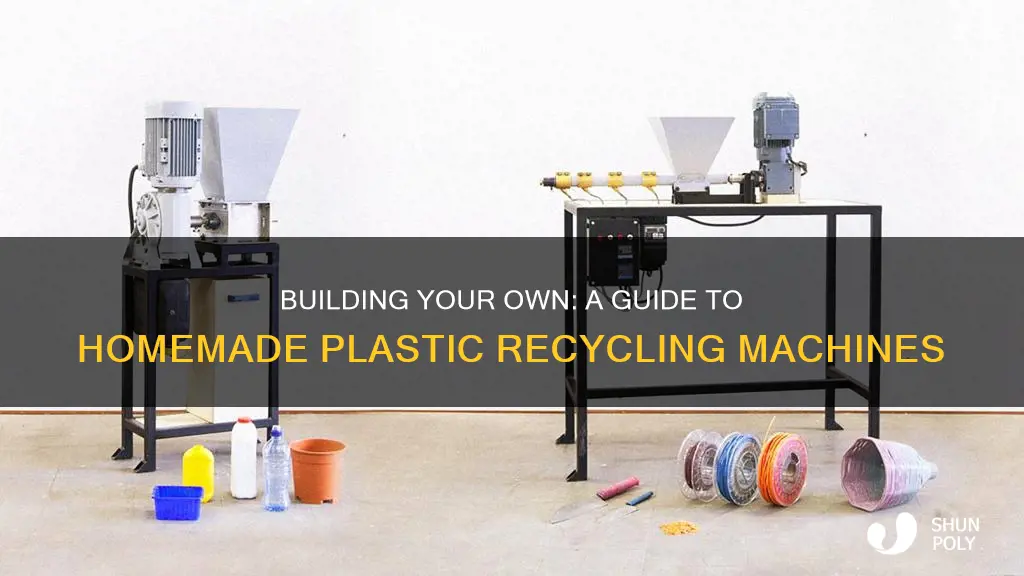
Creating a homemade plastic recycling machine can be a fun and educational project, allowing you to contribute to environmental sustainability. This guide will provide a step-by-step approach to building a basic machine that can help process and recycle plastic waste. The process involves designing a system that can melt and reshape plastic materials, offering a practical solution for managing plastic waste at home or in small-scale recycling operations. By following these instructions, you'll learn about the mechanics of recycling and the potential for upcycling plastic materials into new products.
Characteristics | Values |
---|---|
Materials Required | Plastic bottles, metal frame, motor, gears, conveyor belt, heating element, cooling system, collection bin, safety gear |
Steps | 1. Design and build the frame using metal or wood. 2. Source and prepare the necessary components like a motor, gears, and conveyor belt. 3. Set up the heating element to melt plastic and a cooling system to solidify it. 4. Integrate a collection bin for sorted plastic. 5. Ensure safety measures are in place. |
Process | 1. Collect and sort plastic waste. 2. Feed plastic into the machine. 3. The motor drives the gears to move the conveyor belt, transporting plastic to the heating element. 4. Heat melts the plastic, which is then cooled and solidified. 5. The processed plastic is collected in the bin. |
Challenges | - Requires technical knowledge and engineering skills. - Safety concerns with heating and sharp objects. - May not efficiently handle all types of plastic. - Energy consumption and environmental impact. |
Benefits | - Reduces plastic waste and promotes recycling. - Can be a fun DIY project for learning. - Potentially cost-effective for small-scale operations. |
Considerations | - Local regulations and waste management guidelines. - Maintenance and repair requirements. - Scalability and efficiency for larger operations. |
What You'll Learn
- Materials and Tools: Gather plastic waste, basic tools, and recycled materials
- Design and Blueprint: Create a detailed plan for the machine's structure
- Construction and Assembly: Build the machine step-by-step, ensuring proper alignment
- Plastic Processing: Feed plastic into the machine for cleaning and shredding
- Final Touches and Testing: Adjust settings, test, and refine the machine's performance
Materials and Tools: Gather plastic waste, basic tools, and recycled materials
To begin building your homemade plastic recycling machine, the first step is to gather the necessary materials and tools. This process involves collecting plastic waste, which forms the raw material for your project, along with various basic tools and recycled materials to construct the machine. Here's a detailed breakdown of what you'll need:
Plastic Waste: The primary material for your recycling machine is plastic waste. Collect various types of plastic items that are commonly discarded, such as water bottles, milk jugs, shampoo bottles, and any other plastic containers. Ensure that the plastic is clean and dry to facilitate the recycling process. Different types of plastics, like PET (polyethylene terephthalate) and HDPE (high-density polyethylene), are ideal for recycling and can be identified by their respective recycling symbols (1 and 2).
Basic Tools: You'll require a set of essential tools to assemble the machine. These include a drill with various bits, a saw, a screwdriver set (both flat and Phillips head), a tape measure, a level, and a pair of pliers. These tools will be used for cutting, drilling holes, assembling parts, and ensuring the machine's structural integrity. Additionally, consider having a workbench or a sturdy surface to place your machine during construction.
