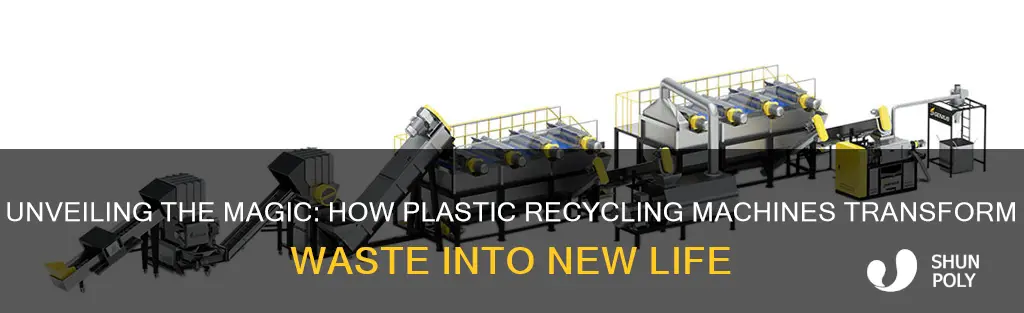
Plastic recycling machines are essential tools in the process of transforming waste plastic into reusable materials. These machines play a crucial role in the recycling industry by efficiently sorting, cleaning, and processing plastic waste. The process begins with the collection of various types of plastic, which are then fed into the recycling machine. Inside, advanced technologies, such as infrared or near-infrared spectroscopy, are used to identify and separate different types of plastics based on their unique molecular structures. Once sorted, the plastics are cleaned to remove contaminants, and then shredded or granulated into smaller pieces. These pieces are then melted and molded into new products, completing the recycling cycle. Understanding the inner workings of these machines is key to optimizing the recycling process and promoting a more sustainable approach to waste management.
What You'll Learn
- Feed Preparation: Plastic waste is sorted, cleaned, and shredded to prepare it for the recycling process
- Melting and Extrusion: Plastic is melted and extruded into a continuous strand, which is then cooled and cut into pellets
- Pelletizing: The molten plastic is shaped into small, uniform pellets, the raw material for new products
- Washing and Drying: Plastic waste is washed to remove contaminants, then dried to prevent moisture-related issues
- Quality Control: The recycled plastic is tested for purity and consistency to ensure it meets industry standards
Feed Preparation: Plastic waste is sorted, cleaned, and shredded to prepare it for the recycling process
The initial stage of the plastic recycling process is crucial as it sets the foundation for the entire recycling cycle. This stage involves meticulous preparation to ensure the plastic waste is in a suitable form for the recycling machine. The process begins with sorting, where plastic materials are separated based on their types and qualities. This sorting is essential as different types of plastics have varying recycling methods and applications. For instance, PET (polyethylene terephthalate) and HDPE (high-density polyethylene) are commonly recycled and have specific uses, while others like PVC (polyvinyl chloride) might require different processing. Sorting can be done manually or through automated systems, where sensors and optical scanners identify the plastic types.
Once sorted, the plastic waste undergoes a cleaning process to remove any contaminants. This step is vital as it ensures the purity of the recycled material and prevents any potential issues during the recycling process. Cleaning involves removing labels, caps, and other non-plastic components, as well as eliminating any dirt, dust, or residual chemicals. This can be achieved through washing the plastic items with water and detergents, followed by drying to remove moisture. Advanced cleaning methods might include using air classifiers to separate plastics based on their density or employing magnetic separators to remove any ferrous materials.
After cleaning, the plastic waste is prepared for the shredding process. Shredding is a critical step as it reduces the size of the plastic materials, making them more manageable for the recycling machine. The shredded plastic can then be further processed into smaller particles or flakes, which are easier to handle and transport. Shredding machines use various techniques, such as single-shaft or double-shaft shredders, to break down the plastic waste into uniform or irregular shapes, depending on the desired output. The shredded plastic is then sorted again, this time by size, to ensure consistency in the final recycled product.
The preparation of feed for the recycling machine is a meticulous and detailed process, requiring careful sorting, cleaning, and shredding. These steps are essential to ensure the efficiency and effectiveness of the recycling process, ultimately contributing to the production of high-quality recycled plastic materials. Each step is designed to optimize the recycling cycle, making it an environmentally friendly and sustainable process.
Apple Sauce, Plastic Dilemma: Recycling or Not?
You may want to see also
Melting and Extrusion: Plastic is melted and extruded into a continuous strand, which is then cooled and cut into pellets
The process of recycling plastic begins with the collection and sorting of plastic waste. Once sorted, the plastic is prepared for the recycling machine. The first step in the recycling process is melting and extrusion. This is a crucial stage where the plastic is transformed into a usable form.
