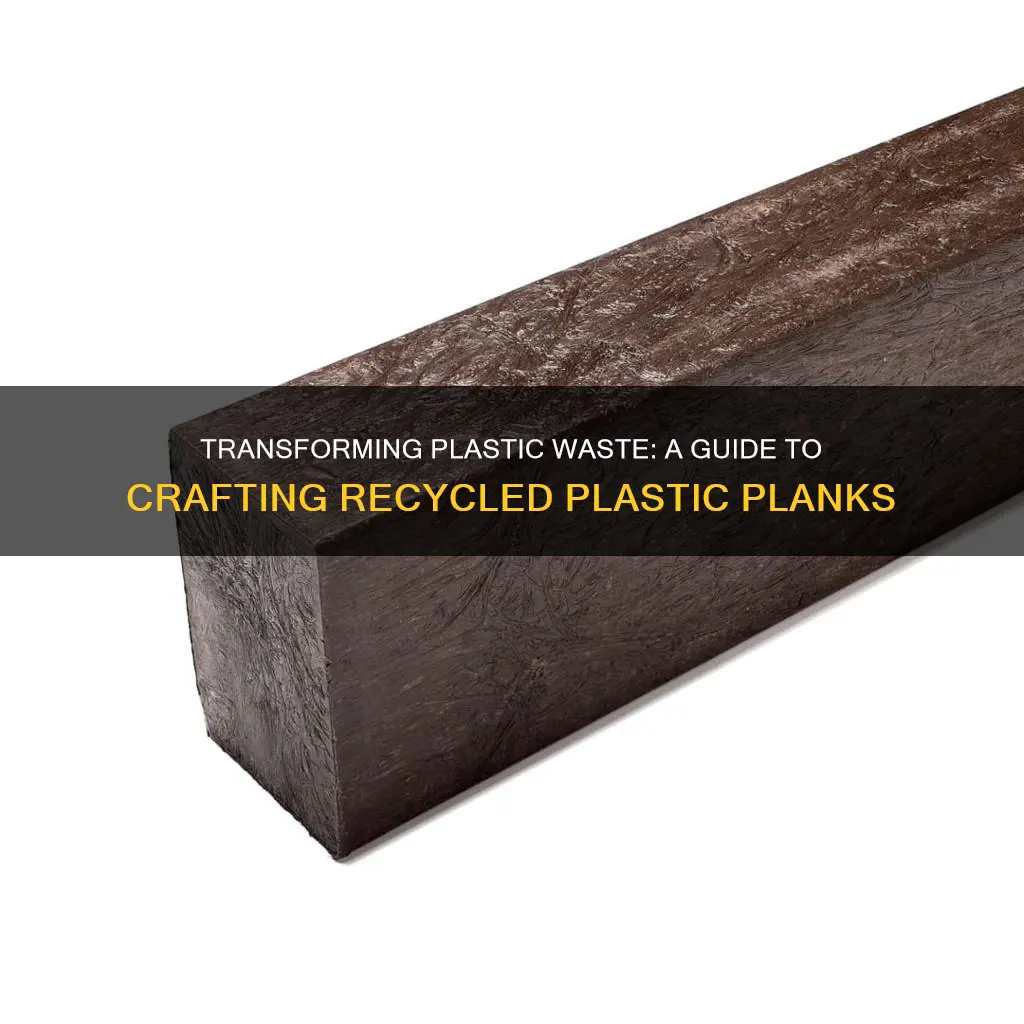
Creating recycled plastic planks is an innovative way to upcycle plastic waste and produce durable, eco-friendly building materials. This process involves transforming used plastic items, such as bottles or containers, into solid planks that can be used for various applications, including flooring, wall cladding, and outdoor furniture. By following a few simple steps, you can turn plastic waste into a valuable resource, reducing environmental impact and promoting sustainability in construction and design.