Recycled Materials: Reusing materials is an eco-friendly approach to building your machine. You can source recycled metal sheets or pipes for the frame, which can be found at salvage yards or online marketplaces. Cardboard boxes can be used for creating compartments or as a base for certain parts. Old computer parts, such as circuit boards or processors, can be utilized for the electrical components, providing a unique and functional design. Recycled plastic sheets or pipes can also be used for creating additional compartments or reinforcing certain parts.
When gathering these materials, it's essential to consider your local recycling guidelines and waste management facilities to ensure that your plastic waste is handled responsibly. Additionally, sourcing recycled materials can often be more cost-effective and environmentally friendly, contributing to a more sustainable project. With the right materials and tools, you'll be well-prepared to start constructing your homemade plastic recycling machine.
Recycling Plastic Model Sprues: Unlocking the Potential for Reuse
You may want to see also
Design and Blueprint: Create a detailed plan for the machine's structure
When designing a homemade plastic recycling machine, a well-structured plan is crucial to ensure the machine's functionality and efficiency. Here's a detailed blueprint for the structure of your plastic recycling machine:
- Frame and Base: Start by constructing a sturdy frame using materials like steel or aluminum. The frame will serve as the backbone of your machine, providing stability and support for all the components. Consider building a rectangular or square-shaped frame with dimensions suitable for your desired machine size. Attach a solid base to the frame, preferably made of heavy-duty wood or metal, to create a solid foundation. Ensure the base has a flat and level surface to facilitate smooth operation.
- Feeding Mechanism: Design an efficient feeding system to handle the plastic waste. You can opt for a manual feeding process where operators feed the plastic into the machine manually. Alternatively, consider adding a conveyor belt system or a auger-style feeder to automate the feeding process. The feeder should be able to handle various plastic types and sizes, ensuring a continuous supply of material to the recycling process.
- Sorting and Cleaning System: Implement a sorting mechanism to separate different types of plastics. This can be achieved using screens, grates, or even air classifiers. The sorted plastics should then pass through a cleaning process to remove contaminants like dirt, labels, and non-plastic debris. You can use a combination of screens, brushes, and air jets to ensure thorough cleaning.
- Shredding and Granulating Unit: This is the heart of your recycling machine. Design a shredding system to break down the cleaned plastic into smaller pieces. You can use a single-shaft or double-shaft shredder depending on your requirements. After shredding, a granulating unit will melt the plastic and extrude it into uniform-sized pellets or granules. This process requires precise temperature control and a cooling system to solidify the plastic.
- Collection and Storage: Create a system to collect and store the recycled plastic pellets or granules. This can be done using hoppers or bins placed below the granulating unit. Ensure the collection area is easily accessible for transportation and further processing.
- Safety Features: Incorporate safety measures to protect operators and ensure the machine's longevity. This includes emergency stop buttons, guards for moving parts, and proper ventilation for any heating elements.
Remember, this blueprint provides a general structure, and you can customize and adapt it based on your specific requirements and available resources. It's essential to consider factors like power supply, noise reduction, and scalability during the design process.
Unraveling the Mystery: Can Giant Plastic Containers Be Recycled?
You may want to see also
Construction and Assembly: Build the machine step-by-step, ensuring proper alignment
Before you begin the construction of your homemade plastic recycling machine, it's crucial to gather all the necessary materials and tools. This includes a sturdy frame made of metal or wood, a powerful motor for shredding, a heating element for melting, a mold or form for shaping, and a cooling system. Ensure you have a clear understanding of the design and specifications of your machine to facilitate a smooth construction process.
Start by constructing the frame, which will be the backbone of your machine. Use metal or wooden beams to create a sturdy structure that can withstand the forces involved in the recycling process. Ensure that the frame is sturdy and well-aligned, as this will impact the overall stability and performance of the machine. Use brackets and screws to join the pieces securely, ensuring that all connections are tight and won't compromise the machine's integrity.
Next, focus on the shredding mechanism. This component is responsible for breaking down the plastic into smaller pieces. Attach the motor to the frame, ensuring it is securely fastened and aligned with the shredding blades. The motor should be powerful enough to handle the task, and the blades should be sharp and properly positioned to ensure efficient shredding. Test the motor's functionality and adjust the blade angles if necessary to optimize the shredding process.
The heating element is a critical component for melting the shredded plastic. Construct a heating chamber that can accommodate the desired amount of plastic. Use a heating element that can generate sufficient heat to melt the plastic efficiently. Ensure proper insulation around the heating element to prevent overheating and potential safety hazards. The melted plastic will then be directed to the shaping area.
Finally, incorporate the shaping and cooling system. This part involves directing the melted plastic into a mold or form to create the desired shape. Use a precise mechanism to control the flow of plastic, ensuring it is evenly distributed. After shaping, a cooling system is essential to solidify the plastic. This can be achieved through air cooling or water cooling, depending on your preference and the scale of your machine. Proper alignment of the cooling system is vital to ensure the plastic sets in the correct shape.
