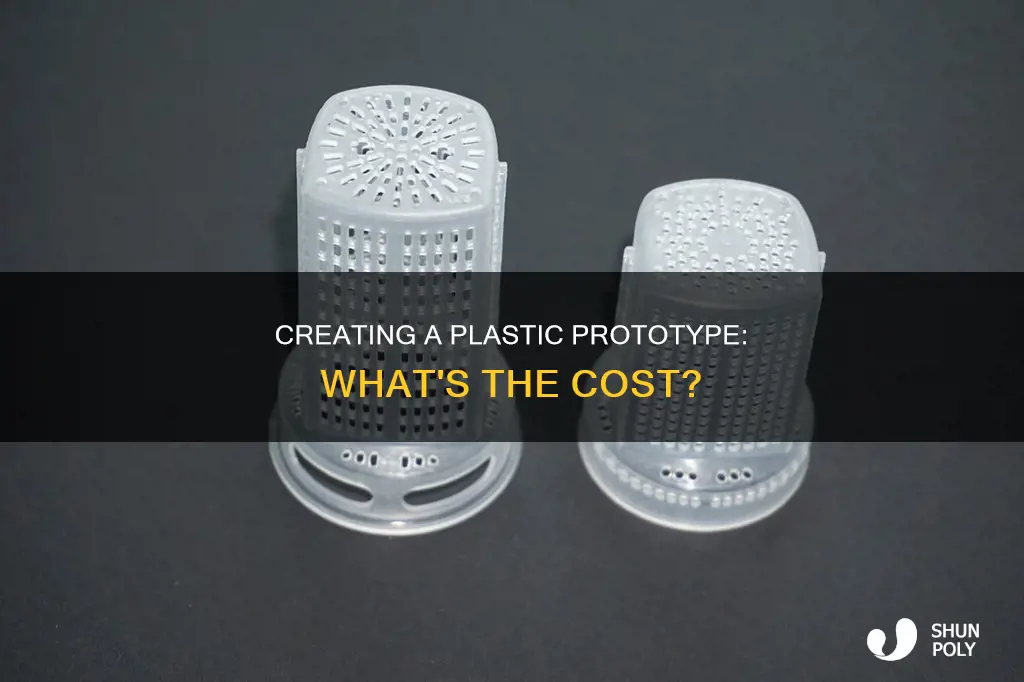
Plastic prototypes can be created through various methods, including 3D printing, CNC machining, injection moulding, and vacuum casting. The cost of creating a plastic prototype can vary depending on several factors such as complexity, scale, materials, and the chosen manufacturing process. Simple 3D-printed plastic prototypes can range from $30 to $5,000, while injection-moulded prototypes can start at around $3,000 and go as high as $100,000. The prototyping stage is crucial for successful production, and inventors often seek patent protection for their unique ideas before moving forward.
How Much to Make a Plastic Prototype
Characteristics | Values |
---|---|
Prototype Type | Visual, Functional, 3D-printed, FDM 3D-printed, SLA 3D-printed, SLS 3D-printed, Injection-moulded |
Cost | Simple plastic prototypes can cost under $15, but the price increases with the complexity of the design and the number of cavities in the mould. 3D-printed prototypes can range from $30 to $5,000, while injection-moulded prototypes can start at $3,000 and go as high as $100,000. |
Time | The time taken to create a prototype depends on its complexity and scale. Simple prototypes may take a few hours, while complex and large ones can take months or even years. |
Purpose | Prototypes are used to test product designs before mass production, assess and minimise design risks, and increase the chances of acquiring a patent. |
Number of Prototypes | The number of prototypes required depends on the product's size, complexity, and budget and time constraints. On average, customers go through 2-4 prototypes before launching a product. |
Other Considerations | The cost of prototypes can depend on the materials used, the size of the business, and the stage of product development. |
What You'll Learn
Plastic prototype costs
The cost of a plastic prototype varies depending on several factors, including the complexity of the design, the size, the materials used, the quantity, and the manufacturing process.
For a simple plastic prototype, the cost can range from under $15 to $5,000. However, if injection moulding is required, the price can increase significantly, ranging from as low as $3,000 to as high as $100,000. The cost of injection moulding depends on factors such as part size, complexity, material, quantity, and the number of cavities in the mould.
Creating a master model before moving on to silicone moulds can also impact the cost. While this process allows for more precise and detailed prototypes, it requires additional steps and materials. 3D printing is often used to create the master model, and the choice of 3D printing technique can also affect the overall cost. FDM 3D printing, for example, is a common and flexible procedure that can create prototypes with greater strength and resolution.
