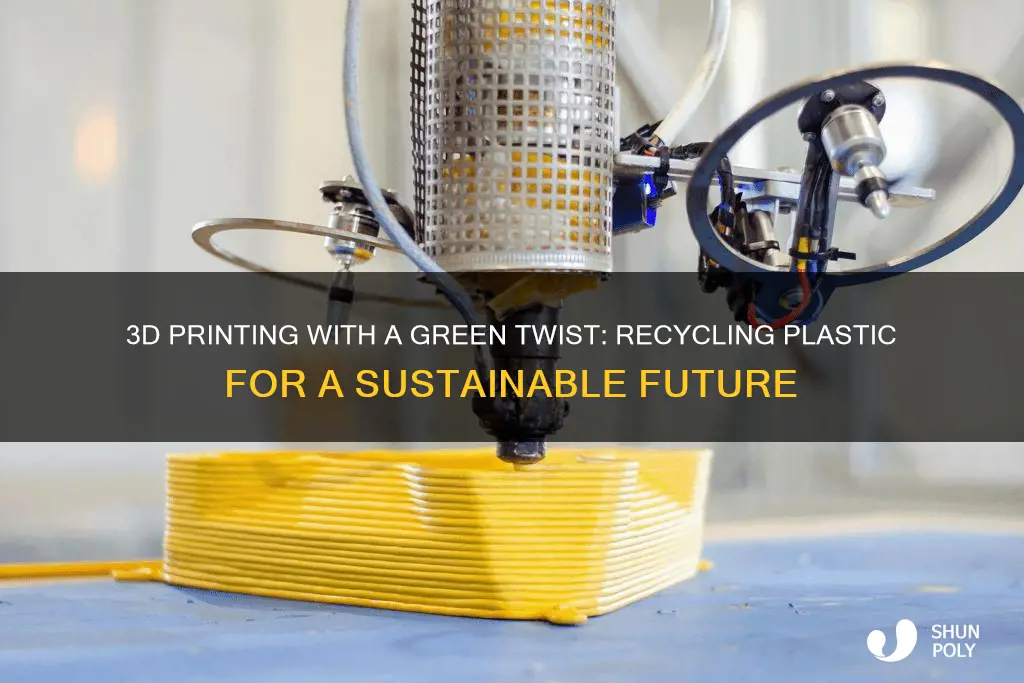
3D printing with recycled plastic is an innovative and sustainable practice that can significantly reduce waste and promote environmental conservation. This guide will explore the process of transforming used plastic materials into 3D printing feedstock, covering various methods and techniques to ensure a successful and eco-friendly 3D printing experience. From collecting and sorting plastic waste to selecting the right filament and optimizing print settings, we'll provide a comprehensive overview to help you create high-quality prints while contributing to a greener future.
What You'll Learn
- Material Selection: Choose recycled plastics suitable for 3D printing, considering strength, flexibility, and ease of printing
- Filtration: Use filters to remove contaminants, ensuring clean, consistent feedstock for optimal print quality
- Bed Leveling: Adjust the print bed for accurate layer adhesion, preventing warping and improving print stability
- Nozzle Temperature: Optimize temperature settings for specific recycled plastics to achieve desired print quality and material flow
- Support Structures: Design and print support structures to aid complex shapes, ensuring easy removal after printing
Material Selection: Choose recycled plastics suitable for 3D printing, considering strength, flexibility, and ease of printing
When it comes to 3D printing with recycled materials, the choice of plastic is crucial for achieving the desired mechanical properties and print quality. Here's a guide to selecting the right recycled plastics for your 3D printing projects:
ABS (Acrylonitrile Butadiene Styrene): ABS is a popular choice for 3D printing, especially for its balance of strength and impact resistance. It has a relatively high melting point, making it suitable for printing at temperatures around 250°C. Recycled ABS can be a cost-effective option, but it may require more precise temperature control during printing to avoid warping. This material is known for its durability and is often used in applications where impact resistance is essential.
PETG (Polyethylene Terephthalate Glycol-modified): PETG is a versatile and easy-to-print plastic that offers a good combination of strength, flexibility, and impact resistance. It has a lower melting point compared to ABS, typically around 220-240°C, making it more forgiving for beginners. Recycled PETG is an excellent choice for those seeking a balance between performance and ease of use. It is also known for its excellent layer adhesion, reducing the chances of warping.