In this process, the sorted plastic waste is fed into the machine, typically through a hopper. The plastic is then heated to its melting point, which varies depending on the type of plastic. For example, high-density polyethylene (HDPE) melts at around 265°C, while polypropylene (PP) melts at approximately 165°C. The heated plastic is then subjected to a high-pressure environment, causing it to melt and become a molten mass.
The molten plastic is then extruded through a die, which shapes it into a continuous strand. This strand is a semi-finished product and is carefully controlled to ensure it meets the required specifications. The extrusion process involves pushing the molten plastic through a shaped opening, creating a strand with a specific diameter and cross-sectional area. This strand is often referred to as a 'pellet' or 'flake' and is a key intermediate product in the recycling process.
After extrusion, the strand is cooled rapidly to solidify it. This is typically done by passing the strand through a cooling bath or by using air blowers to cool it down quickly. The cooling process is essential to prevent the strand from sticking together and to ensure it can be handled and stored easily. Once cooled, the strand is cut into small, uniform pellets using a cutting mechanism. These pellets are the final product of the melting and extrusion stage and are ready for further processing or use in manufacturing.
The quality and consistency of the recycled plastic pellets are vital for their subsequent use. The process of melting and extrusion requires precise control of temperature, pressure, and cooling to ensure the plastic is transformed into a high-quality product. This stage is a critical step in the recycling process, as it determines the success and efficiency of the entire recycling operation.
Seattle's Plastic 5: Unraveling Waste Management's Recycling Mystery
You may want to see also
Pelletizing: The molten plastic is shaped into small, uniform pellets, the raw material for new products
The process of pelletizing is a crucial step in the recycling of plastic, transforming the molten material into a usable form for manufacturing new products. This technique involves shaping the heated plastic into small, uniform pellets, which serve as the raw material for various industries. The process begins with the collection and sorting of plastic waste, ensuring that different types of plastics are separated to facilitate the recycling process. Once sorted, the plastic is cleaned to remove any contaminants, such as labels, caps, or other non-plastic materials.
After cleaning, the sorted plastic is shredded into small pieces, making it easier to process. These shredded pieces are then fed into a machine called a pelletizer, which is designed to melt and shape the plastic. The machine's heating system raises the temperature of the plastic to its melting point, allowing it to become a molten mass. This molten plastic is then extruded through a die, which is a small opening that controls the shape and size of the pellets. The die's design determines the size and uniformity of the pellets, ensuring they meet the required specifications.
As the molten plastic exits the die, it is cooled rapidly by air or water to solidify into small, solid pellets. This cooling process is essential to maintain the integrity and shape of the pellets. The pellets are then separated from the cooling medium and collected in a container. The size and quality of these pellets are critical, as they will be used as the raw material for various industries.
Pelletizing offers several advantages in the recycling process. Firstly, it provides a consistent and standardized form of plastic, making it easier to transport and store. These pellets can be easily handled and fed into manufacturing processes, ensuring a steady supply of raw material. Secondly, pelletizing allows for the creation of a product that is free from contaminants, as the cleaning and shredding processes remove any unwanted materials. This results in a higher-quality raw material, which can be used to produce new products with improved performance and durability.
In summary, pelletizing is a vital step in the recycling of plastic, converting the molten material into small, uniform pellets. This process ensures a consistent and clean supply of raw plastic for various industries. By shaping the molten plastic into pellets, recycling machines enable the production of new products, contributing to a more sustainable and circular economy. The efficiency and precision of pelletizing make it an essential technique in the recycling industry, allowing for the effective utilization of plastic waste.
Eco-Friendly Guide: Transforming Plastic Lotion and Shampoo Containers into New Life
You may want to see also
Washing and Drying: Plastic waste is washed to remove contaminants, then dried to prevent moisture-related issues
The process of recycling plastic waste begins with the collection and sorting of various plastic materials. Once sorted, the plastic waste undergoes a series of cleaning and preparation steps to ensure it is ready for the recycling process. One crucial aspect of this preparation is washing and drying, which is essential to remove contaminants and ensure the quality of the recycled material.
Washing is a critical step to eliminate dirt, labels, and other foreign matter that may be attached to the plastic waste. This process typically involves the use of water and sometimes specialized cleaning agents. The plastic waste is fed into a washing machine or a series of conveyors that move the material through a series of tanks or drums filled with water. During this process, the contaminants are washed away, and the plastic is separated from any non-plastic materials, such as labels or caps. High-pressure water jets and mechanical brushes are often employed to ensure thorough cleaning.
After washing, the plastic waste must be dried to remove excess moisture. Moisture can lead to several issues during the recycling process. It can cause the plastic to become sticky or clump together, making it difficult to process and potentially leading to contamination. To address this, the wet plastic is directed into a drying system, which can vary depending on the type of plastic and the recycling method. One common method is using a series of heated drums or conveyors that gently move the plastic waste. The heat and movement help to evaporate the water, leaving behind a dry and clean material.
