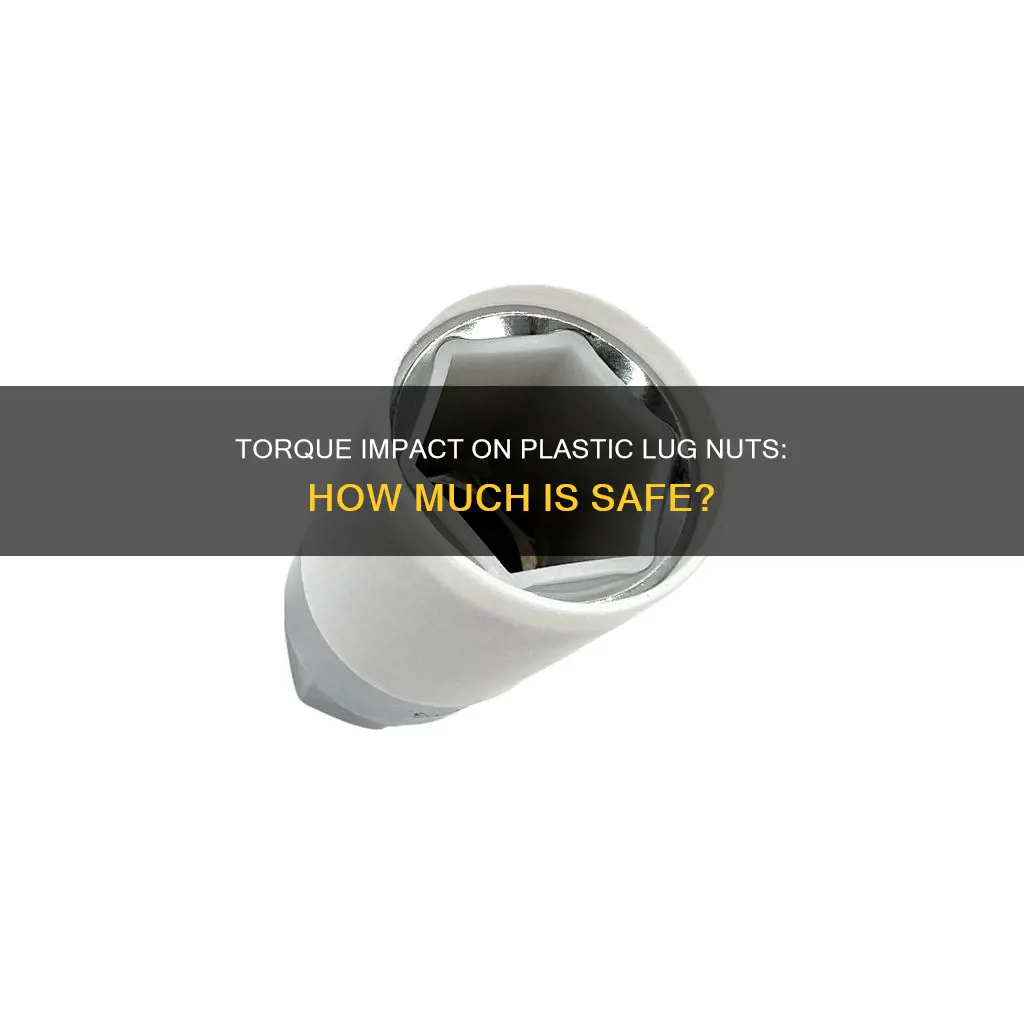
Lug nuts are essential for keeping your vehicle's wheels in place. They are small metal pieces that lock the wheels to the wheel studs on the hub using torque. The right amount of torque for lug nuts depends on the vehicle and the bolt or stud size. For example, older Hondas generally require 80 lb-ft of torque, while newer models require 100 lb-ft. It is important to note that over-torqued lug nuts can weaken the nut's tensile properties, making the bolts more susceptible to cracking or shearing. Therefore, it is recommended to use a torque wrench to tighten lug nuts by hand, rather than using a power impact wrench or torque stick. For plastic lug nut covers, it is recommended to tighten them by hand and then snug them with a socket, without cranking them down to avoid damage.
