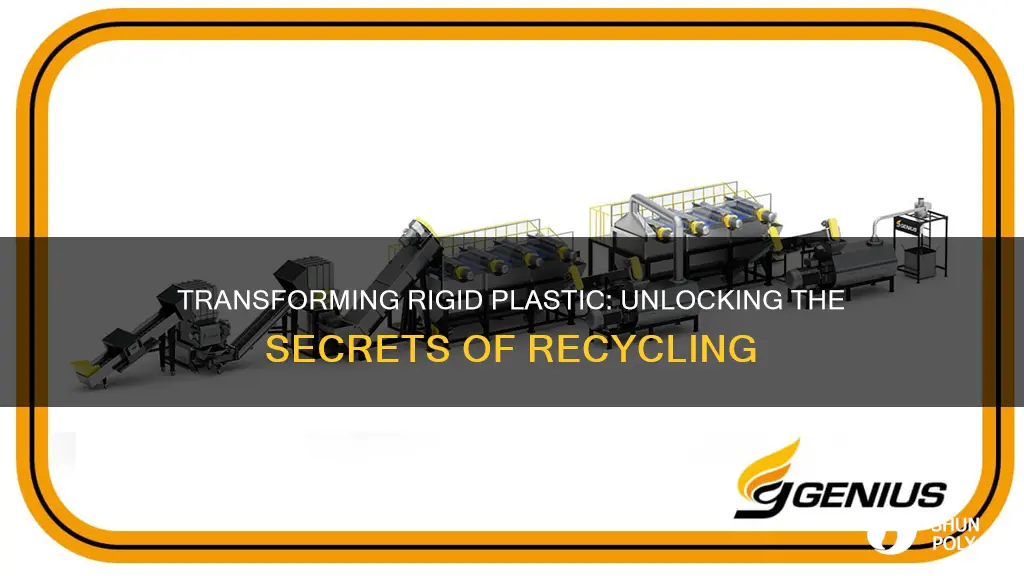
Rigid plastic, commonly found in packaging materials like bottles and containers, is a widely used and easily recyclable material. However, the recycling process for rigid plastic can be complex and varies depending on the type of plastic and local recycling infrastructure. This paragraph will explore the methods and challenges involved in recycling rigid plastic, highlighting the importance of proper sorting, cleaning, and processing to ensure the material can be effectively reused in new products.
What You'll Learn
- Collection and Sorting: Sorting rigid plastics by type and color for efficient recycling
- Cleaning and Shredding: Cleaning and shredding plastic waste to prepare for processing
- Melting and Molding: Melting down shredded plastic and molding it into new products
- Quality Control: Inspecting recycled plastic for quality and consistency before use
- End-of-Life Management: Planning for the end-of-life of recycled plastic products
Collection and Sorting: Sorting rigid plastics by type and color for efficient recycling
The process of recycling rigid plastics begins with a crucial step: collection and sorting. This initial phase is essential as it sets the foundation for efficient recycling and ensures that the materials are processed effectively. The collection process involves gathering rigid plastic items from various sources, including residential areas, commercial facilities, and public spaces. These items can include common household items like water bottles, milk jugs, detergent bottles, and even larger items such as storage containers and outdoor furniture. Proper collection methods are vital to ensure a steady supply of clean and sorted plastic waste.
Once collected, the plastic waste undergoes a meticulous sorting process. This step is critical as it categorizes the plastics into different types and colors, making the recycling process more efficient and effective. The sorting process typically involves manual labor and specialized equipment. Workers carefully examine each plastic item, identifying the type and color of the material. Rigid plastics are often categorized into several groups, such as PET (polyethylene terephthalate), HDPE (high-density polyethylene), and LDPE (low-density polyethylene), each with its own unique properties and recycling methods.
Color sorting is an essential aspect of this process. Rigid plastics can vary in color, and different colors may have distinct recycling pathways. For instance, clear and green PET bottles are often recycled together, while black HDPE containers might be sorted separately due to their unique chemical composition. This color-coding system ensures that the recycling process can be tailored to the specific requirements of each plastic type. By sorting plastics by type and color, recycling facilities can optimize their processes, reducing contamination and improving the overall quality of the recycled material.
Advanced recycling facilities employ automated sorting systems that use infrared sensors and optical scanners to identify and separate plastics based on their type and color. These machines can process large volumes of waste rapidly, improving efficiency. However, manual sorting still plays a significant role, especially in smaller facilities or when dealing with more complex plastic mixtures. Workers trained in this process carefully separate plastics, ensuring that each type and color is directed to the appropriate recycling stream.
Efficient collection and sorting are fundamental to the success of rigid plastic recycling programs. They enable the recycling industry to process plastics more effectively, reducing the environmental impact of plastic waste. Proper sorting also ensures that the recycled materials can be utilized in various applications, contributing to a circular economy. As such, communities and organizations must emphasize the importance of clean and sorted plastic waste to maximize the benefits of recycling and minimize the environmental footprint of rigid plastics.
