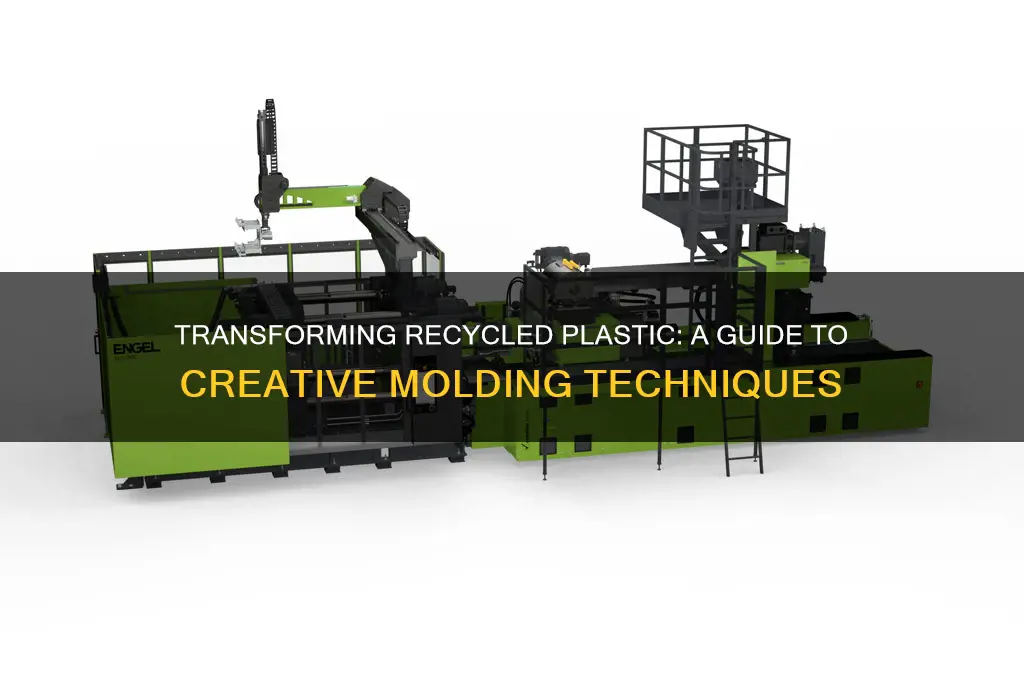
Recycled plastic offers a sustainable alternative to traditional materials, but its effectiveness depends on proper molding techniques. This guide will explore the process of molding recycled plastic, including the preparation of the material, the choice of molding methods, and the considerations for achieving high-quality, durable parts. We'll delve into the benefits and challenges of using recycled plastic, as well as best practices for optimizing its performance in various applications. By understanding these principles, manufacturers can harness the full potential of recycled plastic while contributing to a more sustainable future.
What You'll Learn
- Sorting and Cleaning: Separate plastic types, remove contaminants, and ensure uniform material for molding
- Melt Processing: Heat plastic to its melting point, then shape it using injection or blow molding
- Reinforcement: Add fillers or fibers to enhance strength, durability, and impact resistance
- Cooling and Hardening: Allow molded plastic to cool and solidify for structural integrity
- Finishing Techniques: Sand, paint, or coat molded parts for aesthetics and protection
Sorting and Cleaning: Separate plastic types, remove contaminants, and ensure uniform material for molding
The process of molding recycled plastic begins with meticulous sorting and cleaning to ensure the material is of high quality and suitable for manufacturing. This initial step is crucial as it directly impacts the final product's durability, appearance, and functionality. Here's a detailed guide on how to effectively sort and clean recycled plastic:
Sorting Plastic Types:
The first step is to separate different types of plastics, as not all plastics are compatible with molding processes. Common plastic types include PET (polyethylene terephthalate), HDPE (high-density polyethylene), PVC (polyvinyl chloride), LDPE (low-density polyethylene), and PP (polypropylene). Each type has unique properties and melting points, so proper identification is essential. You can use a plastic identification chart or a testing kit to determine the type of plastic. For instance, PET is commonly found in beverage bottles, while HDPE is used for milk jugs and shampoo bottles. Sorting by type ensures that you can select the appropriate molding technique and equipment for each plastic category.
Contaminant Removal:
Contaminants such as dirt, labels, non-plastic materials, and broken pieces must be removed from the sorted plastic. These impurities can compromise the quality of the final product and may even render it unusable. Here's a breakdown of the process:
- Shredding and Grinding: Large plastic items can be shredded or ground into smaller pieces to facilitate processing. This step reduces the size of the plastic, making it easier to handle and clean.
- Washing: Thorough washing is essential to remove dirt and debris. Use a washing machine or a commercial washing system to rinse the plastic. Hot water and detergents can be employed to ensure a clean surface. After washing, rinse the plastic to remove any remaining soap or residue.
- Sorting by Color and Type: Further sorting can be done based on color and type to create consistent batches. This step is particularly important for colors that may degrade or change during the molding process.