Characteristics and Values of Plastic Lug Nuts
Characteristics | Values |
---|---|
Torque | 40 ft/lbs |
Torque wrench size | 1/2" |
Torque wrench notches | Numbers with intervals of 10 |
Torque wrench adjustment | Twist the bottom |
Torque wrench usage | Manual |
Torque wrench sound | 'Click' |
Torque sequence | Specific to lug count |
Bolt size | 3/4" or 19mm |
Nut type | Shank or mag seat, E/T Ultra tapered mag seat, 60-degree tapered seat, 45-degree tapered seat, hex, spline, hex key |
Nut material | Metal |
Plastic cover tightness | Finger tight |
Plastic cover socket | Snug |
Rim settling | 50-100 miles |
Rim settling causes | Loosened lug nuts |
Over-torquing consequences | Warped brakes, wheel loss |
What You'll Learn
Torque recommendations depend on the lug nut thread size
Torque recommendations do depend on the lug nut thread size. The right torque for lug nuts generally depends on the lug nut's bolt or stud size. The first step is to measure the thread size by measuring the outside diameter of the wheel stud threads on your vehicle. Using a tape measure on a threaded stud is difficult, so it is suggested to use a dial caliper or digital caliper to increase accuracy.
Common thread diameters used for lug nuts in SAE sizes are 7/16, 1/2, 9/16 and 5/8 inches. Common metric thread diameters are 12 mm and 14 mm. To determine the thread pitch on SAE threads, you need to count the number of threads within a one-inch long section of the stud. The common thread pitch for SAE sizes is 11, 18, and 20 threads per inch, making the most common SAE thread sizes 7/16-20, 1/2-20, 9/16-18, 5/8-18, and 5/8-11. The common thread pitch for metric threads is 1.25 and 1.50 threads per millimeter, making the most common thread sizes 12 mm x 1.25, 12 mm x 1.50, and 14 mm x 1.50.
The right torque for lug nuts also depends on the vehicle. For example, Subarus require a torque of 65 ft-lb, while older Hondas require 80 ft-lb and newer ones 100 ft-lb. Most vehicles have lug nuts that require around 100 pound-feet of torque. However, it is always best to check the vehicle's manual to find out the exact specifications.
To properly torque lug nuts, a 1/2-inch drive torque wrench is suggested. The lug nuts should be torqued in two steps, starting at 40 ft/lbs of torque for the first step to get the wheel seated properly.
Profitable Plastic Bead Bracelets: Pricing for Sales
You may want to see also
Torque varies by vehicle
Torque varies not only by vehicle but also by the type of lug nut used. It is important to use the right amount of torque when installing lug nuts as it can be dangerous if they are not properly torqued. If the lug nuts are over-torqued, they can be weakened, making the bolts more susceptible to cracking, shearing, or separating from the lug. This can lead to warped brakes and even wheel loss.
To determine the correct torque for your vehicle, it is recommended to refer to the vehicle's manual or consult a professional. As a general guide, most vehicles require around 100 pound-feet of torque, but this can range from 65 lb-ft for Subarus to 170 lb-ft for sprinter vans. The torque required also depends on the lug nut's bolt or stud size, with larger bolts typically requiring higher torque values.
Different types of lug nuts include hex, spline, and acorn. Hex lug nuts are the most common type and can be installed or removed using easily available sockets or wrenches. Spline drive lug nuts are used to change the look or match a wheel style, and they require a specific socket for installation and removal. Acorn lug nuts are used on vehicles where a capped-off appearance is desired, such as hot rods, muscle cars, and show cars.
It is important to note that the type of lug nut seat also varies. Shank or mag seat lug nuts have a flat seat and typically require a washer between the lug nut and the wheel. Tapered seat lug nuts, on the other hand, help center the wheel as the lug nuts are tightened and provide a truer and more balanced assembly.
When torquing lug nuts, it is recommended to use a 1/2” drive torque wrench and follow a two-step process. The first step is to torque the lug nuts to around 40 ft/lbs to get the wheel seated properly. The final torque value will depend on the specific vehicle and lug nut thread size, as specified in the vehicle's manual or by a professional.
Plastic Palettes: Cost and Creative Possibilities
You may want to see also
Over-torquing can cause wheel loss
Torque is the force that causes an object to rotate about an axis. In the context of lug nuts, torque refers to the force applied to tighten or loosen them. The amount of torque required to tighten lug nuts depends on the type of lug nut and the application. For plastic lug nuts, it is generally recommended to tighten them by hand and then snug them up with a socket. Over-torquing plastic lug nuts can cause wheel loss and other issues.
Over-torquing plastic lug nuts can stretch the plastic, causing it to deform and no longer be certified for its load rating. This means that the lug nuts may not be able to hold the wheel securely, leading to wheel loss. Additionally, over-torquing can cause stress fractures in the plastic, which can also lead to sudden failure and wheel loss.