Unveiling the Truth: Can Plastic Picture Frames Be Recycled?
You may want to see also
Cleaning and Shredding: Cleaning and shredding plastic waste to prepare for processing
The initial step in recycling rigid plastic is a crucial one: cleaning and shredding. This process ensures that the plastic waste is ready for further processing and helps maintain the quality of the recycled material. Here's a detailed breakdown of this essential stage:
Cleaning: Cleaning plastic waste is a critical process to ensure the quality and purity of the recycled material. It involves removing any contaminants, such as dirt, labels, and non-plastic items, that may be present in the waste stream. This step is crucial because contaminants can affect the performance and appearance of the recycled plastic. To clean the plastic, it is typically sorted by color and type to facilitate the process. For instance, PET (polyethylene terephthalate) bottles and HDPE (high-density polyethylene) containers are separated from each other. This sorting process can be done manually or through automated systems. Once sorted, the plastic waste is washed using specialized equipment. This washing process involves the use of water, detergents, and sometimes even ultrasonic cleaning systems to remove any remaining dirt and debris. It is important to ensure that all traces of contaminants are eliminated to maintain the integrity of the recycling process.
Shredding: After cleaning, the plastic waste is shredded into small pieces. Shredding is an essential step as it prepares the plastic for further processing and helps to reduce its volume. The shredding process can be done using various machines, such as shredders or granulators. These machines cut the plastic into uniform-sized pieces, typically in the form of flakes or pellets. The size of the shredded pieces depends on the intended use of the recycled plastic. For example, smaller, more uniform pieces are often preferred for manufacturing new plastic products, while larger flakes might be used for composite materials or as a raw material for 3D printing. Shredding also helps to increase the surface area of the plastic, making it more susceptible to chemical processes during recycling.
The cleaning and shredding process is a vital part of rigid plastic recycling, ensuring that the material is ready for the next stage of recycling, which may involve melting and reforming the plastic into new products. This step requires careful attention to detail and specialized equipment to handle the plastic waste effectively and efficiently.
Rothy's Recycled Revolution: Unveiling the Eco-Friendly Footwear
You may want to see also
Melting and Molding: Melting down shredded plastic and molding it into new products
The process of recycling rigid plastic begins with the collection and sorting of plastic waste. Once sorted, the plastic is shredded into small pieces, a crucial step to ensure the material can be effectively processed. These shredded pieces are then fed into a specialized machine designed for melting and molding.
The first step in this process is melting. Shredded plastic is placed in a high-temperature oven or furnace, where it is heated to a molten state. This requires precise temperature control to ensure the plastic is not burned or degraded. The molten plastic is then transferred to a mold, a critical stage where the material takes its new form.
Molding is a complex process that involves shaping the molten plastic into the desired product. This is typically done using a mold, which is a cavity or form that gives the plastic its final shape. The mold is heated to a specific temperature, allowing the plastic to flow into the mold's cavity. Once filled, the mold is cooled, and the plastic solidifies, taking on the shape of the mold. This step requires careful consideration of the cooling process to ensure the material retains its strength and durability.
After molding, the plastic parts are removed from the mold and may undergo additional processes such as trimming excess material, cleaning, and surface finishing. These steps ensure the final product meets the required specifications and quality standards. The newly formed products can then be used in various industries, contributing to a circular economy and reducing the demand for virgin plastic production.
This recycling method is particularly useful for rigid plastics, such as those used in packaging, containers, and automotive parts. By melting and molding, these materials can be transformed into new products, extending their lifespan and reducing environmental impact. The process is an essential part of sustainable waste management, offering a viable solution to the growing issue of plastic waste.
Unraveling the Journey: 6 Plastic Recycling Steps Revealed
You may want to see also
Quality Control: Inspecting recycled plastic for quality and consistency before use
Quality control is an essential step in the recycling process for rigid plastics, ensuring that the recycled material meets the required standards and can be reliably utilized in various applications. This process involves a series of inspections and tests to evaluate the quality and consistency of the recycled plastic. Here's an overview of the quality control procedures:
Visual Inspection: The first and most basic step is visual inspection. Trained personnel examine the recycled plastic for any visible defects or contaminants. This includes checking for color inconsistencies, foreign matter, debris, or any signs of damage during the recycling process. Visual inspection helps identify obvious issues and ensures that the plastic meets the basic quality requirements.
Material Sorting and Grading: Rigid plastics are often a mix of different types and colors. Quality control involves sorting and grading these materials to ensure consistency. This process separates the plastic into different categories based on type (e.g., PET, HDPE), color, and quality. Grading ensures that the recycled plastic is organized and can be used for specific applications, such as food-grade packaging or industrial products.
Physical Testing: Various physical tests are conducted to assess the properties of the recycled plastic. These tests include measuring the thickness, density, and flexibility of the material. For rigid plastics, hardness and impact resistance are crucial factors. Specialized equipment, such as durometers and impact testers, is used to determine the plastic's hardness and ability to withstand impact, ensuring it meets the required specifications.