Throughout the construction and assembly process, maintain a high level of precision and attention to detail. Double-check all connections and alignments to ensure the machine operates smoothly and efficiently. Consider adding safety features, such as emergency stop buttons and protective guards, to make your homemade plastic recycling machine both functional and safe to use.
Unraveling the Mystery: Can Plastic Milk Caps Be Recycled?
You may want to see also
Plastic Processing: Feed plastic into the machine for cleaning and shredding
To begin the process of recycling plastic using your homemade machine, you'll need to ensure that the plastic is clean and properly prepared. Start by feeding the plastic into the machine's feeding mechanism, which could be a conveyor belt or a manual feeding system. The goal is to ensure a smooth and continuous flow of plastic into the machine.
For cleaning, you might want to consider a simple yet effective method. One approach is to use a washing system where the plastic is washed with water to remove any dirt, labels, or contaminants. This can be done by passing the plastic through a series of water jets or by using a rotating drum with water nozzles. The cleaning process is crucial to ensure that the recycled plastic is of high quality and free from any impurities.
After cleaning, the plastic needs to be shredded into smaller pieces. This step is essential to increase the surface area of the plastic, making it easier to process and recycle. You can use a shredding mechanism consisting of two rotating blades or a hammer mill. The blades should be sharp and designed to cut through the plastic efficiently. As the plastic is fed into the shredder, it will be chopped into flakes or small pellets, which can then be further processed.
The shredding process should be carefully controlled to achieve the desired particle size. Too small particles might lead to processing difficulties, while larger pieces might not meet the requirements for certain applications. Adjusting the speed and force of the shredding mechanism will allow you to customize the output size.
Once the plastic is cleaned and shredded, it is ready for the next stage of recycling, which could involve melting and molding, or it can be used as raw material for other plastic-based products. This initial processing step is fundamental to the entire recycling process and ensures that the plastic is ready for further transformation.
Unraveling the Mystery: Can Plastic Litter Pans Be Recycled?
You may want to see also
Final Touches and Testing: Adjust settings, test, and refine the machine's performance
Once you've built your homemade plastic recycling machine, it's time to fine-tune its performance and ensure it operates efficiently. This phase involves several crucial steps to optimize the machine's functionality and address any potential issues.
Adjusting Settings: Begin by carefully examining the machine's settings. These settings are often customizable and can significantly impact the recycling process. Adjust the temperature and pressure parameters to match the specific plastic types you intend to recycle. For instance, different plastics have varying melting points, so setting the right temperature is essential for effective recycling. Similarly, adjust the feeding mechanism settings to control the material flow. This might involve modifying the speed of the feed roller or the size of the feed opening to accommodate various plastic sizes and shapes.
Testing and Calibration: After adjusting the settings, it's critical to test the machine's performance. Start by feeding a variety of plastic materials through the machine and observe the output. Check for any signs of melting, shredding, or contamination. If the machine is designed for specific plastics, ensure that it processes them correctly without any issues. Calibrate the machine's sensors and controls to ensure accurate measurements and precise adjustments. This step is vital to guarantee consistent performance and high-quality recycling.
Refining Performance: Based on your observations during testing, make necessary refinements. This could involve further adjusting the settings, modifying the machine's design, or adding additional features. For example, if you notice that certain plastics are not being shredded effectively, consider modifying the cutting mechanism or experimenting with different blade angles. Regularly testing and refining the machine's performance will lead to an optimized recycling process.
Safety and Maintenance: While testing, prioritize safety by ensuring all safety guards and interlocks are functional. Regularly maintain the machine by cleaning and lubricating moving parts to prevent wear and tear. Keep the machine's user manual handy for maintenance guidelines specific to your design.
By diligently following these final touches and testing procedures, you can ensure that your homemade plastic recycling machine operates efficiently, consistently, and safely, contributing to a more sustainable approach to plastic waste management.
Recycling Plastic: A Costly Endeavor or Sustainable Investment?
You may want to see also
Frequently asked questions
Building a plastic recycling machine at home can be a complex project, but it primarily requires materials like a motor, gears, a conveyor belt, a heating element, a cooling system, and a collection bin. You'll also need various tools for assembly and electronics components for controlling the machine.
The motor's power and speed are crucial factors. For plastic recycling, a DC motor with a good torque-to-weight ratio is ideal. Consider the size of your machine and the desired processing capacity. A motor with adjustable speed control is beneficial for precise material handling.
While a home oven can be used for melting small amounts of plastic, it's not the most efficient or safe method for a recycling machine. Specialized heating elements and temperature control systems are recommended to ensure consistent melting and prevent overheating.
Safety is essential. Always wear protective gear, including gloves and safety goggles. Ensure proper ventilation when working with plastics and heating elements. Implement safety interlocks to prevent accidents, especially when dealing with moving parts and high temperatures.
Plastic separation is crucial for efficient recycling. You can use color-coding, manual sorting, or automated systems with sensors to identify and separate different plastic types. Research and understand the specific plastics you want to recycle to ensure compatibility with your machine's design.