It's important to keep in mind that the prototyping stage is meant to set the foundation for successful production. The number of prototypes required can range from 2-4 for larger and more complex products to tens or even hundreds for smaller and simpler products. Each prototype may have a different purpose and take a different amount of time, so budgeting for each prototype is crucial to avoid overspending.
The Plastic Problem: 1960s to Now
You may want to see also
Choosing a prototyping partner
The cost of creating a plastic prototype varies depending on the complexity of the design and the chosen materials. Simple plastic prototypes can cost just under $15, but the price can increase to between $10,000 and $100,000 if an injection mould is required.
When choosing a prototyping partner, it is important to consider the type of prototype required, the level of service needed, and the expertise and resources offered by the partner.
The first step is to determine the type of prototype that best suits your needs. There are three main types of prototypes: proof-of-concept prototypes, which are used to validate an idea or part feasibility and do not need to be exact replicas of the final product; visual prototypes, which offer a final representation of the plastic part but do not need to function as the final product; and functional prototypes, which portray the desired final product in terms of both material and mechanics.
The next consideration is the level of service required. Some manufacturers offer quick, low-cost resources, while others provide full-service options, including face-to-face consultations, quick issue resolution, and high-volume capabilities. It is important to assess your specific needs and choose a partner who can meet those needs effectively.
Finally, it is crucial to select a prototyping partner with the necessary expertise and resources to produce high-quality prototypes. Look for a partner with experience in plastic prototyping, access to advanced technologies, and a track record of successful collaborations. Ensure that they can provide the required engineering resources and technologies to produce production prototypes, as this can add value and cost savings by getting your product to market quicker.
Additionally, consider the interface options provided by the prototyping partner. Choose a partner who offers a friendly and easy-to-use interface, especially if your prototype needs are complex and require personalized, face-to-face guidance and expertise. A partner who can provide step-by-step service and recommendations through various communication channels will ensure a smooth collaboration.
By carefully considering these factors, you can make an informed decision when choosing a prototyping partner, setting your project up for success and ensuring a positive collaboration experience.
The Plastic Problem in Margarine: What's the Truth?
You may want to see also
Prototype uses
The cost of creating a plastic prototype varies depending on the complexity of the product and the chosen manufacturing method. Simple plastic prototypes can cost as little as $15, but the price can increase to $10,000 to $100,000 if injection moulding is required.
Plastic prototypes are essential in various industries, including medical, dental, and consumer electronics. Here are some common uses for plastic prototypes:
Visual Representation: Visual prototypes offer a final representation of the plastic part without requiring the functionality of the final product. 3D printing is commonly used for visual prototypes as it is a fast and cost-effective method.
Functional Testing: Functional prototypes portray the desired final product in terms of material and mechanics. These prototypes are used to test the product design before mass production. FDM 3D printing is a popular choice for functional prototypes as it offers strength and resolution, making it suitable for medical, dental, and consumer electronics applications.
Design Iteration and Improvement: Prototypes allow designers to evaluate the form, fit, and function of a product. With each iteration, the design improves, and functional prototypes become more refined.
Customer and Investor Engagement: Plastic prototypes help manufacturers showcase their products to potential investors and customers. This early feedback helps gauge customer interest and refine the product before its official launch.
Master Model Creation: In vacuum casting, a master model is created using CNC machining or 3D printing. This master model is then used to form silicone-based cutting moulds, which are filled with molten plastic to create the final prototype.
The versatility of plastic prototyping methods allows manufacturers to choose the ideal procedure for their specific needs, whether it's visual representation, functional testing, or customer engagement.
Ontario's Plastic Recycling Efforts: How Effective Are They?
You may want to see also
Prototype creation methods
The cost of creating a plastic prototype varies depending on the complexity of the product and the chosen manufacturing method. Simple plastic prototypes can be created for under $15, but the cost increases significantly if injection moulding is required, ranging from as low as $10,000 to around $100,000.
Creating a prototype is a necessary stage in product development, and various manufacturing technologies can be used to produce a plastic prototype. Here are some common prototype creation methods:
3D printing is a widely used manufacturing technology for plastic prototyping, offering speed, affordability, and flexibility. Fused Deposition Modelling (FDM) is the most common 3D printing technique, building objects layer by layer. FDM 3D printing can produce high-resolution and high-strength prototypes, depending on the chosen materials. Industrial-grade FDM printers can be used to create colourful prototypes with materials like Polylactic Acid (PLA), or stronger materials like polycarbonate, Nylon, and ABS.
Stereolithography (SLA) is another 3D printing technique that uses a high-powered laser to solidify plastic resin materials. This method is suitable for prototyping medical, dental, and consumer electronics applications.
Selective Laser Sintering (SLS) is a similar process to SLA, using a high-powered laser to create plastic prototypes.
