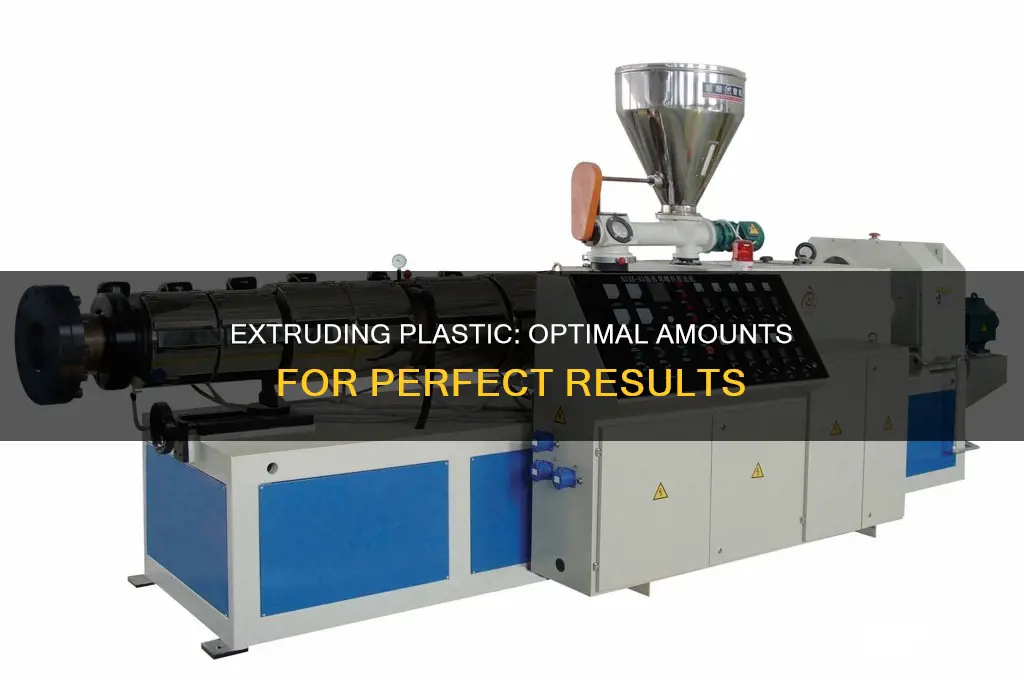
Plastic extrusion is a manufacturing process that turns small plastic pellets into solid plastics of different shapes and sizes. It is indispensable to modern manufacturing, playing a key role in the production of everyday household goods and a wide range of industrial applications. The cost of a plastic extruder machine depends on several factors, including the type and specifications of the machine, its features, and its performance. Single-screw extruders are generally lower-cost, while twin-screw extruders are more expensive due to their greater processing power and adaptability. The capacity, size, and dimensions of the machine will also impact the price.
Characteristics | Values |
---|---|
Plastic extrusion process | Turning small plastic pellets into solid plastics of different shapes and sizes |
Plastic extrusion applications | Household goods, building materials, automotive parts, electronics, furniture, office furnishings, store fixtures, POP displays, industrial |
Plastic extrusion machine cost | Depending on the type and specifications of the machine, features, performance, capacity, size, and material handling capacity |
Plastic extrusion machine type | Single screw extruders, twin-screw extruders |
Plastic extrusion machine cost range | $1,000 to hundreds of thousands of dollars |
Plastic extrusion process steps | Material preparation, preprocessing, cutting, extruding |
Plastic extrusion die | Blown-film extrusion die, long tube-shaped die |
Plastic extrusion output | Continuous flow of plastic, flat sheets, long tubes, hollow or tubular products, thick plastic sheets and films |
Plastic extrusion quality control | Compliance with strict quality control guidelines, monitored and recorded by Quality Assurance personnel |
What You'll Learn
Cost of plastic extrusion machines
Plastic extrusion machines are indispensable in modern manufacturing, playing a key role in the production of everyday household goods and industrial applications. The cost of a plastic extrusion machine depends on several factors, including the type and specifications of the machine, its features, and performance.
