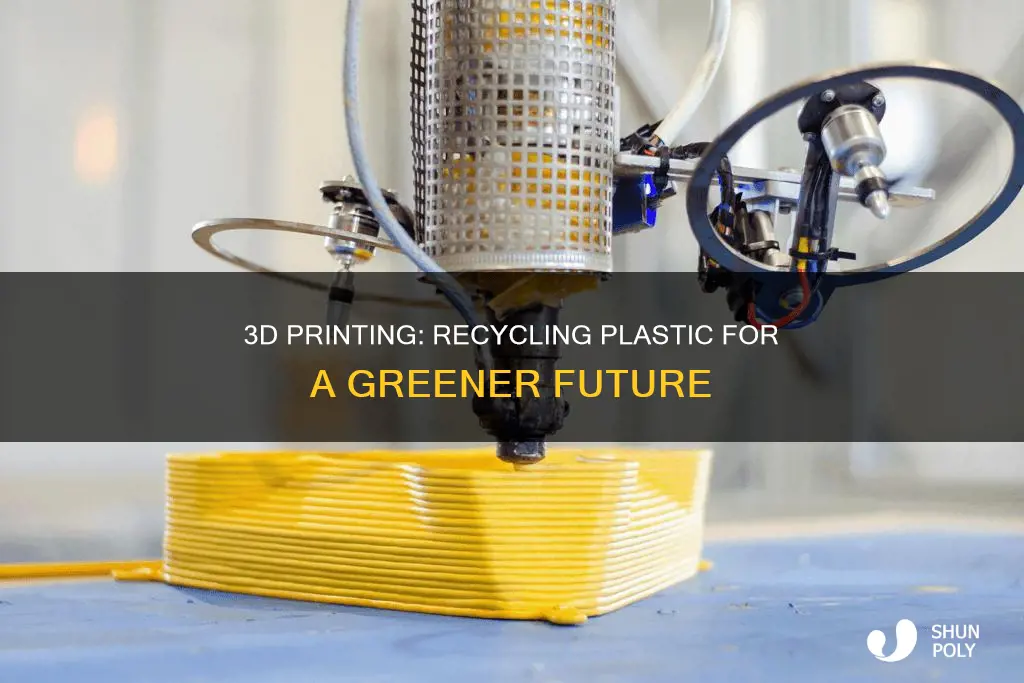
Recycling 3D printer plastic is an important practice for sustainability and cost-effectiveness. With the growing popularity of 3D printing, understanding how to properly recycle the materials used in these printers is crucial. This guide will explore various methods and techniques to recycle 3D printer plastic, including sorting and cleaning the material, using recycling machines, and exploring creative ways to repurpose the recycled plastic. By implementing these practices, you can contribute to a greener environment and potentially save on material costs for your 3D printing projects.
Characteristics | Values |
---|---|
Types of Plastic Used in 3D Printing | ABS, PLA, PETG, Nylon, TPU, and more |
Recycling Methods | Mechanical Recycling, Chemical Recycling, and 3D Printing of Recycled Material |
Mechanical Recycling | Shredding, Granulating, and Re-extrusion |
Chemical Recycling | Pyrolysis, Solvent-based, and Gasification |
Benefits of Recycling | Reduces waste, Conserves resources, Lowers costs, and Promotes sustainability |
Challenges and Considerations | Material Sorting, Contamination, and Quality Control |
Best Practices | Use certified recycling facilities, Follow manufacturer guidelines, and Explore new recycling technologies |
Environmental Impact | Decreases landfill waste, Lowers carbon footprint, and Promotes a circular economy |
Future Trends | Development of advanced recycling techniques, Increased use of recycled 3D printing materials, and Standardization of recycling processes |
What You'll Learn
- Sorting Plastic Types: Identify and separate different types of plastic for effective recycling
- Cleaning and Preparing: Rinse and chop plastic into small pieces for easier processing
- Melting and Extrusion: Heat and melt plastic, then extrude it into new shapes
- Filament Creation: Form recycled plastic into new filaments for 3D printing
- Design and Printing: Use recycled filament to create new 3D models and objects
Sorting Plastic Types: Identify and separate different types of plastic for effective recycling
The process of recycling 3D printer plastic begins with proper sorting and identification of the various plastic types used in these printers. This step is crucial as different plastics require specific recycling methods and can have distinct end-uses. Here's a guide on how to effectively sort and separate these plastics:
Identify the Plastic Types: 3D printers often use a variety of plastics, including ABS (acrylonitrile butadiene styrene), PLA (polylactic acid), PETG (polyethylene terephthalate glycol-modified), and sometimes even flexible materials like TPE (thermoplastic elastomer). Each of these plastics has unique properties and recycling considerations. For instance, ABS is known for its impact resistance, while PLA is biodegradable and derived from renewable resources. Understanding these differences is the first step towards proper recycling.
