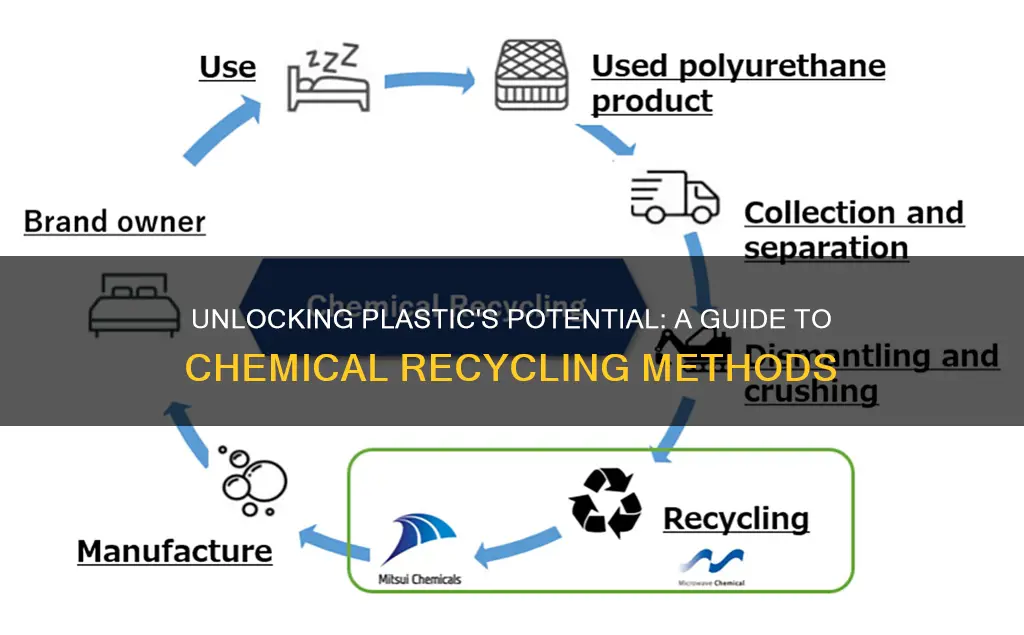
Chemical recycling is an innovative process that offers a sustainable solution to the global plastic waste crisis. It involves breaking down plastic waste into its original chemical building blocks, allowing for the creation of new materials without the need for virgin resources. This method is particularly useful for hard-to-recycle plastics, such as polyolefins and certain types of polyesters, which can be transformed into valuable chemicals, fuels, and even new plastic resins. By employing advanced chemical processes, this recycling technique aims to reduce the environmental impact of plastic waste, promote a circular economy, and provide an alternative to traditional mechanical recycling methods.
What You'll Learn
- Pyrolysis: Heat plastic in absence of oxygen to break it down into smaller molecules
- Hydrolysis: Use water and catalysts to break chemical bonds in plastic
- Gasification: Heat plastic with controlled oxygen to produce a gas for new materials
- Enzymatic Recycling: Employ enzymes to degrade plastic into its original building blocks
- Chemical Upcycling: Transform plastic waste into valuable chemicals and materials
Pyrolysis: Heat plastic in absence of oxygen to break it down into smaller molecules
Pyrolysis is a thermal decomposition process that offers a promising approach to chemically recycling plastic waste. This method involves heating plastic in the absence of oxygen, typically at high temperatures ranging from 300°C to 700°C. The process occurs rapidly, causing the plastic to break down into smaller molecules, which can then be transformed into valuable products.
The key principle behind pyrolysis is the removal of oxygen, which prevents combustion and allows for the controlled breakdown of plastic. When heated, the plastic undergoes thermal degradation, leading to the formation of various products depending on the specific conditions and the type of plastic used. This process can be carried out in different ways, including batch-wise or continuous processing, each with its own advantages.