Uniformity and Quality Control:
The goal of sorting and cleaning is to achieve uniform material that meets the required specifications. Here's how you can ensure quality:
- Size Consistency: All plastic pieces should be of similar size to ensure even distribution during molding. This can be achieved by further shredding or using a screen to separate pieces of similar dimensions.
- Moisture and Contaminant Check: Moisture and contaminants can affect the molding process, so it's crucial to dry the plastic thoroughly and inspect for any remaining impurities.
- Testing: Conduct tests to verify the plastic's quality. This may include checking for residual contaminants, measuring moisture content, and assessing the plastic's flexibility and strength.
By following these sorting and cleaning procedures, you can create a high-quality recycled plastic material ready for molding. This process ensures that the final product is reliable, aesthetically pleasing, and meets the necessary standards. Proper sorting and cleaning are fundamental to the success of any recycled plastic molding project.
The Plastic Cycle: From Creation to Reuse
You may want to see also
Melt Processing: Heat plastic to its melting point, then shape it using injection or blow molding
Melt processing is a crucial technique in the recycling and molding of plastic, allowing for the creation of various products from recycled materials. This method involves heating the plastic to its precise melting point, a temperature at which it transitions from a solid to a liquid state, making it malleable and ready for shaping. The process begins with the collection and sorting of plastic waste, ensuring that only suitable materials are selected for recycling. Once sorted, the plastic is cleaned to remove any contaminants, such as labels or non-plastic components, which can interfere with the molding process.
The next step is to shred or grind the plastic into small, uniform pieces, often referred to as 'flakes' or 'granules'. This process increases the surface area of the plastic, facilitating faster and more efficient heating. The shredded plastic is then fed into a specialized machine called an extruder, which plays a pivotal role in melt processing. The extruder applies heat and pressure to the plastic, gradually raising its temperature to the melting point. This controlled heating process ensures that the plastic remains in a molten state without degrading or burning.
As the plastic melts, it becomes a viscous liquid, and the extruder's screw mechanism pushes it through a die, shaping it into the desired form. This shaping can be achieved through two primary methods: injection molding and blow molding. In injection molding, the molten plastic is injected into a closed mold, where it rapidly cools and solidifies, taking the mold's shape. This process is commonly used for producing complex, hollow objects like containers and automotive parts. On the other hand, blow molding is employed for creating hollow, tubular shapes. The molten plastic is first formed into a parison (a partially hollow shape) and then transferred to a mold, where it is inflated to the desired size.
Both injection and blow molding require precise control of temperature and pressure to ensure the quality and integrity of the final product. The heated plastic must be maintained at its melting point throughout the shaping process to guarantee proper flow and filling of the mold. Once the plastic has cooled and solidified, the mold is opened, and the finished product is ejected. This entire process, from shredding to molding, showcases the transformation of recycled plastic into valuable, usable items, contributing to a more sustainable and circular economy.
Milk Container Recycling: NYC Rules and What's Forbidden
You may want to see also
Reinforcement: Add fillers or fibers to enhance strength, durability, and impact resistance
When it comes to molding recycled plastic, reinforcement is a crucial step to enhance the material's performance and durability. One effective method to achieve this is by adding fillers or fibers to the recycled plastic composition. This process involves incorporating various materials that can significantly improve the mechanical properties of the plastic.
Fillers, such as calcium carbonate, talc, or clay, are commonly used to reinforce recycled plastic. These materials are added in small amounts to the plastic resin, providing additional strength and rigidity. The fillers work by occupying space within the plastic matrix, reducing the movement of plastic molecules and increasing the overall stiffness. For example, calcium carbonate, a common filler, is often used in plastic composites to improve dimensional stability and impact resistance. It helps to fill the voids in the plastic structure, making it more robust and less prone to deformation.
Fiber reinforcement is another powerful technique to enhance the performance of recycled plastic. Glass fibers, carbon fibers, or natural fibers like flax or hemp can be added to the plastic during the molding process. These fibers act as a network, providing excellent strength and stiffness in the direction of the load. When molded into various shapes, the plastic with fiber reinforcement becomes much stronger and more durable. For instance, glass fiber-reinforced plastic (GFRP) is widely used in industries requiring high strength-to-weight ratios, such as automotive and construction.
The addition of fillers or fibers can significantly improve the impact resistance of recycled plastic. Impact resistance is crucial for applications where the material might be subjected to sudden forces or shocks. By incorporating fillers or fibers, the plastic becomes more resilient and less likely to crack or shatter upon impact. This is particularly important for products like outdoor furniture, sports equipment, or packaging materials that need to withstand various environmental conditions.
In summary, reinforcement through fillers and fibers is a vital aspect of molding recycled plastic. It allows for the creation of stronger, more durable, and impact-resistant materials. By carefully selecting and combining different fillers and fibers, manufacturers can tailor the properties of recycled plastic to meet specific requirements, making it a valuable and sustainable material for various industrial applications.
Recycling Plastic Plant Pots: Unlocking Their Environmental Potential
You may want to see also
Cooling and Hardening: Allow molded plastic to cool and solidify for structural integrity
When working with recycled plastic, the cooling and hardening process is crucial to ensure the structural integrity of your molded creation. This step is often overlooked, but it significantly impacts the final product's strength and durability. After the molding process, the plastic is in a malleable state, and allowing it to cool and solidify is essential to transform it into a rigid material.
