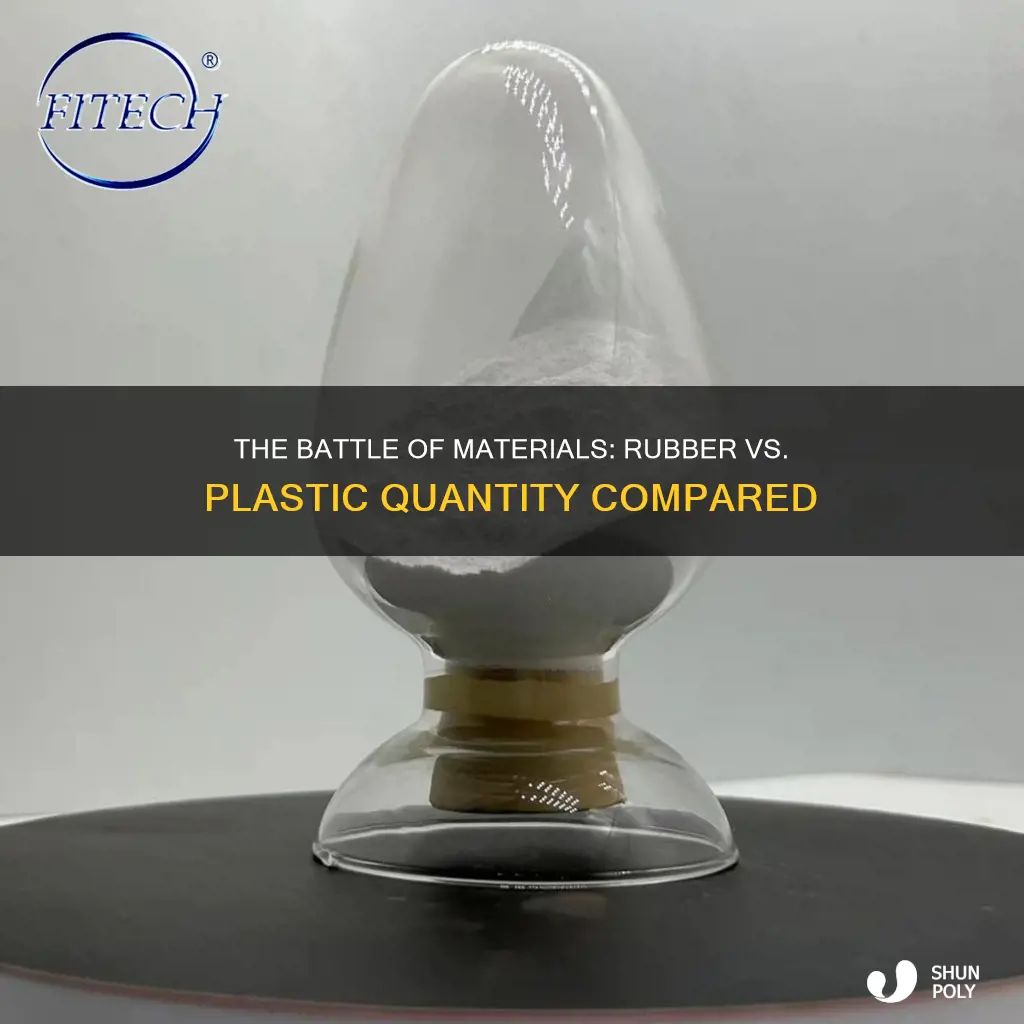
Natural rubber, harvested from rubber trees, and synthetic rubber, crafted from petrochemicals, are both widely used. Plastic, on the other hand, is typically synthetic or semi-synthetic, derived from crude oil or natural gas. While rubber is prized for its elasticity, plastic is known for its malleability, allowing it to be moulded into various shapes. The choice between these materials has significant implications for sustainability and environmental impact. Natural rubber is renewable and sustainable, while plastic pollution and disposal contribute to persistent environmental issues.