What You'll Learn
- Collection and Sorting: Gather and sort plastic waste by type and color for efficient processing
- Cleaning and Shredding: Clean and shred plastic waste to reduce size and prepare for recycling
- Melting and Molding: Melt shredded plastic and mold it into planks using a press or extruder
- Cooling and Trimming: Cool the molded planks and trim excess material for a finished product
- Finishing and Sealing: Sand and seal the planks to enhance durability and appearance
Collection and Sorting: Gather and sort plastic waste by type and color for efficient processing
The first crucial step in the process of creating recycled plastic planks is the meticulous collection and sorting of plastic waste. This initial phase is fundamental as it sets the foundation for the entire recycling and repurposing journey. The goal is to gather a diverse range of plastic materials while ensuring they are organized in a way that facilitates efficient processing.
Collection begins with raising awareness among the community or local businesses about the importance of plastic waste management. Encourage the separation of plastic items at the source, which can be as simple as providing designated bins for different types of plastics in offices, schools, or residential areas. Common household plastics like water bottles, milk jugs, detergent containers, and packaging materials are ideal starting points. It is essential to collect a variety of plastic types, including PET (polyethylene terephthalate), HDPE (high-density polyethylene), and LDPE (low-density polyethylene), as each has unique properties that will influence the final product.
Once collected, the plastic waste undergoes a sorting process, which is a critical step to ensure the quality and consistency of the recycled planks. Sorting should be done by type and color to streamline the recycling process. For instance, PET and HDPE are commonly used in beverage containers and can be identified by their respective resin identification codes (1 and 2). LDPE, often found in shopping bags and some packaging, can be identified by its code (4). Sorting by color is also essential as it helps in creating visually appealing and consistent planks. Clear PET bottles, for example, can be sorted from colored ones to create a uniform product.
Advanced sorting techniques may involve the use of machinery to enhance efficiency. Optical sorters can identify and separate plastics based on their color and type, ensuring that only the desired materials progress through the recycling stream. This level of precision is crucial for producing high-quality recycled planks. For manual sorting, trained personnel can identify and categorize plastics based on their characteristics, ensuring that contaminants are minimized.
In summary, the collection and sorting process is a critical phase that requires a systematic approach. By gathering a wide range of plastic waste and sorting it meticulously, you lay the groundwork for the successful creation of recycled plastic planks. This step not only ensures the efficiency of the recycling process but also contributes to the overall quality and marketability of the final product.
Unraveling the Mystery: Can Plastic 6-Pack Holders Be Recycled?
You may want to see also
Cleaning and Shredding: Clean and shred plastic waste to reduce size and prepare for recycling
The process of creating recycled plastic planks begins with a crucial step: cleaning and shredding plastic waste. This initial stage is essential to ensure the quality and efficiency of the recycling process. Here's a detailed guide on how to effectively clean and shred plastic waste:
Cleaning the Plastic Waste:
Start by collecting and sorting the plastic waste. This step is vital as it separates different types of plastics, each with its own unique properties and recycling requirements. Common household plastics include PET (polyethylene terephthalate), HDPE (high-density polyethylene), and PVC (polyvinyl chloride). Rinse each plastic item to remove any visible dirt, food residue, or contaminants. Use a gentle detergent or dish soap to clean the plastics, ensuring no harsh chemicals that could damage the recycling process. For particularly stubborn stains, a mild abrasive can be used, but always exercise caution to avoid scratching or damaging the plastic. After cleaning, thoroughly rinse the plastics to eliminate any soap residue.
Shredding for Size Reduction:
Once the plastic waste is clean, the next step is shredding. Shredding is a process that reduces the size of the plastic items, making them easier to handle and process during recycling. Here's how to shred plastic waste effectively:
- Use a shredder designed for plastic. These shredders can handle the tough nature of plastic and produce consistent results.
- Feed the cleaned plastic items into the shredder, ensuring they are dry and free of any moisture.
- Adjust the shredder settings to achieve the desired particle size. Smaller particles will result in a finer recycled product, while larger pieces might be suitable for specific applications.