Furthermore, over-torquing plastic lug nuts can damage the wheel itself, especially if it is made of cheap aluminum. The stress exerted on the wheel can cause cracks or deformations around the lug nut holes, compromising the structural integrity of the wheel. This can lead to sudden wheel failure and loss during driving, posing a significant safety risk.
In addition to wheel loss, over-torquing plastic lug nuts can also cause damage to other components. The excessive force applied during over-torquing can transfer to the wheel bearing, creating a side load that the bearing was not designed to handle. This can lead to premature bearing failure and potential damage to the hub and seal.
To avoid over-torquing plastic lug nuts, it is important to follow the manufacturer's recommendations for torque values and tightening procedures. Using a torque wrench can help ensure that the lug nuts are tightened to the specified torque, reducing the risk of over-torquing. Additionally, it is crucial to inspect the lug nuts and wheels regularly for any signs of damage or deformation, ensuring the safety and reliability of the vehicle.
The Weight of 10mm Corrugated Plastic Sheets
You may want to see also
Torque wrenches are recommended
When installing plastic lug nuts, it is crucial to follow the proper procedures to ensure they are securely fastened. Firstly, ensure that the threads on the wheel studs are clean and free from dirt, grime, or metal chips, as these can interfere with accurate torquing. It is also important not to lubricate the threads or use any rust-proofing, as this can prevent a proper connection between the lug nut and the threads.
To install the lug nuts, first attach them by hand, and then use a manual torque wrench to tighten them further. A 1/2-inch torque wrench is commonly used for most wheels. When using a torque wrench, set the torque by twisting the bottom of the wrench. This may involve unscrewing the knob at the end of the wrench to adjust the torque. The notches near the end of the wrench's shaft will have corresponding numbers, allowing you to set the desired torque.
It is important to note that over-torqued lug nuts can be dangerous. Excessive torque can weaken the lug nut's tensile properties, making the bolts more susceptible to cracking, shearing, or separating violently from the lug. This can lead to issues such as warped brakes and wheel loss. Therefore, it is crucial to follow the manufacturer's recommendations for torque specifications and re-torqueing intervals.
Plastic Fumes: Understanding the Dangerous Exposure Risks
You may want to see also
Torque sticks are not recommended for re-torquing
Torque sticks are handy tools that can be used to quickly and accurately torque down wheel nuts and bolts. They are mounted between an impact gun and a socket and are made of sprung steel that stops sending torque to the socket when its limit is reached. While torque sticks can be useful in certain scenarios, they are not recommended for re-torquing.
One of the main reasons torque sticks are not ideal for re-torquing is accuracy concerns. Torque sticks can be affected by factors such as air pressure and the type of impact gun used, which can result in variations in the applied torque. Some users have also reported that torque can still be transferred to the hardware past the limit if it is being sent at a very high rate, rendering the torque stick ineffective.
Additionally, torque sticks are susceptible to variances and can lose their torque values over time. This means that they may not provide the same level of accuracy as a properly cared for and used torque wrench. While torque sticks can be calibrated to ensure accuracy, this defeats one of their main purposes, which is speed and convenience.
For these reasons, it is generally recommended to use a torque wrench for re-torquing. Torque wrenches allow for more precise control over the amount of torque applied and are less likely to result in over-tightening or under-tightening. They are also better suited for at-home wrenching, where speed is usually not a significant concern.
While torque sticks may be suitable for initial torquing, especially in high-volume production or motorsports settings, they are not the best choice for re-torquing. It is important to prioritize accuracy and safety when it comes to re-torquing, and a torque wrench is the tool that provides the necessary precision and reliability for this task.
The Food Industry's Plastic Problem: A Startling Expose
You may want to see also
Frequently asked questions
The right torque for lug nuts depends on the vehicle and the bolt or stud size. For example, Subarus are 65 ft-lb, Hondas are generally 80 ft-lb, and Toyotas are around 80 ft-lb. Most vehicles require around 100 pound-feet of torque, but some require more or less. It is important to refer to your vehicle's manual to find the exact specifications.
Over-torqued lug nuts are stretched too much by pressure, causing the bolts to crack, shear, or separate violently from the lug. This can lead to warped brakes due to uneven load distribution and even wheel loss.
First, ensure that the threads on your wheel studs are clean. Then, attach each lug nut by hand, and use a manual torque wrench to tighten until you hear a 'click' sound, indicating that the correct torque has been reached.