Sorting Techniques: Implement a systematic sorting process to ensure efficiency and accuracy. One common method is to use color-coding or labeling systems. For example, you can assign a specific color or label to each type of plastic, making it easier for recyclers or your team to identify and separate them. ABS, often in blue or clear, and PLA, typically in white or clear, are commonly sorted this way. This simple technique can significantly streamline the recycling process.
Physical Inspection: Visually inspect the plastic materials to identify any differences. ABS, for instance, is usually harder and more rigid, while PLA can feel softer and more flexible. PETG, a popular choice for many 3D printers, is often translucent and has a slight flexibility. These physical attributes can help in distinguishing between different plastics, especially when combined with color-coding.
Consider Recycling Streams: Different types of plastics may have specific recycling streams or facilities that can handle them effectively. For example, some recycling centers might specialize in ABS or PLA, ensuring better processing and end-product quality. Researching and connecting with local recycling experts or facilities that accept 3D printer plastics can greatly enhance the recycling process and reduce contamination.
Educate and Train: Ensure that anyone involved in the recycling process is well-informed about the different plastic types and their proper handling. Providing clear instructions and training materials can prevent errors and promote a more efficient recycling system. This step is essential, especially in large-scale recycling operations or in educational institutions teaching 3D printing and recycling practices.
By following these sorting and identification practices, you can significantly contribute to the effective recycling of 3D printer plastics, reducing waste and promoting a more sustainable approach to 3D printing.
Starbucks' Plastic Cup Recycling: A Green Initiative or Greenwashing?
You may want to see also
Cleaning and Preparing: Rinse and chop plastic into small pieces for easier processing
When it comes to recycling 3D printer plastic, the first crucial step is cleaning and preparing the material to ensure a successful recycling process. This initial phase is essential as it sets the foundation for the entire recycling journey.
The cleaning process begins with rinsing the plastic. It is imperative to remove any residual filament, support structures, or debris that may still be attached to the plastic. Start by gently washing the plastic parts under running water to eliminate any loose particles. For more stubborn residue, a mild detergent or dish soap can be used, ensuring that no harmful chemicals remain on the plastic. Rinsing thoroughly with clean water is vital to remove any soap residue and ensure the plastic is free from contaminants.
Once rinsed, the plastic needs to be prepared for processing. The most effective way to do this is by chopping the plastic into small, uniform pieces. This step significantly simplifies the recycling process and makes it more manageable. Aim for pieces that are approximately 1-2 inches in size, as this size range is ideal for most recycling methods. Smaller pieces can be further processed if needed, but starting with this size range is a good practice. Use a sharp knife or a pair of scissors to carefully cut the plastic, ensuring clean and straight cuts. For larger 3D printer parts, consider using a small saw or a dedicated plastic cutting tool to achieve precise and clean cuts.
Chopping the plastic requires attention to detail to maintain consistency. Irregular pieces might lead to processing challenges, so take the time to carefully cut each piece to the desired size. This step is crucial for the overall efficiency of the recycling process, as it allows for better material handling and processing.