Characteristics | Values |
---|---|
Origin | Rubber: Natural or synthetic. Natural rubber is obtained from rubber trees. Synthetic rubber is made from petrochemicals like crude oil. Plastic: Synthetic or semi-synthetic, derived from crude oil or natural gas |
Composition | Rubber: Polymers of the organic compound isoprene, along with water and other organic compounds. Plastic: Organic compounds |
Properties | Rubber: Elasticity, durability, and resistance. Plastic: Malleability, stiffness or flexibility, UV-resistance, water repellency, flame resistance |
Applications | Rubber: Vehicle tires, waterproof seals, industrial machinery components. Plastic: Packaging, kitchenware, construction, industrial purposes |
Environmental Impact | Rubber: Natural rubber has a lower negative impact on the planet. Synthetic rubber is vulnerable to tearing and abrasion. Plastic: Contributes to persistent pollution and greenhouse gas emissions. Can take hundreds to thousands of years to decompose |
Production | Rubber: Natural rubber depends on crop yields. Synthetic rubber and plastics depend on petroleum prices. Plastic: Most plastics are synthetic polymers derived from petroleum |
What You'll Learn
Natural rubber vs synthetic rubber and plastic
Natural rubber, as the name suggests, is derived from natural sources – primarily the Hevea brasiliensis species of rubber tree. Other sources include the Panama rubber tree, rubber fig, and the common dandelion. Natural rubber is an elastomer, meaning it is an elastic substance that can return to its original shape after being stretched. It is also highly durable and resistant to chemicals. Natural rubber is used in various industrial goods, such as conveyor belts, gaskets, seals, and hoses. It is also commonly used in tyres due to its exceptional elasticity.
On the other hand, synthetic rubber is a man-made creation, produced through chemical processes by polymerizing various petrochemical compounds derived from crude oil and natural gas. Synthetic rubber was invented during World War II when the United States was cut off from international natural rubber supply lines. It is created by turning monomers into specific polymers, and there are several types, each with its own properties. Synthetic rubber is used in a wide range of applications, including wetsuits, balloons, PPE, shoe soles, and rubber bands. It is also commonly used in the automotive industry for tyres, seals, hoses, and flooring.
When comparing natural rubber vs. synthetic rubber, each has its own strengths and weaknesses. Natural rubber is a strong, flexible, and heat-resistant material with a high tensile strength. It is also biodegradable and has a milder odour than synthetic rubber. On the other hand, natural rubber is more susceptible to sunlight and oxidation. Synthetic rubber, meanwhile, is more resistant to tearing and abrasion, and extreme temperatures. It also tends to be cheaper to produce. However, synthetic rubber is not biodegradable and contributes to persistent pollution in the environment.
Plastics are also processed from crude oil and natural gas. They undergo extraction, refinement, and cracking before being polymerized. Plastics can take anywhere from 20 to 500 years to decompose, leading to pollution in oceans, rivers, and landfills. The production and disposal of plastics contribute to greenhouse gas emissions and climate change.
The Microscopic Threat: Regulating Micron Plastic Limits
You may want to see also
Elasticity
The process of making rubber involves building up polymers by sequentially adding short molecular backbone units to the chain through chemical reactions. Natural rubber is derived from the latex sap of rubber trees, while synthetic rubber is made from petrochemicals and petroleum by-products. The elasticity of rubber can be enhanced by adding a small amount of sulphur to produce chemical cross-links between adjacent polyisoprene molecules.
Plastic, on the other hand, is a synthetic or semi-synthetic material made from the polymerization of monomers, usually derived from crude oil or natural gas. It can be moulded into different shapes and forms, offering flexibility and a wide range of physical properties. However, plastic does not possess the same level of elasticity as rubber.
While rubber is commonly used in applications requiring high elasticity, such as vehicle tires, plastic is often chosen for its versatility and affordability. The main differences in composition between rubber and plastic stem from their origins, with rubber being natural or synthetic, and plastic typically being synthetic or semi-synthetic. This distinction leads to varied mechanical properties, making each material suitable for specific industrial purposes.