In a batch-wise process, plastic waste is fed into a reactor, heated, and then cooled, allowing for the collection of the resulting pyrolysis oil, gas, and char. This method is relatively simple and can be used for small-scale operations or when processing diverse types of plastics. On the other hand, continuous processing involves a more complex setup, where plastic is fed into a reactor at a controlled rate, ensuring a steady output of pyrolysis products. This method is more suitable for large-scale operations and can handle high volumes of plastic waste efficiently.
The products obtained from pyrolysis are highly valuable. Pyrolysis oil, also known as pyrolytic oil or bio-oil, is a dark, viscous liquid containing a mixture of hydrocarbons, which can be further refined to produce biofuels, chemicals, and even synthetic materials. Pyrolysis gas, primarily composed of methane, ethylene, and hydrogen, can be utilized as a fuel source or processed to create valuable chemicals. Additionally, the char produced can be used as a carbon source or further processed for various applications.
One of the significant advantages of pyrolysis is its ability to handle various types of plastics, including those that are difficult to recycle through other methods. It can process mixed plastic waste, making it an attractive option for waste management and recycling industries. However, it is important to note that the process requires careful control of temperature and residence time to optimize the yield and quality of the products.
Apple's Plastic Recycling Facilities: Unveiling the Green Giant's Environmental Commitment
You may want to see also
Hydrolysis: Use water and catalysts to break chemical bonds in plastic
Hydrolysis is a promising method for chemically recycling plastic, offering a way to break down the complex polymer chains that make up many plastic materials. This process involves using water and catalysts to initiate a chemical reaction that cleaves the strong covalent bonds within the plastic structure. The goal is to transform the plastic back into its original building blocks, such as monomers or small molecules, which can then be reused to create new products.
The hydrolysis process typically begins with the selection of an appropriate catalyst. Enzymes, acids, or bases can be employed, depending on the specific plastic type. For instance, polyethene terephthalate (PET), commonly used in beverage bottles, can be hydrolyzed using a strong acid catalyst like sulfuric acid. The plastic is exposed to this catalyst in the presence of water, facilitating the breakdown of the ester bonds within the polymer chain. This reaction produces water-soluble products, such as terephthalic acid and ethylene glycol, which can be separated and potentially recycled.
The choice of catalyst is crucial as it determines the efficiency and selectivity of the hydrolysis reaction. Enzymes, such as PETase, have gained attention for their ability to selectively hydrolyze PET. These biological catalysts offer a more environmentally friendly approach, as they are biodegradable and can operate under mild conditions. However, enzymes may require specific conditions to maintain their activity and stability, which can be a challenge for large-scale applications.
In the hydrolysis process, the plastic material is typically ground into small particles or dissolved in a suitable solvent to increase the surface area and enhance contact with the catalyst. The reaction conditions, such as temperature and pressure, are carefully controlled to optimize the hydrolysis rate while minimizing unwanted side reactions. After the reaction, the products are separated from the reaction mixture, often through filtration or extraction, and then purified to remove any residual catalyst or impurities.
Hydrolysis provides a pathway to recycle plastic waste, especially for materials like PET, which are currently challenging to recycle using mechanical methods. By breaking down the plastic into its constituent parts, this process enables the potential for a circular economy in the plastics industry. However, further research and development are needed to optimize the efficiency and scalability of hydrolysis, ensuring that it becomes a viable and cost-effective solution for plastic chemical recycling.
Unstain the Past: A Guide to Removing Stains from Recycled Plastic Shirts
You may want to see also
Gasification: Heat plastic with controlled oxygen to produce a gas for new materials
Gasification is an innovative process that offers a promising solution to the global challenge of plastic waste management. This method involves heating plastic materials with controlled amounts of oxygen, resulting in the production of a valuable gas that can be utilized for various purposes. By applying this technique, we can effectively transform plastic waste into a resource rather than a burden.