HIPS (Hydroxyethyl Methacrylate Styrene): HIPS is a great option for those looking to print with recycled materials while maintaining a high level of impact resistance. It is often used as a support material in 3D printing, especially for overhangs and complex geometries. HIPS has a lower melting point, around 230°C, which makes it easier to print but requires careful handling to prevent warping.
Recycled PLA (Polylactic Acid): PLA is a biodegradable plastic that is widely used in 3D printing. While PLA is not typically recycled in the same way as ABS or PETG, using recycled PLA can still provide environmental benefits. It offers good printability, with a melting point of around 185-210°C. Recycled PLA may have slightly different properties than its virgin counterpart, so it's essential to consider the specific requirements of your project.
When selecting recycled plastics, consider the following factors: strength and durability, flexibility and impact resistance, ease of printing and bed adhesion, and the specific application or end-use of the 3D-printed object. Each plastic has its advantages and trade-offs, so choosing the right one will depend on your project's unique needs. Additionally, ensure that the recycled materials you source are of high quality and free from contaminants to achieve the best results in your 3D printing endeavors.
Recycling Plastic: A Sustainable Rock Cycle in Action
You may want to see also
Filtration: Use filters to remove contaminants, ensuring clean, consistent feedstock for optimal print quality
When it comes to 3D printing with recycled plastic, ensuring a clean and consistent feedstock is crucial for achieving optimal print quality. Contaminants such as dust, debris, and other foreign particles can negatively impact the printing process and the final product. Here's a detailed guide on how filtration can be an essential step in your 3D printing workflow:
Understanding the Importance of Filtration:
Before diving into the technical aspects, it's essential to grasp why filtration is necessary. Recycled plastic often contains various impurities, including small pieces of non-plastic materials, fibers, and even moisture. These contaminants can lead to several issues during printing. For instance, dust and debris might clog the nozzle, causing blockages and inconsistent extrusion. Foreign particles can also affect the mechanical properties of the printed object, making it weaker or more prone to defects. By implementing filtration, you create a clean environment for your 3D printer, ensuring better print quality and potentially reducing the need for post-processing.
Types of Filters and Their Applications:
There are several types of filters available for 3D printing, each serving a specific purpose:
- Mesh Screens: These are commonly used in the recycling process and can be placed in front of the feedstock container. Mesh screens typically have small openings that allow plastic flakes or pellets to pass through while retaining larger contaminants. They are effective in removing visible debris and can be easily replaced or cleaned.
- Centrifugal Filters: This type of filter uses centrifugal force to separate contaminants from the plastic. It is particularly useful for removing fine particles and moisture. Centrifugal filters are often used in industrial settings but can also be adapted for home use with the right equipment.
- Air Filters: While not directly related to plastic feedstock, air filters are essential for maintaining a clean printing environment. They capture airborne particles that might otherwise contaminate the plastic or the printer's components. Regularly replacing air filters is crucial for long-term print quality.
Filtration Process:
Implementing filtration involves a few simple steps:
- Source Quality Recycled Plastic: Start by sourcing high-quality recycled plastic that has already undergone some initial cleaning processes. This ensures that the raw material is less likely to contain significant contaminants.
- Container Filtration: Place a mesh screen or a fine-mesh filter inside the container holding the recycled plastic. This filter should be positioned to catch any debris that might fall or be stirred up during the feeding process.
- Feeding and Maintenance: Regularly feed the filtered plastic into your 3D printer. As you use the plastic, maintain the filtration system by cleaning or replacing the filters as needed. This ensures that the feedstock remains clean and consistent.
- Air Filtration in the Workspace: Consider setting up an air filtration system in your printing workspace to capture any airborne contaminants. This is especially important in areas with poor ventilation or high levels of dust.
By incorporating filtration into your 3D printing routine, you'll notice improved print quality, reduced material waste, and potentially longer-lasting printer performance. It is a simple yet effective method to enhance the overall efficiency of your recycled plastic 3D printing projects. Remember, consistent maintenance and the right choice of filters will contribute to the success of your 3D printing endeavors.
Thermoset Plastics: Can They Be Recycled?
You may want to see also
Bed Leveling: Adjust the print bed for accurate layer adhesion, preventing warping and improving print stability
Bed leveling is a crucial step in 3D printing, especially when using recycled plastic, as it ensures accurate layer adhesion and helps prevent warping and other issues that can compromise the quality of your prints. Here's a detailed guide on how to adjust your print bed for optimal results:
Understanding the Importance of Bed Leveling:
Before diving into the process, it's essential to understand why bed leveling is so critical. When you 3D print, the plastic material needs to adhere to the build plate firmly to create a strong bond between layers. If the bed is not level, the first layer might not adhere properly, leading to warping, where parts of the print lift up from the bed during the printing process. This can result in distorted or failed prints. Proper bed leveling ensures that the plastic has a stable base, allowing for better layer-to-layer bonding and overall print quality.
