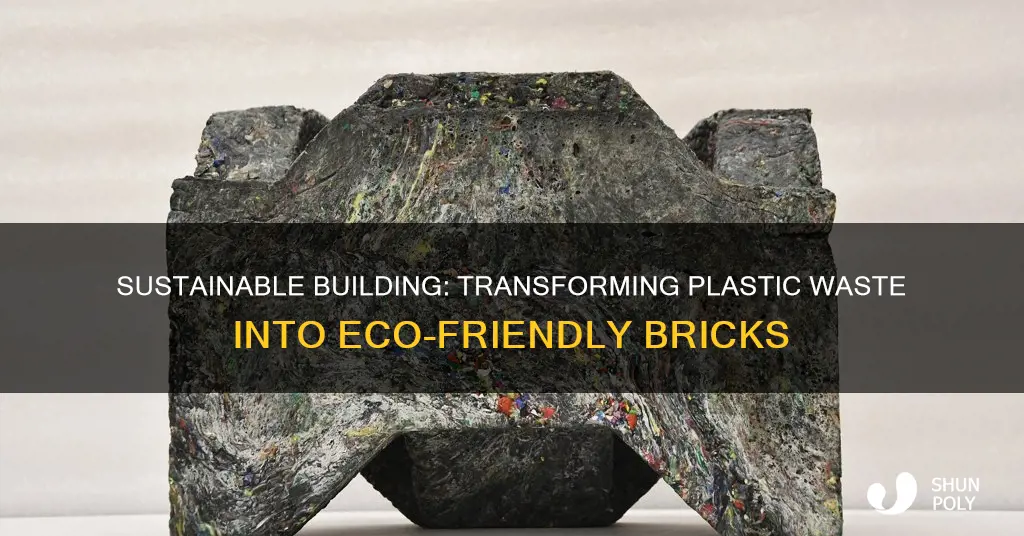
Creating bricks from recycled plastic is an innovative approach to addressing environmental concerns and promoting sustainability. This method involves transforming plastic waste into building materials, offering a unique solution to the growing plastic pollution crisis. By utilizing recycled plastic, we can reduce the demand for virgin resources, minimize waste, and create a more circular economy. The process typically involves cleaning and sorting the plastic, followed by shredding or grinding it into small pieces. These pieces are then heated and compressed to form bricks, which can be used for construction, landscaping, or other applications. This sustainable practice not only reduces the environmental impact of plastic waste but also provides a durable and cost-effective alternative to traditional building materials.
What You'll Learn
- Sorting and Cleaning: Collect and sort plastic waste, then clean to remove contaminants
- Milling and Grinding: Break down plastic into small particles, then grind into a fine powder
- Mixing and Forming: Combine powder with binding agents, mix thoroughly, and shape into bricks
- Curing and Drying: Allow bricks to cure in a controlled environment to ensure strength
- Testing and Quality Control: Inspect bricks for defects, ensuring they meet standards for durability
Sorting and Cleaning: Collect and sort plastic waste, then clean to remove contaminants
The process of creating bricks from recycled plastic begins with meticulous sorting and cleaning of the plastic waste. This initial step is crucial as it directly impacts the quality and durability of the final product. Here's a detailed guide on how to approach this phase:
Collection and Sorting: Begin by collecting various types of plastic waste from different sources. This can include household items like water bottles, milk jugs, and food containers, as well as industrial and commercial plastic scraps. Once collected, the waste needs to be sorted into different categories based on the type of plastic. Common types of plastic include PET (polyethylene terephthalate), HDPE (high-density polyethylene), PVC (polyvinyl chloride), and LDPE (low-density polyethylene). Each type of plastic has unique properties and is suitable for different applications. For instance, PET is commonly used for beverage bottles, while HDPE is often found in milk containers. Sorting ensures that the plastic bricks will have consistent properties and can be utilized effectively.
Cleaning and Preparation: After sorting, the plastic waste undergoes a thorough cleaning process to remove any contaminants. This step is essential to ensure the bricks are strong and durable. Start by removing any non-plastic items like caps, labels, or metal parts from the sorted plastic. This can be done manually or with the help of simple tools. Next, wash the plastic pieces to eliminate dirt, dust, and any remaining labels. Use a gentle detergent and warm water to clean the surfaces. Rinse the plastic thoroughly to remove any soap residue. For a more thorough cleaning, consider using a washing machine or a specialized plastic recycling machine, which can handle large volumes of waste and ensure a more consistent cleaning process.
Drying and Inspection: After cleaning, it is crucial to dry the plastic pieces completely. Moisture can affect the bonding process during brick manufacturing. Place the cleaned plastic on drying racks or flat surfaces, ensuring good air circulation. Allow the plastic to air dry for a few hours or even overnight. Once dry, inspect the sorted and cleaned plastic for any remaining contaminants or damage. This step ensures that only the highest quality plastic is used for brick production.
By following these sorting and cleaning procedures, you lay the foundation for creating high-quality bricks from recycled plastic. This process not only ensures the bricks' strength and durability but also promotes sustainability by giving new life to plastic waste.
