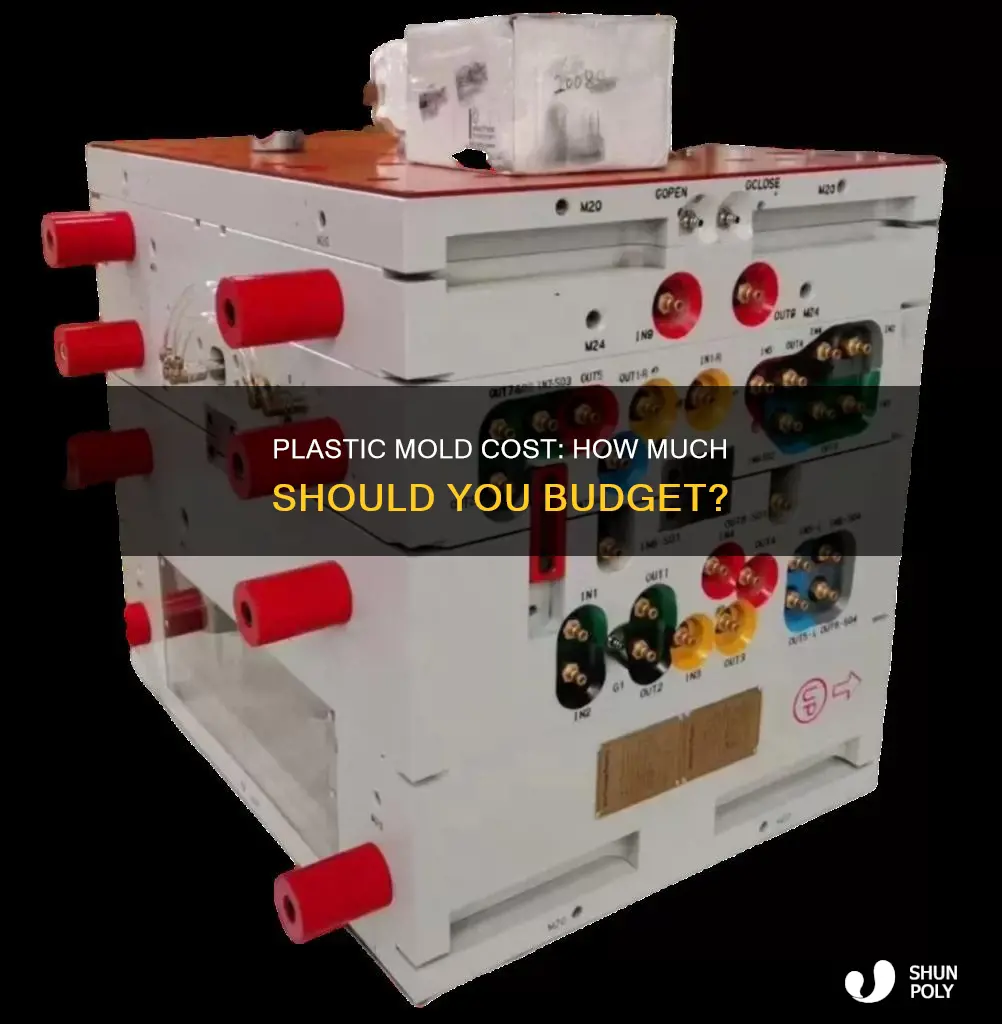
Plastic injection moulding is a manufacturing process known for its ability to produce parts cost-effectively and consistently. However, the cost of a plastic injection mould is not easy to decipher as it is dependent on several factors. These include the type of material used, the complexity of the design, the size of the mould, and the number of cavities in the mould. Simple moulds can range from $3,000 to $6,000, while larger, more complex moulds can start at $25,000 and go up to $50,000 or more. The cost per unit during manufacturing is relatively low, typically ranging from $0.20 to $10.00 per piece.
Characteristics | Values |
---|---|
Cost range | $3,000 to $100,000+ |
Simple moulds | $3,000 to $6,000 |
Larger, more complex moulds | $25,000 to $50,000+ |
Cost-effective material | Aluminium |
Durable material | Steel |
Prototype moulds | Cheaper than official moulds |
Longer production runs | More expensive |
High-strength steel | Required for extended production |
Multi-cavity tools | Larger and more expensive |
Plastic resins | $1 to $5 per kg |
Specialty materials | More expensive |
Additional processes | Increase unit cost |
What You'll Learn
Plastic injection moulding costs
The cost of a plastic injection mould can range anywhere from $3,000 to $100,000 or more. Simple moulds with single cavities and no complicated designs or shapes typically cost between $3,000 and $6,000. Larger, more complex moulds with features like multi-cavity injection, high production volume, or intricate designs can start at $25,000 and go up to $50,000 or more. The material used for the mould also affects the price, with steel being more expensive but lasting longer, and aluminium being a cheaper but less durable option.