In summary, rubber and plastic have distinct elastic properties due to their unique molecular structures and compositions. Rubber's high elasticity makes it ideal for applications requiring flexibility and deformation resistance, while plastic's versatility and affordability make it a popular choice for a wide range of products.
Burning Plastic: Energy Gained, Environment Drained?
You may want to see also
Degradation and decomposition
The degradation and decomposition of rubber and plastic are complex processes influenced by various factors, including the type of material, environmental conditions, and the presence of additives.
Plastic Degradation and Decomposition
Plastic degradation refers to the reduction in the physical and chemical properties of plastic polymers over time. The most significant factors contributing to plastic degradation are heat, light, air, and water. Oxidation and chain scission are the major chemical changes that occur during degradation, leading to a decrease in molecular weight and degree of polymerization. As a result, physical properties such as strength, malleability, appearance, and colour are altered. The degradation of plastic can occur at any stage of its product life cycle, including initial processing, use, disposal, and recycling.
The rate of plastic degradation varies significantly, with some plastics biodegrading very slowly, sometimes even considered non-biodegradable. The addition of certain additives, such as biodegradable additives, can accelerate degradation by improving biodegradability. On the other hand, recycled plastics may exhibit more degradation than fresh materials due to the cumulative effects of multiple processing cycles.
The specific surface degradation rate (SSDR) is a metric used to harmonize and compare degradation rates of different plastics. It is important to understand degradation rates as they provide insights into the persistence of plastic pollution in the environment. For example, high-density polyethylene (HDPE) in the marine environment has an estimated half-life ranging from 58 years for bottles to 1200 years for pipes.
Rubber Degradation and Decomposition
Rubber, particularly natural rubber, polybutadiene, styrene-buteriene rubber, and NBR, is sensitive to degradation through processes like ozonolysis, which can lead to immediate chain scission and ozone cracking. High humidity can also accelerate the degradation of certain types of rubber, promoting the growth of fungi and the action of acidic atmospheric pollutants.
Similar to plastic, the degradation of rubber can be influenced by additives. Antioxidants, for example, can help prevent oxidation, while antiozonants can be added to rubber to prevent ozone cracking.
Environmental Impact
The degradation of plastics and rubber has significant environmental implications. Plastic waste, which is generated at a rate approaching 400 Mt per year, accumulates in the environment and persists for extended periods, leading to widespread contamination. As plastic degrades, it can break down into microplastics and release toxins, causing ecological problems and potential adverse effects on human health.
The degradation of rubber, particularly from tyres, also contributes to the microplastics found in the ocean. However, it is estimated that nearly two-thirds of microplastics in the ocean originate from the washing of synthetic fabrics. The presence of microplastics in the environment affects the physical properties of aquatic ecosystems, alters light penetration, depletes oxygen, and impacts the biological ecosystem.
Affordable Plastic Shot Glasses: How Much Do They Cost?
You may want to see also
Manufacturing processes
Natural rubber is made by extracting latex sap from certain types of trees and other plants. While most latex is sourced from the Hevea brasiliensis tree (aka the rubber tree), over 2,500 varieties of trees and plants (including dandelions) produce the right kind of sap. The latex is harvested through a process called tapping, which involves making a cut in the bark of a tree and collecting the sap in cups. Ammonia is added to prevent the sap from solidifying, and acid is added to extract the rubber in a process called coagulation. The mixture is passed through rollers to remove excess water, and the layers of rubber are hung over racks in smokehouses or left out to air dry. Several days later, they are ready for processing.
Synthetic rubber, on the other hand, is typically produced using petroleum, crude oil, natural gas, or coal. Manufacturers refine these ingredients to produce naphtha, which is then combined with natural gas to create monomers. Rubber is created by converting these monomers to chains of polymers, which require steam and vulcanization. Vulcanization is a chemical process in which the rubber is heated with sulfur, an accelerator, and an activator. This forms cross-links between long rubber molecules, improving the material's elasticity, resilience, tensile strength, viscosity, hardness, and weather resistance.