BIC White-Out EZcorrect Plastic Case: Can It Be Recycled?
You may want to see also
Milling and Grinding: Break down plastic into small particles, then grind into a fine powder
The process of creating bricks from recycled plastic begins with the careful disassembly and sorting of plastic waste. This initial step is crucial to ensure the quality and consistency of the final product. Once the plastic waste is sorted, the next phase involves milling and grinding, which are essential for transforming the plastic into a usable form for brick-making.
Milling is the initial step in this process, where the sorted plastic waste is fed into a milling machine. This machine is designed to break down the plastic into smaller, more manageable pieces. The goal is to reduce the size of the plastic fragments significantly, creating a consistent and uniform particle size. The milling process can be adjusted to achieve the desired particle size, ensuring that the subsequent grinding process is more efficient.
After milling, the plastic particles are further processed through a grinding mechanism. Grinding is a critical step as it aims to reduce the particle size to a fine powder, often referred to as 'plastic flour' or 'plastic meal'. This fine powder is the key ingredient for the brick-making process. The grinding process can be achieved using various methods, such as hammer mills, ball mills, or even specialized plastic grinding machines. The choice of grinding method depends on the specific requirements and the desired outcome.
During the grinding process, it is essential to maintain a controlled environment to prevent the plastic from overheating or melting. This is particularly important when dealing with certain types of plastics that have lower melting points. By keeping the temperature and moisture levels in check, the plastic can be effectively reduced to a fine powder without compromising its structural integrity.
The resulting fine powder from the grinding process is now ready to be combined with other materials and additives to create the brick mixture. This powder forms the base of the brick, providing the necessary strength and structure. The next steps involve mixing, shaping, and curing the brick mixture to produce the final recycled plastic bricks.
James City County's Plastic Lid Recycling: Unlocking the Potential
You may want to see also
Mixing and Forming: Combine powder with binding agents, mix thoroughly, and shape into bricks
To create bricks from recycled plastic, the process begins with a careful mixture of the plastic powder with binding agents. The first step is to source and grind the plastic waste into a fine powder, ensuring it is free from any contaminants. This powder will serve as the base material for your bricks. Next, you'll need to select an appropriate binding agent, which can vary depending on your specific needs and the desired properties of the bricks. Common binding agents include natural materials like clay, lime, or even plant-based fibers, or synthetic options such as polymers or resins. The choice of binding agent will influence the strength, durability, and environmental friendliness of your bricks.
Once you have your plastic powder and binding agent ready, it's time to mix them thoroughly. This step is crucial to ensure an even distribution of the binding agent throughout the powder, creating a homogeneous mixture. You can use a large mixing container or a blender to achieve this. Add the binding agent gradually while mixing, ensuring it is well incorporated. The mixture should be consistent and free from any lumps, as this will affect the final brick quality. Consider wearing protective gear, such as gloves and a mask, during this process to avoid any potential health risks associated with the dust.
After mixing, the real work of shaping begins. You can use various methods to form the bricks, each offering different advantages. One common technique is to use a mold. Prepare a mold in the desired shape and size of your brick, ensuring it is well-fitted and sealed. Pour the mixed plastic powder into the mold, tapping it gently to remove any air bubbles. Allow the mixture to set and cure according to the binding agent's instructions. Once set, carefully remove the brick from the mold, and you'll have a shaped brick ready for further processing or use.
Another method is to create a brick-making machine or a simple press. This involves setting up a frame with a movable platform and a pressing mechanism. Place the mixed plastic powder on the platform, and then use the press to shape and compact it into the desired brick form. This method provides more control over the brick's dimensions and can be useful for producing bricks in large quantities. Remember to wear safety gear and follow proper operating procedures when using any machinery.
Finally, once you've shaped the bricks, they may require additional steps to enhance their strength and durability. This could include curing the bricks in a controlled environment, allowing the binding agent to fully set and harden. You might also consider surface treatments or finishes to improve their appearance and functionality. With these steps, you can successfully transform recycled plastic into reusable bricks, contributing to a more sustainable and environmentally conscious approach to construction and building materials.
Eco-Friendly Fanny Packs: Recycled Plastic Options for Sustainable Style
You may want to see also
Curing and Drying: Allow bricks to cure in a controlled environment to ensure strength
Curing and drying are crucial steps in the process of creating bricks from recycled plastic, as they significantly impact the final product's strength and durability. After the bricks are formed and shaped, they need to undergo a controlled curing process to ensure they reach their maximum potential. This step is often overlooked but is essential for the long-term performance of the bricks.
The curing process typically involves allowing the bricks to sit in a controlled environment, such as a temperature- and humidity-controlled room or a specialized curing chamber. The goal is to provide optimal conditions for the plastic to harden and strengthen over time. During this phase, the bricks should be protected from direct sunlight and extreme temperature fluctuations to prevent any potential damage. It is recommended to maintain a consistent temperature and humidity level throughout the curing period.