The process begins with the careful selection and preparation of plastic waste. It is crucial to ensure that the plastic is clean and free from contaminants to achieve optimal results. The plastic is then fed into a gasifier, a specialized reactor designed to facilitate the gasification process. Inside the gasifier, the plastic undergoes intense heat, typically reaching temperatures of around 1000-1500°C (1832-2732°F). This high-temperature environment initiates a series of chemical reactions.
During gasification, the plastic is exposed to controlled oxygen levels, which play a critical role in the transformation process. The oxygen reacts with the plastic, breaking down its complex molecular structure. This reaction produces a synthesis gas, commonly known as syngas. Syngas is a mixture of carbon monoxide (CO) and hydrogen (H2), along with small amounts of other gases like carbon dioxide (CO2) and water vapor (H2O). The composition of syngas can be tailored by adjusting the oxygen input, making it a versatile product.
The beauty of gasification lies in its ability to convert plastic waste into a valuable resource. The syngas produced can be further processed and refined to create a range of new materials. For instance, carbon monoxide and hydrogen can be utilized in the production of synthetic fuels, chemicals, and even new types of plastics. This approach not only reduces the environmental impact of plastic waste but also provides a sustainable feedstock for various industries.
Additionally, gasification offers the advantage of energy recovery. The process generates heat and electricity, which can be captured and utilized for power generation or other industrial applications. This aspect further enhances the sustainability of the method, making it an attractive option for waste-to-energy systems. By implementing gasification technology, we can move towards a more circular economy, where waste is minimized, and resources are efficiently utilized.
Irvine's Plastic Recycling: A Green Revolution or a Myth?
You may want to see also
Enzymatic Recycling: Employ enzymes to degrade plastic into its original building blocks
Enzymatic recycling is an innovative approach to addressing the global plastic waste crisis, offering a more sustainable and efficient method of breaking down plastic materials compared to traditional chemical recycling. This process involves the use of enzymes, specifically biological catalysts, to degrade plastic polymers back into their original building blocks, such as monomers or small molecules. By doing so, it enables the potential for a circular economy where plastic waste can be continuously recycled and reused.
The process begins with selecting the appropriate enzymes that can target specific plastic polymers. For instance, polyethene terephthalate (PET), a common plastic used in beverage bottles, can be degraded by enzymes like PETase, which is produced by certain bacteria. These enzymes have the unique ability to break down the ester bonds within the PET polymer chain, effectively hydrolyzing it into its constituent monomers, terephthalic acid (TPA) and ethylene glycol (EG).
Once the enzymes are identified and isolated, they can be utilized in a controlled environment, such as a bioreactor, to initiate the degradation process. The plastic waste is ground into small particles and mixed with the enzymes, along with a suitable buffer and cofactors to optimize the reaction. Under specific temperature and pH conditions, the enzymes catalyze the hydrolysis reaction, breaking down the plastic into its basic components. This process is highly selective, ensuring that only the desired plastic polymer is targeted, leaving other materials unaffected.
One of the significant advantages of enzymatic recycling is its ability to operate under mild conditions, typically at room temperature and neutral pH, which reduces energy consumption and minimizes the risk of unwanted side reactions. Moreover, enzymes can be highly efficient, achieving high conversion rates and selectivity, making the process economically viable. After the degradation process, the resulting monomers can be further processed and purified to create new plastic products, completing the recycling loop.
This method of recycling plastic has the potential to revolutionize the way we manage plastic waste, offering a more environmentally friendly and sustainable solution. Enzymatic recycling can contribute to reducing the environmental impact of plastic pollution, especially when combined with other recycling techniques, such as chemical recycling and mechanical recycling, to create a comprehensive waste management strategy. As research in this field continues, the efficiency and scalability of enzymatic recycling methods are expected to improve, making it a viable alternative to traditional plastic disposal methods.