Single-screw extruders are the most common type of extrusion machine and are generally lower in cost. They are suitable for some simple extrusion processes but may be limited in handling more complex plastic materials. On the other hand, double-screw extrusion machines, also known as twin-screw extruders, offer greater processing power and adaptability, making them slightly more expensive. These machines are capable of producing more complex materials and are used in industries that require high-volume production.
The capacity and specification of the machine also impact its cost. Higher-capacity machines tend to require more complex engineering and more powerful drive systems, resulting in a higher price. The size and dimensions of the machine are crucial, as larger machines typically incur higher material and engineering costs. The material handling capacity of a plastic extruder is another factor that directly influences its cost.
The barrel and hopper design, which determine the extruder's ability to handle and feed material into the extrusion zone, also impact the overall cost. Other features like a cooling system, which is common in plastic and rubber extrusion machines to prevent overheating, add to the overall cost. Additionally, the motor power of the machine, determined by the material being processed and the required throughput, will influence the price.
While the cost of a plastic extrusion machine can vary depending on these factors, it is important to note that the quality of the machine and its performance should be the primary considerations when making a purchase decision.
Americans' Plastic Waste: A Year's Horrifying Overview
You may want to see also
Cost of plastic extrusion tooling
The cost of plastic extrusion tooling depends on several factors, including the complexity of the part, raw materials used, machine type, capacity and specifications, and labour costs.
Tooling costs for plastic extrusion can vary depending on the specific requirements and applications. Some companies offer guide prices for simple PVC extrusion tooling, starting at around £600 (plus VAT), with the price increasing for larger and more complex profiles. The cost of tooling for thermoplastics other than PVC and uPVC tends to be more expensive due to higher complexity and longer lead times.
The machine type is a significant factor in determining the cost of plastic extrusion tooling. Single-screw extruders are generally more affordable and suitable for simple extrusion processes, while twin-screw extruders are more expensive due to their greater processing power and adaptability. The capacity of the extruder, measured in hourly output, also impacts the price, as higher-capacity machines require more complex engineering and powerful drive systems.
Additionally, the raw materials used can affect the tooling costs. For example, the balance of physical properties of the material must match the end-use requirements, such as environmental factors, temperature, chemical exposure, flammability, aesthetics, and function. The selection of materials can impact the overall cost of the tooling process.
It's worth noting that the level of detail in the design can also increase tooling and production costs. The production technique, such as drawing down or offline cutting, can impact the cost, as certain techniques may require additional tooling expenses or create additional waste.
TSA Plastic Trays: What's the Cost of Security?
You may want to see also
Cost of plastic extrusion moulds
The cost of plastic extrusion moulds depends on various factors, including the type of machine, its specifications, features, and performance. Single screw extruders are generally more affordable and suitable for simple extrusion processes, while twin-screw extruders, with greater processing power and adaptability, come at a higher price point. The capacity of the extruder, measured in hourly output, also impacts the cost, with higher-capacity machines requiring more complex engineering and commanding a higher price. The size of the machine is another factor, as larger machines tend to cost more due to increased material and engineering requirements.
Tooling costs, which include labour and material expenses to develop "production-ready" tooling, can start at less than $1,000, but the actual cost depends on part complexity and raw materials used. Vacuum sizers, integral to many plastic extrusion setups, can also impact the overall cost.
It's worth noting that plastic extrusion has limitations in creating complex shapes compared to injection moulding, which can produce more intricate three-dimensional forms. Injection moulding has higher initial design costs due to the complex mould structure, but these costs can be mitigated by ordering larger quantities of plastic parts.
Some companies offer no-cost plastic extrusion tooling for a range of profiles and channels, while also providing custom solutions that cater to unique requirements.
Plastic Straws: How Much Do They Pollute Our Oceans?
You may want to see also
Cost of plastic extrusion per kg
The cost of plastic extrusion per kg depends on several factors, including the type of plastic, the complexity of the design, the specific equipment used, and the scale of production. Let's delve into the details and explore the factors influencing the cost of plastic extrusion per kg.
Firstly, the type of plastic plays a crucial role in determining the cost. Different plastics have different raw material costs, which form a significant portion of the overall extrusion cost. Thermoplastics, such as thermoplastic elastomers and flexible PVC, are known for their flexibility and resilience, while rigid PVC and high-impact polystyrene offer superior impact resistance. The choice of plastic depends on the specific application, and each type carries a different price tag.