Computer Numerical Control (CNC) machining is a versatile method that allows for the creation of various surface finishes, such as polishing, painting, and powder coating. CNC machining offers tight tolerances, threads, and undercuts, and can produce plastic prototypes with close mechanical properties to the injected part. It is particularly useful for testing the form, fit, and function of injection-moulded parts without producing injection mould tooling.
Injection moulding is a popular method for full-scale production and prototyping, where plastic resin is mixed into a heated barrel and forcefully injected into a metal die. This method is ideal for limited plastic parts prototype production runs.
Vacuum casting is a manufacturing tool that uses silicone-based cutting moulds to create detailed replicas of a master model. It is a three-step process that starts with creating a CAD design into a master model through 3D printing or CNC machining. The vacuum casting method works with various materials, from opaque to transparent, and the moulds can be reused to make about 25 plastic prototypes.
When creating a plastic prototype, it is important to consider the specific requirements, such as the desired functionality and appearance, and the available materials. Collaborating with a custom manufacturing company or prototype developer can increase the chances of acquiring the right materials and a better-quality prototype.
Singapore's Annual Plastic Waste: A Troubling Overview
You may want to see also
Prototype timeline
The timeline for creating a plastic prototype will vary depending on the complexity of the design, the chosen manufacturing method, and the number of iterations required. Here is a general step-by-step guide to give you an idea of the process and timeline for creating a plastic prototype:
- Design Phase: Begin by creating a Computer-Aided Design (CAD) model of your proposed plastic part. This digitally represents how the plastic part should appear and function, including how the plastic components assemble. This step is crucial in helping you prepare for the next stages of prototyping. The duration of this phase will depend on the complexity of your design and the availability of skilled CAD designers.
- Choose Prototyping Method: Select the most suitable prototyping method for your specific needs. Common methods include 3D printing, vacuum casting, injection molding, and CNC machining. The chosen method will impact the speed, cost, and quality of your prototype. For example, 3D printing is often the fastest and most cost-effective option for early-stage prototypes, while injection molding may be more suitable for high-resolution prototypes.
- Create Master Model: If you choose vacuum casting as your prototyping method, you will first need to create a master model. This step ensures that your silicone molds accurately represent the desired shape and details of your final product. The time required for this step will depend on the complexity of your design and the chosen manufacturing process.
- Create Silicone Molds: After completing the master model, you will need to create silicone-based cutting molds. These molds will be used to form the final plastic prototype. The creation of these molds can take time, as you need to ensure they are precise and accurate.
- Prototype Creation: Now, you can begin creating your plastic prototype. Inject the molten plastic or raw material into the mold cavity using a vacuum bell jar. The solidification process usually takes around 30-40 minutes for plastic prototypes. However, the total time for this step may vary depending on the number of prototypes you create and any potential issues encountered.
- Testing and Iteration: Once you have a physical prototype, it's time for testing and validation. This includes engineering validation testing (EVT), design validation testing (DVT), and production validation testing (PVT). The duration of this phase will depend on the complexity of your design and the number of iterations required to reach a functional and reliable product.
- Refinement and Finalization: Based on the results of the testing phase, you may need to refine and iterate your design. This could involve making changes to the CAD model, creating new master models, and producing additional prototypes for further testing. Each iteration will add time to your overall timeline, but it is crucial for ensuring a high-quality final product.
- Mass Production: After you are satisfied with the testing and refinement process, you can move forward with mass production. The duration of this phase will depend on the quantity of products being manufactured and the capabilities of your chosen manufacturing partner.
It is important to note that the above timeline is a general overview and that each project is unique. The specific steps, duration, and sequence may vary depending on your specific product and requirements. Additionally, it is common to work on multiple iterations and prototypes simultaneously to optimize the timeline and make informed decisions.
The Weight of Plastic Golf Balls: How Much?
You may want to see also
Frequently asked questions
The cost of a plastic prototype depends on various factors, such as the complexity, scale, and type of prototype required. A simple 3D-printed plastic prototype can cost anywhere from $30 to $5,000, while more complex prototypes with advanced features can range from $1,500 to over $20,000.
Several factors influence the cost of a plastic prototype. These include the size and complexity of the design, the materials used, the number of prototypes needed, and the manufacturing process chosen.
The time required to create a plastic prototype depends on its complexity and scale. Simple prototypes may take a few hours, while complex and large prototypes can take months or even years. On average, the timeline for developing a prototype is between one and three months.
Yes, besides 3D printing, other methods such as vacuum casting and injection molding are commonly used for plastic prototyping. Vacuum casting involves creating a master model and then using silicone molds to form detailed replicas. Injection molding is another technique where molten plastic is injected into a mold to create the prototype.