The majority of plastic in use today is synthetic, derived from crude oil, natural gas, or coal. The first step in the manufacturing process is the extraction of these raw materials, which are then refined to obtain specific chemicals needed to make plastic—hydrocarbons. Large hydrocarbon molecules are broken down into smaller molecules in a process called cracking, which requires high temperatures. These smaller molecules are then reassembled into long chains through a process called polymerization, often with the aid of a catalyst. During processing, various additives may be mixed with the polymer to enhance properties such as strength, flexibility, colour, and resistance to UV light or fire. Common additives include plasticizers, stabilizers, fillers, pigments, and flame retardants.
The growing demand for limited oil reserves has driven the need for newer plastics derived from renewable resources, such as waste biomass, animal waste products, carbohydrates, fats, and oils. These plastics are marketed as biobased or bioplastics, and they offer a more sustainable alternative to traditional plastics. However, it's important to note that bioplastics are not automatically more sustainable, as they differ in the ways they break down and still require resources in their production.
Coca-Cola's Plastic Problem: Environmental Impact Exposed
You may want to see also
Applications and use cases
Rubber
Natural rubber is derived from latex sap harvested from rubber trees, while synthetic rubber is crafted through various chemical reactions using petrochemicals like crude oil. The elasticity, durability, and resistance of rubber make it a versatile material with a wide range of applications.
Common uses of rubber include:
- Vehicle tires
- Waterproof seals
- Industrial machinery components
- Phone cases: Rubber cases offer excellent grip and protect against minor drops and impacts. They are lightweight and have a soft-touch feel.
- Silicone cases, a type of rubber case, are popular due to their flexibility, protection, and grip.
- Watersports, sports medicine, accessories, footwear, and automotive components
- Fabrics and clothing: Natural rubber can be used to create biobased filaments for textiles.
Plastic
Plastic is a broad category of synthetic or semi-synthetic materials derived from organic compounds, typically crude oil or natural gas. It is known for its high malleability, allowing it to be formed into various shapes and sizes.
The different types of plastic include:
- Thermoplastics: These become pliable when heated and return to a solid form upon cooling. Examples include polyethylene and polypropylene.
- Thermosetting plastics: Once molded and cooled, they cannot be remelted or remolded. Examples include Bakelite and Melamine.
Common uses of plastic include:
- Packaging
- Kitchenware
- Construction
- Industrial machinery
- Phone cases: Plastic is the most common material for phone cases due to its low cost, versatility, and durability. Polycarbonate (PC) plastic cases, in particular, are impact-resistant.
- Synthetic leather: Many leather phone cases are made from vegan and faux leathers, which are usually derived from petroleum-based plastics.
Plastic Chess Set: How Valuable Are They Really?
You may want to see also
Frequently asked questions
Rubber is a natural product, harvested from latex obtained from rubber trees. Plastic, on the other hand, is a synthetic or semi-synthetic product, derived from crude oil or natural gas. Rubber is known for its elasticity, while plastic is known for its malleability.
Both rubber and plastic deteriorate continuously and in different ways, with rates that vary and are unpredictable. Deterioration may be caused by chemical, physical, or biological factors. For example, rubber may become brittle, hard, cracked, or sticky, while plastic may lose strength and exhibit similar physical changes.
Natural rubber has a significantly lower negative impact on the planet than synthetic rubber and plastics. The production of natural rubber does not contribute to deforestation, as trees are not cut down in the process. In contrast, plastics can take hundreds to thousands of years to decompose, leading to persistent pollution in the environment.
Rubber is commonly used in vehicle tires, waterproof seals, and industrial machinery components due to its elasticity and durability. Plastic, given its malleability, is used in a wide range of applications, including packaging, kitchenware, construction, and industrial purposes.
Both rubber and plastic can release harmful vapors as they deteriorate. Additionally, certain plastics may contain additives, such as plasticizers, that can evaporate over time, affecting the stability and safety of the material. Proper care and control of agents of deterioration can help extend the lifetime of these materials.