Secondly, the complexity of the design can impact the cost. Custom plastic extrusion allows businesses to create products tailored to their exact specifications. However, intricate designs may require additional setup costs and increase the overall price per kg. The versatility of plastic extrusion lies in its ability to accommodate a wide range of applications, from custom plastic profiles to wire insulation and plastic tubing.
Moreover, the specific equipment and technology used in the extrusion process can influence the cost. The energy consumption of the extruder is a significant factor, as it requires energy to heat the plastic to the desired temperature. Efficient equipment, such as a well-designed extruder screw, can help reduce energy costs, leading to long-term savings. Additionally, the use of recycled plastics or foamed plastics can be a cost-effective approach, although it may introduce processing and quality challenges.
Lastly, the scale of production can impact the cost per kg. Plastic extrusion typically becomes more cost-effective at larger production quantities. The setup costs are spread out over a higher number of units, reducing the average cost per kg. However, it's important to note that the minimum production quantity may vary depending on the specific setup and requirements.
In conclusion, determining the cost of plastic extrusion per kg involves considering various factors, including raw material costs, design complexity, equipment efficiency, and production scale. By carefully evaluating these aspects, businesses can make informed decisions about the cost-effectiveness of plastic extrusion for their specific needs.
Paper and Plastic Waste: How Much Do You Contribute?
You may want to see also
Cost of plastic extrusion for 3D printing
The cost of plastic extrusion for 3D printing can vary depending on several factors, including the type of plastic, the diameter of the filament, and the complexity of the object being printed. Let's take a closer look at these factors and how they influence the cost.
Firstly, the type of plastic used significantly affects the cost. Standard materials like Polylactic Acid (PLA) and Acrylonitrile Butadiene Styrene (ABS) are generally more affordable and accessible. For example, a 2.2 lbs spool of PLA filament typically costs around $20. On the other hand, specialty filaments, such as flexible TPU, composite materials with carbon fiber or metal particles, and conductive filaments, tend to be more expensive due to their unique properties and manufacturing processes.
The diameter of the filament is another critical factor in determining the cost. The most common diameters are 1.75 mm and 2.85 mm (also known as 3.00 mm). Filaments with a smaller diameter, such as 1.75 mm, tend to be more expensive than those with larger diameters. This is because they require more precise manufacturing processes and often have higher tolerance, resulting in better print quality.
Additionally, the complexity and size of the object being printed play a significant role in the overall cost. Larger and more intricate designs will naturally require more filament material, increasing the cost of the print. To estimate the cost of a specific project, it is essential to consider the amount of filament needed, taking into account factors such as infill percentage and layer height settings. Various software tools and online resources can help estimate filament usage and provide cost calculations.
It is worth noting that labor costs and electricity expenses should also be factored into the overall cost of plastic extrusion for 3D printing. These additional costs may include the time spent on design, setup, and manpower required for the printing process. By considering all these factors and utilizing available resources, individuals and businesses can effectively estimate and manage the costs associated with plastic extrusion for 3D printing.
The Deadly Impact of Plastic on Marine Life
You may want to see also
Frequently asked questions
The cost of a plastic extrusion machine varies depending on the type and specifications of the machine, as well as its features and performance. Single screw extruders are generally lower in cost, while twin-screw extruders are more expensive due to their greater processing power and adaptability. The capacity, size, and material handling capacity of the machine will also impact the price. Industrial machines can range from tens to hundreds of thousands of dollars.
Yes, there are low-cost plastic extruders available for startups or individuals looking to recycle plastic waste. These machines can cost over $1,000 when considering material costs and electronic parts. While still cheaper than industrial machines, they may not be affordable for most individuals.
The cost of producing plastic products through extrusion depends on the complexity of the part and the raw materials used. Tooling costs, labour, and material costs must also be considered. The minimum production quantity may be restricted to 1,000 lineal feet to keep costs down.
The cost of a plastic extruder is influenced by its type, capacity, specification, and size. Single screw extruders are typically less expensive than twin-screw extruders. The capacity of the extruder, or how much product it can produce per unit of time, also impacts the price, with higher capacities requiring more complex engineering.