By following these cleaning and preparation steps, you are setting the stage for a successful 3D printer plastic recycling journey. Proper cleaning ensures that the material is free from contaminants, and chopping it into uniform pieces simplifies the recycling process, making it more accessible and efficient.
Unveiling the Truth: Do Straws and Plastic Lids Sabotage Recycling?
You may want to see also
Melting and Extrusion: Heat and melt plastic, then extrude it into new shapes
The process of recycling 3D printer plastic through melting and extrusion is a fascinating and sustainable way to give new life to old materials. This method involves heating and softening the plastic, allowing it to be reshaped and molded into new forms. Here's a step-by-step guide to mastering this technique:
Melting the Plastic: Begin by sourcing your 3D printer plastic waste, which could be from old prints or discarded parts. Ensure the plastic is clean and dry to avoid any contamination. The first step is to melt the plastic, and this can be achieved using a dedicated plastic melting machine or a heat gun. Set the temperature according to the type of plastic you are working with. For common materials like ABS or PLA, temperatures ranging from 200°C to 250°C are typically required. Carefully heat the plastic, ensuring it reaches a uniform temperature to avoid uneven melting.
Preparing the Extrusion Setup: Once the plastic is melted, it's time to prepare your extrusion setup. This process involves using an extruder, which can be either a simple heated nozzle or a more complex machine with precise temperature control. The extruder should be set to the desired temperature, usually matching the melting point of your chosen plastic. This setup will be responsible for shaping the molten plastic.
Extrusion Process: Now, the magic happens! Feed the melted plastic into the extruder, ensuring it is properly centered and aligned. The extruder will then push the plastic through a heated nozzle, which will further melt and shape it. The temperature of the nozzle should be slightly lower than the melting point to maintain the desired consistency. As the plastic exits the nozzle, it solidifies due to cooling, taking the shape of the nozzle's orifice. This process allows you to create custom shapes, from simple cylinders to complex designs.
Shaping and Cooling: After the extrusion, the plastic is still hot and malleable. You can now manipulate it into your desired form. This might involve cutting, bending, or shaping the material while it is still pliable. Once shaped, allow the plastic to cool down, which will harden it and preserve the new form.
Post-Processing: Depending on your application, further post-processing may be required. This could include sanding, painting, or adding additional features to the newly created object. With this method, you can recycle 3D printer plastic waste, reducing environmental impact and creating unique, custom-made items.
Plastic Drinks: Trash or Recycle? Unraveling the Waste Mystery
You may want to see also
Filament Creation: Form recycled plastic into new filaments for 3D printing
The process of creating new filaments from recycled plastic is an exciting and sustainable way to contribute to the 3D printing community while reducing waste. Here's a step-by-step guide to help you get started with filament creation:
Collection and Sorting: Begin by gathering used plastic materials that are suitable for recycling. This can include plastic trimmings, old 3D printer filament spools, or even larger plastic items like bottles or containers. Ensure that the plastic is clean and free from contaminants. Properly sort the collected plastic by type and color to facilitate the recycling process. Common types of plastic used in 3D printing include PLA (Polylactic Acid), ABS (Acrylonitrile Butadiene Styrene), and PETG (Polyethylene Terephthalate Glycol-modified).
Shredding and Granulation: Once sorted, the plastic needs to be shredded into small pieces. This step helps in reducing the size of the plastic, making it easier to process. Use a shredder or a blender to grind the plastic into a fine powder. For PLA, a particle size of around 100-200 mesh is ideal. ABS and PETG may require slightly different particle sizes, so adjust accordingly. After shredding, the plastic powder can be further processed into granules, which will serve as the raw material for filament production.
Extrusion and Filament Formation: This is the core step in creating new filaments. You will need a specialized machine called an extruder, which can be either a desktop or a larger industrial model. The extruder heats and melts the plastic granules, then pushes the molten plastic through a die to form the filament. The die has a specific diameter, typically 1.75mm or 3mm, which determines the final diameter of your filament. As the plastic is extruded, it is cooled and solidified, forming a continuous strand of filament.