Steps to Level Your Print Bed:
- Prepare Your Workspace: Start by ensuring your print bed is clean and free of any debris or old prints. Use a soft cloth or a brush to remove any loose particles. If you have a heated bed, make sure it's turned off and cooled down before proceeding.
- Leveling Tools: You'll need a precision tool to level the bed accurately. A simple and effective option is a straight edge or a ruler, preferably one with a length that covers the entire print bed. For more advanced users, a laser level or a bed leveling probe can provide even more precision.
- Initial Inspection: Place your straight edge across the print bed, running parallel to the bed's edges. Ensure it is as straight as possible. If you notice any gaps or unevenness, you'll need to adjust the bed accordingly.
- Adjusting the Bed: If the straight edge is not level, you'll need to adjust the bed's height. Most 3D printers have screws or knobs that allow you to raise or lower the bed. Turn the screws counterclockwise to lower the bed or clockwise to raise it. Make small adjustments at a time, ensuring the bed is level in both the front-back and left-right directions.
- Precision Leveling: For a more precise approach, use the leveling tool to check the bed's evenness at multiple points. Adjust the bed's height slightly at each point until you achieve a consistent and flat surface. This step is crucial for intricate prints or those requiring high precision.
Tips for Optimal Results:
- Always level your bed before each print job, especially if you've made adjustments to the bed's height.
- Consider using a bed adhesive or a thin layer of glue stick to improve layer adhesion, especially with recycled plastic, which can be more prone to warping.
- Regularly inspect and level your bed to maintain print quality, especially if you notice any warping or print failures.
- For advanced users, exploring bed leveling probes or software-based solutions can provide even more accurate adjustments.
By following these steps, you can ensure that your 3D prints using recycled plastic have excellent layer adhesion and stability, resulting in high-quality and successful prints. Remember, proper bed leveling is a fundamental practice in 3D printing that significantly contributes to the overall success of your projects.
Unraveling the Mystery: Can Plastic Egg Cartons Be Recycled?
You may want to see also
Nozzle Temperature: Optimize temperature settings for specific recycled plastics to achieve desired print quality and material flow
When it comes to 3D printing with recycled plastics, optimizing the nozzle temperature is a critical factor in achieving high-quality prints and ensuring the material flows smoothly through the extruder. Different types of recycled plastics have unique properties and melting points, so adjusting the temperature accordingly is essential. Here's a guide to understanding and fine-tuning nozzle temperature for various recycled plastics:
Understanding Plastic Properties: Start by researching the specific recycled plastic you are using. Each type of plastic has its own glass transition temperature (Tg), which is the temperature range where the material changes from a rigid, glassy state to a more pliable, rubbery state. For example, ABS (acrylonitrile butadiene styrene) has a Tg around 105°C, while PLA (polylactic acid) has a lower Tg of approximately 55-60°C. Knowing these temperatures is crucial for setting the right nozzle temperature.
Setting the Optimal Temperature: The general rule is to set the nozzle temperature slightly above the plastic's Tg to ensure proper melting and flow. For ABS, a temperature of 250-270°C is commonly used, while for PLA, 190-210°C is ideal. These temperatures provide a good balance between material flow and preventing overheating, which can lead to warping and other issues. It's important to note that these values are guidelines, and adjustments may be necessary based on your specific printer and filament.
Experimentation and Calibration: 3D printing with recycled plastics often requires some experimentation to find the perfect temperature settings. Start with the recommended temperatures for your chosen plastic and make small adjustments as needed. You can use calibration tools or software to monitor the temperature of the nozzle and adjust it accordingly. Fine-tuning the temperature will help you achieve consistent prints with minimal warping, cracking, or other defects.
Consider Environmental Factors: External factors like ambient temperature and humidity can also influence the nozzle temperature. In colder environments, you might need to increase the temperature slightly to compensate for the lower ambient temperature. Similarly, high humidity can affect the material's behavior, so monitoring these conditions and adjusting the temperature settings is beneficial.