- Collect the shredded plastic and store it in a dry, sealed container to prevent any moisture absorption, which could lead to mold or degradation.
By cleaning and shredding plastic waste, you are preparing it for the recycling process, ensuring that the final recycled plastic planks are of high quality and suitable for various construction and decorative purposes. This initial step is a critical part of the recycling journey, contributing to a more sustainable and environmentally friendly approach to plastic waste management.
Unstain the Past: A Guide to Removing Stains from Recycled Plastic Shirts
You may want to see also
Melting and Molding: Melt shredded plastic and mold it into planks using a press or extruder
The process of transforming shredded plastic into durable planks involves a combination of melting and molding techniques, which can be achieved through the use of a press or extruder. This method is an efficient way to recycle plastic waste and create a valuable, reusable material. Here's a step-by-step guide to mastering this process:
Melting Process: Begin by gathering and shredding plastic waste into small, uniform pieces. This shredded plastic, often referred to as 'flakes' or 'pellets', is the raw material for your planks. Next, set up a melting machine or furnace capable of reaching temperatures suitable for the type of plastic you're working with. Common plastics like PET (polyethylene terephthalate) or HDPE (high-density polyethylene) can be melted at temperatures around 250-300°C. Ensure the melting process is controlled and precise to avoid overheating, which can lead to unwanted chemical reactions or the degradation of the plastic's properties. Once melted, the plastic should be stirred or agitated to ensure even heating and to prevent the formation of air bubbles, which can affect the final product's strength.
Molding and Pressing: After melting, the plastic is ready for molding. This step requires specialized equipment, such as an extruder or a hydraulic press, to shape the molten plastic into planks. The extruder is a popular choice as it allows for continuous production and can be adjusted to create planks of various thicknesses and sizes. Here's a breakdown of the process: First, feed the melted plastic into the extruder's hopper. The plastic is then heated and pushed through a die, which is a shaped opening that determines the final shape of the plank. The die can be designed to create a smooth surface or incorporate patterns for added texture. As the plastic exits the die, it is cooled by air or water to solidify and maintain its shape. The cooled planks can then be cut to the desired length using a sharp blade or a saw.
For a more hands-on approach, a hydraulic press can be used, especially if you're working with smaller batches or unique designs. The process involves placing the melted plastic into a mold, which is then closed and pressed to form the planks. This method offers more flexibility in terms of design but requires precise control over pressure and temperature to ensure the plastic doesn't melt or warp.
Post-Processing and Finishing: Once the planks are formed, they may require additional finishing touches. This can include trimming excess material, smoothing rough edges, and applying a protective coating to enhance durability. Proper cooling and handling are crucial during this stage to prevent warping or damage to the planks.
Mastering the art of melting and molding recycled plastic into planks is a valuable skill for creating sustainable building materials, furniture, or decorative elements. With the right equipment and techniques, you can transform waste plastic into a valuable resource, reducing environmental impact and promoting a circular economy.
Unraveling the Mystery: Can Plastic Drawers Be Recycled?
You may want to see also
Cooling and Trimming: Cool the molded planks and trim excess material for a finished product
The process of creating recycled plastic planks involves several steps, and one crucial phase is cooling and trimming the molded planks to achieve a refined and marketable product. After the molding process, the plastic planks are still in a semi-solid state, requiring careful handling to ensure they set correctly and attain the desired dimensions.
Cooling is an essential step to stabilize the plastic and allow it to harden. It is recommended to cool the planks in a controlled environment, such as a refrigerated area or a temperature-regulated room. The cooling process should be gradual to prevent the plastic from becoming brittle or warping. Place the molded planks on a flat surface or in a mold to maintain their shape during cooling. The duration of cooling can vary depending on the thickness and size of the planks, but typically, it takes several hours for the plastic to reach a solid state.