Drying and Spooling: After extrusion, the freshly created filament needs to be dried to remove any moisture. Place the filament on a drying rack or in an oven set to a low temperature (around 60-70°C) for a few hours. Proper drying ensures the filament's strength and longevity. Once dried, cut the filament into desired lengths and spool it for easy storage and use in your 3D printer.
Creating your own filaments from recycled plastic is a rewarding process that reduces environmental impact and provides a unique, personalized 3D printing experience. It requires some technical knowledge and equipment, but the results can be highly satisfying, offering a sustainable alternative to traditional filaments.
Ohio's Plastic Recycling Journey: A Green Revolution
You may want to see also
Design and Printing: Use recycled filament to create new 3D models and objects
The process of recycling 3D printer plastic is an exciting and sustainable way to give new life to your old filament and create unique, eco-friendly objects. Here's a guide on how to design and print with recycled materials:
Sourcing Recycled Filament: Begin by acquiring recycled filament, which can be sourced from various online retailers or local recycling centers. Many companies now offer recycled PLA (Polylactic Acid), a popular 3D printing material, made from post-consumer waste. Look for reputable brands that provide information about their recycling processes and the origin of the recycled materials. This ensures that you are contributing to a more sustainable practice.
Design Considerations: When designing 3D models, keep in mind the properties of recycled filament. It might have slightly different characteristics compared to virgin filament, such as a slightly lower melting point or a more consistent color. Experiment with your designs to understand how the recycled material behaves during printing. You can create intricate designs and complex structures, but be mindful of potential warping or dimensional changes due to the recycled nature of the filament.
Printing Process: Setting up your 3D printer for recycled filament is similar to using regular filament. Calibrate the nozzle temperature and bed adhesion to suit the specific recycled material you are using. Some recycled filaments may require a slightly higher temperature to ensure proper extrusion. Pay attention to the printing settings, as you might need to adjust the flow rate or layer height to accommodate the unique properties of recycled PLA.
Creating New Objects: With your recycled filament ready, you can now design and print a variety of objects. Consider creating functional items like phone stands, desk organizers, or even small furniture. For decorative pieces, you could design intricate sculptures or personalized gifts. The possibilities are endless, and you can explore different design software to create 3D models that showcase your creativity while promoting sustainability.
Sharing and Inspiring Others: Once you've printed your recycled creations, share your designs online or within your local 3D printing community. This encourages others to explore recycling in 3D printing and promotes a circular economy. By showcasing the quality and versatility of recycled filament, you can inspire a new generation of eco-conscious creators.
Curbside Recycling: Unraveling the Mystery of Plastic 4
You may want to see also
Frequently asked questions
Most 3D printers use PLA (Polylactic Acid), ABS (Acrylonitrile Butadiene Styrene), or PETG (Polyethylene Terephthalate Glycol-modified) plastics. These are the most common and widely accepted materials for recycling. It's important to check with your local recycling center to confirm which types they accept.
Before recycling, ensure the plastic is clean and dry. Remove any non-plastic components like metal parts, supports, or filament spools. Break down large objects into smaller pieces to increase the chances of successful recycling. For PLA, it's best to shred or grind the material to create a consistent, fine powder.
Yes, filament recycling requires careful handling. For PLA, you can melt and re-extrude it into new filament, but this process is more complex and requires specialized equipment. ABS can be recycled by shredding it into small pieces and then using a pelletizer to create new pellets. Always follow safety guidelines when working with hot materials.
Yes, failed prints and support structures can be recycled, but they should be cleaned and sorted separately. Remove any residual filament or debris from the failed parts. For support structures, you can dissolve them in a suitable solvent or melt them down, depending on the material. Proper preparation ensures a higher quality recycled product.