Chemical Analysis: Advanced chemical testing is employed to analyze the composition of the recycled plastic. This step identifies any potential contaminants or additives that may affect the material's performance. Techniques like spectroscopy and chromatography are used to detect the presence of heavy metals, plasticizers, or other chemicals that could compromise the quality. Ensuring the plastic is free from harmful substances is vital for its safe and sustainable use.
Consistency and Batch Control: Consistency is key in quality control. Each batch of recycled plastic should be consistent in terms of color, thickness, and chemical composition. Quality control teams monitor and control the recycling process to maintain these standards. This includes precise temperature control during processing, ensuring that the plastic is not degraded or contaminated. Batch control also involves documenting and tracking each batch's properties for future reference and quality assurance.
By implementing these quality control measures, recyclers can guarantee that the rigid plastic they produce is of high caliber and suitable for various industrial and consumer applications. This process is crucial for building trust in recycled materials and promoting a circular economy.
Unrecyclable Plastics: Exploring the Limits of Recycling Technology
You may want to see also
End-of-Life Management: Planning for the end-of-life of recycled plastic products
The end-of-life management of recycled plastic products is a critical aspect of the circular economy, ensuring that these materials are handled responsibly and sustainably. When planning for the end-of-life of rigid plastic items, several key considerations come into play to minimize environmental impact and maximize resource recovery.
Firstly, it is essential to establish a comprehensive collection system. This involves designing products with end-of-life in mind, incorporating features like disassembly, modularity, and the use of easily recyclable materials. For instance, rigid plastic packaging can be designed with removable parts, allowing for individual components to be recycled separately. Implementing deposit-return schemes or providing convenient collection points can significantly improve the efficiency of plastic waste collection.
Once collected, the plastic waste undergoes processing to be transformed into raw materials. This stage includes sorting, cleaning, and shredding the plastic to prepare it for recycling. Advanced technologies, such as near-infrared (NIR) spectroscopy, can be employed to identify and separate different types of plastics, ensuring a more efficient and pure recycling process. The sorted plastics are then washed, dried, and ground into small pellets, which can be used as feedstock for new products.
The next step is to develop a robust recycling infrastructure. This involves establishing partnerships with recycling facilities and ensuring they have the necessary equipment and expertise to process the collected plastic effectively. It is crucial to have a well-connected network of recycling centers to handle the volume of plastic waste generated. Additionally, investing in research and development to improve recycling technologies and processes can lead to higher-quality recycled materials.
When planning for the end-of-life of recycled plastic products, it is vital to consider the entire lifecycle. This includes designing products with recyclability in mind, ensuring that they can be easily disassembled and processed. Manufacturers should also focus on reducing the use of additives and chemicals that may hinder the recycling process. By promoting a closed-loop system, where products are designed for disassembly and reuse, or recycled into new products, the environmental impact of plastic waste can be significantly reduced.
In summary, effective end-of-life management for recycled plastic products requires a holistic approach. It involves designing products with recyclability, establishing efficient collection systems, investing in advanced recycling technologies, and fostering collaboration between various stakeholders. By implementing these strategies, the plastic industry can move towards a more sustainable future, minimizing waste and maximizing the value of recycled materials.
Unraveling Minneapolis's Plastic Recycling Mystery: 5 Key Insights
You may want to see also
Frequently asked questions
Rigid plastic recycling involves a series of steps to process and transform used plastic items into new products. It typically begins with the collection of plastic waste, which is then sorted based on the type of plastic (e.g., PET, HDPE, LDPE). The sorted plastic is cleaned to remove contaminants, and the material is ground into small pieces called flakes. These flakes are further processed to remove any remaining impurities, and then they are melted and molded into new shapes, creating a raw material that can be used for manufacturing.
To recycle rigid plastic, ensure that the items are clean and dry. Remove any non-plastic components like caps, labels, or non-plastic parts. Rinse the plastic items to eliminate food residue or other contaminants. Flatten or break down large items to save space in recycling bins. Properly sorting rigid plastics by type (resin identification code) is also crucial for efficient recycling.
Not all rigid plastics are recyclable in every recycling program. Common types like PET (1), HDPE (2), and LDPE (4) are widely accepted. However, some plastics like polystyrene (6) and certain types of plastic packaging may have limited recycling options. Always check with your local recycling guidelines to understand what types of rigid plastics are accepted in your area.
Recycled rigid plastic can be transformed into various new products. It can be used to create new containers, bottles, furniture, automotive parts, construction materials, and even clothing fibers. The process involves reprocessing the plastic flakes into pellets, which are then used by manufacturers to produce new items. Recycling rigid plastic helps reduce the demand for virgin plastic production and minimizes environmental impact.
It's best to avoid recycling rigid plastic packaging with food residue. While the plastic itself can be recycled, food waste can contaminate the process and make the recycled material unsuitable for food-grade applications. Rinse the packaging thoroughly to remove any food particles before recycling. If the plastic is heavily soiled, it might be better to dispose of it in the regular trash to prevent contamination.