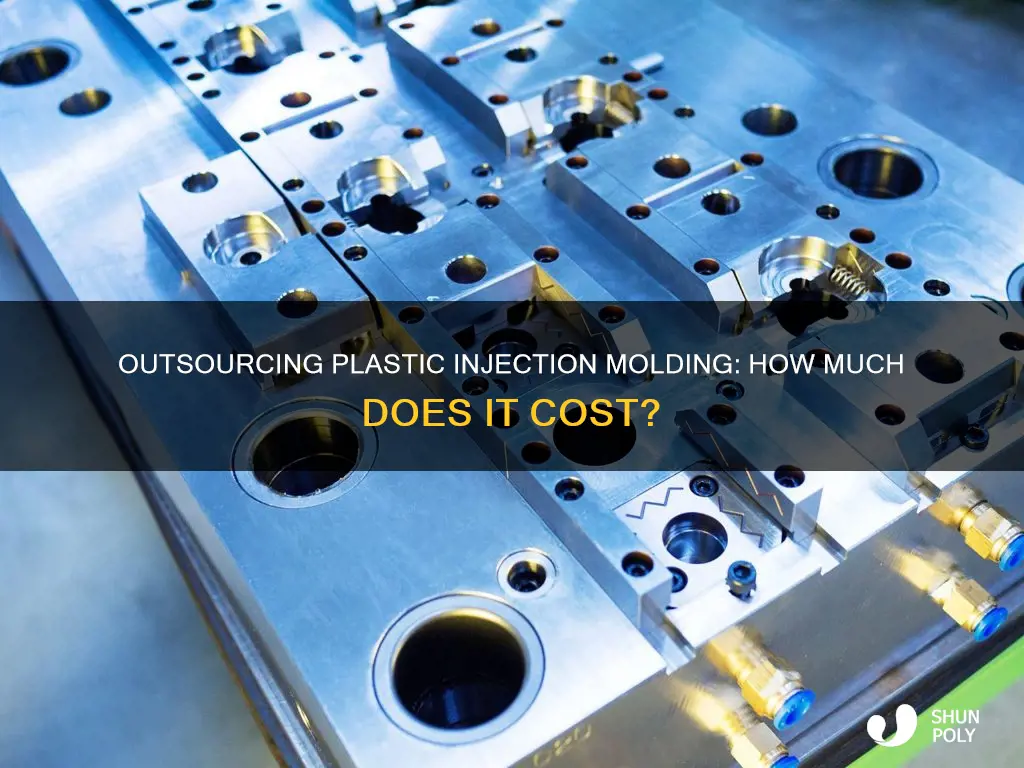
Plastic injection molding costs can vary widely, ranging from $100 for simple 3D-printed molds to over $100,000 for complex steel molds used in high-volume production. The cost depends on factors such as mold complexity, production volume, and material choice. For example, the price of a small and simple single-cavity plastic injection mold usually falls between $1,000 and $5,000, while very large or complex molds may cost upwards of $80,000. Outsourcing plastic injection molding services can be a cost-effective option, allowing clients to source the lowest cost for the required parts and minimize variable production costs.
Characteristics | Values |
---|---|
Cost range | $100 to $100,000+ |
Simple single-cavity mold cost | $1,000 to $5,000 |
Large or complex mold starting cost | $25,000 |
Average cost | $12,000 |
Desktop injection molding machine cost | $50,000 to $100,000+ |
Industrial injection molding equipment cost | $50,000 to $200,000 |
Plastic resin cost | $2 to $20 per pound |
Plastic resin pellet cost | $1 to $5 per kg |
Labor cost | $10,000 to $20,000 |
Total cost of the injection-molded process | $15,000 to $30,000 |
Production volume | 5,000 to 10,000 units |
What You'll Learn
Cost of materials
The cost of materials for plastic injection moulding varies depending on the type of plastic resin chosen, the size of the mould, and the complexity of the design. Plastic resins can range in price from $2 to $20 per pound, or from $1 to $5 per kg. The more complex the design, the more material is required, and the higher the cost. For example, highly complex designs with multiple cavities and a high-quality finish will result in extra costs.
The size of the mould is also a factor, as larger parts will consume more materials and increase costs. Additionally, the choice of mould material can impact the overall cost. While moulds are typically made from steel or aluminium, steel moulds used in high-volume production can cost over $100,000.
It is worth noting that the cost of materials is just one aspect of the overall injection moulding cost. Other factors, such as labour, setup, and maintenance, can also contribute significantly to the total expense.
For low-volume production, manufacturers often create moulds in-house using 3D-printed polymer resin, which is a cheap and efficient option. On the other hand, medium to high-volume production may require outsourcing mould production and the moulding process, which can increase costs.
Overall, the cost of materials for plastic injection moulding can vary widely depending on the specific requirements and scale of the project.
Plastic Crushing Machines: How Much Do They Cost?
You may want to see also
Labour costs
For low-volume production, typically between 100 to a few thousand parts, manufacturers often handle the moulding process in-house without the need for sophisticated machinery. This reduces labour costs as the process can be completed within three days using affordable 3D-printed polymer resin or rapid tooling methods.
However, as production volume increases to several thousand parts, outsourcing becomes more common. At this scale, the labour costs associated with mould production and the technical expertise required for more complex designs contribute to the overall expense. For example, a production volume of 5,000 to 10,000 units using thermoplastic materials can result in total labour costs ranging from $10,000 to $20,000.
The labour costs in injection moulding are influenced by specific setup requirements, such as machine setup and configuration for each stage of the process. Additionally, the choice of materials can impact labour expenses. Using standard materials that the moulder already carries is usually more cost-effective than special orders.