The cost per unit during manufacturing is relatively low after the initial mould costs are covered, typically ranging from $0.20 to $10.00 per piece, depending on the quantity. Plastic resins used in injection moulding can vary in price, with standard resins like PP or ABS being more affordable, and specialty materials like glass-filled polymers or elastomers costing more.
To reduce costs, it is recommended to simplify the design, use standard resins, and minimise additional processes such as assembly, post-moulding treatments, or finishing. 3D printing is also suggested as a cheaper alternative for quick prototyping, although it may not be suitable for high-volume production.
When deciding on a manufacturer, it is essential to consider the specific requirements of the project and request quotes from multiple suppliers. It is also important to keep in mind that the price of injection moulding is affected by various factors, and a detailed quote should be obtained from the manufacturer based on the specific needs of the project.
The Cost of Plastic: Price Per Square Inch Explored
You may want to see also
Cost-effectiveness of different materials
The cost of a new plastic mold can vary significantly, ranging from $3,000 to $100,000 or more. The price is determined by various factors, including the complexity of the design, the size, the type of plastic, and the material used to make the mold. Speaking of the materials, here's a detailed overview of the cost-effectiveness of different materials used in mold-making:
Aluminum
Aluminum is a cost-effective option for mold-making, especially for low-volume production runs due to its affordability and ease of fabrication. It is also a good choice for projects that require quick turnaround times and flexibility in design modifications. However, aluminum is not as durable as steel and cannot be repaired or modified, leading to higher costs over time due to regular replacements.
Steel
Steel is a more expensive option compared to aluminum, but it offers superior durability and longevity. It is suitable for high-volume production requirements as it can withstand repeated use without deterioration. Steel molds can also be easily modified through welding processes to change the design or make repairs, which can lower the price-per-piece in the long run for mass production.
Silicone
Silicone is a cost-effective option for low-volume production runs and intricate designs due to its flexibility and ease of use. It captures fine details well and is ideal for projects that need flexible mold materials. However, silicone may not be suitable for high-volume production or applications that require strong and durable molds.
Beryllium-Copper Alloy
Beryllium-copper alloy is not commonly used for mold-making, but it can be a good choice for specific applications. It offers good thermal conductivity and hardness, which can improve cycle times and reduce costs. However, the availability and cost of this alloy may vary, and it may not be suitable for all types of molding processes or production volumes.
Other Materials
Other materials used in mold-making include polyurethane and latex. The choice of material depends on the specific application, production volume, design complexity, and material properties. For example, food-safe mold-making materials are necessary for molds used in food production, while durable materials like concrete are essential for creating molds for concrete structures. Additionally, eco-friendly mold-making materials are gaining popularity due to their positive environmental impact.
Plastic Consumption: How Much Do We Ingest?
You may want to see also
Cost of prototype moulds
The cost of a plastic injection mould is not easy to decipher; it depends on many factors and can range anywhere from $3,000 to $100,000, sometimes even more. Simple moulds range from $3,000 to $6,000, while larger, more complex moulds usually start at $25,000 and can increase depending on the details involved. The price of the plastic injection moulding service is generally expensive. However, after the initial purchase, the remaining process is simple as the mould carries the bulk of the financial burden.
The cost of prototype moulds is always lower than the official mould used during production runs. Prototype moulds are designed to speed up the manufacturing process and lower the mass manufacturing cost. Prototype moulding achieves cost efficiency, functionality and mechanical resistance depending on the desired part. The only difference between prototype and mass-production moulds is the mould itself. Prototype moulds are usually made from aluminium, which is a cheaper option than steel and suitable for short-term use and smaller production runs. Aluminium, however, is not as durable as steel and cannot be repaired or modified.
The primary driver of cost is the cycle time of the mould. Cycle time includes the time it takes to close the mould, inject the plastic, cool the part, and open and eject the mould. Prototype moulds have longer cycle times, which increases the part cost. However, prototype moulds can be beneficial as they can produce a large number of parts using the injection-moulded plastics to be used in manufacturing, which can support critical late development activities such as clinical trials, user studies, marketing samples, and design verification.
If you already have a prototype or drawing of your ideal mould, taking it to your manufacturer for a price estimate will be easier. They will consult with their engineers and other experts and provide a quote. The final price will depend on several factors, including the materials used, the plastic materials of the moulded products, and the complexity of the plastic parts.