Singapore's Plastic Recycling Revolution: A Green Transformation
You may want to see also
Chemical Upcycling: Transform plastic waste into valuable chemicals and materials
Chemical upcycling is a promising approach to address the global plastic waste crisis, offering a sustainable solution by transforming plastic waste into valuable chemicals and materials. This process involves breaking down plastic polymers into their constituent monomers or smaller molecules, which can then be used to create new products, reducing the need for virgin resources and minimizing environmental impact. Here's an overview of the process and its potential applications:
Process Overview:
Chemical upcycling primarily focuses on two methods: chemical recycling and advanced chemical recycling. Chemical recycling involves breaking down plastics through chemical processes, often using catalysts or solvents, to produce smaller molecules or monomers. These monomers can then be repurposed into new materials. Advanced chemical recycling, on the other hand, employs more sophisticated techniques, such as sol-gel processes or hydrothermal treatment, to convert plastic waste into valuable chemicals like fuels, oils, or platform chemicals. The key is to find efficient and selective reactions that can target specific plastic types without compromising the quality of the resulting products.
Applications and Benefits:
- Fuel Production: One of the most well-known applications is the conversion of plastic waste into fuels. Through processes like pyrolysis or gasification, plastic polymers can be transformed into synthetic crude oil, which can then be refined into gasoline, diesel, or jet fuel. This approach not only reduces plastic waste but also provides an alternative energy source.
- Chemical Feedstock: Upcycled plastics can serve as valuable feedstocks for the chemical industry. For instance, polyolefins, a common plastic type, can be chemically recycled to produce ethylene and propylene, which are essential building blocks for various chemicals, including plastics, solvents, and lubricants. This process ensures a circular economy where waste is minimized, and valuable resources are recovered.
- New Materials: Chemical upcycling enables the creation of new materials with unique properties. For example, polyesters, a widely used plastic, can be chemically recycled to produce terephthalic acid and ethylene glycol, which are then used to make new polyesters with improved performance. This process can lead to the development of biodegradable plastics, advanced composites, and innovative textiles.
- Environmental Impact: By upcycling plastic waste, we can significantly reduce the demand for virgin resources, decreasing the need for oil drilling and mining, which have environmental consequences. It also minimizes the amount of plastic ending up in landfills or the environment, thus mitigating pollution and potential ecological damage.
Implementing chemical upcycling technologies on a large scale requires collaboration between researchers, industries, and policymakers. Optimizing processes, developing efficient catalysts, and establishing infrastructure for waste collection and processing are crucial steps. Additionally, educating the public about the benefits of chemical recycling can foster a culture of sustainability and encourage responsible waste management practices.
Unveiling the Truth: Is Plastic Recycling a Myth?
You may want to see also
Frequently asked questions
Chemical recycling, also known as feedstock recycling, is a process that breaks down plastic waste into its original chemical building blocks, such as monomers or petrochemicals. Unlike traditional recycling, which typically involves mechanical processes to reshape plastic into new products, chemical recycling can handle a wider range of plastic types and even those contaminated with food or other materials. This method can potentially produce high-quality feedstocks for manufacturing new plastics.
Chemical recycling offers several advantages. Firstly, it can process mixed plastic waste streams, including those that are difficult to recycle through mechanical means. This technology can also reduce the reliance on virgin fossil fuels, as it converts plastic waste back into valuable chemicals and feedstocks. Additionally, chemical recycling can help divert plastic waste from landfills and incinerators, contributing to a more sustainable and circular economy for plastics.
Yes, certain types of plastics are more amenable to chemical recycling. Polyolefins, such as polyethylene (PE) and polypropylene (PP), are commonly targeted due to their abundance and relatively low melting points, making them easier to process. Polyethylene terephthalate (PET), a common plastic used in beverage bottles, can also be chemically recycled. However, the process may vary depending on the specific plastic type and its composition.
While chemical recycling shows promise, there are some challenges to consider. The process can be energy-intensive and may require specialized equipment and catalysts. Scaling up chemical recycling processes to handle large volumes of waste is another hurdle. Additionally, ensuring the economic viability of chemical recycling plants and finding cost-effective ways to separate and collect different types of plastics for recycling are ongoing areas of research and development.