Outsourcing plastic injection moulding is often chosen to reduce labour costs by leveraging the expertise and equipment of specialised partners. This allows companies to access skilled labour and modern equipment without incurring the full costs of purchasing and maintaining their own machinery.
Plastic Waste: Global Comparison of Country Contributions
You may want to see also
Cost of equipment
The cost of equipment for plastic injection moulding varies depending on the scope and intricacy of the project. Injection moulding equipment costs can range from $100 for simple 3D-printed moulds to over $100,000 for complex steel moulds used in high-volume production. The price of a mould can also vary depending on the size of the product being created, with larger products requiring larger tooling and a larger mould machine, which can increase costs.
The type of plastic selected will also impact the upfront material expenses, as well as the durability, performance, and production efficiency of the final product. High-performance plastics, for example, may initially be more expensive but can reduce maintenance and replacement costs over time.
The cost of labour is another factor to consider when calculating the overall cost of equipment. For a production volume of 5,000 to 10,000 units using thermoplastic materials, the total labour cost can range from $10,000 to $20,000.
Additionally, the cost of creating a mould tool can be influenced by the design and the material used. For instance, a mould made of steel will likely be more expensive than one made of a different material.
It is worth noting that outsourcing injection moulding can be more cost-effective than purchasing the equipment, as it eliminates the costs of buying and maintaining machines. By partnering with a trusted manufacturer, companies can access cutting-edge equipment and skilled staff, resulting in lower costs and higher quality.
Marietta Facelift: Cost and Surgeon Expertise
You may want to see also
In-house vs. outsourced production
The cost of plastic injection molding varies depending on the project's scope and intricacy. Simple 3D-printed molds can cost as little as $100, while complex steel molds for high-volume production can exceed $100,000. The cost of the mold itself typically ranges from $1,000 to $5,000 for a small, simple single-cavity mold, while large or complex molds can cost upwards of $25,000. The price per unit decreases as the number of units produced increases.
When deciding between in-house and outsourced production for plastic injection molding, there are several factors to consider:
In-house Production
In-house production provides direct control over the manufacturing process, allowing you to avoid management costs associated with outsourcing. It also leverages your team's expertise and knowledge of your product. However, producing in-house may require heavy investment in new equipment and employees to meet design and production requirements. Additionally, your team's capacity may become a limiting factor, especially when there is a large influx of new business.
Outsourced Production
Outsourcing plastic injection molding can provide access to cutting-edge equipment and highly skilled, experienced staff dedicated solely to injection molding. It offers cost savings, as labor and fixed costs are typically lower than in-house production. Outsourcing also allows you to utilize the expertise and insights of specialized injection molding companies, ensuring high-quality products. However, it is important to thoroughly evaluate potential suppliers by considering their portfolio, customer reviews, and quality assurance certificates.
In conclusion, both in-house and outsourced production have their advantages. In-house production provides control and leverages internal expertise, while outsourced production offers cost savings, specialized expertise, and access to advanced resources. The decision should be made based on a thoughtful consideration of the organization's vision and goals, as well as capacity constraints, ensuring that the chosen option aligns with its strategic objectives.
The Value of Recycled Plastic: Worth a Fortune?
You may want to see also
Complexity of design
The cost of plastic injection moulding depends on several factors, one of the most important being the complexity of the design. The more complex the design, the more expensive it will be. This is because intricate designs require more research, development, and technical expertise, as well as additional manufacturing operations.
Design complexity is often associated with the number of cavities in the mould. For example, a simple single-cavity plastic injection mould usually costs between $1,000 and $5,000, whereas a 12-cavity "family" mould can cost $25,000 or more. The number of cavities is determined by the number of parts that need to be produced per cycle. For instance, a single-cavity mould is suitable for low-volume production, such as 1,000 washers per year, whereas a 12-cavity mould might be needed for producing 100,000 Xbox controllers per month.
The type of plastic resin used also influences the cost of complex designs. Plastic resins can range from $2 to $20 per pound, and the amount used depends on the size and complexity of the mould. Using cheaper resins can save money, but only if the manufactured part does not require any special qualities.
Other factors that contribute to the cost of complex designs include the use of advanced tools such as 3D printing, CNC, or EDM machining, as well as the need for high-strength steel to maintain high-quality, repeated use. Non-essential features like textures or high polish can also increase costs, as they require more cavities and demand more expertise.
Overall, the complexity of the design has a significant impact on the cost of plastic injection moulding. By understanding the relationship between design complexity and cost, businesses can make informed decisions and optimise their budgeting and production practices.
The Cost of Plastic Bedliners: How Much Do They Cost?
You may want to see also
Frequently asked questions
Outsourcing plastic injection molding can be cost-effective as it allows the client to source the lowest cost for the part required and minimize the variable costs of production. It also gives you access to the expertise of a company dedicated to injection molding services, allowing you to reap the benefits of their investments in equipment, training, and research.
The cost of outsourcing plastic injection molding depends on the scope and intricacy of the project. The price of a simple 3D-printed mold starts at $100, while complex steel molds used in high-volume production can cost over $100,000. The cost of the raw material for plastic resin pellets used in the injection molding process ranges from $1 per kg to $5 per kg. The total cost of the injection-molded process for a production volume of 5,000 to 10,000 units is estimated to be between $15,000 and $30,000.
The cost of outsourcing plastic injection molding is influenced by various factors, including the part size, complexity, material, anticipated quantities, and production volume. The number of cavities, surface finish, and undercuts required also play a role in determining the cost. The production process may also incur setup costs, repair costs, and operator costs.