The cooling process begins immediately after the molding is complete. It is vital to maintain a controlled environment during this phase. The temperature and humidity levels should be carefully monitored to prevent rapid cooling, which can lead to warping or cracking. A gradual cooling process is ideal, typically achieved by placing the molded plastic in a temperature-regulated room or using specialized cooling equipment. The goal is to reach a stable, room-temperature solidification without any sudden temperature fluctuations.
Hardening, or the solidification of the plastic, is a critical step that requires patience. Once the plastic has cooled to the desired temperature, it should be left undisturbed for an extended period. This duration can vary depending on the type of plastic and the complexity of the mold. For simpler shapes, a few hours might be sufficient, while more intricate designs may require several days to fully harden. During this time, the plastic undergoes a chemical transformation, forming strong intermolecular bonds that provide structural stability.
It is essential to handle the molded plastic with care during this stage. Avoid any excessive force or impact that could compromise its integrity. Once hardened, the plastic will become much stronger and more resistant to stress, making it suitable for its intended purpose. Proper cooling and hardening techniques are fundamental to the success of your recycled plastic project, ensuring a high-quality, long-lasting end product.
Remember, the cooling and hardening process is a delicate balance, and each project may require specific conditions. Always refer to the guidelines provided by the plastic type and the molding method employed to achieve the best results. This attention to detail will contribute to the overall success of your recycled plastic molding endeavor.
Unraveling the Plastic Recycling Mystery: A Guide to Sorting Your Waste
You may want to see also
Finishing Techniques: Sand, paint, or coat molded parts for aesthetics and protection
When it comes to finishing molded plastic parts, there are several techniques to enhance their appearance and protect the material. Sanding is a fundamental process that helps to smooth out the surface and remove any imperfections or excess material. Start by using a coarse-grit sandpaper to remove any sharp edges or rough spots. Gradually move to finer grits for a more refined finish. Pay close attention to the curves and contours of the molded part, ensuring that the sanding is consistent and even. This process not only improves the overall aesthetics but also prepares the surface for further finishing.
After sanding, you can choose to paint the molded parts to add color and enhance their visual appeal. Prepare the surface by applying a primer specifically designed for plastics. This step ensures better adhesion and a more professional finish. Select a paint that is compatible with the type of plastic used; acrylics and latex paints are commonly used for their ease of application and durability. Apply multiple thin coats, allowing each layer to dry thoroughly before applying the next. This technique is particularly useful for creating vibrant colors and adding a decorative element to the molded parts.
Coating is another effective method to protect and finish molded plastic components. A clear coat or varnish can be applied to provide a protective barrier against wear and tear. This is especially important for parts that will be subjected to harsh conditions or frequent use. Choose a coating that is suitable for the specific application, such as a UV-resistant clear coat for outdoor use. Apply the coating evenly, ensuring complete coverage, and allow sufficient drying time. The coating not only improves the part's appearance but also increases its durability, making it more resistant to scratches and environmental damage.
Additionally, consider using specialized finishes like rubberized coatings or textured finishes for unique effects. Rubberized coatings can provide a non-slip surface, making the molded parts functional as well as aesthetically pleasing. Textured finishes, on the other hand, can add a tactile element, making the parts more engaging to the touch. These finishing techniques allow for customization and can transform the molded plastic parts into products that are not only functional but also visually appealing.
In summary, finishing molded plastic parts involves a combination of sanding, painting, and coating techniques. Sanding ensures a smooth surface, while painting adds color and personality. Coating provides protection and durability, making the parts suitable for various applications. By employing these finishing techniques, you can significantly enhance the overall quality and appeal of recycled plastic molded items.
Plastic Film Recycling: Where to Find the Right Drop-Off Points
You may want to see also
Frequently asked questions
Molding recycled plastic involves shaping the material into a desired form using a molding process. This can be achieved through various techniques such as injection molding, blow molding, or compression molding. The plastic is first shredded and cleaned to remove contaminants, then melted and injected into a mold, where it takes the shape of the mold cavity. After cooling and solidification, the molded part is ejected from the mold.
Selecting the appropriate recycled plastic depends on several factors, including the desired properties of the final product, the application, and the availability of the material. Common types of recycled plastics include PET (polyethylene terephthalate), HDPE (high-density polyethylene), and LDPE (low-density polyethylene). Each type has unique characteristics, such as strength, flexibility, and transparency, which can be advantageous for different projects. Researching the specific requirements of your project and understanding the properties of different recycled plastics will help you make an informed decision.
To ensure the best results when molding recycled plastic, consider the following: maintain a clean and dry environment to prevent contamination; use a reputable source for the recycled material to ensure consistency in quality; monitor and control the molding process parameters, such as temperature and pressure, to optimize material flow and reduce defects; and consider using a mold release agent to facilitate easy part ejection and minimize surface imperfections. Additionally, regular maintenance and calibration of the molding machinery are essential to consistent results.