Once the planks have cooled, it's time to trim and shape them. This step requires precision and attention to detail. Start by identifying the desired thickness and width of the final product. Use sharp, specialized tools such as utility knives, saws, or routers to carefully trim the excess material from the edges. Ensure that the cuts are straight and accurate to maintain a professional finish. For intricate designs or patterns, consider using a band saw or a jigsaw to achieve more complex shapes.
When trimming, it's important to work slowly and steadily to avoid any mistakes. Take your time to measure and mark the cutting lines, especially when dealing with larger planks. Safety should always be a priority, so wear protective gear, including gloves and safety goggles, to prevent any accidents. After trimming, inspect the planks to ensure they meet the required specifications. Any minor imperfections can be smoothed out using a file or sandpaper.
The cooling and trimming process is a critical phase in the manufacturing of recycled plastic planks, as it determines the final appearance and quality of the product. By taking the time to cool the planks properly and using precise trimming techniques, you can create durable and aesthetically pleasing planks that are ready for various applications, from outdoor flooring to decorative features.
Garland's Plastic Recycling: Unveiling the Truth Behind Number 6
You may want to see also
Finishing and Sealing: Sand and seal the planks to enhance durability and appearance
Finishing and sealing your recycled plastic planks is a crucial step to ensure their longevity and aesthetic appeal. This process involves sanding the planks to achieve a smooth surface and then applying a protective sealant. Here's a detailed guide on how to accomplish this:
Sand the Planks: Begin by inspecting the planks for any rough edges or imperfections. Use a power sander or a handheld sander with fine-grit sandpaper (e.g., 120-grit or higher) to gently smoothen the surface. Focus on areas where the plastic might be slightly raised or uneven. Take your time and work in small sections to avoid over-sanding. After sanding, wipe away any dust or debris with a damp cloth to ensure a clean surface for sealing.
Choose the Right Sealant: Selecting an appropriate sealant is essential for protecting your recycled plastic planks. Opt for a high-quality outdoor sealant designed for plastic surfaces. Look for sealants that offer UV protection and are resistant to fading. You can find these at hardware stores or online retailers specializing in outdoor materials. Ensure you follow the manufacturer's instructions for the specific sealant you choose.
Application Process: Once you have the necessary materials, it's time to seal the planks. Start by applying a thin, even coat of sealant to one plank at a time. Use a brush or a roller, depending on the size of the planks and your preference. Work quickly but carefully to avoid dripping or pooling. Allow the first coat to dry according to the sealant's instructions. After it's dry, inspect the surface and apply a second coat for added protection.
Enhancing Appearance: Sanding and sealing not only improves the durability of the planks but also enhances their visual appeal. The sanding process will give the plastic a more natural, wood-like texture, making it less noticeable as recycled material. The sealant adds a subtle shine and protects against UV rays, preventing color fading. You can further customize the appearance by staining or painting the sealed planks, creating a unique and personalized look.
Maintenance and Care: To maintain the finished appearance, regularly inspect the sealed planks for any signs of wear or damage. Reapply the sealant periodically, especially after exposure to harsh weather conditions. With proper care, your recycled plastic planks will remain durable and aesthetically pleasing for years to come.
Transforming Recycled Plastic into Sustainable Post-Consumer Materials
You may want to see also
Frequently asked questions
The process typically involves collecting and sorting plastic waste, which is then cleaned and shredded into small pieces. These plastic flakes are melted and extruded into a continuous sheet, which is then cut into desired plank sizes. The planks are often reinforced with other materials for added strength and stability.
Not all plastics are suitable for this process. Common types used include high-density polyethylene (HDPE), polypropylene (PP), and polyvinyl chloride (PVC). These plastics are chosen for their durability, weather resistance, and ease of processing. It's important to ensure the plastic is clean and free from contaminants to maintain the quality of the final product.
Absolutely! Recycling plastic waste into planks helps reduce the amount of plastic ending up in landfills or the environment. It also decreases the demand for virgin plastic production, which often relies on fossil fuels. By using recycled materials, you contribute to a more sustainable and circular economy, reducing the carbon footprint associated with traditional building materials.