Drying is a critical step to ensure the plastic is free from moisture, which can cause problems during the recycling process. The dried plastic is then ready for the next stage, where it is shredded or granulated into small pieces or pellets, depending on the desired form of the recycled material. This process ensures that the plastic is in a consistent and usable state for manufacturing new products.
In summary, washing and drying are essential processes in plastic recycling to maintain the quality and purity of the recycled material. These steps remove contaminants and ensure that the plastic is ready for further processing, contributing to the overall efficiency and effectiveness of the recycling machine's operation. Proper washing and drying techniques are vital to producing high-quality recycled plastic products.
The Environmental Impact of Recycling Plastic: Is It Worth It?
You may want to see also
Quality Control: The recycled plastic is tested for purity and consistency to ensure it meets industry standards
Quality control is an essential step in the plastic recycling process, ensuring that the recycled material is of high quality and meets the required industry standards. This process involves rigorous testing and evaluation to guarantee the purity and consistency of the recycled plastic.
When the plastic waste is collected and sorted, it undergoes a series of quality checks. The first step is to inspect the material for any contaminants or impurities. This includes checking for non-plastic items such as metals, glass, or paper, which can compromise the integrity of the recycled product. Advanced screening techniques, such as magnetic separation and optical sorting, are employed to efficiently remove these foreign materials. Additionally, the plastic waste is examined for any visible defects, such as tears, burns, or discolored areas, which may affect the final quality.
Purity testing is then conducted to ensure that the plastic is free from any harmful substances. This involves analyzing the material for heavy metals, additives, and potential chemical contaminants. Various analytical techniques, such as inductively coupled plasma mass spectrometry (ICP-MS) and X-ray fluorescence (XRF) spectroscopy, are utilized to detect and quantify these impurities. The results are compared against industry standards to determine if the recycled plastic meets the required purity levels.
Consistency is another critical aspect of quality control. The recycled plastic must have uniform properties to ensure its usability in various applications. This involves testing the material's color, density, and molecular weight distribution. Color consistency is achieved through advanced sorting techniques, ensuring that similar-colored plastics are grouped together. Density measurements are taken to verify that the recycled plastic has the desired characteristics, often requiring the use of specialized equipment like density meters. Molecular weight analysis is performed to assess the distribution of polymer chains, ensuring a consistent and predictable structure.
Furthermore, the recycled plastic is often subjected to additional tests to evaluate its performance and durability. This includes impact resistance, tensile strength, and thermal stability assessments. These tests help determine the material's suitability for specific applications, ensuring it meets the required industry standards. By subjecting the recycled plastic to these comprehensive quality control measures, manufacturers can guarantee the production of high-quality, reliable materials, contributing to a more sustainable and efficient recycling process.
Garland's Plastic Recycling: Unveiling the Truth Behind Number 6
You may want to see also
Frequently asked questions
Plastic recycling machines use various processes to break down and process plastic waste. The initial step involves sorting the plastic materials based on their types and colors. This is crucial as different plastics have varying melting points and properties, which affects the recycling process. Once sorted, the plastics are cleaned to remove any contaminants like labels, caps, or non-plastic items. The cleaned plastics are then shredded or granulated to reduce their size, making them easier to handle and melt. The shredded plastic is heated and melted in a machine, and any remaining impurities are removed. Finally, the molten plastic is shaped and cooled to form recycled pellets or flakes, which can be used to produce new products.
There are several methods employed in the recycling of plastics, each with its own advantages and applications. One common method is mechanical recycling, which involves physically breaking down the plastic into smaller pieces and then reforming them into new products. This process is often used for single-material plastics like PET (polyethylene terephthalate) bottles. Another approach is chemical recycling, which utilizes chemical processes to break down plastics into their original building blocks, such as monomers or polymers. This method can handle a wider range of plastic types and is particularly useful for complex plastic waste streams. Advanced recycling techniques include gasification and pyrolysis, which convert plastics into synthetic gases or oils, offering a more sustainable way to recycle.
Plastic recycling machines offer numerous advantages in the recycling industry. They enable the efficient processing of large volumes of plastic waste, reducing the environmental impact of plastic disposal. These machines can handle various plastic types, ensuring a more comprehensive recycling process. However, challenges exist, such as the complexity of sorting and identifying different plastic types, which can impact the quality of the recycled material. Additionally, the energy consumption and costs associated with the recycling process can be significant. Despite these challenges, plastic recycling machines play a vital role in promoting sustainability, reducing landfill waste, and providing a source of raw materials for the manufacturing industry.