Post-Processing and Quality Control: After printing, inspect the prints for any signs of imperfections or issues related to temperature. Check for warping, layer shifting, or poor surface finish. If you notice any problems, you may need to further adjust the temperature settings or consider other factors like bed adhesion and cooling fans. Regularly calibrating and optimizing the nozzle temperature will contribute to improved print quality and a more reliable 3D printing process with recycled materials.
Unraveling the Dirt-Resistant Magic of Recycled Plastic Clothing
You may want to see also
Support Structures: Design and print support structures to aid complex shapes, ensuring easy removal after printing
When 3D printing recycled plastic, support structures are crucial for maintaining the integrity of complex shapes and ensuring a successful print. These structures act as a temporary framework that holds the printed parts in place during the printing process, allowing for the creation of intricate designs that might otherwise be impossible to achieve. Here's a detailed guide on designing and printing support structures:
Design Considerations:
- Material Selection: Choose a support material that is compatible with your recycled plastic filament. PLA (Polylactic Acid) is a popular choice due to its ease of removal and compatibility with many 3D printers.
- Strength and Flexibility: Supports should be strong enough to withstand the stresses of the printing process but also flexible enough to allow for easy removal. Consider using a material with a lower melting point than your main print material for easier detachment.
- Design Complexity: The complexity of your support structure depends on the intricacy of your model. For simple overhangs, basic supports may suffice. For more complex designs with deep cavities or delicate features, more intricate support patterns are necessary.
- Orientation: Carefully plan the orientation of your model during printing. Supports should be placed strategically to minimize material waste and ensure easy removal.
Software Tools:
Utilize 3D modeling software to create your support structures. Many slicing software packages offer built-in support generation tools. These tools allow you to define support density, material type, and removal strategies. Popular options include Cura, Simplify3D, and PrusaSlicer.
Printing Process:
- Support Placement: During slicing, ensure that support structures are placed correctly around the areas requiring support. Adjust the support density and pattern based on the complexity of your model.
- Support Material Settings: Set your 3D printer's material settings accordingly. This may involve using a different extruder or adjusting temperature to accommodate the chosen support material.
- Bed Adhesion: Ensure your print bed is properly adhered to prevent warping. Consider using a bed adhesive or a build plate with a textured surface.
- Layer Height and Speed: Use a finer layer height and slower printing speed for supports to ensure accuracy and strength.
Post-Processing:
After printing, removing supports is essential. Here are some methods:
- Chemical Removal: Soak the printed part in a solvent like acetone or isopropyl alcohol to dissolve the supports.
- Mechanical Removal: Carefully sand, file, or grind away the supports using tools appropriate for your chosen material.
- Breakout: In some cases, supports can be carefully pried or snapped off once cooled.
Tips for Success:
- Plan your support structure design carefully to minimize material waste and potential damage to the final part.
- Test print prototypes to refine your support design and removal process.
- Experiment with different support materials and removal techniques to find the best approach for your specific project.
Unleashing the Power of Recycled Pet Plastic: A Sustainable Revolution
You may want to see also
Frequently asked questions
3D printing recycled plastic involves several steps. First, the plastic waste is collected, sorted, and cleaned to remove any contaminants. Then, it is shredded or ground into small pieces, which are called flakes or pellets. These plastic flakes are then melted and extruded through a nozzle, layer by layer, to create the desired 3D object.
Using recycled plastic for 3D printing offers numerous advantages. It helps reduce waste and promotes sustainability by giving new life to plastic materials that would otherwise end up in landfills. Recycled plastic is often more affordable and accessible compared to virgin plastic, making it an eco-friendly and cost-effective choice for 3D printing enthusiasts.
Selecting the appropriate recycled plastic depends on various factors. Consider the desired strength, flexibility, and color of the printed object. Common types of recycled plastic for 3D printing include ABS (Acrylonitrile Butadiene Styrene), PLA (Polylactic Acid), and PETG (Polyethylene Terephthalate Glycol-modified). Each material has unique properties, so research and choose the one that best suits your printing needs.
While 3D printing with recycled plastic is an excellent practice, there are some challenges to consider. Recycled plastic may have inconsistencies in quality, color, and mechanical properties compared to virgin plastic. It can also be more prone to warping and may require additional support structures during printing. Proper material selection, printing parameters, and post-processing techniques can help mitigate these issues.
Yes, many 3D printed objects made from recycled plastic can be recycled again. However, the recycling process might vary depending on the chosen material. For example, ABS and PLA are generally easier to recycle and can be ground back into flakes for reuse. It's essential to follow proper recycling guidelines and consider the specific recycling capabilities of your local waste management system.