A recommended duration for the curing process is around 7 to 14 days. During this time, the bricks should be regularly inspected to ensure they are not warping or cracking. The curing environment should be well-ventilated to allow for proper air circulation, which aids in the drying process and prevents the accumulation of moisture within the bricks. Proper ventilation also helps to eliminate any potential odors that may arise during the curing process.
After the initial curing period, the bricks can be moved to a drying area with controlled conditions. This step is crucial as it helps to eliminate any remaining moisture and ensures the bricks are completely dry before they are handled or used. The drying process can take several days, and the bricks should be regularly monitored to ensure they are not absorbing any excess moisture from the environment.
By allowing the bricks to cure and dry in a controlled environment, you can ensure that the plastic material fully sets and hardens, resulting in strong and durable bricks. This process is a critical aspect of the recycling and construction process, as it transforms the recycled plastic into a valuable building material with long-lasting performance. Proper curing and drying techniques will contribute to the overall success of your recycled plastic brick project.
Unraveling the Mystery: Can Plastic Spoons Be Recycled?
You may want to see also
Testing and Quality Control: Inspect bricks for defects, ensuring they meet standards for durability
The process of creating bricks from recycled plastic involves several crucial steps to ensure the final product is durable and meets the required standards. Once the plastic is collected, sorted, and processed into a usable form, it is time to begin the brick-making process. The raw plastic material is typically extruded and then shaped into brick-like forms using molds or presses. This step requires precision to achieve consistent dimensions and a uniform appearance. After the bricks are formed, rigorous testing and quality control procedures are essential to guarantee their integrity.
One of the primary methods of inspection is visual examination. Each brick should be carefully scrutinized for any visible defects, such as cracks, voids, or uneven surfaces. These imperfections can compromise the brick's structural integrity and durability. Inspectors should look for any signs of warping or distortion, especially at the joints where bricks are connected. Proper alignment and straightness are critical to ensure the bricks can withstand the stresses of construction and environmental factors.
In addition to visual inspection, dimensional accuracy is vital. Bricks must meet specific size and shape specifications to fit together seamlessly and provide a solid foundation for construction. Calipers or measuring tools should be used to verify the dimensions, including length, width, and height. Any deviations from the standard measurements should be noted and addressed, as they can lead to issues with bonding and structural stability.
Another critical aspect of quality control is assessing the mechanical properties of the bricks. This involves subjecting the bricks to various tests to evaluate their strength and performance. One common test is the compressive strength test, where bricks are subjected to controlled pressure to measure their ability to withstand loads. This test helps identify any potential weaknesses or brittleness in the material. Additionally, bricks can be tested for their resistance to water absorption, which is crucial for ensuring they remain durable in moist environments.
Furthermore, long-term durability should be a key consideration. Bricks can be exposed to various environmental conditions during their lifetime, so it is essential to simulate these conditions in the testing phase. This includes subjecting the bricks to accelerated aging tests, where they are exposed to extreme temperatures, UV radiation, and moisture to assess their resistance over time. By conducting these tests, any potential issues related to material degradation or performance can be identified and rectified before mass production.
In summary, the testing and quality control process for bricks made from recycled plastic is a comprehensive and critical phase in their manufacturing. It ensures that the final product meets the necessary standards for durability, strength, and appearance. By employing visual inspections, dimensional accuracy checks, mechanical property tests, and environmental simulations, manufacturers can produce reliable and long-lasting bricks, contributing to sustainable construction practices.
Washing Plastic: Essential Step for Recycling Success
You may want to see also
Frequently asked questions
The process typically involves collecting and sorting plastic waste, which is then cleaned and shredded into small pieces. These plastic pieces are mixed with a binding agent and moisture to create a malleable mixture. The mixture is then pressed and shaped into brick forms, often using a mold. After pressing, the bricks are left to cure and harden, usually in a controlled environment with specific temperature and humidity conditions.
Not all plastics are suitable for brick production. The ideal plastics for this process are those that are durable, lightweight, and have a low melting point, such as polystyrene (PS), high-density polyethylene (HDPE), and polypropylene (PP). These plastics are often chosen due to their ease of processing and the desired properties of the final brick product.
Using recycled plastic for brick-making offers several advantages. Firstly, it helps reduce plastic waste that often ends up in landfills or pollutes the environment. By repurposing plastic, we can minimize the demand for virgin resources and reduce energy consumption associated with plastic production. Additionally, plastic bricks can be lightweight, making them easier to transport and install, and they can also provide good insulation properties.
Plastic bricks can be engineered to match or even exceed the strength and durability of traditional clay bricks, depending on the specific design and manufacturing process. By adjusting the mixture of plastic and binding agents, as well as the curing process, manufacturers can create bricks with impressive compressive strength and resistance to weathering. However, the load-bearing capacity and longevity of plastic bricks may vary, so it's essential to choose the right grade for the intended application.
Yes, there are a few environmental factors to consider. The energy consumption and carbon emissions associated with the recycling process should be evaluated to ensure it is an environmentally friendly choice. Additionally, the choice of binding agents and the overall manufacturing process should aim to minimize any potential environmental impact. Proper waste management and recycling of any by-products generated during brick production are also crucial.