Plastic Waste in Australia: An Annual Crisis
You may want to see also
Cost per unit
The cost per unit of a new plastic mold depends on several factors, including the type of materials used, the complexity of the design, the number of parts or units required, and the manufacturer's expertise.
Materials such as steel or aluminum are commonly used for molds, with steel being the preferred choice due to its durability and longevity. Aluminum is a more cost-effective option for short-term use, but it is less durable and cannot be repaired or modified. Other materials like beryllium-copper alloy are also options but are less commonly used.
The complexity of the mold design and the number of cavities or parts required will impact the cost per unit. Simple molds with basic designs and single cavities can range from $3,000 to $6,000, while larger, more intricate, and complex molds can start at $25,000 and go up to $50,000 or even $100,000. The more intricate the design, the higher the cost per unit, as it increases the overall cycle time and production costs.
The quantity of parts or units required also influences the cost per unit. Higher volumes can lead to lower per-piece costs, making the manufacturing process more economical. Additionally, the expertise and reputation of the manufacturer can play a role in pricing.
It is important to note that the cost per unit during manufacturing is relatively low compared to the initial cost of the molds. Typically, the cost per part ranges from $0.20 to $10.00 per piece, depending on the quantity and specific requirements.
To obtain an accurate estimate, it is recommended to provide detailed specifications, such as CAD drawings or similar products, to the manufacturer, who can then consult with their engineers and experts to provide a precise quote.
The World's Plastic Pollution Crisis: A Global Disaster
You may want to see also
Cost of additional processes
The cost of a plastic injection mold is determined by several factors, and the price can vary from \$3,000 to \$100,000 or more. The cost of additional processes will depend on the specific requirements and scope of the project. Here are some key factors that will influence the cost of additional processes:
Type of Plastic
The type of plastic used will impact the cost. Some plastics, such as PP, PC, Acrylic, PS, and PU, are more common and readily available, while others may be more specialized and costly. The choice of plastic will depend on the specific application and desired properties of the final product.
Complexity and Size of the Mold
The complexity and size of the mold will affect the cost. Larger and more intricate designs will likely require a higher financial commitment. Simple molds typically range from \$3,000 to \$6,000, while larger, more complex molds can start at \$25,000 and increase from there.
Number of Cavities
The number of cavities in the mold will impact the cost. Multi-cavity molds, which are used for high production runs, are larger and more expensive. However, they can also bring down the per-part cost, especially for projects requiring a large number of parts.
Material of the Mold
The material used for the mold will also affect the cost. Steel is a popular choice due to its durability and longevity, but it is more expensive than aluminum. Aluminum is suitable for short-term use and lower production volumes, but it is less durable and cannot be repaired or modified.
Post-Molding Treatments and Finishing
Any additional processes, such as assembly, post-molding treatments, or finishing, will increase the unit cost. It is important to consider the desired finish during the design phase to minimize additional post-processing steps.
Volume of Production
The volume of production will impact the cost per part. Higher volume production runs will result in a lower per-piece cost, making the process more cost-effective in the long run.
It is important to note that the cost of additional processes can vary widely depending on the specific requirements and scope of the project. It is always recommended to consult with a manufacturer to obtain an accurate price estimation based on the unique details of the project.
The Cost of Plastic Dental Partials: How Much?
You may want to see also
Frequently asked questions
The cost of a new plastic mold varies depending on several factors. Simple molds can range from \$3,000 to \$6,000, while larger, more complex, and higher-production molds can cost \$25,000 to \$50,000 or more. The price is determined by factors such as the materials used, the size and complexity of the mold, the number of cavities, and the level of precision required.
The materials used for the mold, such as steel or aluminum, can impact the cost. Steel is typically more expensive but lasts longer, while aluminum is more cost-effective for short-term use but may wear down quickly. The type of plastic used can also affect the price, as some plastics cause molds to wear out faster.
The complexity and size of the mold design can significantly influence the cost. Simple designs with minimal features are typically more affordable, while intricate details, larger parts, and multi-cavity molds can increase the price. Additionally, the number of parts required can impact the cost, as higher volumes may require larger and more expensive tools.
Yes, there can be additional costs for assembly, post-molding treatments, and finishing processes. The choice of materials can also affect the overall cost, with specialty materials like glass-filled polymers or elastomers typically incurring higher expenses. The cycle time or injection molding time, including setup and running time, can further impact the total cost.
The volume of production can impact the cost per part. Higher volumes can result in a lower per-piece cost, as the initial investment in the mold is spread across a larger number of units. Therefore, it is essential to consider the expected production volume when determining the cost-effectiveness of a plastic mold.